Imagine a machine that can take metal powder and transform it into the intricate shapes that form a car’s body. This isn’t science fiction; it’s the reality of automobile profile making machines, also known as additive manufacturing (AM) machines specifically designed for the automotive industry. These machines are revolutionizing car manufacturing by offering:
- Increased design flexibility: Create complex shapes and lightweight structures previously impossible with traditional methods.
- Reduced waste: Utilize only the necessary material, minimizing scrap and environmental impact.
- Faster prototyping: Expedite the development and testing of new car models.
- On-demand production: Produce parts as needed, reducing inventory costs and storage space.
This article delves into the world of automobile profile making machines, exploring their production process, applications, benefits, limitations, and future potential.
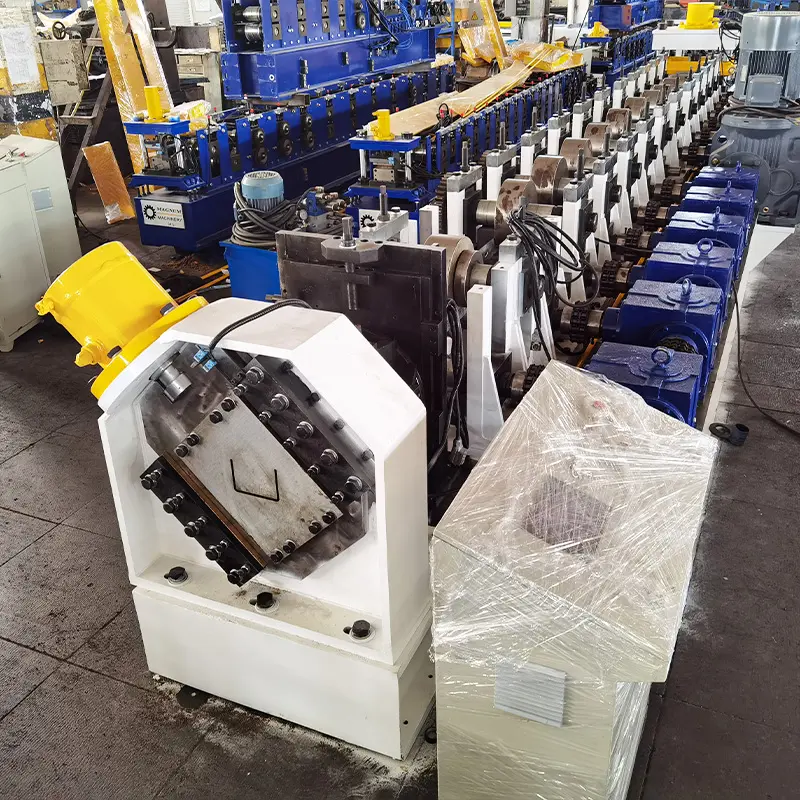
Production Process
At the heart of these machines lies metal additive manufacturing (MAM) technology. Here’s a simplified breakdown of the process:
- Digital Design: Engineers create a 3D model of the desired car profile using computer-aided design (CAD) software.
- Material Preparation: Metal powder, chosen for its specific properties, is fed into the machine’s hopper. Popular metal powder models include:
- 17-4 PH Stainless Steel: Offers high strength, good corrosion resistance, and weldability.
- 316L Stainless Steel: Known for its excellent corrosion resistance, making it ideal for exposed car parts.
- Maraging Steel: Provides superior strength and toughness, suitable for high-performance vehicles.
- Aluminum Alloys: Offer a lightweight option with good strength-to-weight ratio, improving fuel efficiency.
- Titanium Alloys: Possess exceptional strength and weight-saving capabilities, but are typically more expensive.
- Nickel-based Superalloys: Deliver high-temperature resistance and strength, ideal for engine components.
- Copper Alloys: Exhibit excellent thermal and electrical conductivity, useful for heat exchangers and wiring components.
- Inconel Alloys: Offer high-temperature resistance and resistance to harsh environments, making them suitable for exhaust systems.
- Tool Steels: Provide high wear resistance for parts subjected to friction and wear.
- Cobalt Chrome Alloys: Exhibit excellent wear resistance and corrosion resistance, making them ideal for demanding applications.
- Layer-by-Layer Building: The machine uses a laser beam or electron beam to melt the metal powder layer by layer, following the digital design.
- Support Structure Removal: Once complete, the support structures holding the part during printing are removed.
- Finishing: The final part may undergo post-processing steps like heat treatment or machining for additional strength and surface finish.
Think of it like building a car with Legos, but instead of plastic bricks, you’re using layers of metal powder. Each layer meticulously fuses with the previous one, creating the desired shape with remarkable precision.
The Application of Automobile Profile Making Machines
Automobile profile making machines find application in various areas of car manufacturing, including:
- Prototyping: Quickly and cost-effectively create prototypes for new car models, allowing designers and engineers to test form, fit, and function before mass production.
- Low-volume production: Manufacture limited-edition cars, custom parts, or spare parts for older models where traditional production methods might be uneconomical.
- Performance parts: Create lightweight and high-strength components like engine brackets, suspension parts, and aerodynamic elements.
- Interior components: Design and fabricate personalized or customized interior elements like cup holders, door handles, or dashboard panels.
These machines empower car manufacturers with unprecedented flexibility and customization capabilities, opening doors for innovative car designs and personalized driving experiences.
-
Highway Guardrail End Terminal Forming Machine
-
Highway U/C Post Roll Forming Machine
-
2 Waves Highway Guardrail Roll Forming Machine
-
3 Waves Highway Guardrail Roll Forming Machine
-
Auto Size Changeable Sigma Purlin Roll Forming Machine
-
Auto Size Changeable C Z Purlin Roll Forming Machine
-
Auto Size Changeable Z Purlin Roll Forming Machine
-
Auto Size Changeable C U Purlin Roll Forming Machine
-
Electrical Cabinet Frame Roll Forming Machine
Benefits of Automobile Profile Making Machines
Compared to traditional car manufacturing methods like stamping and forging, AM offers several advantages:
- Design freedom: Create complex geometries and intricate details not possible with traditional methods.
- Lightweight construction: Utilize lightweight materials like aluminum alloys to improve fuel efficiency and performance.
- Reduced waste: Eliminate the need for extensive tooling and minimize scrap material, promoting sustainability.
- On-demand production: Produce parts only as needed, reducing inventory costs and storage space.
- Faster time to market: Prototype and iterate designs quickly, accelerating the development process.
Think of AM as a sculptor’s chisel for car manufacturing, allowing the creation of intricate shapes with minimal material waste.
Limitations of Automobile Profile Making Machines
Despite their potential, AM technologies still face some challenges:
- Cost: The machines and metal powders can be expensive, making them less suitable for mass production of high-volume car models.
- Build size: Current machines have limitations on the size of parts they can produce, restricting their application for entire car bodies.
- Surface finish: Achieving a smooth surface finish comparable to traditional methods might require additional post-processing, adding to the cost and time.
- Material limitations: While the range of metal powders is expanding, some materials with specific properties might not yet be readily available for AM.
These limitations are actively being addressed through ongoing research and development. As technology advances, we can expect AM to become more cost-effective, faster, and capable of handling larger parts with improved surface finishes and a wider range of material options.
Future Potential of Automobile Profile Making Machines
The future of automobile profile making machines is bright, with the potential to revolutionize car manufacturing in several ways:
- Mass customization: AM’s ability to create personalized car parts could pave the way for mass customization, allowing customers to tailor their cars to their specific needs and preferences.
- Complex and lightweight structures: Advancements in AM technology might enable the creation of even more intricate and lightweight car structures, further improving fuel efficiency and performance.
- Distributed manufacturing: AM’s decentralized nature could lead to the establishment of smaller, localized manufacturing facilities, bringing production closer to consumers and reducing transportation costs.
- Sustainable manufacturing: Reduced waste, on-demand production, and the potential to use recycled metal powders contribute to a more sustainable car manufacturing process.
Imagine a future where you can walk into a car dealership and not just choose a color, but personalize the interior layout, add custom features, and even have the car manufactured locally using sustainable practices. This future is closer than you might think, thanks to the ever-evolving capabilities of automobile profile making machines.
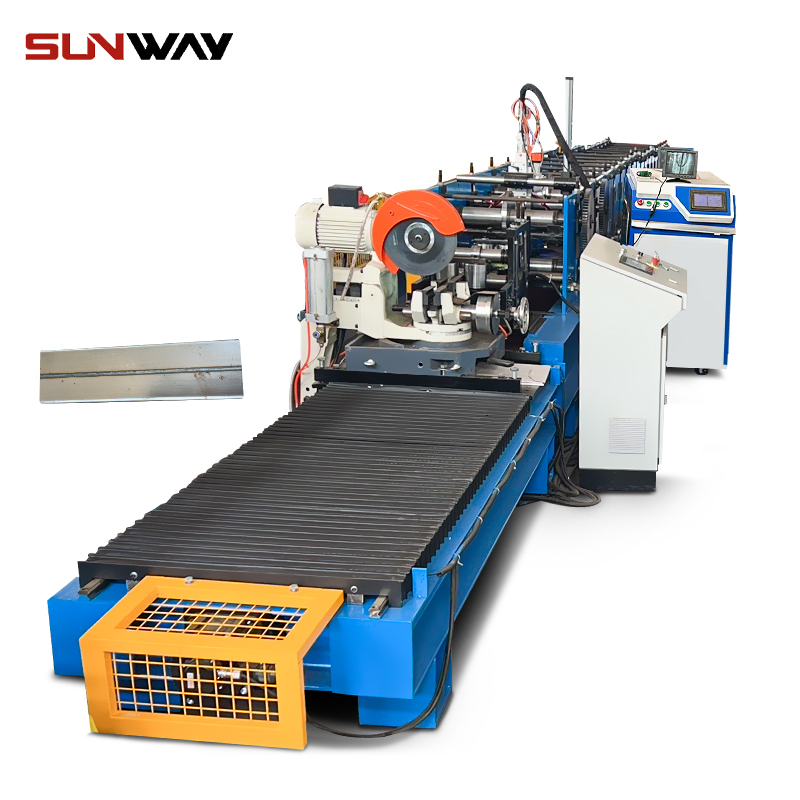
FAQ
Q: What are the different types of metal additive manufacturing (MAM) technologies used in automobile profile making machines?
A: Two main technologies are used:
- Laser Beam Melting (LBM): A high-powered laser beam melts the metal powder layer by layer.
- Electron Beam Melting (EBM): A focused electron beam melts the metal powder in a vacuum chamber, offering higher density and improved mechanical properties for the final part.
Q: How strong are parts made using automobile profile making machines?
A: The strength of the parts depends on the chosen metal powder and the specific AM process used. However, AM parts can achieve strength comparable to traditionally manufactured parts, and in some cases, even exceed them.
Q: Are there any safety concerns associated with automobile profile making machines?
A: As with any industrial process, safety precautions are necessary. These machines involve high temperatures and potential hazards like laser radiation or metal dust. However, proper training, personal protective equipment, and adherence to safety protocols can mitigate these risks.
Q: What is the future of automobile profile making machines?
A: The future is promising, with continuous advancements in technology expected to address current limitations and unlock new possibilities. We can anticipate faster build times, larger build volumes, wider material options, and potentially even lower costs, making AM an even more attractive proposition for car manufacturers.
In conclusion, automobile profile making machines represent a significant leap forward in car manufacturing. By offering design freedom, lightweight construction, and on-demand production capabilities, these machines are paving the way for a future of personalized, sustainable, and innovative car design.