Roll forming is a metal working process in which sheet metal is progressively formed into a desired cross-sectional profile through a series of roll stations. Roll formed profiles are used extensively in building construction for purlins, wall panels, roofing, railing systems and more.
Cz roll forming machines are a popular type of roll former used to produce these structural profiles. This guide provides a detailed overview of cz roll forming machine technology, operating principles, components, capabilities, applications and more. Whether you are looking to buy a new cz roll former or learn more about the process, this article covers everything you need to know.
Overview of Cz Roll Forming
Roll forming with cz roll machines involves continuously bending and shaping sheet metal stock into customized parts and profiles. It is an efficient, high-speed process suitable for producing large quantities of parts with long lengths and constant cross-sections like building materials or automobile body panels.
Cz roll forming gets its name from the C- and Z- shaped roll forming stands used that bend and shape the metal progressively. As the material passes through consecutive stands, it gains the desired contour and dimensional accuracy. Common roll formed sections include C & U channels, angles, square and rectangular tubes, and complex custom shapes.
Compared to other processes like extrusion or press braking, roll forming has advantages of flexibility, efficiency and cost-effectiveness. Cz roll forming lines can be equipped with decoilers, feed tables, pre-punching & cutting stations, welding units and other inline processes for complete production.
Key Benefits of Cz Roll Forming:
- High production rates up to 100 m/min with excellent precision and repeatability
- Low tooling costs compared to stamping or pressing
- Minimal material waste – continuous production from coils
- Consistent quality and mechanical properties
- Flexible equipment produces variety of profiles from same machine
- Scalable production by adding more roll forming stands
- Suitable for high strength steels, stainless steel, aluminum etc.
- Integration with upstream and downstream processes
With roll formed sections gaining popularity in many industries, cz roll forming lines are an important manufacturing equipment for modern plants.
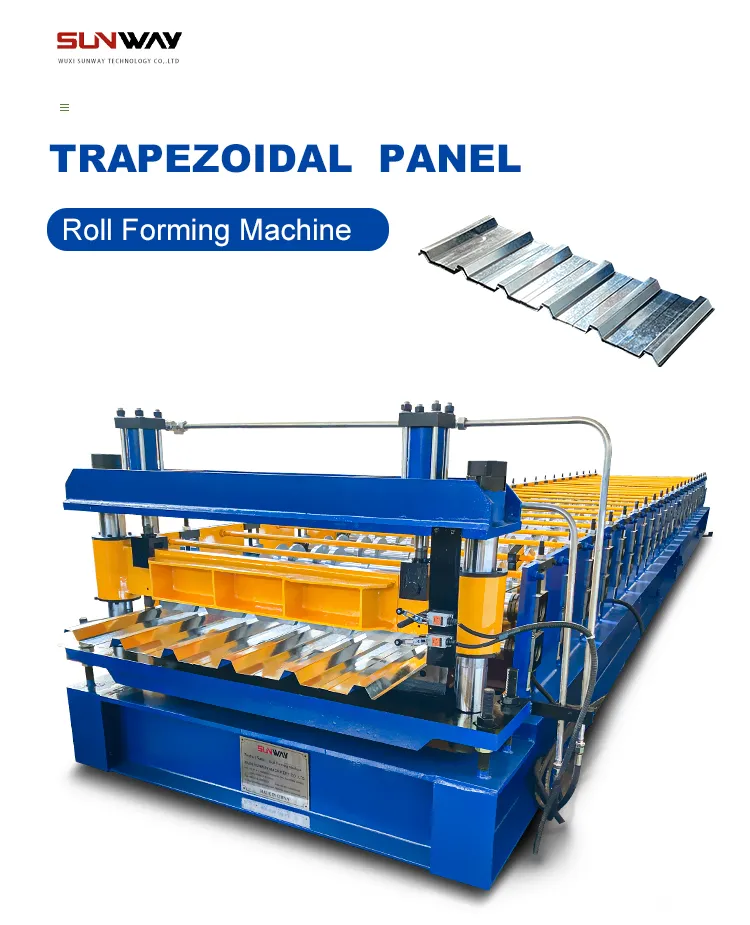
How Does a Cz Roll Forming Machine Work?
Cz roll forming machines work on the principle of progressively bending sheet metal through a series of stands containing pairs of rolls. Each stand performs an incremental amount of bending until the final cross-section is formed.
The key processes involved in cz roll forming are:
1. Decoiling
Sheet metal coil of the required thickness and material is loaded onto a decoiler which allows unwinding of the coil into the roll former. The decoiler prevents tangling and backlash during unwinding.
2. Feeding
The sheet is fed into the roll forming line through a set of feed rolls. This stage straightens the sheet and feeds it at the required speed into the forming section.
3. Pre-punching
Holes, notches and other features can be punched into the sheet before roll forming if required. This allows profiles with holes or slots to be created.
4. Forming
The core of the machine is the forming section with multiple roll forming stands arranged in a serial flow. As the sheet passes through each stand, the rolls make longitudinal bends until the final shape is progressively achieved.
5. Cutoff
A cutoff press or flying shear cuts the continuously produced profile into required lengths as per the application. The cutoff can be manual or automatic.
6. Downstream processes
Additional processes like deburring, marking, stacking can be integrated downstream of the cutting station for finished parts.
The series of shaped rollers bend the material incrementally without over-stressing it. Lubricants are used to control friction between the rolls and sheet metal during the process.
Key Components of a Cz Roll Forming Machine
Cz roll forming lines are equipped with a range of components and sub-systems for handling coils, feeding, forming, cutting and material handling:
Roll Forming Stands
The roll forming section has a number of C-shaped (opening downward) and Z-shaped (opening upward) stands. Typical small lines have 3-5 stands while industrial lines can have 15 or more stands for complex profiles.
- Roll tooling is machined to precise shapes matching the desired profile
- Advanced 3D Roll Design software is used to simulate material flow and roll design
- Quick changeover systems allow fast die changeovers
Decoiler
Used to hold the coil being fed into the machine and control the unwinding of sheet. Features include:
- Coil holding arms/brackets with quick loading system
- Expansion mandrel to mount coil ID
- Active tension control
- Multi-diameter decoiler for flexible coil widths
- Coil car for quick loading
Feed System
Consists of a set of feed rolls which straighten the strip and feed it into the roll forming stands.
- Servo-motor driven rolls for accurate speed control
- Descaled, hardened pinch rollers
- Quick release urethane coated rollers
- Anti-backlash system
Roll Forming Controls
The forming process is controlled via:
- PLC/PC based controls with HMI touchscreen
- Servo motors on each roll station for precision bending
- Alignment control via hydraulic jacking of stands
- Roll gap/position actuators on each stand
Cutoff System
Cuts the continuously produced profile into desired lengths
- Flying shear/rotary shear for high speed cutoff
- Pneumatic or servo presses for blanking
- Length measuring system for automatic cutoff
- Conveyor for part offload
Safety Equipment
- Safety fences around forming section
- Interlocks on doors, covers
- E-stop buttons
- Overload, overheat monitoring
Proper design of each component is crucial for achieving high productivity and quality in cz roll forming.
Key Specifications of Cz Roll Forming Machines
Cz roll formers are customized to produce profiles of different sizes, materials and complexities. The main specifications to consider are:
Specification | Typical Range |
---|---|
Line Speed | 10 – 100 m/min |
Material Thickness | 0.5 – 4 mm |
Material Type | Mild steel, stainless steel, aluminum etc. |
Profile Width | 50 – 300 mm |
Roll Stands | 3 – 20 |
Forming Length | 3 – 25 m |
Drive Power | 5 – 30 kW |
Control System | PLC, servo motors, HMI |
Coil Weight Capacity | Up to 10 tons |
Advanced 3D modeling and simulation is used to design roll tooling and machines to meet the desired output. Customized units can be built to meet specific production requirements.
Key Considerations for Buying a Cz Roll Former
While purchasing a cz roll forming system, some of the key factors to evaluate are:
- Required output – profile dimensions, quantities needed, line speed
- Material specifications – thickness, grade, width, coil weight
- Product precision and surface quality needs
- Level of automation – manual vs fully automatic
- Budget constraints – optimize performance for budget
- Production efficiency – minimum downtime, changeovers
- Flexibility for future products
- Available space for installation
- Noise/safety requirements
- Cost of tools vs machine price
- After-sales service support from supplier
Working closely with an experienced cz roll forming machine manufacturer is important to get equipment tailored to your needs.
Types of Cz Roll Forming Machines
There are two main categories of cz roll forming lines:
Fixed or Dedicated Lines
Designed for high volume production of the same profile.
- Only one set of roll tooling
- Very fast production of repetitive orders
- Lower cost due to fixed tooling
- Require separate lines for different profiles
Flexible or Universal Lines
Capable of quick profile changes with minimal downtime
- Modular tooling design enables fast die changes
- Higher initial cost due to quick change systems
- Production flexibility for changing orders
- Reduced requirement of extra lines
Many modern cz roll formers use a flexible modular approach combining the best of both designs. Tooling carts with quick connects allow fast die changes while dedicated flow paths improve output.
Typical Applications of Roll Formed Profiles
Cz roll forming technology is widely used to produce structural framing and building components:
- Purlins, girts, eave struts
- Wall panels, roofing sheets
- Metal roof trusses, rafters
- Door & window frames
- Railing and highway safety barriers
- Solar panel frames
- Scaffolding, stage props
- Roller shutter door guides
- Rack post profiles
- Furniture tubing
- Automotive chassis parts
Almost any open structural section can be roll formed to near-net shape for immediate use. The flexibility of roll forming allows both simple and highly complex custom shapes to be produced.
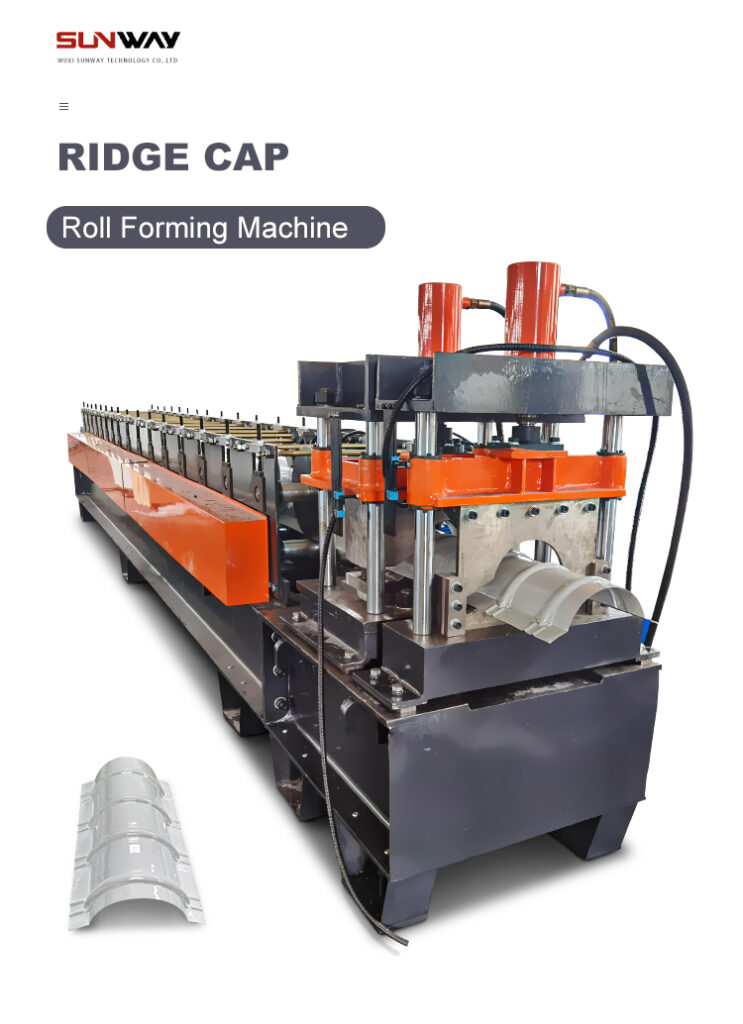
Advantages of Cz Roll Formed Profiles
There are several benefits of using roll formed sections instead of other manufacturing processes:
- Superior functional performance – optimized strength/weight ratio compared to extruded or hot rolled sections
- Cost savings – reduced material cost due to no machining or waste
- Higher production rates than competing processes like fabrication or stamping
- Closer dimensional tolerances than other high speed processes
- Consistent quality along the length with no warping or deformities
- High strength – cold worked material has excellent mechanical properties
- Material savings – near net shape forming reduces excess material use
- Wide material choices – aluminium, steel, stainless steel etc.
- Environmental benefits – lower embedded energy compared to mill shapes
- Design flexibility – custom profiles are possible
- Scalability – production output can be easily increased
These factors make cz roll formed profiles ideal for many industries. The cold forming process delivers both performance and value.
Limitations of Roll Forming Process
Despite the benefits, roll forming does have some inherent limitations:
- Complex shapes with deep re-entrant features are difficult to roll form in one pass. Two pass forming may be needed.
- Heavy gauge thick materials are harder to roll form continuously. Strength of machine is a constraint.
- Surface finish can show marks from rolls. Post-treatment like powder coating may be needed.
- Not suitable for short length parts – continuous process has length constraints.
- Only open profiles are possible, closed tubes need welding after forming.
- High initial investment required for roll design and machine.
- Skill needed to set up rolls and control forming process.
- Roll marking on soft materials like aluminum, copper. Needs appropriate lubrication.
For simpler profiles, other processes like press braking or extruding may be more suitable. Roll forming excels in producing high volumes of open sections.
Tips for Successful Roll Forming
Here are some best practices to follow for smooth cz roll forming and quality output:
- Choose correct material thickness and properties – yield strength impacts bending
- Review roll designs thoroughly before tooling fabrication
- Align stands precisely using jacking systems and test materials
- Ensure proper leveling and feed speed into forming section
- Use appropriate lubrication – type and amount
- Monitor roll wear and refinish rolls when needed
- Allow sufficient distance between stands for good bend progression
- Adjust bottom roll heights to control sheet lifting
- Check formed profile continuously and tune process
- Avoid stop marks by planning cutoff sequence
- Correctly calculate machine capacity for intended output
- Keep dies maintained, inspected and change when worn
- Train operators thoroughly for best practices
With attention to these aspects, cz roll forming lines can deliver high productivity and near-perfect profiles.
Step-by-Step Process of Roll Profile Design
Designing the roll tooling profile is a critical first step in the roll forming process. The main steps are:
1. Define Desired Profile Geometry
- Create 2D and 3D models of finished part geometry
- Specify dimensions like flange width, wall angles, radii etc.
- Include any slots, holes, embossings needed on profile
2. Material Selection
- Choose metal type, thickness, mechanical properties
- Consider strength needed, bendability, surface finish
3. Simulation and Roll Design
- Use FEA software to simulate sheet bending sequence
- Determine number and configuration of roll stands
- Design roll geometries to match material flow in simulation
4. Roll Tooling Fabrication
- Machine rolls according to design profiles and fits
- Ground and polished dies for surface finish
- Hardening and heat treatment
5. Roll Assembly & Testing
- Assemble rolls on stands in proper sequence
- Test run initial forming with trial materials
- Refine roll design if needed based on test results
6. Final Trials & Production
- Conduct final machine trials before production
- Monitor process until optimal forming achieved
- Initiate regular production after machine sign-off
The roll profile design is optimized through simulation and trials to produce the desired part geometry.
Choosing the Right Roll Forming Equipment Supplier
Choosing the right cz roll forming machine manufacturer is key to getting equipment that meets your needs. Some criteria to consider include:
- Technical expertise & experience – decades of machine design experience preferred
- Roll tooling design capabilities – extensive simulation and in-house roll manufacturing
- Range of equipment – small units to large production lines
- Customization skills – ability to design for specific profiles
- Quality and precision of machinery
- Automation capabilities – ease of integration with other processes
- After-sales service – installation support, maintenance contracts, spare parts supply
- Training provided – proper orientation to operators
- Long-term relationship – upgrade support for future needs
- Cost and delivery – competitive pricing and lead times
- Manufacturing facilities – modern plant with good infrastructure
- Reputation in the industry – long-term client relationships
Partnering with a reputed roll forming OEM with design expertise and quality manufacturing capabilities ensures you get machinery that meets your objectives.
Cz Roll Forming Machine Pricing
Cost of cz roll forming equipment depends on:
- Number of roll stands
- Level of automation and additional equipment
- Electric motor power and forming speed
- Material thickness and coil capacity
- Changeover and control systems
- Additional processes integrated
Machine Capacity | Average Pricing Range |
---|---|
Small unit < 3 tons/day | $50,000 – $100,000 |
Medium unit, 10 tons/day | $150,000 – $300,000 |
Large line, >50 tons/day | $500,000 – $2,000,000 |
Pricing can vary widely based on the desired output, precision, level of automation and production rate. Discuss requirements with manufacturers to get an accurate estimate.
Maintaining a Cz Roll Forming Machine
Proper maintenance of a cz roll former improves its performance, productivity and longevity. Here are some important aspects of roll forming machine maintenance:
- Regular lubrication of roll bearings, gearbox and friction points
- Inspection and replacement of worn rollers and forming dies
- Checking roll alignment and stand adjustment
- Monitoring drive motors and gearbox for temperature and noises
- Cleaning dirt and metal debris from machine parts
- Verifying electronic components and wiring are intact
- Checking hydraulic systems and pipelines for leaks
- Tightening any loose mechanical fasteners
- Applying rust preventing oils/greases during idle time
- Monitoring sheet feeding for defects or marking
- Tracking and replacing consumable items like lubricants
Roll inspection and preventive replacements at fixed intervals is crucial to avoid disruptions. Training production personnel on routine maintenance goes a long way in trouble-free operation.
Safety Tips for Cz Roll Forming
Roll forming operations involve handling heavy machinery and materials at high speeds. Some key safety tips:
- Restrict access to operating area with safety fencing and interlocks
- Ensure proper machine guarding around rotating parts
- Shut power before roll changes or maintenance
- Wear protective gear like close-fitting clothing, gloves, glasses
- Follow lockout/tagout procedures during servicing
- Keep work area clean and clear of oil spills or debris
- Train workers on safe material handling procedures
- Implement strict protocols for machine startup, shutdown and emergencies
- Install e-stop buttons near pinch points
- Monitor noise levels and provide ear protection if needed
- Conduct regular safety training and inspections
Making safety a priority and creating a culture of caution goes a long way in preventing accidents.
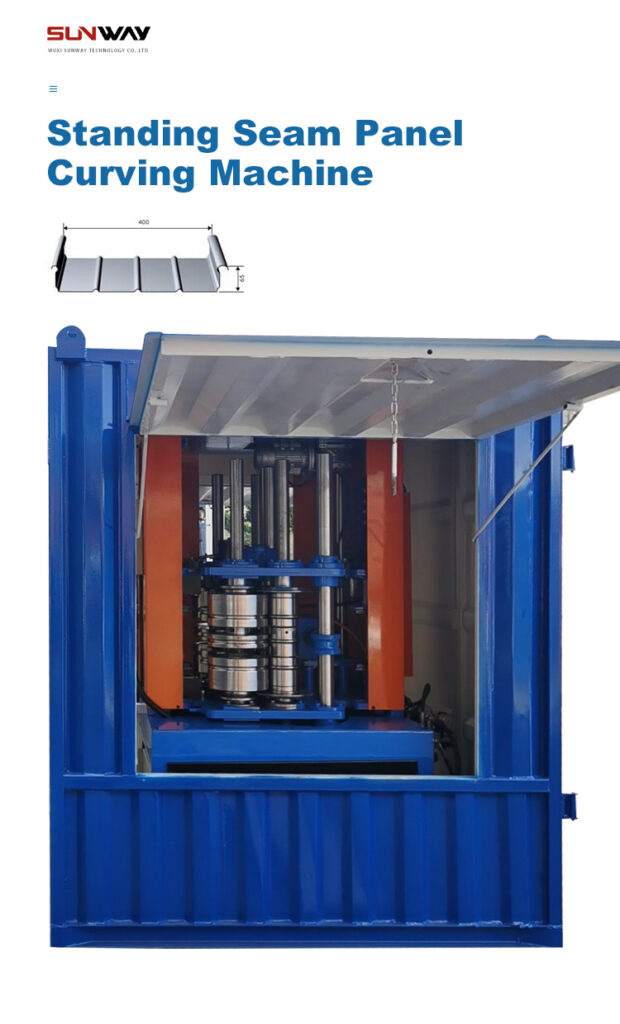
FAQ
Q: What materials can be roll formed?
A: Most ductile metals like low carbon steel, stainless steel, aluminum, copper, brass can be roll formed. Mild steel is the most common. Maximum thickness is about 3-4mm for carbon steel in a single pass.
Q: How long are the profiles produced?
A: Production lengths range from 2-3 meters for smaller machines to 20 meters or more for large industrial lines. length depends on application requirements. Parts can be cut into required lengths.
Q: How many types of profiles can be produced on one machine?
A: On fixed roll formers only one profile shape is possible. On quick change or flexible lines, up to 4-5 profiles can be easily changedover. More dies can be added.
Q: What tolerances can be achieved?
A: Roll formed parts can achieve dimensional tolerances upto +/- 0.5 mm on standard sections. More precision requires additional processes.
Q: What is the cost of profile design and roll tooling?
A: Roll design using software costs around $2000 upwards per profile. Roll tooling including machining can range from $3000 for simple profiles to $15000 for complex shapes.