Metal roof roll forming machines are equipment used to convert flat metal sheets into customized roofing and wall panels. This equipment is in high demand due to increased construction activity and infrastructure projects. We discuss the working, types, cost considerations, and suppliers of these machines.
Metal Roof Roll Forming Machine Equipment
A metal roof roll forming machine takes a coil of flat sheet metal and processes it through a series of roller dies to shape it into various long panel profiles. Common panel profiles produced are corrugated, box ribbed, flat, standing seam, concealed fix, and several other customized shapes.
The main components of a metal roof sheet roll forming machine are:
- Decoiler to hold the sheet coil
- Feeder section with pinch rolls to feed the sheet
- Forming stations with roller dies to shape the sheet
- Fly shear/rotary shear to cut panels to length
- Stacker to collect cut panels
Other optional accessories are embossing unit, notching, hole punching units as per application needs.
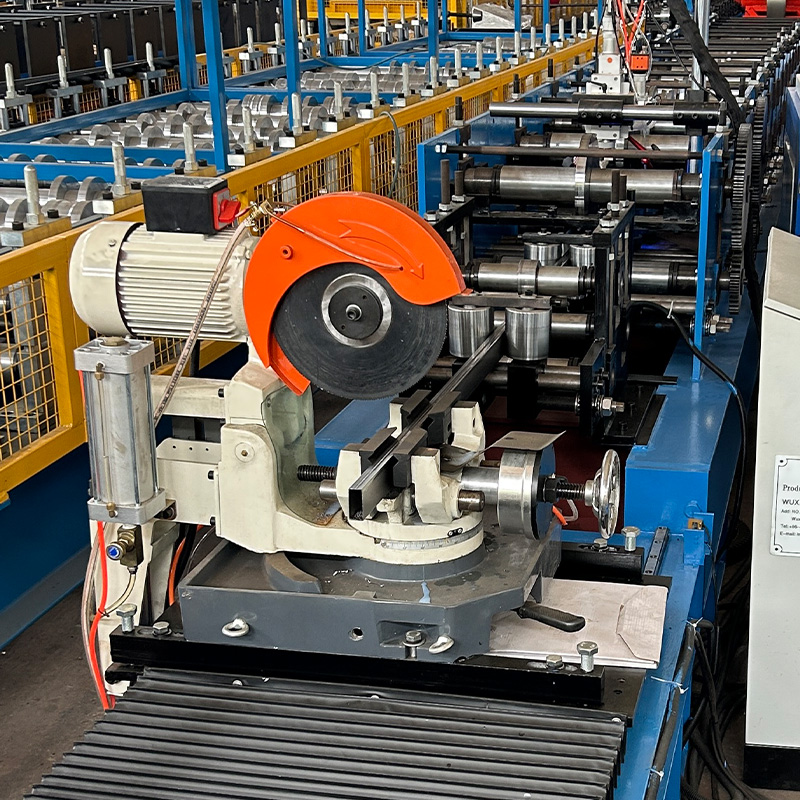
Types of Metal Roof Roll Forming Machines
Type | Description |
---|---|
By Capacity | Light duty, medium duty, heavy duty depending on sheet thickness handled |
By Operation | Manual, Semi-automatic, Fully-automatic with servo motor drives & plc control |
By Forming Type | Cold roll forming at room temperature |
By Structure | All-in-one combined units, Separate component modular machines |
By End-Use | Roofing, Wall paneling, Rolling shutter, Highway barriers, Drainage profiles |
Working Process of a Roofing Sheet Roll Forming Machine
The working process involves decoiling a thin metal sheet and feeding it through a series of stands containing roller dies. As the sheet passes each stand, it takes the shape defined by the profile of the rolls. Finally, the long formed profile sheet is cut into lengths by the shear and collected on the exit stacker.
For complex profiles more forming stands are used to achieve the desired shape gradually. Inline operations like punching holes, notching, embossing can also be incorporated.
Material Feeding, Forming, Design in Roof Panel Roll Forming
Sheet Metal Material Selection
Common sheet metals are galvanized steel, galvalume steel, pre-painted steel, aluminum sheets, stainless steel sheets depending on corrosion resistance, strength, and cost considerations for the application.
Thickness range: 0.15mm to 1.2mm Width range: 600mm to 1250mm
Material surface coating, width, thickness, and mechanical properties are to be specified when ordering the roof sheet roll forming equipment.
Profile Shape Options
Over 100+ standard and custom profiles for roofing and wall flashings are possible. Some common ones being manufactured are:
- Trapezoidal rib / Corrugated sheets
- Box ribbed sheets
- Standing seam sheets
- Wide pan sheets
- Deeplink sheets
- Concealed fix sheets
- Composite panels
- Clip-lock panels
Custom profiles can be developed based on architectural drawings.
Roll Tooling Design & Bending
The profile is designed and roll passes are calculated using software like MetalForm and SigmaNest. The flower pattern outlines the progressive bending steps.
The rolls are CNC machined from D2 steel and heat treated to 45-50 HRC for sheet metal forming hardness.
-
Rolling Shutter Slat Roll Forming Machine
-
Vineyard Post Roll Forming Machine
-
Auto Size Changeable Sigma Purlin Roll Forming Machine
-
Electrical Cabinet Frame Roll Forming Machine
-
Din Rail Roll Forming Machine
-
Cable Ladder Roll Forming Machine
-
PV Mounting Bracket C Shape Profile Roll Forming Machine
-
Cable Tray Roll Forming Machine
-
C Z Purlin Channel Cold Roll Forming Machine Full Auto Galvanized Steel Profile
Slicing and Customization in Roll Formed Sheets
- Fly Shear – Guilotine type shear with top and bottom blades is used for instant squaring of the panels. No scratches or deformation to panels.
- Rotary Shear / Circular Shear – Used where curved edges or notch cuts are required on panels.
- Hole Punching Units – For making bolt holes on the sheet for fixation.
- Embossing Rollers – For decorative bumps/geometry.
- Notching Unit – For connecting flashings between panels.
- Length Cutting Control – Cut to length as per order requirement from 0.5m to 12m.
- Stacker – Collects cut panels sequentially.
Leading Roll Forming Machine Manufacturers & Cost Range
Brand | Location | Price Range |
---|---|---|
Zhongli Roll Forming Machine | China | $5000-$15000 |
BOTOU Xianfa Roll Forming Machine | China | $6000-$18000 |
Jouanel Industrie | France | $8000-$25000 |
Shanghai Rollwell Machinery | China | $4000-$28000 |
Bradbury Group | UK | $12000-$50000 |
Formtek | USA | $15000-$78000 |
Dynamik Roofing Machines | South Africa | $5000-$21000 |
Wolffkran | India | $4000-$15000 |
Howick Ltd. | New Zealand | $13000-$71000 |
Framecad Technologies | New Zealand | $14800-$128000 |
CO-Z Roll Forming Machinery | Taiwan | $8800-$38000 |
SIPPI Machine Tools | India | $3500-$12000 |
Light duty basic machines for thin sheets cost $4000 to $15,000. Heavy duty fully automatic fast machines with production over 100meters/minute cost over $40,000.
European and American manufacturers generally have higher prices but better quality and durability up to 20 years lifespan.
Installation and commissioning
- The roll forming machine requires a covered shade and flat platform for placement. It needs 3 phase electrical connection.
- Once bolted and grouted on the floor, the decoiler sheet coil is loaded and threaded through the entry guides.
- Machine is run on trial at slow speed, presets adjusted to center the sheet alignment. Gradually speed increased in steps up to production speed while checking vibration, noise issues.
- Multiple coiljoining is setup for automatic splicing when coil ends. Run some test panels through the entire process from feeding to stacking. Check for any scratches, deformation of panels.
- Fine tune all setting presets related to feed angle, shear depth, cut length variations.
- The machine is now ready for starting production after successful commissioning.
Operation and Working
- Machine operator feeds the sheet coil on unwinding decoiler and threads sheet through entry guides adjusting the feed angle.
- Length and shape profile is selected on the PLCD screen by choosing saved recipes.
- Jog buttons allow inch-wise movement for adjustments. Auto mode starts production run as per set speed and length parameters.
- Formed panels getting cut drop onto exit conveyor and stacker which can be collected in trolley. Counters keep track of production.
- Periodic oiling of moving shafts is needed. Roller guides, shear blades need inspection and replaced when worn out. Electric panel, motors and wires need checks for heating or loose contacts.
Maintenance Tips
- Clean sheet metal slivers, scrap pieces frequently off the floor
- Ensure proper frame grounding and safety signs on machine
- Check screw tightness on stands periodically
- Inspect roll bearings & gearbox oil levels
- Monitor electrical load when running
- Apply rust preventive coating on unpainted machine parts
- Check hydraulic system oil leakage, filter clog, pump operation
Proper maintenance improves lifespan, performance and safety.
Selection Criteria When Buying Roll Forming Equipment
Parameters to compare:
- Sheet metal thickness handling capacity
- Profile forming ranges – height, width
- Production speed – meters/minute
- Length cutting capacity – minimum & maximum
- Type of punching & notching accessories
- Material of construction of rolls and overall machine
- Floor space dimensions of overall line
- Price, payment terms, warranty period
- After-sales service response
Get above details from various suppliers before deciding. Check demo videos and client testimonials. Finalize based on reputation, features vs budget ratio.
Pros and Cons of Metal Sheet Roll Forming Process
Benefits & Advantages
- High production rates up to 120 meters/minute possible leading to faster projects
- Consistent quality panels produced reduce wastage in site
- Custom profiles as per design choice gives architectural flexibility
- Lightweight long span panels reduce building deadload costs
- Lower maintenance than traditional roof & wall cladding methods
- Better water drainage and leakproof panels improve life of structure
- Industry leading 20 year warranty on metal sheet coating from suppliers
- Fireproof panels as metal sheets are non-combustible needing no extra treatment
- Recoating at end of life restores sheets avoiding demolition & rebuild costs
- 100% recyclable metal sheets help achieve green building certification
Limitations & Disadvantages
- High initial capital investment requiring business scale impact assessment
- Sheet surface prone to rusting needing regular paint touchup post installation
- Expansion/contraction of long sheets due to temperature calls for provision of expansion joints
- Training needed for first-time installers to avoid improper seam joining or leaky walls
- Remote areas have lack of servicing access to maintain or repair roll form lines
- Existing platforms may require assessment and rework to handle heavy equipment loads
- Custom profile design & roll tooling have long lead times of 6-8 weeks
By planning appropriately for the above limitations, reliable operational results can be obtained from these versatile roll forming machines.
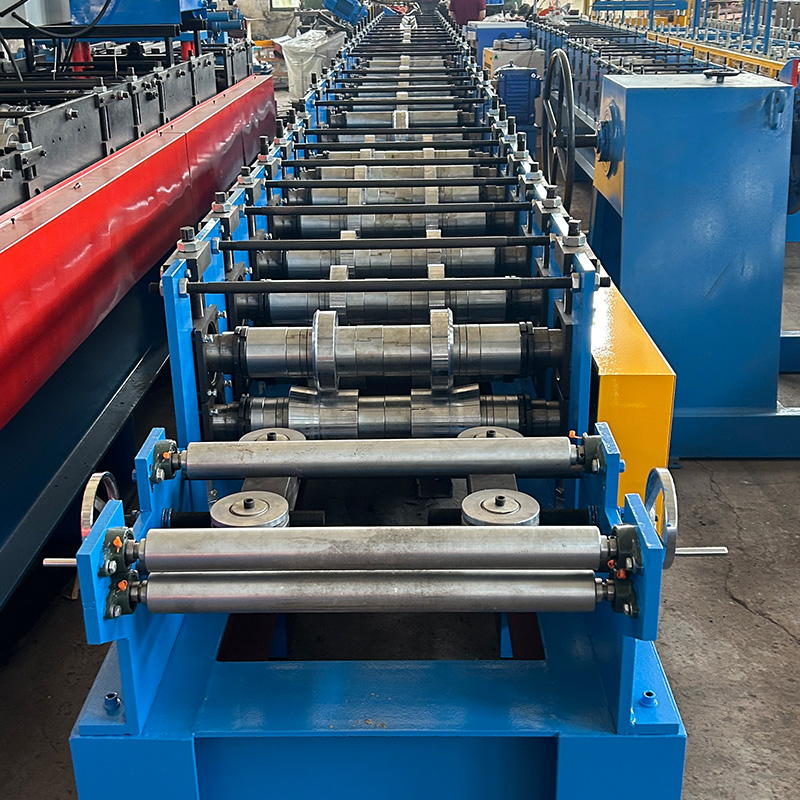
FAQs
Q: What thickness of sheets can be formed?
A:Thickness range capability is 0.15mm to 1.2mm for steel/aluminum. Up to 2mm stainless steel/titanium possible.
Q: What drivetrain system is used in these machines?
A: Basic models use manual hand cranks. Advanced industrial models use servo motor & drives withPLC control for speed, positioning and automation.
Q: Does it require any foundation or base?
A: A flat leveled hard surface like RCC slab is needed. Grouted bolts fix it firmly to avoid vibration at high speeds.
Q: How to calculate power requirement?
A: Depends on sheet metal thickness, no. of rolls, accessories added like punch/notcher. Typically 11kw to 30kw for machines of varying capacity.
Q: Can different width coils be run?
A: Yes. But all forming rollers & decoiler would need changing to match coil width. Time consuming job requiring expertise.
Q: What accuracy and surface finish is achieved?
A: High end CNC machined rolls provide panel accuracy upto +/- 1.0mm and glossy surface finish.
Q: What standards should these machines comply to?
A: ISO 9001 quality certification and CE marking compliance demonstrates rigor in design, manufacturing process and validation testing.