Flying-shear roll forming machines utilize a unique cut-to-length system to boost efficiency in roll formed profile production. The flying shear mechanism shears the moving strip just before it enters the roll forming section.
Key details about flying-shear roll formers:
- Cut-to-length system integrated into roll former
- Rotary shear cuts moving strip at high speed
- Precise shear timing synchronized to line speed
- Permits faster overall line speeds
- Quick and easy size changes
- Used for metals up to 4mm thickness
- Ideal for producing parts in standard lengths
- Commonly used to make roofing panels, decking, and panels
By removing the stop-and-start action of typical end shears, flying shears optimize the roll forming process.
Types of flying-shear roll forming machine
Machine Type | Description |
---|---|
Mechanical | Shear timing via Geneva mechanism and servo drive |
Electronic | Shear controlled by PLC with encoder feedback |
Hydraulic | Hydraulic cylinder actuates shear at right moment |
Mechanical flying shears precisely time the cut mechanically for a simpler, economical design.
Electronic flying shears offer more flexibility and speed control through the system’s logic controller.
Hydraulic flying shears generate high shearing force while maintaining accurate timing.
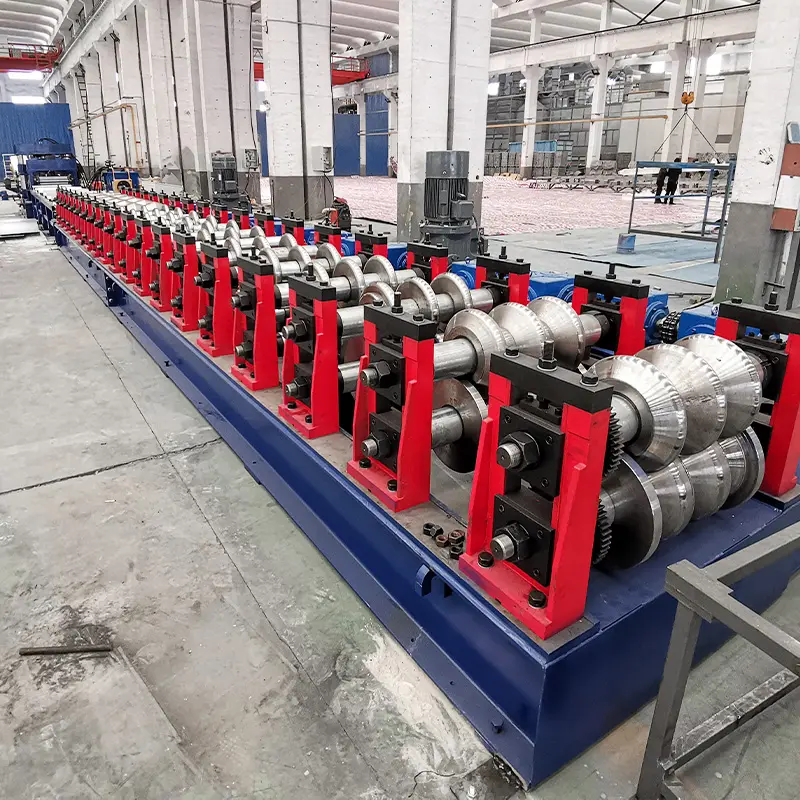
Key Components of Flying Shear Roll Formers
Component | Function |
---|---|
Decoiler | Feeds strip from coil into line under proper tension |
Roll Tooling | Forming stations gradually shape the strip |
Flying Shear | Rotary shear cuts moving strip at high speed |
Conveyor | Receives cut parts and discharges from line |
PLC Control | Coordinates decoiler, shear, conveyor, and monitoring |
Operator Interface | Touchscreen to control and adjust forming parameters |
Flying shears combine dynamic roll forming technology with synchronized high speed shearing for superior productivity.
Typical Applications of Flying Shear Roll Forming Lines
Products | Details |
---|---|
Roofing Panels | For standing seam, concealed fastener panels |
Siding and Cladding | Wall panels, architectural facades |
Decking | Roof deck, flooring panels |
Solar Frames | For solar panel mounting structures |
Shelving | Adjustable shelves, support beams |
Drainage Systems | Culverts, rain gutters, downspouts |
Flying shear roll formers are ideal for producing roofing, siding, decking, and numerous profiles in standard lengths.
Design Standards for Flying Shear Roll Forming Machines
Component | Standards |
---|---|
Frame | Rigid steel, stress-relieved welded construction |
Tooling | Hardened rolls, machined shafts, bearings |
Shear Blade | Hardened D2 steel, heat treated |
Shear Timing | Precise Geneva or electronic control |
Drives | Helical gearboxes or servo motors |
Controls | PLC, color touchscreen HMI |
Finishes | Primed then powder coated |
Safety | Fully enclosed guards, e-stops |
Robust framing matched with high quality components and smart controls result in reliable, consistent performance and end product quality.
Specifications of Flying Shear Roll Formers
Specification | Typical Values |
---|---|
Line Speed | 10 – 50 m/min |
Max Strip Width | 1000 – 1300 mm |
Thickness Capacity | 0.5 – 4 mm |
Length Tolerance | ± 1 mm |
Length Range | Any cut length |
Power | 30 – 75 kW |
Machine Weight | 5000 – 8000 kg |
Speeds, widths, and power requirements vary across mechanical, hydraulic, and electronic flying shear machine models.
Pricing Details for Flying Shear Roll Forming Equipment
Manufacturer | Price Range |
---|---|
Metform | $150,000 – $250,000 |
ETP | $140,000 – $220,000 |
Samco | $160,000 – $280,000 |
China manufacturers | $80,000 – $150,000 |
Prices range from $80,000 to $280,000 depending on size, features, and precision. Installation and shipping add 10-20%.
Installation and Commissioning of Flying Shear Machines
Task | Description |
---|---|
Site Preparation | Clear space, anchor bolts to foundation |
Lifting | Use appropriate lifting gear to offload sections |
Assembly | Bolt frame together; install components |
Alignment | Precision align and level all sections |
Electrical | Wire motors, PLC, controls, and accessories |
Conveyor | Bolt in feed and exit conveyors |
Test Run | Cycle slowly, inspect operation and cut parts |
Optimization | Refine shear timing, control parameters |
Proper installation and thorough testing ensures smooth startup and quality output from the machine.
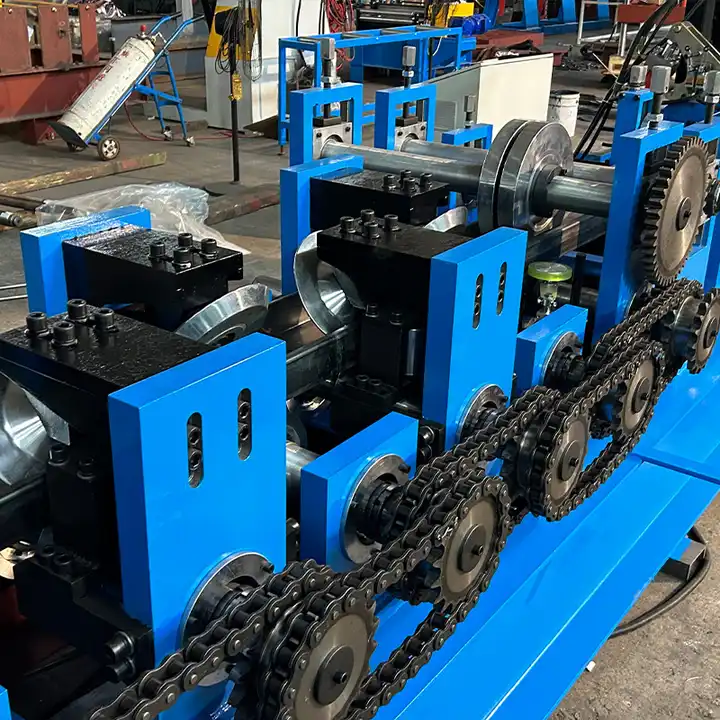
Operation and Maintenance of Flying Shear Roll Lines
Activity | Frequency |
---|---|
Safety Checks | Per shift |
Coil Loading | As needed |
Parameter Adjustment | As needed |
Blade Lubrication | Daily |
Blade Inspection | Weekly |
Bearing Lubrication | Monthly |
Hydraulic Service | Quarterly |
Gearbox Oil | Per manual |
Alignment | Annual |
Daily safety procedures must be followed. Careful operation and regular maintenance are vital for flying shear longevity and performance.
Selecting a Flying Shear Roll Former Manufacturer
Considerations | Guidance |
---|---|
Experience | Look for extensive background with flying shears |
Customization | Ability to tailor machine to application needs |
Support | Installation help, training, manuals, service |
Reputation | Choose established brand known for quality |
Delivery | Manufacturer can deliver on required schedule |
Value | Balance capabilities against price paid |
Consider expertise with this specialized equipment along with customization, support, and fair cost.
Benefits of Flying Shear Roll Forming Lines
- Faster production than standard roll former with end shear
- Precisely cut parts immediately off the roll former
- Quick and easy size changeovers
- Increased throughput from uninterrupted strip flow
- Ideal for producing profiles in standard lengths
- Consistent cut tolerance and quality
- Compact design minimizes space
- Lower labor requirements
- Ability to cut to length on the fly
- Simpler material handling
Key advantages include speed, changeover ease, consistency, and labor savings versus typical stop-and-cut systems.
Limitations of Flying Shear Roll Forming Technology
- Higher initial capital cost than standard roll formers
- Requires more maintenance and skilled operation
- Limited to thinner/softer material gauges
- Not as easy to cut non-standard length parts
- Precise alignment critical for smooth operation
- Timing mechanisms can wear over time
- Special tooling required for different profiles
- Can increase roll changing time during size changes
- Scrap generation during initial setup
The main limitations relate to higher cost and maintenance requirements versus basic roll formers.
Cost Comparison of Flying Shear vs End Shear Machines
Machine Type | Price Range | Benefits | Drawbacks |
---|---|---|---|
Flying Shear | $150,000 – $300,000 | Faster speeds, easy length changes | Higher cost, specialized maintenance |
End Shear | $100,000 – $200,000 | Lower initial cost, simple operation | Slow cut-to-length method |
Flying shears improve productivity but have higher capital and operating costs. Evaluate based on volume, changeovers, and budget.
Troubleshooting Issues with Flying Shear Roll Lines
Issue | Solution |
---|---|
Inaccurate shear timing | Adjust/replace worn gears; check encoder |
Blade wear | Rotate/replace shear blades |
Strip marks | Increase blade/roll hardness; adjust guides |
Hydraulic leaks | Replace seals, hoses, cylinders |
Excess vibration | Check alignment, mountings; repair as needed |
Electrical faults | Check/replace wires, connections, drives |
Proper blade maintenance along with swift repairs of leaks, looseness, or electrical problems prevents unplanned downtime.
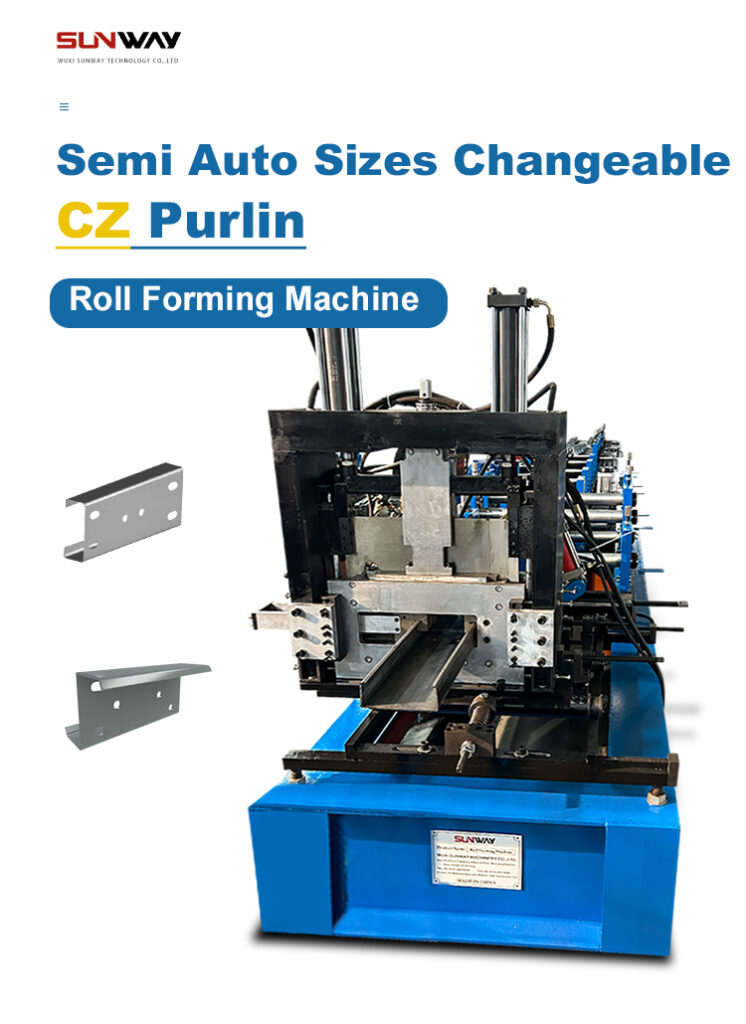
FAQ
Q: What thickness of steel can flying shears accommodate?
A: Most machines can handle up to 4 mm thickness. Heavier models are available for thicker material.
Q: How fast can flying shear roll formers operate?
A: Speeds range from 10 to over 50 meters per minute depending on machine size.
Q: What length parts can be produced?
A: Any cut length can be produced, though typical lengths are from 1 to 7 meters.
Q: How accurate are the cut lengths?
A: Precision flying shears can achieve a tolerance of ± 1 mm or better.
Q: How long does it take to change to a new profile?
A: With quick change tooling, profile changeover takes 30-60 minutes in general.
Q: What safety features are included?
A: Full guarding, e-stops, access interlocks, and control reliability per prevailing standards.
Q: What is the typical production lifetime of a machine?
A: Approximately 15-20 years of productive life can be expected with proper maintenance.
Q: What types of warranty are offered by manufacturers?
A: Warranty periods range from 6 months to 1 year on most components. Extended warranties may be purchased.