Overview of CZ Purlin Roll Forming Machines
CZ Purlin roll forming machines are used to continuously bend metal coils into customized C and Z shaped purlins and girts for the construction industry. Purlins provide structural framing and support for roofing and siding materials.
What is a CZ Purlin?
C and Z purlins have a unique cross-sectional shape that provides strength and rigidity from the angled web. The flanges allow easy attachment to roofing and walls. Common materials are galvanized steel, aluminum, and stainless steel.
Benefits of Using CZ Purlins
- Lightweight but load-bearing for long roof spans
- Easy to install, requiring simple bolted connections
- Angled web provides torsional rigidity under wind or seismic loads
- Variety of sizes suit residential, commercial and industrial applications
- Galvanizing offers corrosion resistance for low maintenance
Working Principle of CZ Purlin Roll Forming
- Coiled metal sheet or strip is unrolled and fed into the mill
- Forming rollers progressively cold-form the strip into C or Z shape through a series of bending steps
- Cutoff knives slice formed sections to specified lengths
- Formed purlins are collected on the output side for bundling and shipping
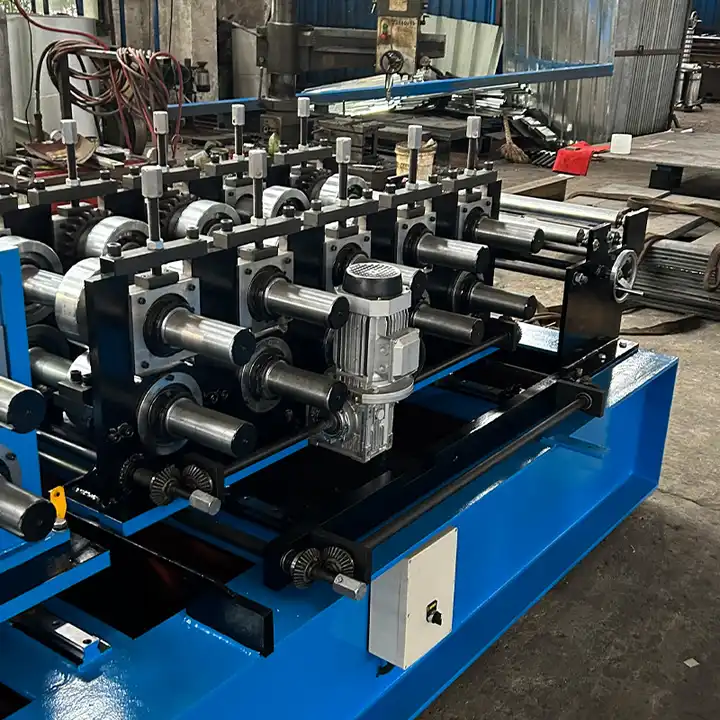
Types of CZ Purlin Roll Forming Equipment
Equipment Type | Description | Production Rate |
---|---|---|
Manual Lines | Basic manually-operated machines for small scale producers | Around 10 m/min |
Automatic Lines | Feature powered unwinding, feeding and cutting for high volume efficiency | Up to 35 m/min |
Customized Lines | Designed to make specialized purlin sizes and thicknesses | Varies based on need |
Working Process of CZ Purlin Roll Forming
The CZ purlin production line forms the raw metal strip from coiled stock through a series of progressive bending and forming stages into the final C or Z-shaped profile.
Key processes include:
- Material Feeding: Automated powered unwinding of coiled sheet metal into the mill
- Forming: Precision roller dies continuously cold form the strip through multiple bending steps
- Design and Sizing: Roller dies customized to produce exact purlin dimensions
- Cutting: Automated cutoff knives slice formed CZ sections to fixed lengths
- Customization: Lines can be adapted to make special purlin sizes
Forming rollers are machined to precision tolerances for accurate profile dimensions and straightness. The forming process induces work hardening into the metal for a strong finished purlin product.
Material Feeding in CZ Purlin Roll Forming
Feature | Details |
---|---|
Stock Material | Hot-dip galvanized steel coil / Aluminum coils |
Width Range | 50mm to 750mm |
Thickness Range | 0.4mm to 2.0mm |
Coil I.D. | 508mm (standard) |
Coil O.D. | 1200mm to 1500mm (standard) |
Decoiler Capacity | 5 tons to 20 tons |
Feeder Type | Powered mechanical, servo motor, hydraulic |
Feed Speed | Up to 35 m/min |
Galvanized steel is commonly used, along with aluminum and stainless steels in some cases. A variety of stock coil widths, thicknesses, diameters can be accommodated. Powered decoilers and programmable feed systems provide reliable, high-speed material input.
Design and Sizing Capabilities
CZ purlin roll forming lines can produce different designs, sizes, lengths and material gauges.
Parameter | Capabilities |
---|---|
Profile Shape | C or Z shape purlins |
Height | 50mm to 400mm |
Flange Width | 30mm to 80mm |
Lip Height | 6mm to 20mm |
Material Thickness | 0.4mm to 2.0mm |
Purlin Lengths | 2m to 15m programmable |
Through precision tooling, various purlin heights, flange widths, material gauges can be formed in standard or custom dimensions. Cutoff knives slice purlins from 2 to 15 meter fixed lengths.
-
Rolling Shutter Slat Roll Forming Machine
-
Highway Guardrail End Terminal Forming Machine
-
Highway U/C Post Roll Forming Machine
-
2 Waves Highway Guardrail Roll Forming Machine
-
3 Waves Highway Guardrail Roll Forming Machine
-
Electrical Cabinet Frame Roll Forming Machine
-
Din Rail Roll Forming Machine
-
Two waves highway guardrail machine
-
Three waves highway guardrail machine
Cutting Operation in Roll Forming Lines
Feature | Details |
---|---|
Cutting Principle | Pneumatically actuated shear knives |
Cutting Tolerance | +/- 1.0mm |
Minimum Cut Length | 2000mm |
Maximum Cut Length | 15000mm |
Section Length Indicator | Digital meter counter |
Section Length Tolerance | +/- 1.0mm |
Scrap Collection | Chute below shear station |
Purlin lengths are set by precision ballscrew mechanisms to position the pneumatic shears. A high tolerance cutting operation ensures each purlin is within +/- 1mm of the exact programmed length.
Customization of CZ Purlin Roll Forming Lines
Roll forming lines can be customized to produce specialized purlin and girt sections based on customer requirements:
Possible Customizations
- Non-standard purlin and girt dimensions
- Special material types and thicknesses
- Custom coatings and finishes
- Integration with packing equipment
- Non-standard power supplies
- Motor control hardware upgrades
- UL/CE compliance packages
Custom lines enable small scale producers to make specialized products for niche markets cost effectively.
Installation, Operation and Maintenance
Activity | Description | Frequency |
---|---|---|
Installation | Performed by supplier technicians onsite. Requires flat, level floor and provision of utilities. | One time |
Operation | Machine operators feed coils, set dimensions, monitor production. Basic mechanical aptitude is needed. | Daily production runs |
Maintenance | Includes lubrication, inspection, spare parts replacement and recalibration of components. | As per supplied manual |
Proper installation forms the base for smooth functioning. Routine maintenance helps maximize production uptime and output quality.
How to Choose the Right CZ Purlin Roll Forming Machine
Key considerations when selecting a roll forming machine:
- Type and volume demand
- Product dimensions, specifications
- Raw material type and thickness
- Level of automation needed
- Production efficiency targets
- Budget constraints
- Options for future expansion
- Supplier reputation and service
Accurately estimating key requirements will help identify the ideal machine specifications and avoid overpaying. Leading manufacturers offer production guidance.
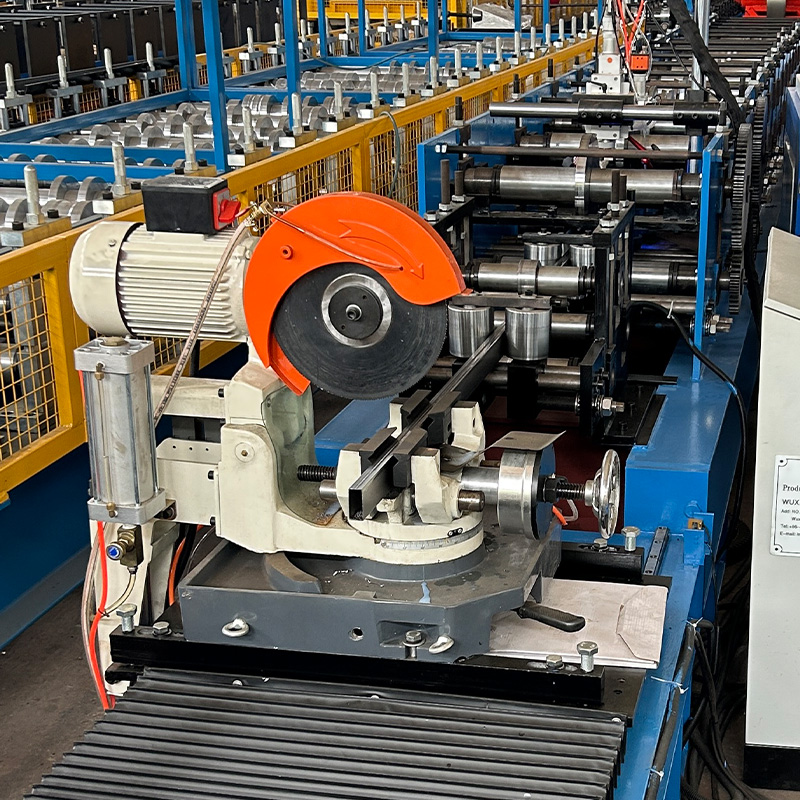
Pros and Cons of CZ Purlin Roll Forming Machines
Advantages | Limitations |
---|---|
Continuous unattended production | Fixed tooling limits profile shapes |
High material yield from coil inputs | Significant initial capital expenditure |
Consistent quality end product | Complex for extremely thick metals |
Versatile production capacities | Narrow sheets under 50mm challenging |
Simple bolt-together field installation | Maximum 15 m lengths without secondary bending |
When correctly specified, CZ purlin roll forming lines offer efficient, automated production of roofing components with quick payback on investment.
FAQ
Q: What thickness of sheets can be formed on these machines?
A: Standard machines accommodate metal thickness from 0.4mm up to 2mm. Special heavy gauge lines are available for plates over 2mm.
Q: Can other profiles be produced besides C and Z?
A: Machine tooling is currently limited to CZ purlins and girts. Custom roll dies would be needed for different profiles.
Q: How long is supplier training and commissioning?
A: Standard lines require just 2-3 days at the factory. For customized equipment, specialists may remain 5-7 days for full transfer.
Q: What is the typical production rate?
A: 10 – 35 meters per minute based on automation level and power. Faster cycles are possible with accumulator cutoff.
Q: What factors affect price most?
A: Key drivers are production speed, level of automation, customization needs, and ancillary equipment integration.