An electric cabinet frame machine is an important piece of equipment used to manufacture metal cabinet enclosures and racks for electronic controls, switchgears, distribution boards, and automation systems. This comprehensive guide provides key details about electric cabinet frame machines.
Overview
Electric cabinet frame machines, also known as roll formers or bending machines, automate the process of shaping metal sheets into custom cabinet frames and enclosures through a series of bending, punching, cutting, and rolling operations.
They offer an efficient alternative to manual metal fabrication, enabling high productivity and consistency in producing cabinets of various sizes with different structural designs to meet safety and electrical standards. Modern electric frame machines include programmable controls and touchscreen interfaces for flexible and precise fabrication.
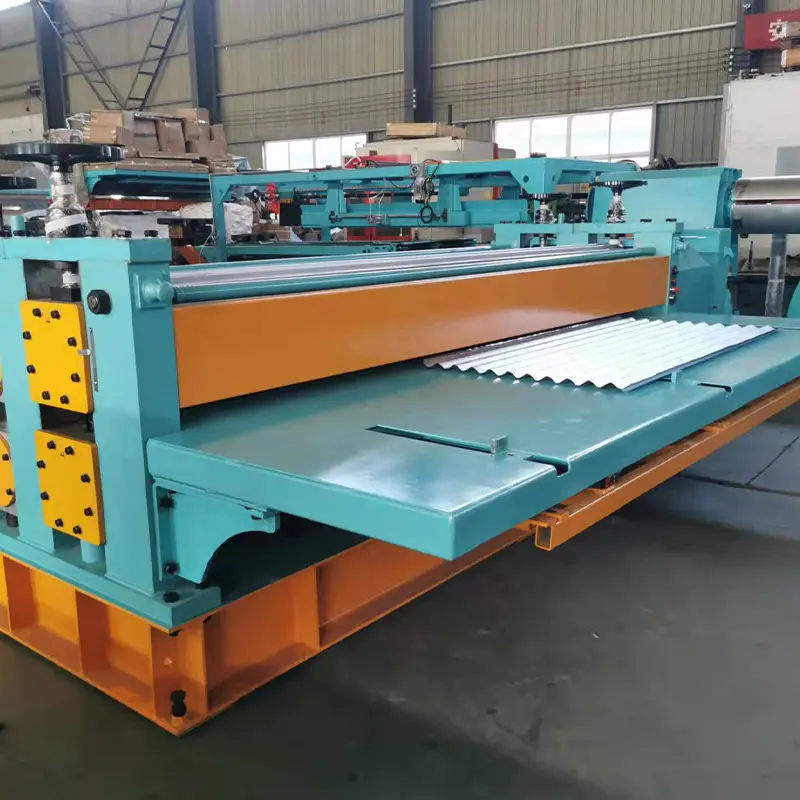
Main Components
The major components of an electric cabinet frame machine include:
- Feeding mechanism – Auto-feeds raw metal coil/sheets
- Roll forming stations – Forms bends through an arrangement of rollers
- Punching unit – Punches holes for rivets and cables
- Shearing blade – Trims sheets to required cabinet size
- Controller – Controls machine parameters and production flow
Working Process
The typical working process on an electric cabinet frame machine involves:
- Loading raw metal sheet or coil
- Feeding material through sets of rollers and bend stations
- Forming structural bends and rolls as required
- Punching/cutting electrical cabling holes
- Shearing final enclosure frame to dimensions
- Unloading finished cabinet carcass
Types of Electric Cabinet Frame Machines
Type | Description |
---|---|
Roll forming | Utilizes sets of rollers to progressively bend metal sheets into custom profiles |
Press brake | Uses a powered press to produce accurate bends and folds |
CNC Folder | Computer numerically controlled (CNC) folding machine for intricate designs |
Hybrid | Combines multiple processes like rolling, bending, punching |
-
Vineyard Post Roll Forming Machine
-
Auto Size Changeable Sigma Purlin Roll Forming Machine
-
Auto Size Changeable C Z Purlin Roll Forming Machine
-
Auto Size Changeable Z Purlin Roll Forming Machine
-
Auto Size Changeable C U Purlin Roll Forming Machine
-
PV Mounting Bracket C Shape Profile Roll Forming Machine
-
Light Keel Wall Angle Roll Forming Machine Protector Corners Wall Angle Forming Machine
-
Light Keel Corner Bead Making Machine V Keel Angle Iron Roll Forming Machine
-
Full Automatic C Z Purlin Machine Steel Metal Former Frame & Purlin Machines
Typical Specifications
Parameter | Range |
---|---|
Forming Length | 1 – 6 m |
Metal Thickness | 0.5 – 2 mm |
Forming Speed | 10 – 15 m/min |
Punching Stations | Up to 20 |
Installed Power | 15 – 75 kW |
Working Principle
The working principle involves feeding a metal sheet or coil through various fabrication stations to shape it into a finished cabinet frame. The material gets formed into custom bends and profiles through an arrangement of rollers, while holes get punched by pneumatic rams. Finally, a shearing blade cuts the frame to the exact size required.
Industrial Applications
Electric cabinet frame machines enable efficient mass production of enclosures for:
- Power distribution boards
- Motor control centers
- Switchgears and control panels
- Operator interfaces and consoles
- Battery racks and chargers
- Instrumentation cubicles
- Automation system cabinets
Buying Considerations
While choosing an electric cabinet frame machine, some key factors to consider include:
Fabrication Flexibility : Ability to produce various bending designs and enclosures of different sizes
Control and Automation
: Ease of programming and integrating with other metalworking machines
Precision and Repeatability : Consistent and accurate frame production with tolerance of ±0.1 mm
Safety Features : Light curtains, emergency stops, safety guards for operator protection
Post-sales Service : Machine installation support, responsive after-sales service
Operational Efficiency : Reduce set-up times, downtimes and material wastage
Total Cost of Ownership
: Consider purchasing, operating and maintenance costs
Suppliers and Pricing
Supplier | Starting Price Range | Key Offerings |
---|---|---|
Supplier 1 | $50,000 – $150,000 | Max forming length: 3m; Thickness capacity: 2 mm steel |
Supplier 2 | $80,000 – $250,000 | Integrated touchscreen control, barcode scanning |
Supplier 3 | $100,000 – $500,000 | Roll forming + Punching + Shearing configuration |
Pricing varies based on specifications, customization, and geographic location. Contact suppliers for quotes based on requirements.
Maintenance Tips
Proper maintenance is vital for longevity and performance. Key tips include:
- Inspect machine routinely for loose parts or damage
- Lubricate moving components per manufacturer schedule
- Check hydraulic systems and pumps
- Replace worn out rollers and punching tools
- Clear metal debris and dust buildup
- Keep machine free of moisture accumulation
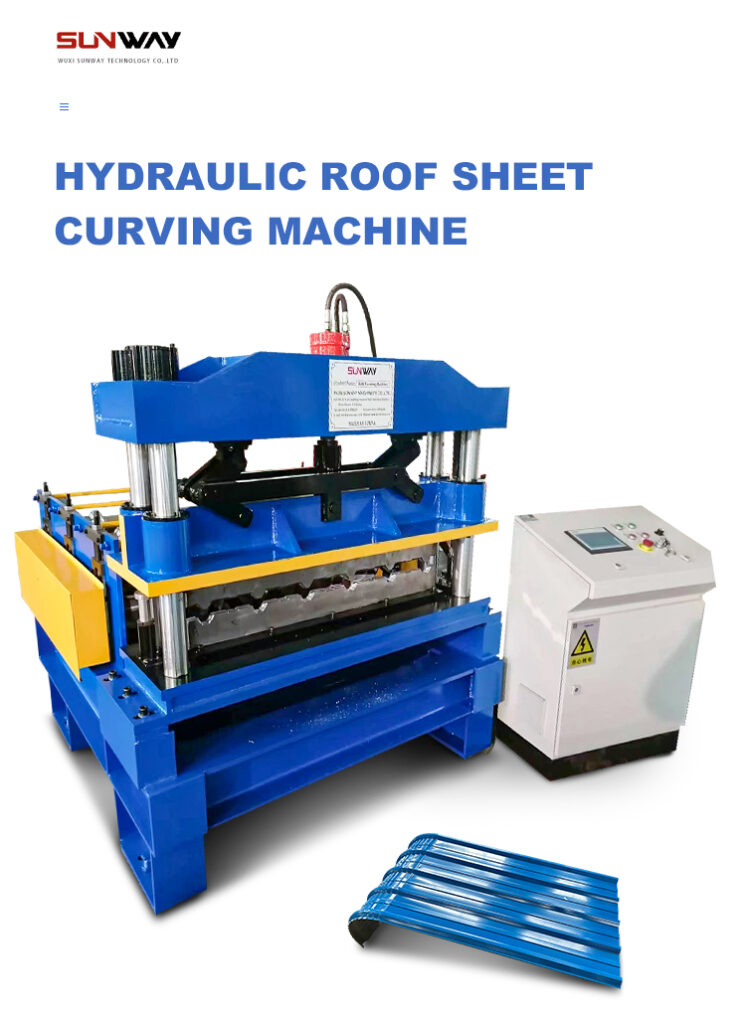
FAQs
Q: What sheet metal thickness can be formed on these machines?
A: Electric cabinet frame machines can typically process sheet metal ranging from 0.5 mm to 2 mm thickness. Special variants are available to form much thicker sheets.
Q: Can existing cabinet designs be fabricated on the machine?
A: Yes, custom cabinet 3D models can be imported or programmed into the machine control software to produce those designs automatically.
Q: What safety precautions are required?
A: Safety measures like emergency stop circuits, light curtains, guards, operator training are essential to prevent hazardous moving part accidents.
Q: What expertise is needed to operate these machines?
A: While computer programming knowledge helps, no special expertise is required as suppliers provide adequate training for using the machine safely.