Overview of Metal Roll Forming Machines
Metal roll forming machines are essential in modern manufacturing, particularly in the production of metal profiles and components. These machines shape metal by passing it through a series of rollers, gradually bending it into the desired shape. Whether you’re a seasoned professional in the metalworking industry or a newcomer looking to understand the intricacies of these machines, this guide will provide a detailed, SEO-optimized overview to help you navigate this complex topic.
In this article, we will explore various aspects of metal roll forming machines, from their types and working processes to their applications and maintenance. We’ll delve into the specifics of different models, discuss key components, and offer insights into selecting the best supplier for your needs. By the end, you’ll have a thorough understanding of metal roll forming machines and how they can benefit your operations.
What is a Metal Roll Forming Machine?
A metal roll forming machine is a piece of equipment used to bend and shape metal sheets or strips into continuous profiles, such as panels, gutters, or structural components. This process is highly efficient, producing precise shapes with minimal waste, making it ideal for high-volume production.
How Does a Metal Roll Forming Machine Work?
The working process of a metal roll forming machine involves several stages:
- Feeding: The metal sheet or strip is fed into the machine.
- Forming: The material passes through a series of rollers, each set progressively bending the metal closer to the final shape.
- Cutting: Once the desired shape is achieved, the metal is cut to the required length.
- Ejection: The finished product is ejected from the machine, ready for further processing or assembly.
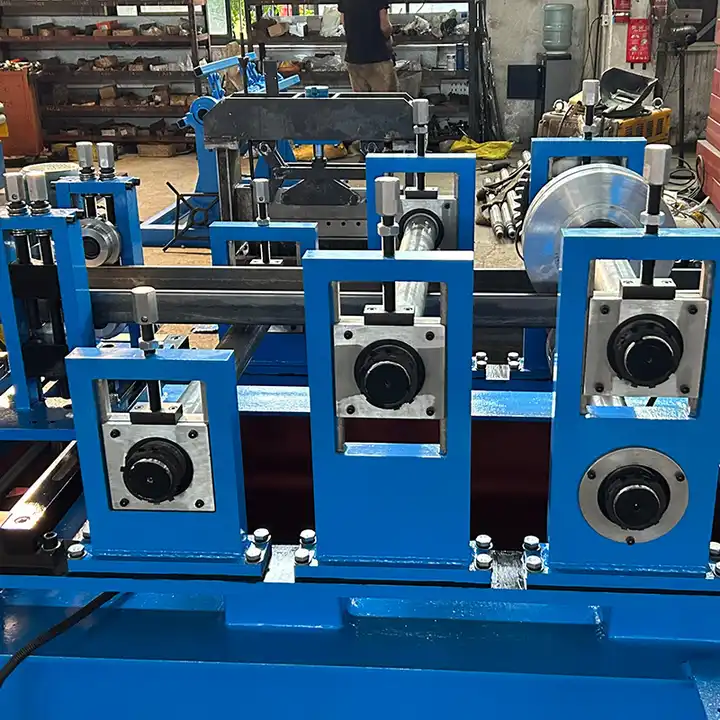
Key Components of a Metal Roll Forming Machine
Component | Function |
---|---|
Rollers | Bend and shape the metal |
Feeder | Guides the metal into the machine |
Cutting Mechanism | Cuts the formed metal to the desired length |
Drive System | Powers the rollers and other components |
Control System | Manages machine operations and settings |
Frame | Supports and stabilizes the machine structure |
Types of Metal Roll Forming Machines
Type | Description |
---|---|
Single Roll Forming Machine | Ideal for small-scale production, focusing on one profile at a time |
Double Roll Forming Machine | Capable of producing two different profiles simultaneously, increasing efficiency |
Continuous Roll Forming Machine | Designed for high-volume production with continuous feeding and forming |
Adjustable Roll Forming Machine | Allows for quick changes in profile specifications without major retooling |
Portable Roll Forming Machine | Compact and mobile, suitable for on-site operations |
Hydraulic Roll Forming Machine | Utilizes hydraulic systems for enhanced power and precision |
Electric Roll Forming Machine | Relies on electric motors, offering smooth and consistent operation |
Servo Roll Forming Machine | Equipped with servo motors for precise control over speed and position |
High-Speed Roll Forming Machine | Optimized for maximum speed and efficiency in large-scale production |
Custom Roll Forming Machine | Tailored to specific production needs, offering unique features and capabilities |
Working Process of Metal Roll Forming Machines
The roll forming process is intricate and requires precise control at each stage. Here’s a more detailed look at each step:
- Material Loading: The raw metal strip is loaded onto a decoiler, which unrolls the metal as it is pulled into the machine.
- Entry Guide: The entry guide aligns the metal strip to ensure it enters the rollers correctly.
- Roll Forming Stages: The metal passes through multiple sets of rollers, each performing a specific bend. The number of stages can vary depending on the complexity of the profile.
- Cutting to Length: A cutting mechanism, usually a hydraulic or mechanical shear, cuts the continuous profile into specified lengths.
- Exit Table: The finished pieces are collected on an exit table or conveyor, ready for further processing or packaging.
Efficiency and Speed of Metal Roll Forming Machines
Machine Type | Speed | Efficiency |
---|---|---|
Single Roll Forming Machine | 10-20 meters/minute | Moderate |
Double Roll Forming Machine | 20-40 meters/minute | High |
Continuous Roll Forming Machine | 40-60 meters/minute | Very High |
High-Speed Roll Forming Machine | 60-100 meters/minute | Extremely High |
-
Highway Guardrail End Terminal Forming Machine
-
Highway U/C Post Roll Forming Machine
-
2 Waves Highway Guardrail Roll Forming Machine
-
3 Waves Highway Guardrail Roll Forming Machine
-
Vineyard Post Roll Forming Machine
-
Auto Size Changeable Sigma Purlin Roll Forming Machine
-
Auto Size Changeable C Z Purlin Roll Forming Machine
-
Auto Size Changeable Z Purlin Roll Forming Machine
-
Auto Size Changeable C U Purlin Roll Forming Machine
Customized Mechanical Parameters of Metal Roll Forming Machines
Parameter | Description |
---|---|
Profile Width | Adjustable to accommodate various metal strip widths |
Material Thickness | Can be customized for different thickness ranges |
Number of Stages | Configurable based on the complexity of the profile |
Roller Material | Selectable based on the type of metal being formed |
Cutting Mechanism | Options for hydraulic, mechanical, or laser cutting |
Automation Level | Customizable from manual to fully automated systems |
Applications of Metal Roll Forming Machines
Application Area | Uses |
---|---|
Construction | Roofing panels, wall cladding, structural components |
Automotive | Chassis parts, body panels, trim pieces |
HVAC | Air ducts, vents, and other ventilation components |
Appliance Manufacturing | Refrigerator panels, washing machine parts |
Storage Solutions | Shelving units, racks, and cabinets |
Furniture Manufacturing | Metal frames, supports, and decorative elements |
Electrical Industry | Cable trays, conduit systems, and enclosures |
Agriculture | Greenhouse frames, irrigation channels, and fencing |
Transportation | Trailer bodies, rail components, and bus frames |
Energy | Solar panel frames, wind turbine components |
Installation, Operation, and Maintenance of Metal Roll Forming Machines
Aspect | Details |
---|---|
Installation | Requires a stable foundation, electrical connections, and calibration |
Operation | Involves feeding material, monitoring the process, and adjusting settings as needed |
Maintenance | Regular lubrication, inspection of rollers and cutting mechanisms, and replacement of worn parts |
Suppliers and Price Range of Metal Roll Forming Machines
Supplier | Price Range |
---|---|
FormTech Systems | $50,000 – $200,000 |
RollForm Machines Inc. | $40,000 – $180,000 |
MetalForming Solutions | $45,000 – $190,000 |
Precision Roll Forming | $60,000 – $250,000 |
ProRoll Engineering | $55,000 – $220,000 |
Advanced Forming Technology | $70,000 – $300,000 |
FlexForm Machinery | $65,000 – $280,000 |
SteelMaster Machinery | $50,000 – $210,000 |
CustomRollForm Tech | $75,000 – $320,000 |
Ultimate Roll Forming | $80,000 – $350,000 |
How to Choose a Supplier for Metal Roll Forming Machines
Choosing the right supplier for a metal roll forming machine is crucial for ensuring the quality and efficiency of your production process. Here are some factors to consider:
- Reputation and Experience: Look for suppliers with a solid reputation and extensive experience in the industry.
- Customer Reviews and Testimonials: Check reviews and testimonials from other customers to gauge satisfaction and reliability.
- Technical Support and Service: Ensure the supplier offers robust technical support and after-sales service.
- Customization Options: Evaluate whether the supplier can tailor the machine to your specific needs.
- Pricing and Value: Compare prices and assess the overall value, considering the machine’s features and capabilities.
Pros and Cons of Metal Roll Forming Machines
Advantages | Disadvantages |
---|---|
High Efficiency | Initial High Cost |
Precision and Consistency | Requires Skilled Operators |
Minimal Waste | Maintenance Intensive |
Versatile Applications | Space Requirement |
Long-term Cost Savings | Complex Setup |
Key Considerations for Equipment Parameters, Price Ranges, and Forming Processes
When evaluating metal roll forming machines, consider the following:
- Equipment Parameters: Ensure the machine can handle your specific profile dimensions and material types.
- Price Ranges: Balance your budget with the machine’s capabilities and long-term benefits.
- Forming Processes: Understand the specific forming processes involved to ensure compatibility with your production requirements.
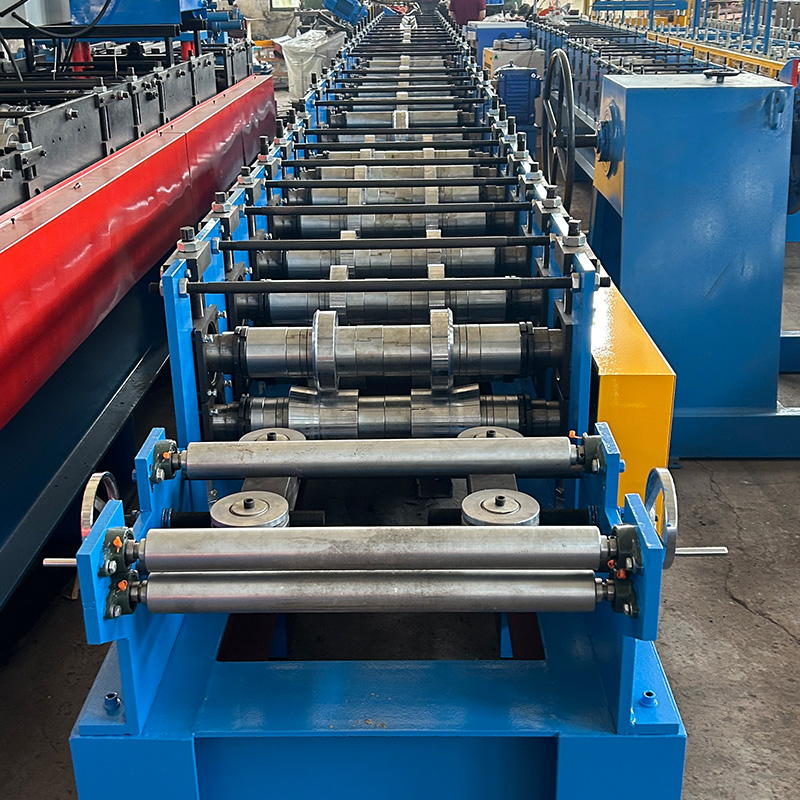
FAQ
Question | Answer |
---|---|
What materials can be used in metal roll forming machines? | Most metals, including steel, aluminum, copper, and stainless steel. |
How long does it take to set up a metal roll forming machine? | Setup time can vary but typically takes several hours to a full day depending on complexity. |
Can roll forming machines be customized? | Yes, many suppliers offer customization options to meet specific production needs. |
What maintenance is required for metal roll forming machines? | Regular lubrication, inspection of components, and replacement of worn parts are essential. |
How does roll forming compare to other metal forming processes? | Roll forming is highly efficient and produces consistent, high-quality profiles with minimal waste. |
Conclusion
Metal roll forming machines are vital tools in modern manufacturing, offering efficiency, precision, and versatility. Whether you’re producing structural components for construction, intricate parts for the automotive industry, or custom profiles for unique applications, these machines can significantly enhance your production capabilities. By understanding the different types of machines, their working processes, and how to choose the right supplier, you can make informed decisions that will benefit your operations in the long run.
With this comprehensive guide, you’re now equipped with the knowledge to navigate the world of metal roll forming machines effectively. If you have any further questions or need personalized advice, feel free to reach out to industry experts or trusted suppliers. Happy roll forming!