Roll forming machines are essential pieces of equipment for any manufacturing process that involves shaping metal or other materials into specific shapes. With so many different types of roll forming machines available, choosing the right one for your production needs can be a daunting task. The wrong choice could lead to decreased efficiency, increased downtime, and ultimately, lost revenue. In this guide, we’ll explore the key factors to consider when choosing the right roll forming machine for your production needs. Whether you’re a seasoned manufacturer or just getting started, this guide will provide you with the knowledge you need to make an informed decision and get the most out of your roll forming machine.
Understanding the Different Types of Roll Forming Machines
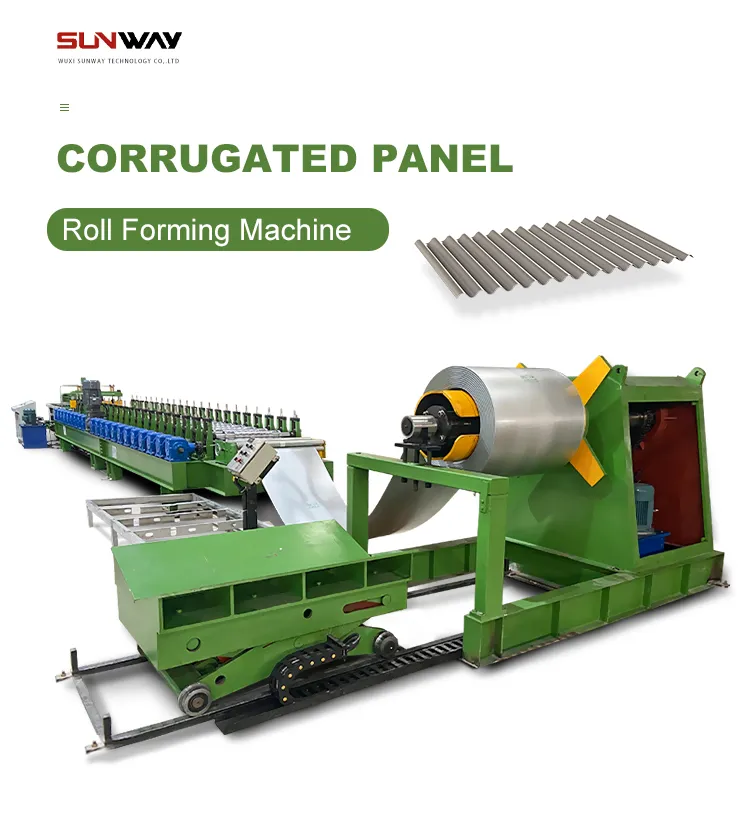
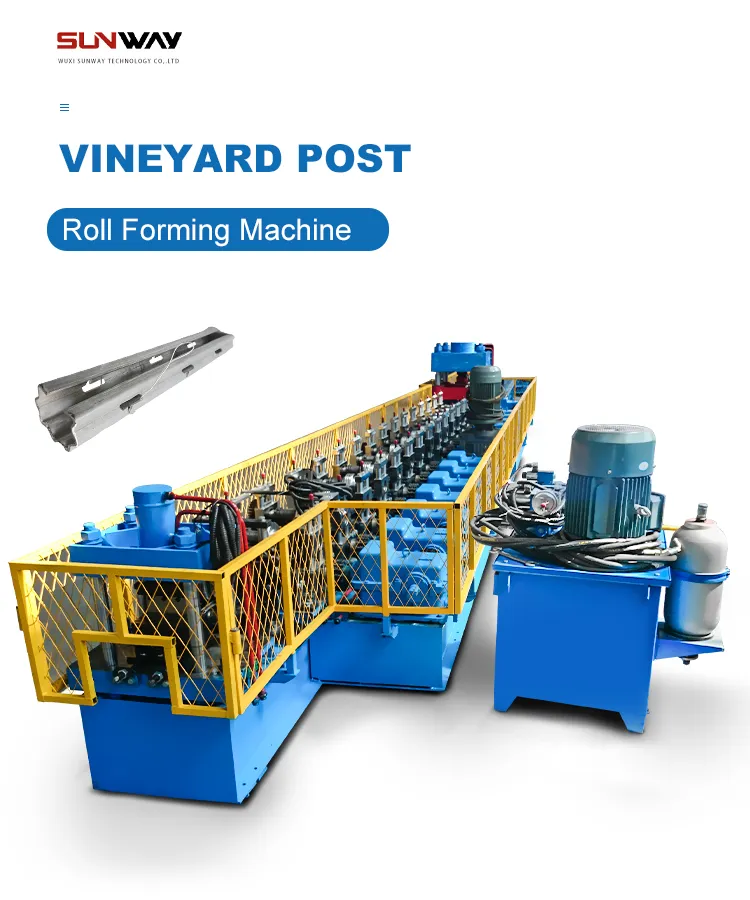
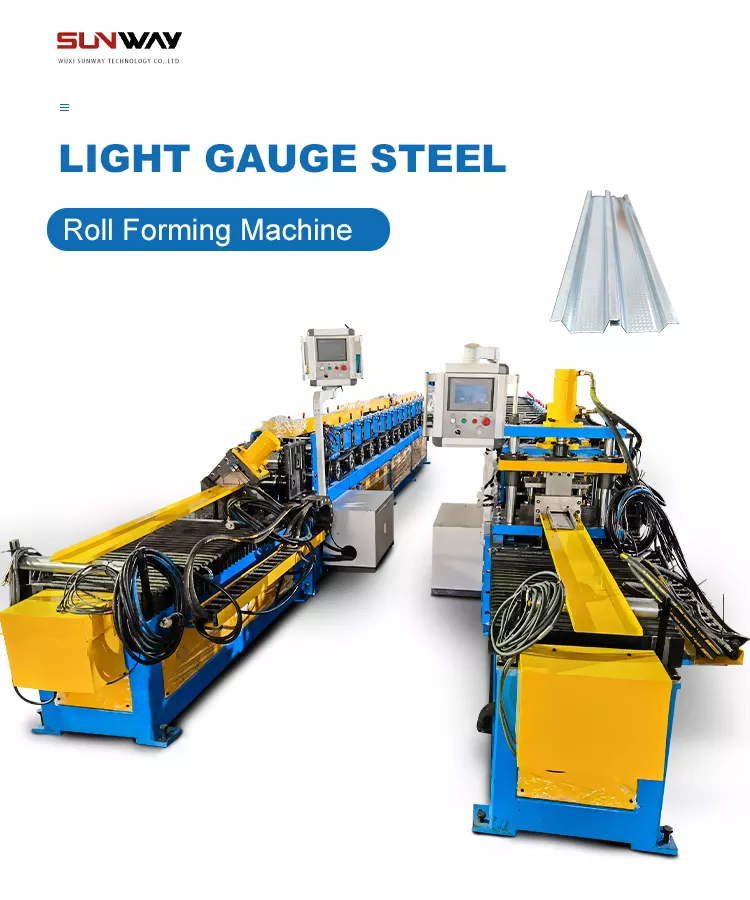
Roll forming machines are designed to shape a wide range of materials including metals, plastics, and composite materials. When it comes to choosing the right roll forming machine for your production needs, it’s important to understand the different types of machines available and what they are used for.
One of the most common types of roll forming machines is the C-channel machine. C-channel machines are used to produce C-shaped profiles that are commonly used in construction, electrical, and manufacturing industries. These profiles are used as structural elements in buildings, support beams for industrial equipment, and as frames for conveyor systems.
Another type of roll forming machine is the U-channel machine. U-channel machines are used to produce U-shaped profiles that are commonly used in the construction of steel buildings, bridges, and other large-scale infrastructure projects. U-channels are also used in the automotive and aerospace industries as framing elements for vehicles and aircraft.
Z-channel machines are another type of roll forming machine that are used to produce Z-shaped profiles. Z-profiles are commonly used in roofing and cladding systems, as well as in the construction of industrial equipment and machinery.
Other types of roll forming machines include hat channel machines, angle machines, and tube and pipe machines. Hat channel machines are used to produce hat-shaped profiles that are commonly used in the construction of metal buildings and other structures. Angle machines are used to produce L-shaped profiles that are commonly used as framing elements in construction projects. Tube and pipe machines are used to produce round or rectangular tubing for a wide range of applications, including furniture, automotive parts, and industrial equipment.
By understanding the different types of roll forming machines and what they are used for, you can make a more informed decision when it comes to choosing the right machine for your production needs.
Determining Your Production Needs of roll forming machine
Determining your production needs is a crucial step in choosing the right roll forming machine for your business. There are several factors that you should consider when assessing your production needs, including:
- Type of Product: The type of product you are producing will have a significant impact on the roll forming machine you choose. Different products require different profiles, which in turn require different roll forming machines. Consider the shape, size, and material of the product you are producing when evaluating your production needs.
- Required Production Speed: The speed at which you need to produce your products is another important factor to consider. Some roll forming machines are designed to operate at high speeds, while others are better suited for lower volume production. If you need to produce a high volume of products in a short amount of time, you may need to invest in a machine with a higher production speed.
- Size of the Product: The size of your product will also play a role in the roll forming machine you choose. If you need to produce large, bulky products, you will need a machine with a larger workpiece capacity. Conversely, if you are producing smaller products, a machine with a smaller workpiece capacity may be sufficient.
- Volume of Production: The volume of production you need to achieve is another important factor to consider. If you need to produce a large number of products in a short amount of time, you may need to invest in a roll forming machine with a higher production speed and capacity.
By carefully considering these factors, you can determine your production needs and choose the right roll forming machine for your business. This will help you achieve greater efficiency, lower costs, and higher quality products.
Considering Customization Options of roll forming machine
When it comes to choosing the right roll forming machine for your production needs, it’s important to consider the customization options available to you. Here are some customization options to explore:
- Extra Stations: Adding extra stations to the machine can help increase production efficiency by allowing you to perform multiple operations in a single pass. This can help reduce the number of passes needed to produce a finished product, which in turn can reduce production time and costs.
- Increased Power: Increasing the power of the machine can help it handle thicker, heavier materials more efficiently. This can help increase production speed and capacity, while also improving the quality of the finished product.
- Special Tooling: Special tooling can be added to the machine to help produce custom profiles and shapes. This is particularly useful if you are producing unique products that require non-standard shapes or features.
- Material Handling: Depending on the type of material you are working with, you may need to customize the machine’s material handling capabilities. This could involve adding special rollers or feeders, or modifying the machine’s workpiece capacity.
- Control Systems: Upgrading the control systems on the machine can help improve automation and reduce labor costs. This could involve adding computer-controlled systems or automatic material feeders to the machine.
By exploring these customization options, you can choose a roll forming machine that is tailored to your specific production needs. Be sure to consult with a qualified supplier or manufacturer to determine which customization options are best for your application.
Choosing the Right Supplier of roll forming machine
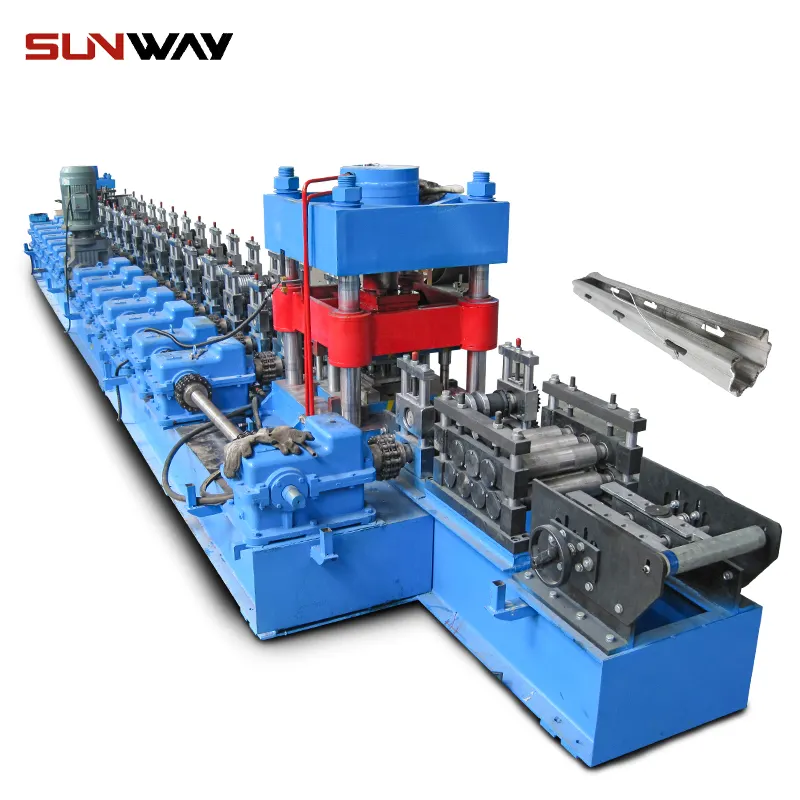
Choosing the right supplier for your roll forming machine is just as important as choosing the right machine itself. Here are some key factors to consider when selecting a supplier:
- Industry Experience: Look for a supplier with a proven track record of providing roll forming machines to your specific industry. This will ensure that they have the knowledge and expertise necessary to help you choose the right machine for your production needs.
- Reputation for Quality: Choose a supplier that has a reputation for producing high-quality machines that are built to last. This will ensure that you get a machine that is reliable, durable, and capable of producing high-quality products.
- Customer Service: Look for a supplier that is committed to providing excellent customer service. This includes offering technical support, maintenance and repair services, and ongoing training to help you get the most out of your roll forming machine.
- Customization Options: Choose a supplier that offers a wide range of customization options to help you tailor your roll forming machine to your specific production needs.
- Price: Of course, price is always a factor when choosing a supplier. Look for a supplier that offers competitive pricing without compromising on quality or customer service.
By choosing the right supplier for your roll forming machine, you can ensure that you get a high-quality machine that is tailored to your specific production needs. This will help you achieve greater efficiency, reduce costs, and produce higher quality products.
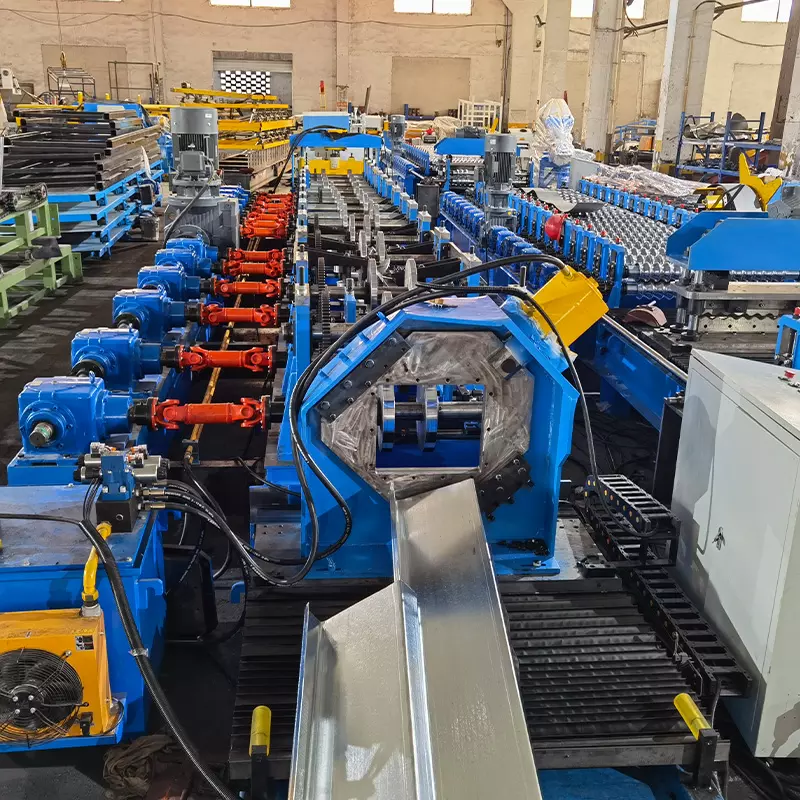
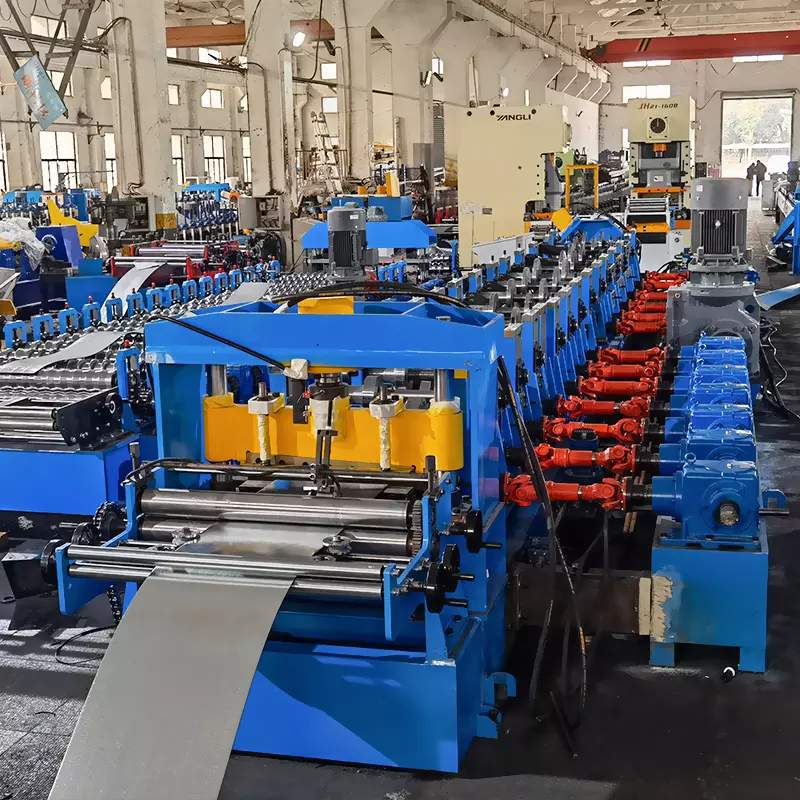
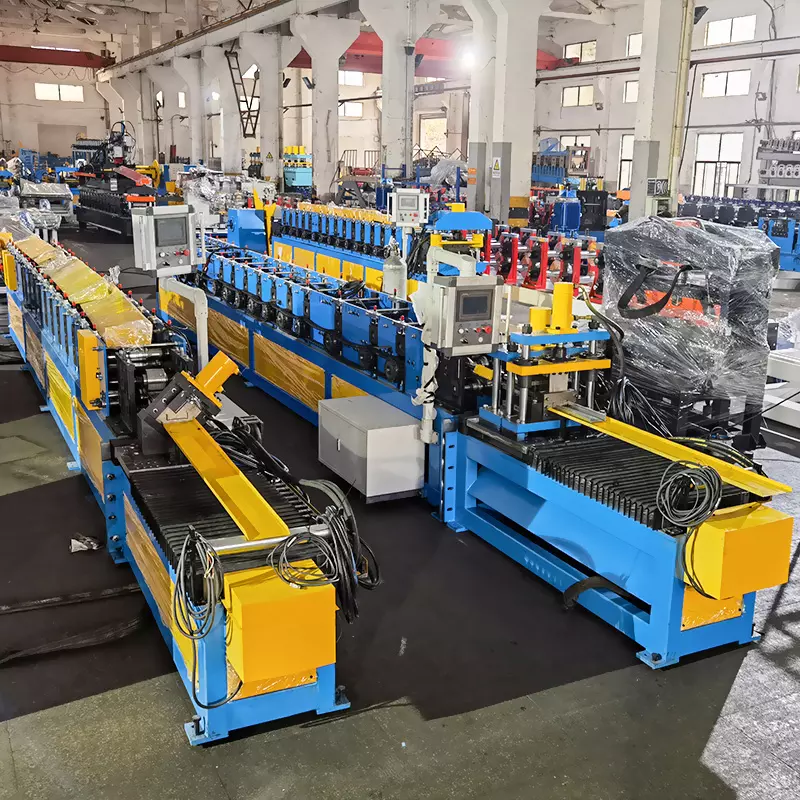
In conclusion, choosing the right roll forming machine for your production needs requires careful consideration of several factors, including the type of product, required production speed, size of the product, and volume of production. Evaluating machine features, considering customization options, and choosing the right supplier are also crucial steps in the decision-making process. By taking these factors into account, you can choose a roll forming machine that will help you achieve greater efficiency, reduce costs, and produce higher quality products. With the right machine and supplier, you can take your production process to the next level.