Door frame roll forming machines are equipment used to automatically bend metal coils into customized door frame profiles. This equipment is versatile, efficient, and delivers quality end products for door frame manufacturing.
Roll formed door frames have several benefits compared to traditional fabrication methods:
- More uniform profile dimensions
- Higher production rates
- Lower labor requirements
- Consistent quality and precision
- Flexibility to create custom frame designs
This guide will cover the working process, types, features, parameters, applications, operation, suppliers, costs, pros/cons, and FAQs about door frame roll forming lines.
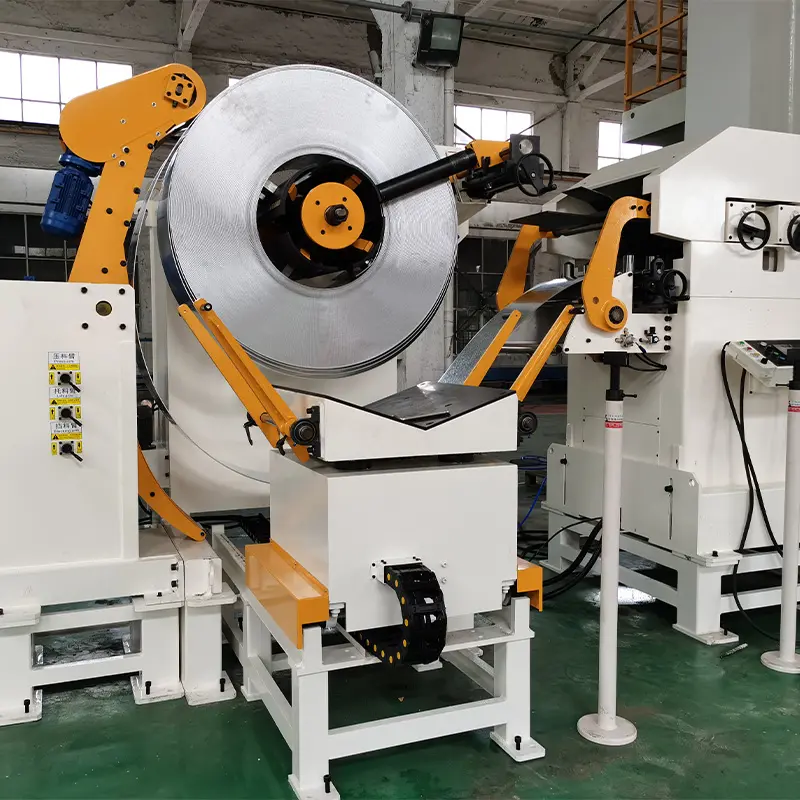
How Door Frame Roll Forming Machines Work
The roll forming working principle involves feeding metal coil strips through a series of roller dies to shape the material incrementally into chosen frame cross-sections…
Types of Door Frame Roll Formers
There are two main categories of lines for roll forming door frame profiles:
Type 1: Automatic Cut-to-Length Roll Forming Lines
These systems roll form the metal coil into door frame sections of fixed length as per order requirements. They incorporate a cutting unit to automatically cut profiles to customized sizes.
Key Components: Decoiler, guiding rolls, forming stations, cutting unit, PLC control
Benefits: High degree of automation, consistency, and efficiency
Type 2: Variable Length Roll Forming Machines
These roll formers produce frame profiles in continuous lengths rather than fixed sizes. They require manual cutting post-production to cut sections at desired lengths.
Key Components: Decoiler, forming stations, pinch rolls, manual cutting post-production
Benefits: Flexibility in production planning, lower cost
Comparison of Roll Former Types
Parameter | Type 1 Cut-to-Length | Type 2 Variable Length |
---|---|---|
Automated Cutting | Yes | No, manual post-production cutting needed |
Length Flexibility | Low, fixed cut sizes | High, continuous lengths produced |
Process Control | High degree via PLC | Medium, manual monitoring required |
Productivity | Higher, efficient inline process | Lower, additional processing step |
Equipment Costs | Higher due to cutting unit | Lower without built-in cutting |
Working Process of Roll Forming Machines
The step-by-step working methodology to create door frames on these machines involves:
1. Material Feed
- Decoiler feeds metal coil strip into roll former
- Guide rolls straighten strip
2. Forming
- Sheet passes through series of roller dies
- Rollers bend strip incrementally
- Profile is gradually formed across stations
3. Door Frame Design and Dimension
- Roller dies customize frame design and dimensions
- Various cross-sections like rectangular, round, etc. achieved
4. Cutting (for Type 1 machines)
- Cutting unit sizes profiles at fixed lengths
- PLC automatically sets cut lengths
5. Output
- Formed door frames collected at the end
- Manual bundling and storage follows
Typical Roll Forming Line Layout
The major sub-systems like decoiler, forming stands with roller dies, and cutting unit (if included) are labeled.
-
Rolling Shutter Slat Roll Forming Machine
-
Highway Guardrail End Terminal Forming Machine
-
Highway U/C Post Roll Forming Machine
-
2 Waves Highway Guardrail Roll Forming Machine
-
3 Waves Highway Guardrail Roll Forming Machine
-
Electrical Cabinet Frame Roll Forming Machine
-
Din Rail Roll Forming Machine
-
Two waves highway guardrail machine
-
Three waves highway guardrail machine
Key Features of Door Frame Roll Forming Equipment
Roll forming machines can be customized with additional capabilities to enhance automation, precision, changeovers, and monitoring.
Feature | Details | Benefits |
---|---|---|
Servo Feeding | Servo motors on decoiler | Accurate speed/tension control |
Auto Lubrication | Automated oiling to rollers | Reduced manual maintenance |
Quick Die Change | Tool-less die change parts | Faster profile changeovers |
Profile Monitoring | Laser or camera inspection | Improved quality control |
Touchscreen HMI | User-friendly interface | Enhanced production management |
Data Logging | Tracking production metrics | Monitoring efficiency |
Key Technical Parameters
Roll forming equipment have different capacity ratings and capabilities to suit production needs:
Parameter | Typical Range |
---|---|
Metal Thickness | 0.15 – 1 mm |
Strip Width | 50 – 200 mm |
Production Speed | 10 – 25 m/min |
Profile Width | 50 – 300 mm |
Cut Lengths | 1000 – 6000 mm |
Modern lines have a modular designs for flexibility to create small to large door frame sections by changing components.
Application Areas
Door frame roll forming technology is widely used across industries requiring metal door frames:
- Residential Buildings
- Commercial Spaces
- Industrial Structures
- Infrastructure Projects
Common materials used are:
- Mild Steel
- Stainless Steel
- Aluminum
From small homes to large warehouses, roll formed door frames provide structural integrity.
Choosing Right Roll Forming Machine Supplier
Selecting an ideal roll forming equipment partner involves:
Parameter | Details |
---|---|
Experience | Number of years providing machines |
Domain Expertise | Depth of knowledge in technology |
Customization | Capability to tailor lines to needs |
Cost | Pricing fitting budget |
Lead Time | Delivery schedules |
Support | Installation, training, maintenance |
Reliability | Build quality for uptime |
Overall Reputation | Market trust and customer reviews |
Analyze above factors thoroughly while shortlisting vendors.
Pros and Cons of Roll Forming Process
Pros | Cons |
---|---|
Automated process | High initial capital expenditure |
High production rates | Complex maintenance procedures |
Dimensional accuracy | Lack of flexibility to profile changes |
Excellent surface finish | Limited formability for certain designs |
Material savings from coil inputs | Require skilled technicians for operation |
Lower long term costs than fabrication | Layout space needed for equipment |
Cost Analysis
Cost Component | Price Range |
---|---|
Equipment Purchase | $10000 – $50000 |
Spare Parts | $2000 per year |
Installation | $1500 upwards |
Energy Consumption | ~$5 per hour |
Total cost for the roll forming line depends on:
- Automation extent
- Production capacity
- Additional capabilities
Economies of scale apply – higher throughput lines provide lowest cost per door frame.
Top Door Frame Roll Forming Machine Manufacturers
Company | Location | Contact |
---|---|---|
Botou Xianfa | China | web: www.rollformingmachine.net |
Jingxing Rollforming | China | email: [email protected] |
Shanghai Metal Corporation | China | phone: +862160882528 |
SASCO | India | website: sascopvtltd.com |
Agile Rollers | UK | phone: +44 07538 799536 |
The above companies provide customizable roll forming solutions catered to door frame production needs and budgets.
Maintenance and Operation
Follow standard protocols for operation and maintenance:
Activity | Frequency | Details |
---|---|---|
Machine Inspection | Daily | Check rollers, wires, sensors |
Lubrication | Weekly | Grease bearings and pins |
Safety Checks | Monthly | Ensure guards and stops working |
System Upgrades | Yearly | Update software and hydraulics |
Proper maintenance as per schedule improves uptime. Monitor wear on consumables like rollers for timely replacement.
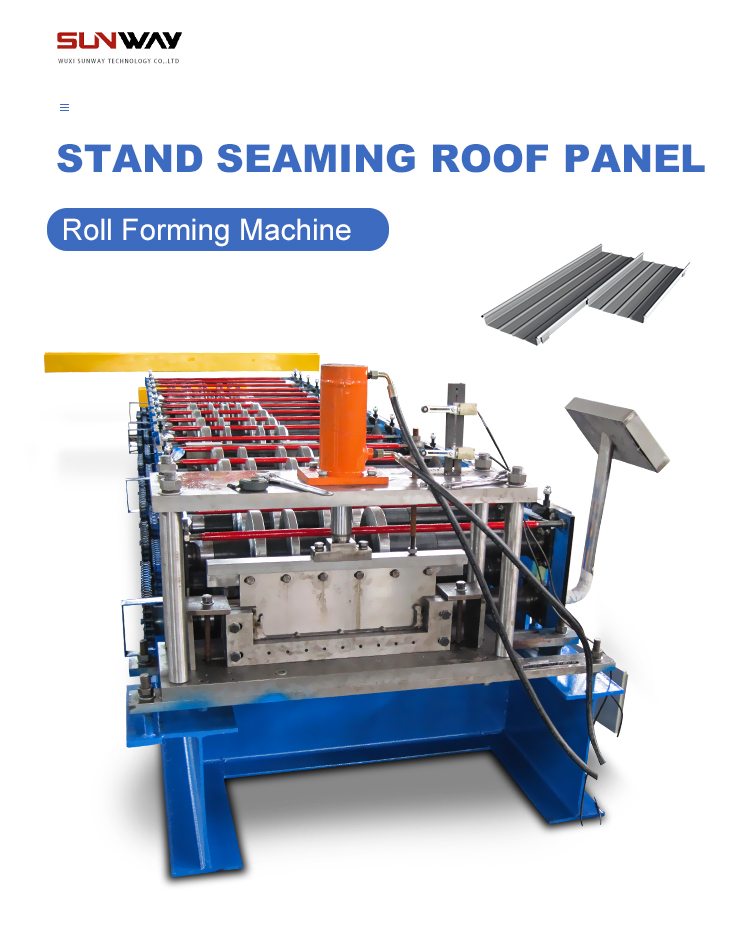
FAQ
Q: What sheet metal thickness can be roll formed?
A: Standard machines handle 0.15 mm to 1 mm thickness. Higher rigidity models available for thicker sheets like 1.2 mm.
Q: What alloys are compatible for door frames?
A: Mild steel, stainless steel 304/316, aluminum 6061 are commonly roll formed alloys.
Q: What is the fastest production rate for lines?
A: High speed servo motor CNC models output ~25 meters/minute.
Q: What profile dimensions are possible?
A: 50 mm x 50 mm to 300 mm x 100 mm profiles can be produced.
Q: Is surface coating like powder coating possible inline?
A: Separate powder coating line needed after roll forming process.
Q: What is the lifespan for these machines?
A: Approximately 15 years with proper maintenance and part replacements.