gypsum channel roll forming machine produce lightweight Channel-U and C-shaped metal stud profiles from coiled galvanized steel used to construct interior walls and partitions across residential and commercial building projects. Optimized roll forming allows high speed fabrication of straight and curved gypsum channel members meeting architectural specifications.
This guide covers common channel product dimensions, workings of gypsum roll former configurations, quality assurance, applications and considerations when investing in channel profile roll forming equipment.
Typical Formed Stud Product Specifications
Attribute | Range |
---|---|
Web width | 35 to 300mm |
Flange width | 30 to 43mm |
Height | 51mm to 254mm |
Metal thickness | 0.46mm to 0.86mm (20ga – 14ga) |
Coating | G-40 galvanized; G-60 hot dip options |
Channel stud styles and steel material thickness tolerance align with gauge design parameters from stud manufacturers.
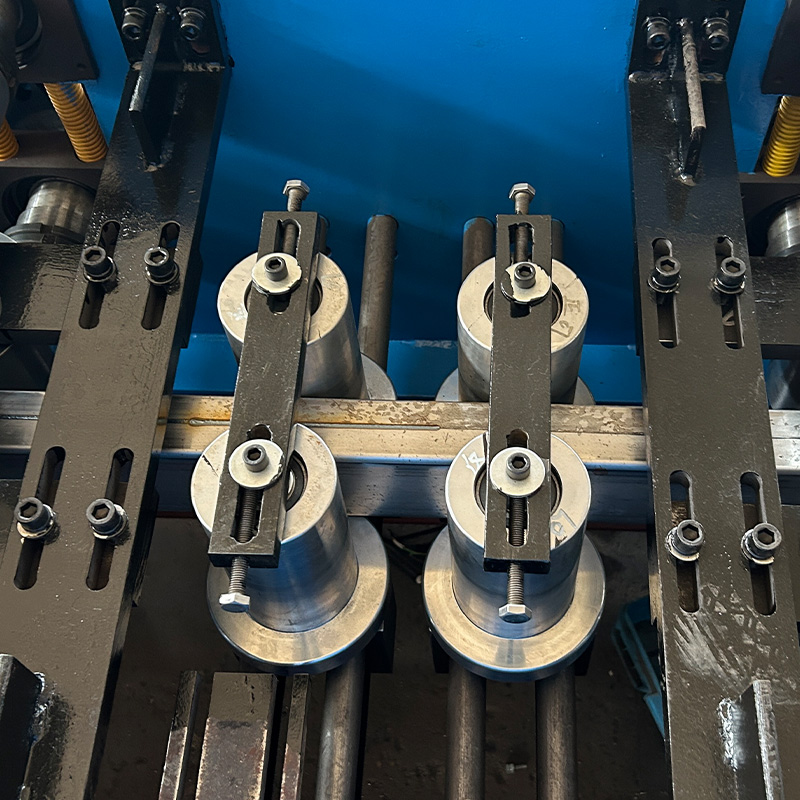
Working Principle of gypsum channel roll forming machine
Key roll forming stages
- Decoiling – Sheet steel loaded on payoff reel
- Feeding – Feed rollers engage and pull metal sheet into dies
- Pre-cutting – Transverse cut-off shears slices blanks
- Roll forming – Gradually bending through a series of stations into C-profile
- Punching – Pierce mounting slots spaced periodically
- Final cutoff – Pre-configured lengths sliced by rotary shear
- Counting stacker – Collects pre-set number of pieces
Coordinate punch placements, shear cycles and exit conveyors with precision feeding of coil optimizing production rates to target straightness and dimensional tolerances.
Equipment Types
Machine | Description |
---|---|
Standard | 10-12 roll stations, 600-800kN, basic controls |
Servo Electric | Independent AC servo roll drives for speed changes, precision gaging |
Hybrid Configurations | Optimized mechanical/servo roll sets for productivity vs precision |
Select machinery automation factors based on annual volumes matching quality level needed for stud framing application areas.
Roll Former Components
- Decoiler/feeder – Programmable loop control
- Feed table – Powered rollers with scale, gage stop
- Roll housing units – Height adjustable bearing chocks
- Bending roll sets – Hardened durable tool steel rolls
- Punching unit – Indexing piercing, slotting sections
- Transverse shear – Pre-cut blanks before forming
- Rotary shear – Slices to length at production speed
- Exit conveyor tables – Transfer finished goods
- Control station – Touchscreen HMI stores recipes
Review manufacturing and calibration certifications on key assemblies directly impacting product quality and changeover repeatability.
-
Electrical Cabinet Frame Roll Forming Machine
-
Din Rail Roll Forming Machine
-
Cable Ladder Roll Forming Machine
-
PV Mounting Bracket C Shape Profile Roll Forming Machine
-
Cable Tray Roll Forming Machine
-
PV Mounting Bracket Roll Forming Machine (HAT / Omega Profile)
-
PV Mounting Bracket Z Shape Profile Roll Forming Machine
-
Solar mounting strut channel roll forming machine
-
Strut Channel Roll Forming Machine
Popular Channel Stud Roll Former Layout
- Decoiler
- Feed unit
- Blanking shear
- 10-12 Progressive roll stations
- Punching press – periodic slotting
- Flying rotary shear
- Exit tables, conveyor
- Control desk
Optional integrated finishing
- Punching holes, notching
- Hole countersinking
- Special profile embossing
- Custom part stamping
Tailor gypsum channel machining capabilities to match capacity needs optimizing production design.
Machine Customization Factors
Parameter | Options |
---|---|
Forming Length | 6 – 12 meter standard based on profiles |
Maximum Line Speed | 60 meters per minute |
Web Width Range | 35mm to 300 mm+ within same line |
Metal Thickness | 0.46mm to 0.86 mm (20 ga to 14 ga) |
Mounting Slot Styles | Round, square, diagonal, triangular etc |
Added Features | Hole punching, notching, embossing, beading |
Quick Roll Changes | Shaft couplers, tool receivers, preset gaging |
Secondary Operations | Auto-packing, sheet stackers, conveyors |
Discuss profile dimension variability, length accuracy needs and order changeover frequencies when specifying capabilities catering to future distribution center replenishments.
Production Quality Control Metrics
- Sample dimensional checks after changeovers
- Wall thickness consistency
- Channel straightness
- Punch placement alignment as per specs
- Member length accuracy
- Visual surface quality
- Packaging integrity checks
- Tagging and labeling
Follow applicable ASTM C645 standard test procedures validating key parameters on channel stud framing members.
Building Construction Application Areas
Residential, commercial and institutional segments utilize roll formed stud channels including:
- Wall framing, furring, shafts, partitions
- Modular housing, panelized assemblies
- Drywall and plaster ceilings
- Stud layouts needing short pieces
- Contour shaped frames, arches
- Curved wall segments
Optimized lightweight steel profiles assembled into essential structural interior framing and substrates for finishing.
Cost Considerations
- Machinery Capital – $80,000 to $300,000 baseline depending on automation level, speeds and forming width flexibility
- Tooling Costs – $2000+ per additional roll set for future profile variability
- Yearly Maintenance – ~2% of equipment cost
- Consumable Supplies – Coil stock, lubricants, power as operational expenses
Analyze total cost of equipment ownership over minimum 5 years when justifying return on investment from improved manufacturing productivity and minimizing external channel stud sourcing.
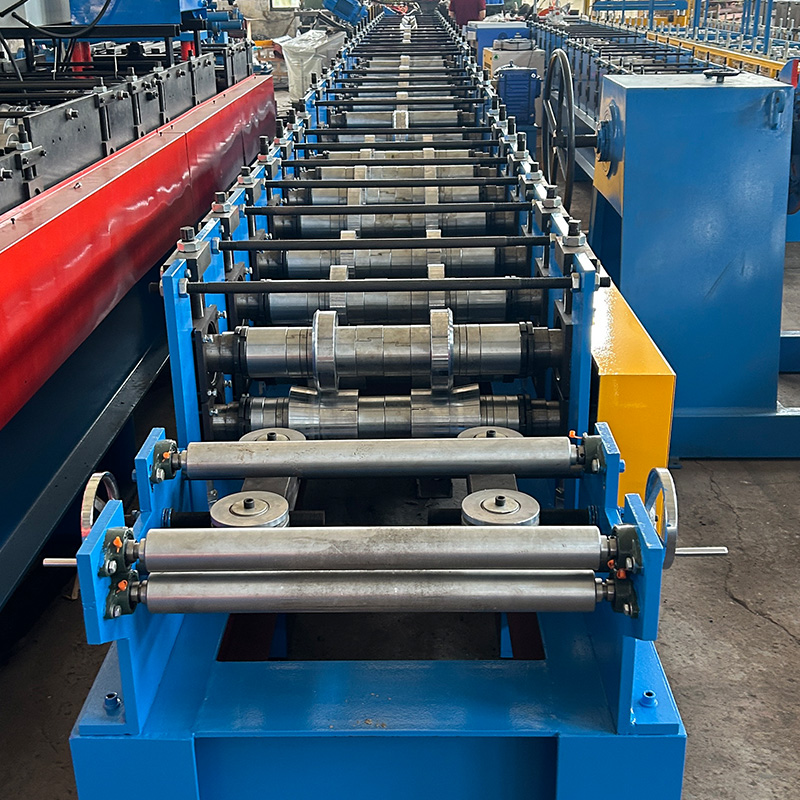
Purchasing Considerations
Parameter | Importance |
---|---|
Production Speed | High |
Quick Changeover | High |
Precision | Medium |
Cost Factors | Low |
FAQs
Q: What steel thickness is commonly used for roll formed gypsum channel studs?
A: Most residential framing uses 20 gauge (0.5mm) to 16 gauge (0.6mm) steel thickness. Commercial construction moves to 14 gauge (0.7mm) or heavier for greater structural strength to height ratios.
Q: What standards cover roll formed metal stud framing?
A: ASTM C645 standard covers materials, testing and tolerances. AWS D1.3 regulates welding. AISI S240 applies to steel grades. ICC IBC for building code compliance.
Q: How fast can a gypsum stud roll forming line operate?
A: Mechanical gypsum channel lines produce around 50 meters per minute enabling efficient distribution center replenishments. Servo electric machines with advanced controls can reach over 80m per minute with precision tolerances.
Q: How should stud roll tooling be maintained?
A: Tool steel bending rolls should be regularly cleaned and lubricated to prevent scratching. Inspect for any early hairline cracks needing replacement. Re-calibrate punching dies periodically. Hardened rollers may need offsite cryogenic retempering annually preventing longitudinal bowing.