Post roll forming machines are used to bend and shape metal coils into customized profiles through a series of progressive roll forming stands. This versatile technology can create complex and accurate cross-sections for various applications in industries like construction, transportation, infrastructure and more.
This comprehensive guide will cover all aspects of post roll forming machines from types, working principles, components, specifications, applications, advantages and limitations. It includes detailed tables and FAQs to help compare different options and make an informed decision for your roll forming needs.
Overview of Post Roll Forming Machines
Post roll forming is a continuous and versatile metal shaping process that converts flat metal strips or coils into customized profiles. It works by gradually bending the material through a series of roll stands arranged in a line. Each stand makes a small incremental bend until the final cross-section profile is achieved.
Key features of post roll forming:
- Creates long, complex, and accurate cross-section profiles
- Highly automated and efficient process with fast production rates
- Ability to form high strength materials like stainless steel and aluminum
- Low tooling costs compared to other fabrication methods
- Minimal material wastage since processing is done on coil stock
- Changes in profiles accomplished by altering roll tooling
- Integrated with operations like punching, cutting, welding for finished parts
Types of Post Roll Forming Machines
Machine Type | Description |
---|---|
Fixed Post Machines | Roll tooling fixed on individual roll stands in sequence to incrementally form the profile |
Movable Post Machines | Roll stands movable to adjust forming stages as per profile |
Cage Roll Machines | Combines features of fixed and movable post machines for flexibility |
High Speed Roll Forming Lines | Produce profiles at speeds over 100 m/min by overlapping roll stations |
Main Components of a Post Roll Forming Machine
Component | Function |
---|---|
Decoiler | Feeds metal coil strip into roll forming stands |
Feed rolls | Pulls material into forming section at set speed |
Forming rolls | Progressively bend material through a series of stands |
Pinch rolls | Support and guide strip through roll stations |
Shearing station | Cuts profiles to desired lengths |
Stacker | Collects cut profiles |
Control panel | Controls speed, guides adjustments and monitoring |
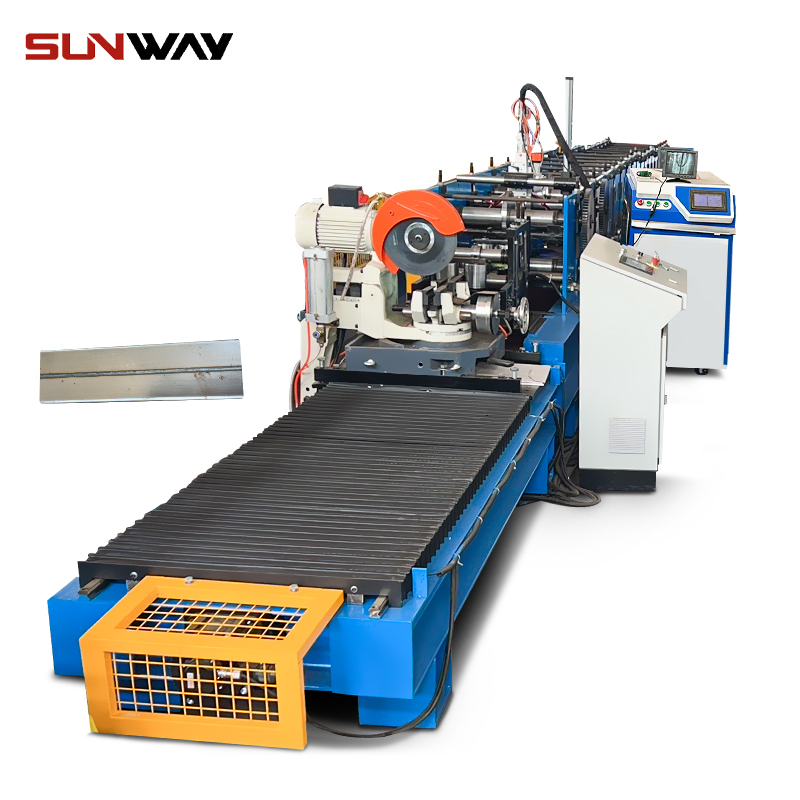
Applications of Post Roll Forming Machines
Post roll forming is used to manufacture metal profiles across a wide range of industries:
Construction and Infrastructure
- Roofing (standing seam, concealed fix)
- Cladding panels
- Bridge decking
- Drainage profiles
- Structural sections
- Railing systems
- Highway products
- Purlins and girts
Automotive and Transportation
- Chassis components
- Truck bodies
- Bus body frames
- Railway car roofing
- Silencers and mufflers
- Automotive panels
Equipment and Appliances
- Rack uprights
- Electrical enclosures
- Lighting fixtures
- Shelving sections
- Window sections
- Office furniture
- Cookware and utensils
Advantages of Post Roll Forming
- Highly versatile process capable of intricate and complex profiles
- Consistent quality and tolerance in profiles
- Fast production with high material yield
- Ability to form high and ultra high strength steels
- Low tooling investment compared to other processes
- Minimal scrap loss since coils are gradually formed
- Lower energy use than machining or pressing
- Quick roll changeover using modular tooling
- Compact equipment requiring less space than other metal fabrication processes
Buying Considerations for Post Roll Forming Machines
Key factors to consider when investing in a post roll forming machine:
Desired Profile Specifications
- Product shape and complexity of cross-section
- Metal thickness and material grade
- Dimensional accuracy and tolerances
- Required production rate or output
- Width range of coil material to be formed
Production Efficiency Requirements
- Level of automation needed
- Integration with other operations like punching or cutting
- Quick changeover between profiles
- Built-in monitoring and control features
Space and Layout Constraints
- Overall length based on number of forming stands
- Infeed and outfeed requirements
- Line height and headroom
- Integration with existing processes
Budget and Cost Considerations
- Machine base price plus auxiliary equipment
- Shipping, installation and commissioning
- Training for operators and maintenance staff
- Level of after sales service and technical support needed
Properly evaluating above factors will ensure you choose the ideal roll forming solution tailored for your specific production needs.
Specifications of Post Roll Forming Machines
Post roll forming lines are customized with components selected based on application requirements. Below is an overview of typical machine specifications:
Frame and Rolls
- Frame design: C-frame or O-frame
- Roll station quantity: 10 to 26 typically
- Roll material: D2, alloy steel, adamite
- Roll diameter: 100 to 250 mm
- Roll adjustment: Manual or power assisted
- Roll power source: Electric servo motor or hydraulic drive
Material Parameters
- Material type: Mild steel, stainless steel, aluminum
- Material thickness: 0.5 to 3 mm commonly
- Material width: 300 to 1250 mm range
- Coil I.D.: 400 to 610 mm standard
Speed and Production
- Forming speed: 10 to 120 m/min
- Cut length range: 1 to 10 m
- Production rate: Up to 8000 m/hour
Design and Engineering Standards
Post roll forming machine design, components and safety features should comply with national and international standards. Key ones include:
- ISO 12100 – Safety of Machinery
- EN 1010 – Safety Requirements for Machinery
- ISO 841 – Industrial Robots and Robot Systems
- ISO 5348 – Roll Forming Machines
- OSHA Machine Guarding Regulations
Reputable manufacturers will build machines meeting or exceeding the latest standards. Compliance ensures operational safety and globally accepted production quality.
Installing and Operating Post Roll Forming Machines
Proper installation and operation procedures are vital for safe, efficient and high quality roll forming:
Installation Guidelines
- Ensure sufficient space for machine length, material infeed/outfeed
- Level ground surface to prevent vibration issues
- Proper grounding and power supply lines readied
- Roll tooling, safety guards and devices installed
- All stations aligned, calibrated and tested
Operation Checklist
- Select and load appropriate coil material
- Thread strip through rolls and into feed mechanism
- Set parameters like line speed, shear length
- Start forming process and test sample pieces
- Monitor strip feed, roll adjustment, cutting quality
- Conduct regular maintenance between production runs
Safety Precautions
- Ensure proper staff training on machine operation
- Mandatory PPE like close fitting clothing, safety glasses
- Never reach into operating areas or open guards
- Stop operation if coil strip misfeeds or jams detected
- Follow lockout procedures for maintenance and servicing
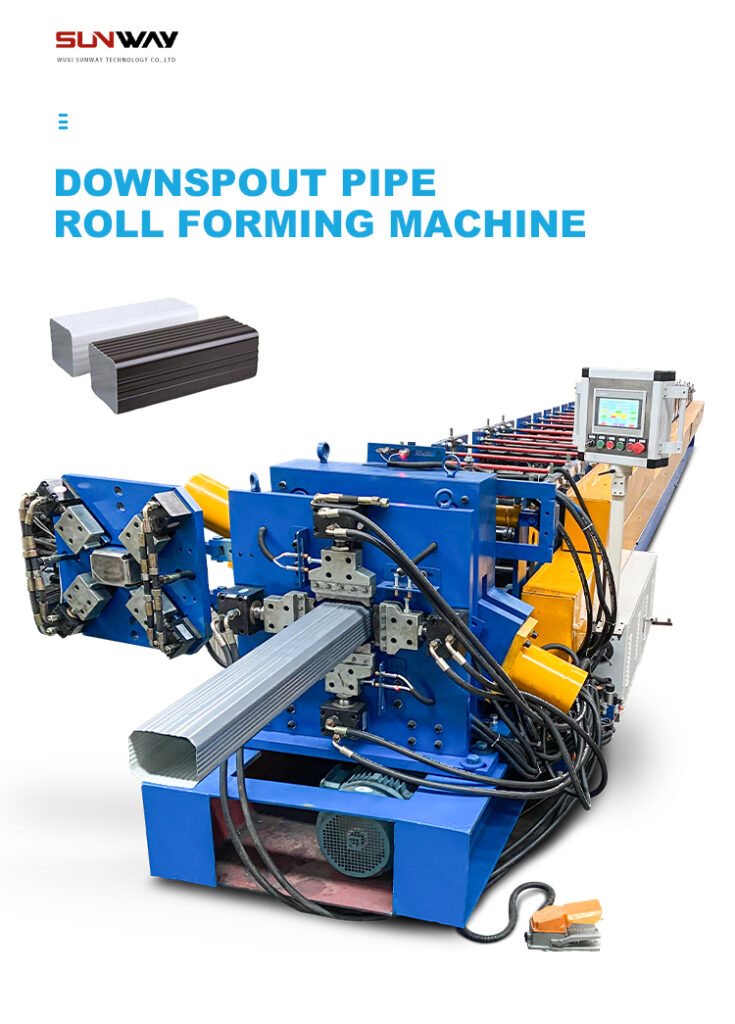
Maintenance of Post Roll Forming Machines
Regular maintenance greatly improves uptime, productivity and safety. Key aspects include:
Daily:
- Visual inspection of roll tools, strip alignment, cut quality
- Check for loose fasteners, abnormal vibration or noise
- Remove metal debris and dust buildup
Weekly:
- Lubricate bearings and roll shafts
- Inspect chains, sprockets, gears
- Check hydraulic fluid levels
- Test emergency stop and safety devices
Monthly:
- Thorough cleaning of all stations
- Inspect shafts, bearings, seals for wear
- Check electrical wiring and connections
- Calibrate/adjust components and rolls if needed
Yearly:
- Complete inspection of frame, rolls, motors
- Replace worn components like bearings, seals
- Upgrade machine parts or software if needed
Proper maintenance as per above schedule and machine manual guidelines will maximize post roll forming machine lifetime and performance.
Choosing a Post Roll Forming Machine Manufacturer
Selecting the right manufacturer is crucial for getting a high performance roll forming machine suiting your needs:
Key Evaluation Criteria
- Years of experience in roll forming equipment
- Variety of profiles capable of producing
- Use of quality materials and components
- Level of customization offered
- Design innovation and advanced features
- Compliance with safety standards
- Responsive pre-sales technical support
- Professional installation and operator training
- Maintenance and service capability
- Long term spare parts availability
- Competitive pricing and product warranty
Performing due diligence across above parameters will help identify the best roll forming partner for your production requirements and long term success.
Cost Analysis of Post Roll Forming Machines
Post roll forming machine cost depends on factors like:
- Frame size and capacity
- Number of roll forming stations
- Level of automation and additional features
- Material of construction
- Production speed and output
- Manufacturer’s brand and location
Typical price range:
Machine Capacity | Price Range |
---|---|
Manual and semi-automatic lines | $40,000 to $60,000 |
Medium duty roll forming lines | $60,000 to $150,000 |
High speed and automated lines | $150,000 to $500,000 |
Heavy duty lines for high strength materials | $500,000 to $2,000,000 |
Auxiliary equipment like decoilers, shears, stackers add $20,000 to $60,000 typically.
Installation, shipping and training can cost 15-25% extra depending on location and scope.
After-sales service contracts are around 5-10% of machine cost per year.
Selecting higher capacity, automated lines from premium brands understandably costs more compared to basic roll forming solutions. But the increased investment pays off via higher production, efficiency, precision and lower operating costs.
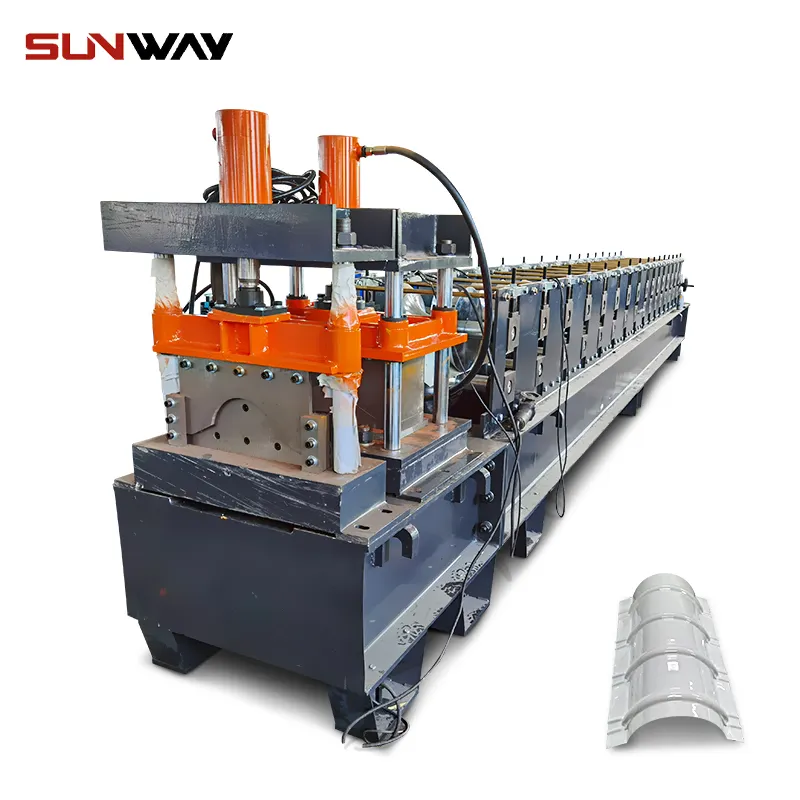
Pros and Cons of Post Roll Forming Machines
Advantages
- Highly flexible process capable of intricate profile shapes
- Consistent quality with close dimensional tolerance
- High production speeds and volumes
- Low tooling cost vs other processes
- Quick profile changeover using modular tooling
- Compact footprint saves factory space
- Wide range of materials can be formed including advanced high strength steels
- Lower scrap loss since coils are gradually formed
- Automated production improves safety and reduces labor
Limitations
- Initial machine investment is higher for automated lines
- Design complexity increases for certain exotic profiles
- Not ideal for small batch or prototype production
- Roll design requires expertise and experience
- Regular maintenance needed to sustain performance
- Limited ability to form symmetric profiles
While post roll forming has some drawbacks, its numerous benefits make it a valuable fabrication process suitable for long production runs of metal parts across many industries.
FAQ
Q: What materials can be post roll formed?
Post roll forming machines can produce profiles from:
- Low carbon steel
- High strength steel
- Stainless steel
- Aluminum
- Copper
- Brass
Range is 0.3 mm to 4 mm thickness for metals with good ductility.
Q: What tolerances are achievable?
Standard roll forming can achieve:
- Profile length tolerance ± 1 mm
- Cut length tolerance ± 2 mm
- Bow tolerance ± 1 mm per 1000 mm length
With high precision tooling and machines, tolerances of ± 0.5 mm are possible.
Q: How quick are profile changeovers?
Changeover time depends on roll forming line complexity:
- Basic machines: 1 to 2 hours
- Quick change systems: 30 mins to 1 hour
- Fully automated lines: 15 to 30 mins
So investing in quick change modular tooling minimizes changeover delays.
Q: What affects the price of post roll forming machines?
Major factors influencing cost:
- Production speed and output requirements
- Level of automation
- Advanced features like quick changeover
- Raw material thickness and strength
- Precision and tolerance levels
- Reputation of manufacturer
Higher capacity, faster and automated lines understandably cost more.
Q: What safety aspects should be considered?
Critical safety features include:
- Interlocked physical guards and barriers
- Emergency stop buttons within easy reach
- Warning lights, alarms and visual indicators
- Sensors to detect jams or misalignment
- Equipment compliance with safety standards
- Proper staff training on procedures
This minimizes potential hazards in the roll forming process.
Q: What are common roll formed profiles?
Common shapes produced include:
- C and U channels
- Zed and sigma sections
- Angles and L profiles
- Panels with ribs and corrugations
- Box and rectangular tube sections
- Curved and round tube profiles
- Special sections like highway guardrails
Profile possibilities are endless based on your product design needs.
Q: How to minimize roll tooling costs?
Strategies to reduce tooling expenses:
- Standardize profiles for multiple uses if possible
- Opt for movable post machines to reuse some stands
- Use modular tooling that allows roll segments to be rearranged
- Store tooling properly for reuse on future orders
- Work with tooling supplier to optimize design
- Build in-house tooling expertise for cost effective fabrication
Above methods help lower overall tooling investment.
Conclusion
Post roll forming is a versatile, accurate and productive method to form metal profiles continuously from coils. It offers significant advantages for long production runs across diverse applications.
This guide covers all aspects from working principle, types of machines, key components, specifications, applications, benefits, costs and more. It provides a detailed overview of the roll forming process using tables to compare different factors. Critical considerations are presented to help select the ideal post roll forming equipment according to your manufacturing needs and budget.