Roll forming technology enables rapid mass production of highway crash barriers in various steel grades cost-efficiently. This guide covers highway crash barrier roll forming machine types produced by roll formers, working principles, key machine components, installation guidelines, maintenance factors, leading global manufacturers, and typical end-use case comparisons.
highway crash barrier roll forming machine
Barrier Type | Key Attributes | Typical Materials |
---|---|---|
W-beam | Corrugated broad waves | Galvanized steel |
Thrie-beam | Added center ridge | Corten steel |
Single slope | Inward 30° angle | Hot rolled steel |
Vertical wall | Perpendicular sides | Stainless steel |
Box-beam rails | Hollow tubular | Structural steel |
Roll formed highway barriers accommodate vehicle impacts safely while providing aesthetic finish.
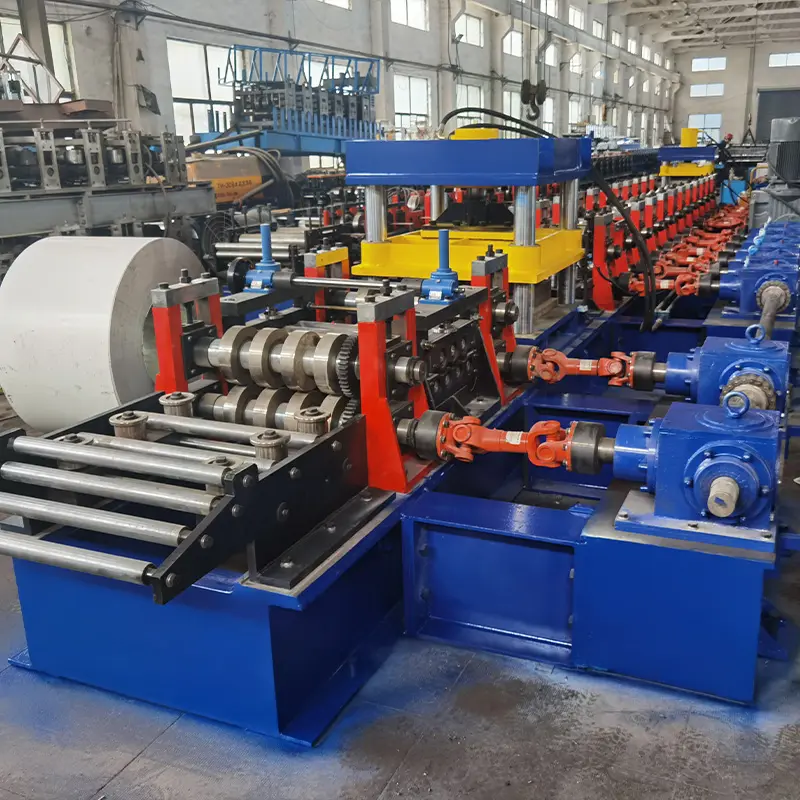
Working Principle of Roll Forming Process
Continuous forming from coil stock into barrier profiles achieved through sequential bending and shaping by matching upper and lower roller dies synchronously. Key aspects:
- Programmable roller inserts for defined rib geometries
- Strategic positioning of material grain flow
- Automatic edge guidance and gauging
- Supporting straightener/decoilers
- Flying shear cutoff saw length control
- Exit transfer tables, stackers
Entire part profile generated through incremental bending steps in one pass when roll feeds optimized.
Key Components of Highway Barrier Roll Forming Machine
Component | Role |
---|---|
Decoiler | Feeds raw steel coil stock |
Joining welder | Links coil ends for continuous input |
Entry guides | Align strip before dies |
Forming stations | Gradually impart profile |
Hydraulic system | Controls roller actuation |
Controller | Handles production logic |
Exit conveyor | Transfers finished barriers downstream |
Standardized modular designs allow upgrading machine width/speed capabilities.
Installation Best Practices
Activity | Guidelines |
---|---|
Incoming inspection | Validate drives, controls, safeties |
Positioning | Level, plumbed foundations |
Layout | Rear access considered for maintenance |
Connections | Power drops, conduits |
Trial runs | Confirm die clearances |
Programming | Template recipes for each profile |
Utilize factory technicians to streamline commissioning and maximize uptime productivity faster.
-
Electrical Cabinet Frame Roll Forming Machine
-
Din Rail Roll Forming Machine
-
Cable Ladder Roll Forming Machine
-
PV Mounting Bracket C Shape Profile Roll Forming Machine
-
Cable Tray Roll Forming Machine
-
PV Mounting Bracket Roll Forming Machine (HAT / Omega Profile)
-
PV Mounting Bracket Z Shape Profile Roll Forming Machine
-
Solar mounting strut channel roll forming machine
-
Strut Channel Roll Forming Machine
Operation and Maintenance Factors
Schedule | Tasks |
---|---|
Daily | Verify roller lubrication |
Weekly | Inspect belt tensions, guides |
Monthly | Check hydraulic leaks |
Quarterly | Electrical terminations |
Yearly | Bearing replacement |
Keep historical records of all production metrics including length inspection data, stops analysis and mean time between failures tracking to prioritize reliability-centered maintenance.
Considerations When Buying Highway Barrier Roll Forming Equipment
Factor | Evaluation Criteria |
---|---|
Production rate | Linear feet per hour rate |
Material grades | Hot rolled, Corten etc |
Profile range | Barrier variants required |
Accuracy | Rib sequencing, length tolerance |
Automation level | Degree of manual operation |
Runtime guarantees | Mean time between failures |
Delivery terms | Install schedules |
Training included | Operator familiarization scope |
Request machine tolerance capabilities report from vendors during purchase considerations.
Comparative Analysis of Major Highway Barrier Roll Former Manufacturers
Company | Accuracy | Lead Time | Cost |
---|---|---|---|
Metform | Very good | 12 weeks | Medium |
Roll Force | Excellent | 16 weeks | Higher |
EWMenn | Good | 10 weeks | Lower |
Gasparini SpA | Very good | 14 weeks | Higher |
DAHe | Good | 8 weeks | Lower |
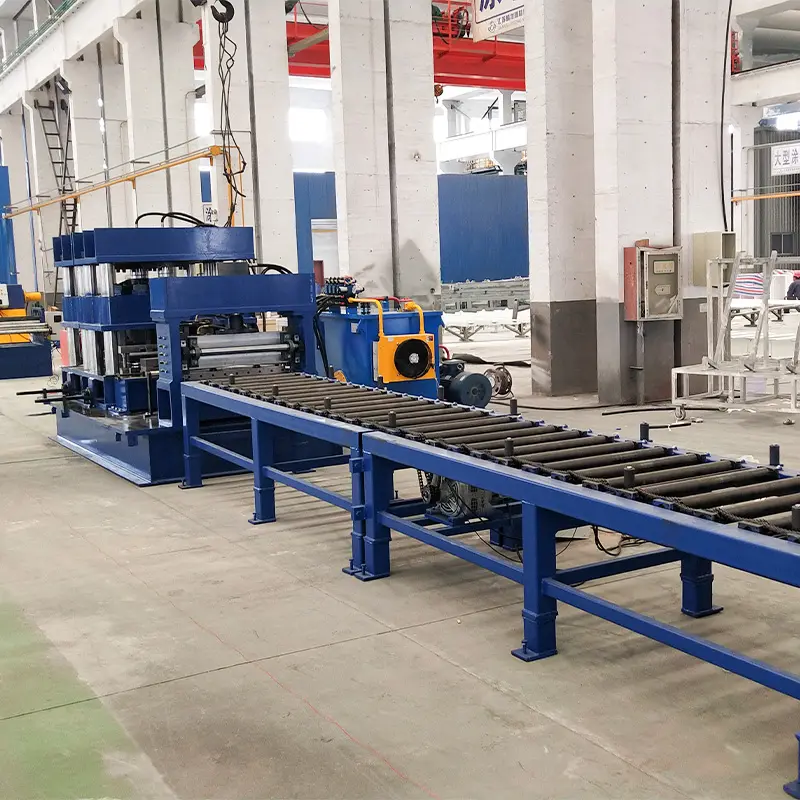
Advantages and Limitations
Pros | Cons |
---|---|
Rapid mass production | High initial tooling expense |
Lower operating costs | Specialist operator experience |
Consistent end product quality | Substantial foundations needed |
Range of hardware integration | Large production footprint |
Cost efficiency at volume | After-sales service accessibility |
Leverage mass production economies only at full utilization rates through careful regional demand planning.
FAQ
What thickness range can these machines handle typically?
Most standard lines proficiently process 1.5 mm to 4 mm thickness steels. Thicker plates require heavier presses and custom roller tooling design. Aluminum much easier to form.
What determines maximum production line speed?
Motor drive power ratings, press tonnage capabilities, decoiler capacities and downstream handling rates govern peak throughput tempo. Vendor technical proposal should provide speed calculations.
How quick are profile changeovers?
2-3 day changeover typical for skilled technicians to switch barrier profile roller sets for similar ribbon steel widths. Reduce changeover times through modular machine design.
What degree of length accuracy is held?
Precision cutoff presses with stepping motor control and rigid framing maintain under 5 mm length tolerance capability at top production speeds.
How should appropriate lubricants be selected?
Consult lubricant vendor to match fluids, oils and greases to operational pressures, temperatures, material specs and ambient conditions to maximize equipment lifespan while preventing contamination.
Conclusion
In closing, optimized highway barrier roll forming equipment delivers productive interstate safety infrastructure buildouts combining high operational efficiencies with precision quality control essential for national transportation modernization initiatives. Careful demand planning and reliability-focused maintenance practices ensure maximum line utilization.