Metalworking has been an essential part of manufacturing for centuries. Over the years, various methods have been developed to create metal components, from stamping and welding to extrusion and casting. However, in recent times, a new method has emerged that has revolutionized metalworking – C channel roll forming machines. These machines have transformed the way metal components are produced, introducing automation, efficiency, and precision to the manufacturing process. In this post, we will discuss how C channel roll forming machines have revolutionized metalworking, the benefits they offer, and how they are shaping the future of manufacturing.
Introduction to C channel roll forming machines
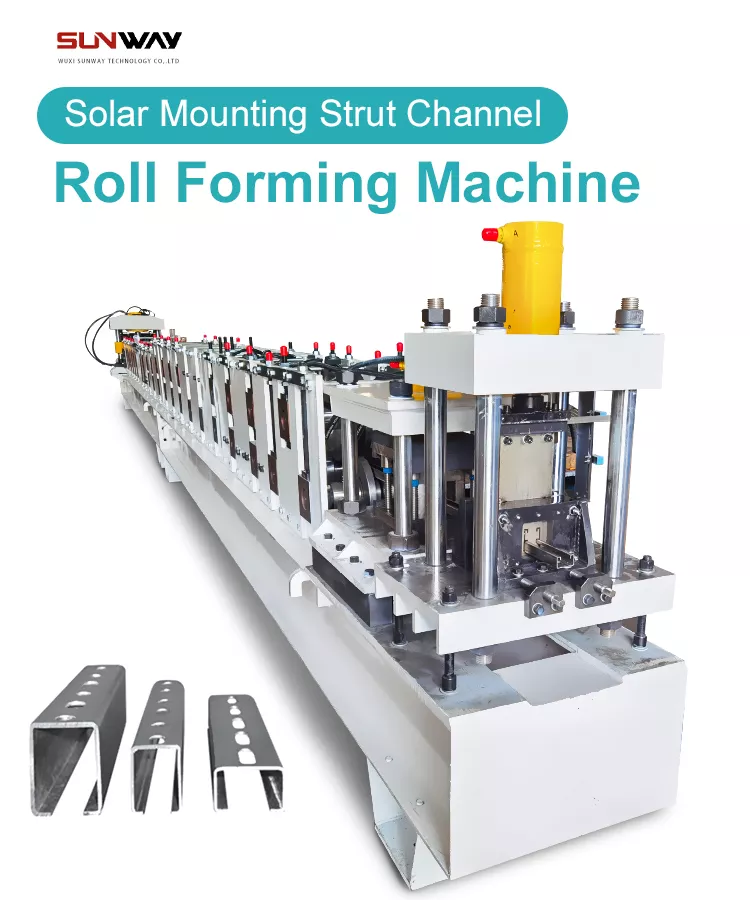
C channel roll forming machines are a type of machine used in metalworking to produce C channels of different sizes and shapes. Roll forming is a manufacturing process that involves bending and shaping metal coils into a desired profile or cross-section using a series of rollers and dies. This process has been used for many years, and over time it has evolved into a highly efficient and automated manufacturing process.
The history of roll forming can be traced back to the 17th century when craftsmen used manual rollers to shape metal sheets. In the 19th century, roll forming machines were introduced that used steam-powered rollers to produce metal components. These machines were used to produce a wide range of metal products, from roofing and gutter systems to car bodies and airplane parts.
In the 20th century, roll forming machines became more advanced, with the introduction of electric motors, hydraulics, and computer controls. These advancements made roll forming a highly efficient and automated manufacturing process, reducing the need for manual labor and increasing the precision and accuracy of the end product.
Today, C channel roll forming machines are widely used in various industries, including construction, transportation, automotive, and machinery. These machines have revolutionized metalworking by introducing automation, efficiency, and precision to the manufacturing process, enabling businesses to produce high-quality metal components at a faster rate and with fewer resources.
In conclusion, C channel roll forming machines are an essential tool in modern metalworking, providing a highly efficient and automated manufacturing process that can produce high-quality metal components of different sizes and shapes. The history of roll forming shows how this process has evolved over time, becoming a highly advanced and versatile manufacturing method that has revolutionized metalworking.
The revolution of metalworking that C channel roll forming machines have had on
C channel roll forming machines have had a significant impact on metalworking, revolutionizing the way metal components are produced. Here are some possible topics to consider:
- Automation: C channel roll forming machines have introduced a high level of automation to metalworking. These machines can produce metal components with minimal human intervention, reducing the risk of errors or defects. With automated controls and sensors that monitor the production process in real-time, roll forming machines can adjust the settings and parameters to ensure a smooth and consistent operation. This automation has increased the efficiency of metalworking, allowing businesses to produce high-quality metal components at a faster rate and with fewer resources.
- Efficiency: C channel roll forming machines have increased the efficiency of metalworking by reducing the need for multiple operations and setups. With roll forming machines, metal components can be produced in a single pass, without the need for additional cutting, punching, or welding. This means that the manufacturing process is faster and more streamlined, with fewer resources and materials wasted. The result is a lower cost per part and a faster turnaround time.
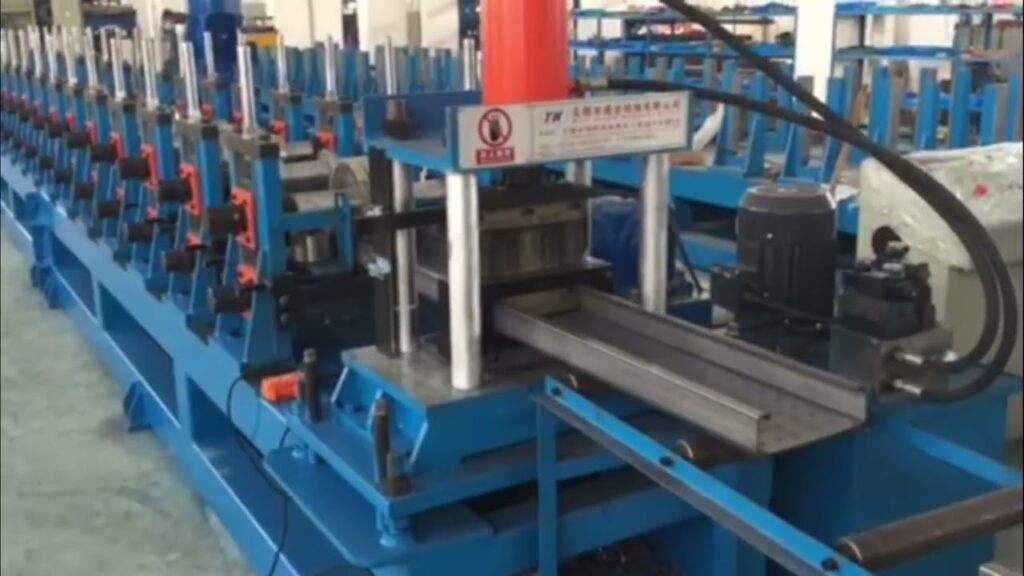
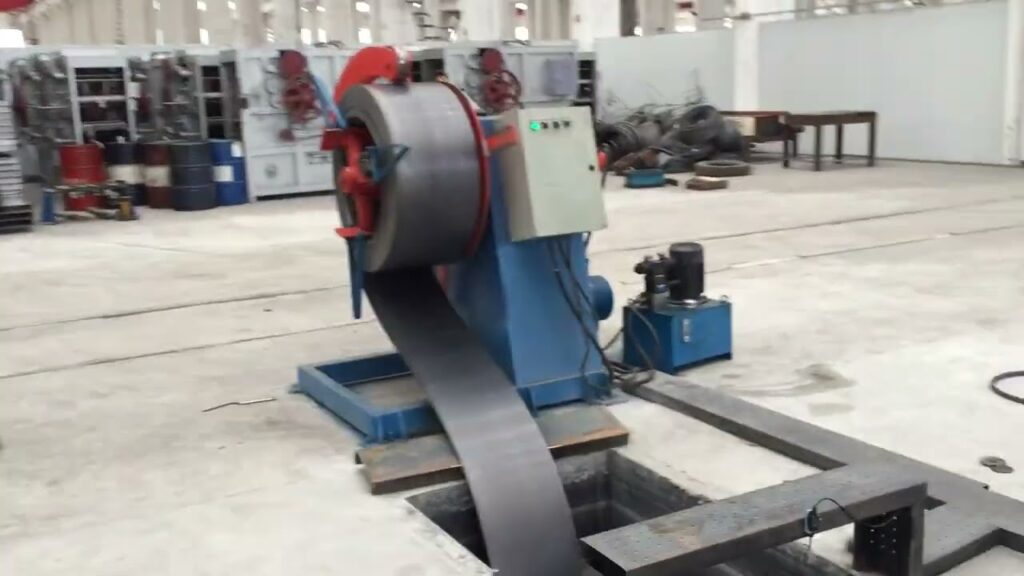
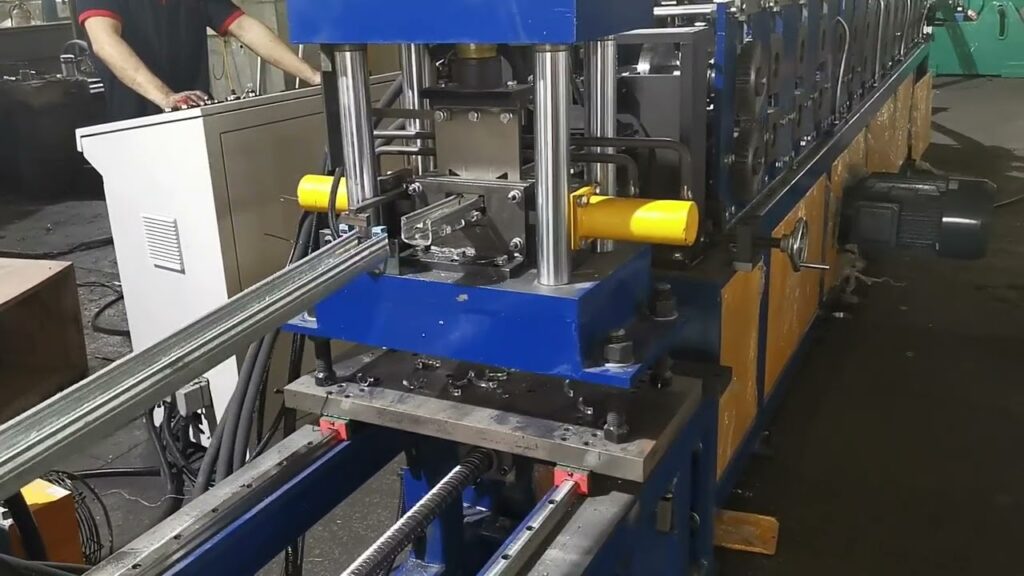
- Precision: C channel roll forming machines have introduced a high level of precision and accuracy to metalworking. Roll forming machines use a series of rollers and dies that gradually bend and shape the metal coil into the desired profile, ensuring a consistent shape and dimension throughout the production process. This precision means that the final product is of high quality, meeting the required specifications and standards. This accuracy is particularly important in industries where metal components are used in critical applications, such as aerospace, automotive, or medical devices.
- Versatility: C channel roll forming machines are versatile manufacturing tools that can produce metal components of different shapes and sizes. These machines can be customized and adjusted to produce a wide range of profiles and geometries, making them suitable for various applications and industries. This versatility means that businesses can adapt to changing market demands and offer customized solutions to their customers, without compromising on the efficiency or quality of the manufacturing process.
In conclusion, C channel roll forming machines have revolutionized metalworking by introducing automation, efficiency, precision, and versatility to the manufacturing process. These machines have transformed the way metal components are produced, enabling businesses to produce high-quality components at a lower cost and with faster turnaround times. As technology continues to evolve, it is likely that roll forming machines will continue to shape the future of metalworking and manufacturing.
The benefits of C channel roll forming machines
-
Electrical Cabinet Frame Roll Forming Machine
-
Din Rail Roll Forming Machine
-
Cable Ladder Roll Forming Machine
-
PV Mounting Bracket C Shape Profile Roll Forming Machine
-
Cable Tray Roll Forming Machine
-
PV Mounting Bracket Roll Forming Machine (HAT / Omega Profile)
-
PV Mounting Bracket Z Shape Profile Roll Forming Machine
-
Solar mounting strut channel roll forming machine
-
Strut Channel Roll Forming Machine
C channel roll forming machines offer several benefits for metalworking, making them an attractive option for businesses looking to produce high-quality metal components efficiently and cost-effectively. Here are some of the benefits of using C channel roll forming machines for metalworking:
- Cost savings: C channel roll forming machines can produce metal components at a lower cost than other manufacturing methods. These machines can eliminate the need for secondary operations such as cutting, punching, or welding, reducing the amount of labor required and the cost of materials. Additionally, roll forming machines can produce metal components in large quantities, reducing the cost per part and increasing profitability.
- High quality: C channel roll forming machines can produce metal components with high precision and accuracy, ensuring that each part meets the required specifications and standards. This high-quality production is essential in industries such as aerospace, automotive, or medical devices, where even small deviations in shape or dimension can have significant consequences.
- Production efficiency: C channel roll forming machines can produce metal components at a high-speed rate, reducing the turnaround time and increasing the overall production efficiency. These machines can also be customized and adjusted to produce metal components of different shapes and sizes, providing versatility and flexibility in the manufacturing process.
- Reduced waste: C channel roll forming machines can significantly reduce the amount of scrap metal generated during the manufacturing process. These machines use a continuous process that minimizes material waste and maximizes material utilization. This not only reduces the environmental impact but also results in cost savings for the business.
- Customization: C channel roll forming machines can be customized and adjusted to produce metal components of different shapes, sizes, and profiles, making them suitable for various applications and industries. This customization allows businesses to meet the specific needs and requirements of their customers, providing a competitive edge in the market.
In summary, C channel roll forming machines are a crucial part of modern metalworking, providing an efficient, cost-effective, and automated manufacturing process that can produce high-quality metal components of different sizes and shapes. The history of roll forming shows how this process has evolved over time, becoming a highly advanced and versatile manufacturing method that has revolutionized metalworking. C channel roll forming machines have introduced automation, efficiency, and precision to the manufacturing process, enabling businesses to produce high-quality metal components at a faster rate and with fewer resources. As technology continues to evolve, it is likely that roll forming machines will continue to play a significant role in shaping the future of metalworking and manufacturing.