Machines de profilage à cisaillement volant utilisent un système unique de coupe à la longueur pour améliorer l'efficacité de la production de profilés formés par laminage. Le mécanisme de cisaille volante cisaille la bande en mouvement juste avant qu'elle n'entre dans la section de profilage.
Détails clés sur les profileuses à cisaillement volant :
- Système de coupe à longueur intégré à la profileuse
- La cisaille rotative coupe la bande mobile à grande vitesse
- Temps de cisaillement précis synchronisé avec la vitesse de la ligne
- Permet des vitesses de ligne globales plus rapides
- Changements de taille rapides et faciles
- Utilisé pour les métaux jusqu'à 4 mm d'épaisseur
- Idéal pour la production de pièces de longueur standard
- Couramment utilisé pour fabriquer des panneaux de toiture, des terrasses et des panneaux.
En supprimant l'action d'arrêt et de démarrage des cisailles d'extrémité typiques, les cisailles volantes optimisent le processus de formage des cylindres.
Types de profileuses à cisaillement volant
Type de machine | Description |
---|---|
Mécanique | Temporisation du cisaillement par le mécanisme de Genève et l'entraînement par servomoteur |
Électronique | Cisaillement contrôlé par PLC avec retour d'information par encodeur |
Hydraulique | Le vérin hydraulique actionne la cisaille au bon moment |
Cisailles volantes mécaniques chronométrer précisément la coupe mécaniquement pour une conception plus simple et plus économique.
Cisailles électroniques offrent une plus grande flexibilité et un contrôle de la vitesse par le biais du contrôleur logique du système.
Cisailles volantes hydrauliques générer une force de cisaillement élevée tout en maintenant une synchronisation précise.
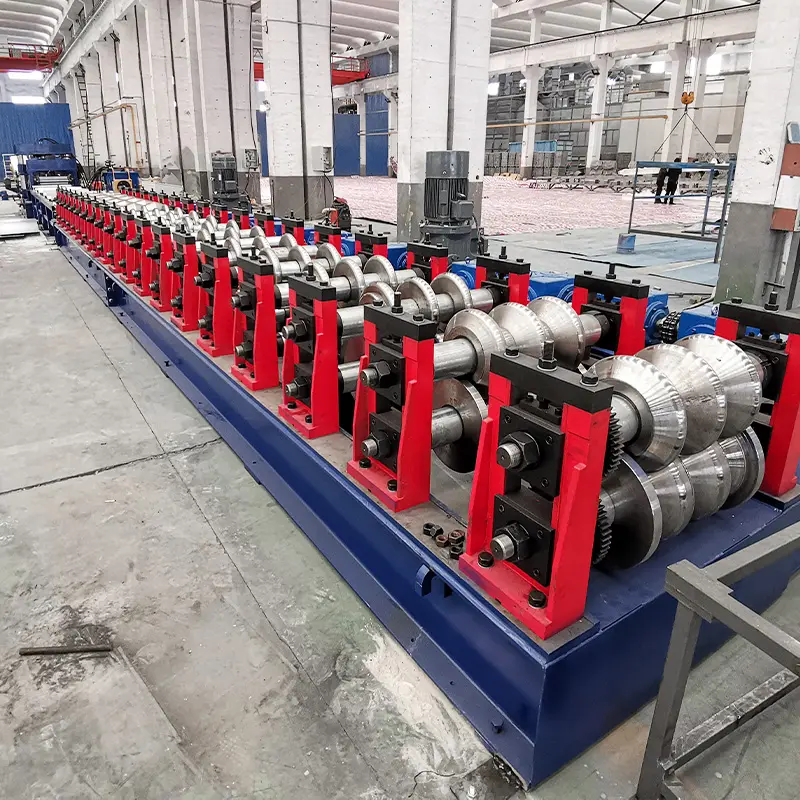
Composants clés des laminoirs à cisaillement volant
Composant | Fonction |
---|---|
Dérouleur | Introduit la bande de la bobine dans la ligne sous une tension appropriée |
Outil de roulage | Les stations de formage façonnent progressivement la bande |
Cisaille volante | La cisaille rotative coupe la bande mobile à grande vitesse |
Convoyeur | Réceptionne les pièces coupées et les décharge de la ligne |
Contrôle PLC | Coordonne le dérouleur, la cisaille, le convoyeur et la surveillance. |
Interface opérateur | Écran tactile pour contrôler et ajuster les paramètres de formage |
Les cisailles volantes combinent la technologie du profilage dynamique avec un cisaillage synchronisé à grande vitesse pour une productivité supérieure.
Applications typiques des lignes de profilage à cisaillement volant
Produits | Détails |
---|---|
Panneaux de toiture | Pour les panneaux à joint debout et à attaches dissimulées |
Bardage et revêtement | Panneaux muraux, façades architecturales |
Plancher | Toit-terrasse, panneaux de revêtement de sol |
Cadres solaires | Pour les structures de montage de panneaux solaires |
Rayonnage | Étagères réglables, poutres de soutien |
Systèmes de drainage | Ponceaux, gouttières, tuyaux de descente |
Les profileuses à cisaillement volant sont idéales pour la production de toitures, de bardages, de terrasses et de nombreux profilés en longueurs standard.
Normes de conception des profileuses à cisaillement volant
Composant | Normes |
---|---|
Cadre | Construction rigide en acier, soudée sans contrainte |
Outillage | Rouleaux trempés, arbres usinés, roulements |
Lame de cisaillement | Acier D2 trempé, traité thermiquement |
Temps de cisaillement | Contrôle précis à Genève ou électronique |
Entraînements | Réducteurs à engrenages hélicoïdaux ou servomoteurs |
Contrôles | PLC, IHM à écran tactile couleur |
Finitions | Apprêt puis revêtement en poudre |
Sécurité | Protecteurs entièrement fermés, e-stops |
Une structure robuste associée à des composants de haute qualité et à des commandes intelligentes permet d'obtenir des performances fiables et constantes ainsi qu'un produit final de qualité.
Spécifications des laminoirs à cisaillement volant
Spécifications | Valeurs typiques |
---|---|
Vitesse de la ligne | 10 - 50 m/min |
Largeur maximale de la bande | 1000 - 1300 mm |
Épaisseur Capacité | 0,5 - 4 mm |
Tolérance de longueur | ± 1 mm |
Longueur Plage | Toute longueur de coupe |
Puissance | 30 - 75 kW |
Poids de la machine | 5000 - 8000 kg |
Les vitesses, les largeurs et les besoins en énergie varient selon les modèles de cisailles volantes mécaniques, hydrauliques et électroniques.
Détails des prix pour Cisaille volante - Equipement de formage de rouleaux
Fabricant | Fourchette de prix |
---|---|
Metform | $150,000 – $250,000 |
PTE | $140,000 – $220,000 |
Samco | $160,000 – $280,000 |
Fabricants chinois | $80,000 – $150,000 |
Les prix varient de $80 000 à $280 000 en fonction de la taille, des caractéristiques et de la précision. Les frais d'installation et d'expédition s'élèvent à 10-20%.
Installation et mise en service de cisailles volantes
Tâche | Description |
---|---|
Préparation du site | Dégager l'espace, ancrer les boulons à la fondation |
Levage | Utiliser des engins de levage appropriés pour décharger les sections |
Assemblée | Boulonner le cadre ; installer les composants |
Alignement | Alignement et nivellement de précision de toutes les sections |
Électricité | Câbler les moteurs, les automates, les commandes et les accessoires |
Convoyeur | Convoyeurs d'alimentation et de sortie à boulons |
Test de fonctionnement | Cycle lent, contrôle du fonctionnement et découpe des pièces |
Optimisation | Affiner le temps de cisaillement et les paramètres de contrôle |
Une installation correcte et des tests approfondis garantissent un démarrage en douceur et un rendement de qualité de la machine.
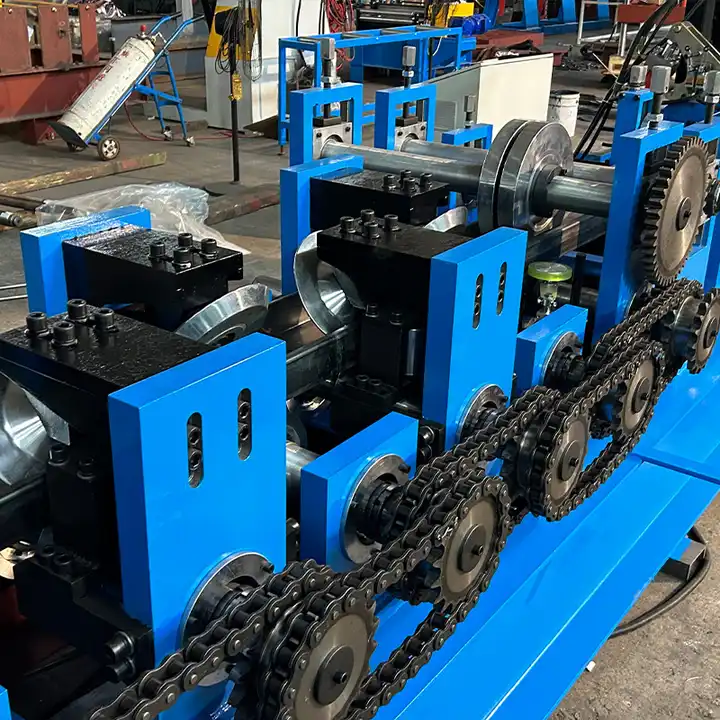
Fonctionnement et entretien des lignes de cisaillement à rouleaux volants
Activité | Fréquence |
---|---|
Contrôles de sécurité | Par équipe |
Chargement de la bobine | Selon les besoins |
Réglage des paramètres | Selon les besoins |
Lubrification des lames | Quotidiennement |
Inspection des lames | Hebdomadaire |
Lubrification des roulements | Mensuel |
Service hydraulique | Trimestrielle |
Huile de boîte de vitesses | Par manuel |
Alignement | Annuel |
Les procédures de sécurité quotidiennes doivent être respectées. Une utilisation prudente et un entretien régulier sont essentiels pour assurer la longévité et les performances de la cisaille volante.
Sélection d'un fabricant de profileuses à cisaillement volant
Considérations | Orientations |
---|---|
Vivre | Recherchez une expérience approfondie avec les cisailles volantes |
Personnalisation | Possibilité d'adapter la machine aux besoins de l'application |
Soutien | Aide à l'installation, formation, manuels, service |
Réputation | Choisir une marque reconnue pour sa qualité |
Livraison | Le fabricant peut livrer dans les délais requis |
Valeur | Mettre en balance les capacités et le prix payé |
Tenez compte de l'expertise de cet équipement spécialisé ainsi que de la personnalisation, de l'assistance et du coût équitable.
Avantages des lignes de profilage à cisaillement volant
- Production plus rapide qu'une profileuse standard avec cisaille d'extrémité
- Des pièces coupées avec précision dès la sortie de la formeuse
- Changements de taille rapides et faciles
- Augmentation du débit grâce à une circulation ininterrompue des bandes
- Idéal pour la production de profils en longueurs standard
- Tolérance et qualité de coupe constantes
- Conception compacte minimisant l'espace
- Besoins en main-d'œuvre réduits
- Possibilité de couper la longueur à la volée
- Une manutention plus simple
Les principaux avantages sont la vitesse, la facilité de changement, la cohérence et les économies de main-d'œuvre par rapport aux systèmes de coupe et d'arrêt classiques.
Limites de la technologie de formage par cisaillement volant
- Coût d'investissement initial plus élevé que celui des profileuses standard
- Nécessite plus d'entretien et de compétences
- Limité aux matériaux les plus fins et les plus tendres
- Il n'est pas aussi facile de couper des pièces de longueur non standard
- Un alignement précis est essentiel pour un fonctionnement sans heurts
- Les mécanismes de synchronisation peuvent s'user avec le temps
- Un outillage spécial est nécessaire pour les différents profils
- Peut augmenter le temps de changement de rouleau lors des changements de taille
- Production de déchets lors de l'installation initiale
Les principales limitations sont liées au coût plus élevé et aux exigences de maintenance par rapport aux profileuses à rouleaux de base.
Comparaison des coûts des cisailles volantes et des cisailles d'extrémité
Type de machine | Fourchette de prix | Avantages | Inconvénients |
---|---|---|---|
Cisaille volante | $150,000 – $300,000 | Des vitesses plus rapides, des changements de longueur faciles | Coût plus élevé, entretien spécialisé |
Cisaillement d'extrémité | $100,000 – $200,000 | Coût initial réduit, fonctionnement simple | Méthode de coupe lente |
Les cisailles volantes améliorent la productivité mais ont des coûts d'investissement et d'exploitation plus élevés. L'évaluation doit se faire en fonction du volume, des changements et du budget.
Résolution des problèmes liés aux lignes de laminage à cisaillement volant
Enjeu | Solution |
---|---|
Temps de cisaillement imprécis | Ajuster/remplacer les engrenages usés ; vérifier l'encodeur |
Usure de la lame | Rotation/remplacement des lames de cisailles |
Marques de bandes | Augmenter la dureté de la lame/du rouleau ; ajuster les guides |
Fuites hydrauliques | Remplacer les joints, les tuyaux, les cylindres |
Excès de vibrations | Vérifier l'alignement, les fixations ; réparer si nécessaire |
Défauts électriques | Vérifier/remplacer les fils, les connexions, les entraînements |
L'entretien adéquat des lames et la réparation rapide des fuites, du relâchement ou des problèmes électriques permettent d'éviter les temps d'arrêt imprévus.
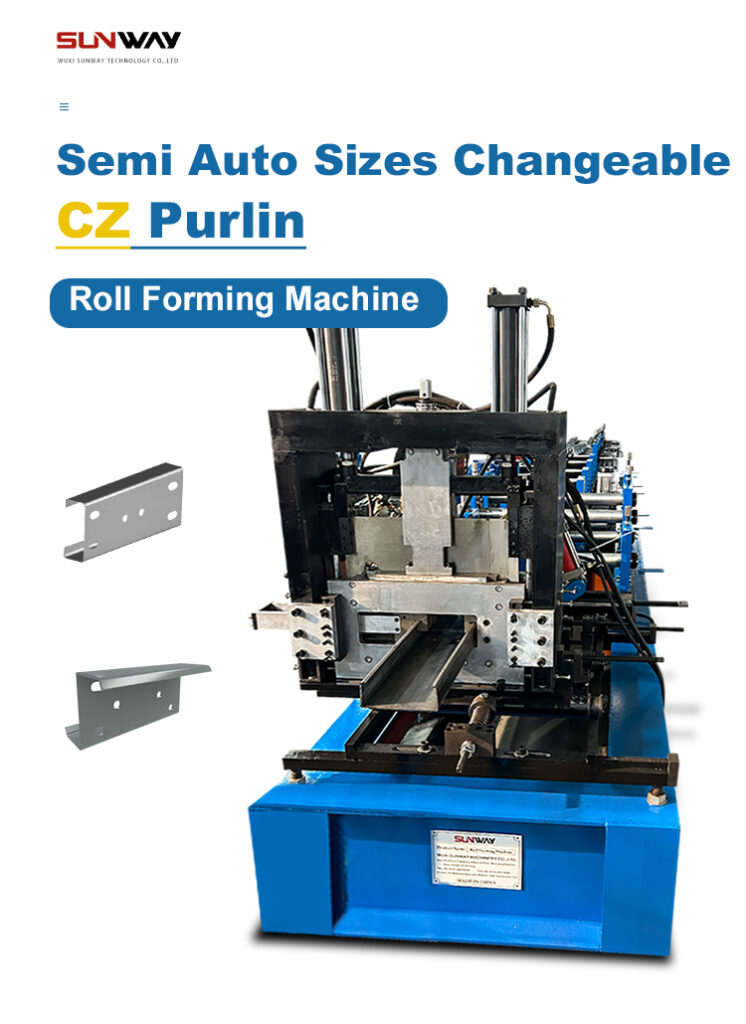
FAQ
Q : Quelle épaisseur d'acier les cisailles volantes peuvent-elles accepter ?
R : La plupart des machines peuvent traiter jusqu'à 4 mm d'épaisseur. Des modèles plus lourds sont disponibles pour les matériaux plus épais.
Q : À quelle vitesse les rouleaux de cisaillement volants peuvent-ils fonctionner ?
R : Les vitesses varient de 10 à plus de 50 mètres par minute en fonction de la taille de la machine.
Q : Quelle est la longueur des pièces qui peuvent être produites ?
R : Toutes les longueurs de coupe peuvent être produites, mais les longueurs habituelles sont comprises entre 1 et 7 mètres.
Q : Quelle est la précision des longueurs coupées ?
R : Les cisailles volantes de précision peuvent atteindre une tolérance de ± 1 mm ou mieux.
Q : Combien de temps faut-il pour passer à un nouveau profil ?
R : Avec l'outillage à changement rapide, le changement de profil prend en général 30 à 60 minutes.
Q : Quels sont les dispositifs de sécurité inclus ?
A : Protection complète, arrêts d'urgence, verrouillages d'accès et fiabilité des contrôles conformément aux normes en vigueur.
Q : Quelle est la durée de vie typique d'une machine ?
R : On peut s'attendre à une durée de vie productive d'environ 15 à 20 ans avec un entretien adéquat.
Q : Quels sont les types de garantie offerts par les fabricants ?
R : Les périodes de garantie vont de 6 mois à 1 an pour la plupart des composants. Il est possible d'acheter des extensions de garantie.