Roll forming machines have revolutionized the manufacturing industry, providing a seamless and efficient way to shape metal. The process involves continuously bending a long strip of metal (typically coiled steel) into a desired cross-section. The need for precision and efficiency in metal forming has led to the development of advanced automatic roll forming machines. This comprehensive guide will delve into everything you need to know about these machines, from their working process and key components to their applications and how to choose the right supplier.
Overview of Automatic Roll Forming Machines
Automatic roll forming machines are vital tools in the metalworking industry. These machines automate the process of shaping metal sheets into specific profiles with high precision and efficiency. They are used in various industries, including construction, automotive, and aerospace, to produce parts such as roof panels, door frames, and structural components.
Key Features:
- Precision: Ensures exact measurements and uniformity across all products.
- Speed: High-speed models significantly increase production rates.
- Automation: Minimizes human intervention, reducing labor costs and human error.
- Versatility: Can produce a wide range of profiles and shapes.
Roll Forming Machine Guide
Understanding the different aspects of roll forming machines is crucial for making informed decisions. Here, we will guide you through the types, working processes, and essential components of these machines.
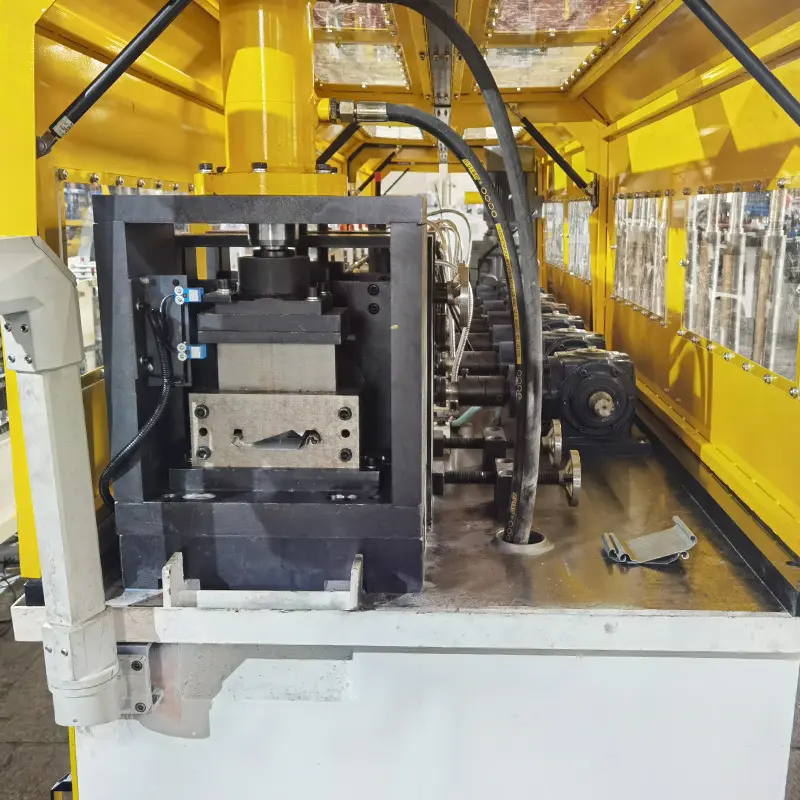
Types of Roll Forming Machines
Machine Type | Description |
---|---|
Single Head Roll Forming Machine | Utilized for simple profiles and smaller production runs. |
Double Head Roll Forming Machine | Allows for more complex profiles and higher production rates. |
High-Speed Roll Forming Machine | Designed for maximum efficiency and speed, ideal for large-scale operations. |
Precision Roll Forming Machine | Offers the highest level of accuracy, suitable for critical applications. |
Modular Roll Forming Machine | Provides flexibility with interchangeable parts for different profiles. |
Custom Roll Forming Machine | Tailored to specific production needs and profiles. |
Hydraulic Roll Forming Machine | Uses hydraulic power for more robust forming capabilities. |
Servo Roll Forming Machine | Features servo motors for enhanced control and precision. |
Portable Roll Forming Machine | Compact and mobile, ideal for on-site forming tasks. |
Multi-Profile Roll Forming Machine | Capable of producing multiple profiles without extensive retooling. |
Working Process of High-Speed Roll Forming Machines
The high-speed roll forming process involves several steps, each crucial for achieving the desired profile with precision and efficiency.
- Uncoiling: The metal coil is placed on an uncoiler, feeding the strip into the machine.
- Feeding: The metal strip is guided through a series of rollers, which gradually bend it into the desired shape.
- Forming: Successive sets of rollers incrementally shape the metal, ensuring precision and uniformity.
- Cutting: The formed metal is cut to the desired length using an automated cutting system, often integrated into the roll forming machine.
- Stacking: The finished pieces are collected and stacked for further processing or packaging.
Key Components and Their Functions
Component | Function |
---|---|
Uncoiler | Holds and feeds the metal coil into the machine. |
Rollers | Incrementally bend and shape the metal strip. |
Drive System | Powers the rollers and ensures smooth operation. |
Cutting Mechanism | Cuts the formed metal to the desired length. |
Control System | Manages the machine’s operations, ensuring precision and efficiency. |
Stacking System | Collects and organizes the finished products. |
Hydraulic System | Provides additional power for robust forming tasks. |
Servo Motors | Enhance control and precision of the forming process. |
Safety Guards | Ensure operator safety during machine operation. |
Lubrication System | Maintains smooth operation by reducing friction and wear. |
Machine Speed and Efficiency
Model | Speed (m/min) | Efficiency |
---|---|---|
High-Speed Model A | 100 | High efficiency, suitable for large-scale production. |
High-Speed Model B | 120 | Ultra-high efficiency, ideal for continuous production. |
Precision Model C | 80 | High precision with moderate speed. |
Standard Model D | 60 | Balanced speed and efficiency for general use. |
-
Highway Guardrail End Terminal Forming Machine
-
Highway U/C Post Roll Forming Machine
-
2 Waves Highway Guardrail Roll Forming Machine
-
3 Waves Highway Guardrail Roll Forming Machine
-
Vineyard Post Roll Forming Machine
-
Auto Size Changeable Sigma Purlin Roll Forming Machine
-
Auto Size Changeable C Z Purlin Roll Forming Machine
-
Auto Size Changeable Z Purlin Roll Forming Machine
-
Auto Size Changeable C U Purlin Roll Forming Machine
Customized Mechanical Parameters
Parameter | Value |
---|---|
Width Range | 100-800 mm |
Thickness Range | 0.3-3.0 mm |
Material Type | Steel, Aluminum, Copper |
Profile Type | U-Shape, C-Shape, Z-Shape |
Roller Material | High-Grade Steel |
Cutting Method | Hydraulic, Servo, Mechanical |
Applications and Uses
Automatic roll forming machines are used in various industries due to their versatility and efficiency.
Industry | Application |
---|---|
Construction | Roof panels, wall panels, door frames. |
Automotive | Chassis components, body panels. |
Aerospace | Structural components, fuselage parts. |
Electrical | Cable trays, enclosures. |
Furniture | Frames, supports. |
Energy | Solar panel frames, wind turbine parts. |
Agriculture | Machinery components, fencing. |
Transportation | Rail car parts, shipping containers. |
Packaging | Metal boxes, cans. |
HVAC | Ductwork, vent covers. |
Installation, Operation, and Maintenance
Proper installation, operation, and maintenance are crucial for the longevity and efficiency of roll forming machines.
Aspect | Details |
---|---|
Installation | Ensure a stable foundation, proper alignment of components, and secure electrical connections. |
Operation | Follow the manufacturer’s guidelines, conduct regular inspections, and ensure operator training. |
Maintenance | Regular lubrication, checking for wear and tear, replacing damaged parts, and keeping the machine clean. |
Suppliers and Price Range
Choosing the right supplier is essential for getting a reliable and efficient roll forming machine.
Supplier | Price Range |
---|---|
ABC Machinery | $50,000 – $100,000 |
XYZ Industries | $75,000 – $150,000 |
RollFormTech | $60,000 – $120,000 |
Forming Solutions | $80,000 – $140,000 |
MetalMaster | $70,000 – $130,000 |
Prime Rollers | $90,000 – $160,000 |
Precision Formers | $85,000 – $145,000 |
TechRollers | $65,000 – $125,000 |
SpeedyForm | $100,000 – $180,000 |
CustomForm Inc. | $95,000 – $170,000 |
How to Choose a Supplier
Selecting the right supplier involves considering several factors to ensure you get the best machine for your needs.
- Reputation: Look for suppliers with positive reviews and a good track record.
- Experience: Experienced suppliers are more likely to offer reliable and advanced machines.
- Support: Ensure the supplier provides excellent after-sales support and training.
- Customization: Check if the supplier can customize the machine to your specific requirements.
- Price: Compare prices and ensure you get value for your investment.
Pros and Cons of Automatic Roll Forming Machines
Aspect | Advantages | Disadvantages |
---|---|---|
Precision | High accuracy and uniformity. | Requires precise calibration. |
Speed | Fast production rates. | Initial setup can be time-consuming. |
Automation | Reduces labor costs and human error. | High initial investment. |
Versatility | Can produce various profiles. | Limited to specific material types and thicknesses. |
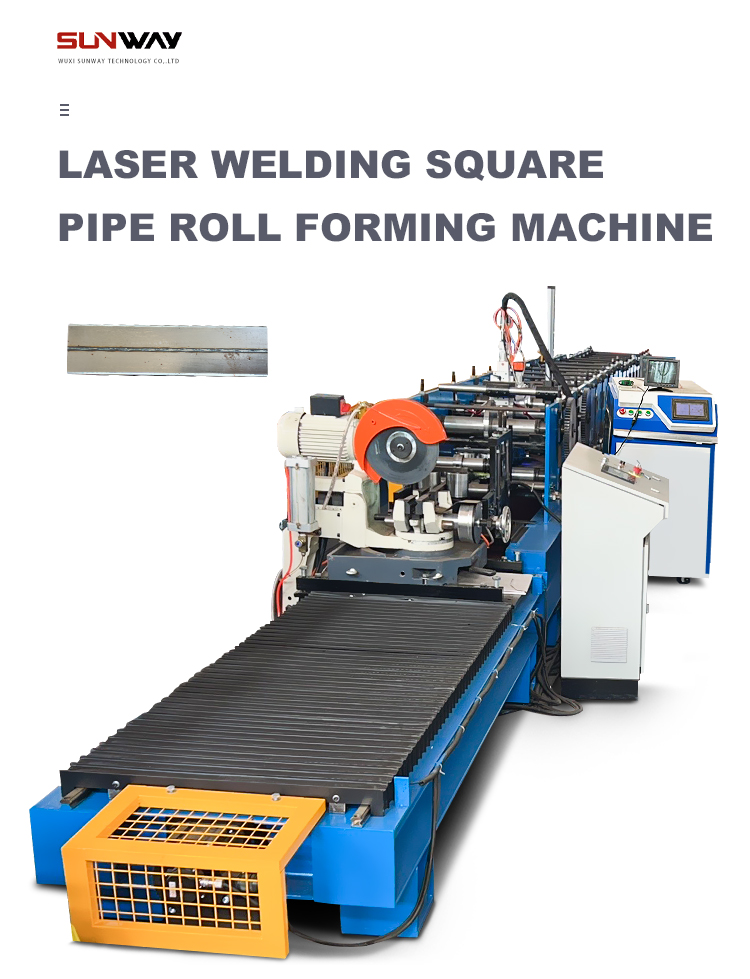
FAQ
Question | Answer |
---|---|
What is an automatic roll forming machine? | It is a machine that automates the process of shaping metal sheets into specific profiles using rollers. |
How does a roll forming machine work? | It feeds a metal strip through a series of rollers that gradually bend it into the desired shape. |
What are the benefits of using an automatic roll forming machine? | Benefits include high precision, fast production, reduced labor costs, and versatility. |
Can roll forming machines be customized? | Yes, many suppliers offer customized machines to meet specific production needs. |
What materials can be used in roll forming machines? | Common materials include steel, aluminum, and copper. |
How do I maintain a roll forming machine? | Regular maintenance includes lubrication, checking for wear and tear, and keeping the machine clean. |
What industries use roll forming machines? | Industries include construction, automotive, aerospace, electrical, and more. |
What is the price range for roll forming machines? | Prices typically range from $50,000 to $180,000, depending on the model and features. |
How do I choose the right roll forming machine supplier? | Consider factors like reputation, experience, support, customization options, and price. |
What are the main components of a roll forming machine? | Key components include the uncoiler, rollers, drive system, cutting mechanism, and control system. |