Floor decks are corrugated structural sheets providing the base for concrete slabs in buildings. Roll forming offers a continuous, efficient process to mass produce steel floor decking. This guide covers the end-to-end system for setting up steel deck production lines.
Overview of steel floor decking roll forming machine
Roll forming shapes steel coils into various floor decking profiles using consecutive roller dies. Key benefits include:
- High throughput for cost efficiency
- Flexible output with quick die changeovers
- Consistent quality with precision tolerances
- Small equipment footprint for space savings
- On-demand just-in-time supply avoiding inventories
- Fully automatic for reduced direct labor
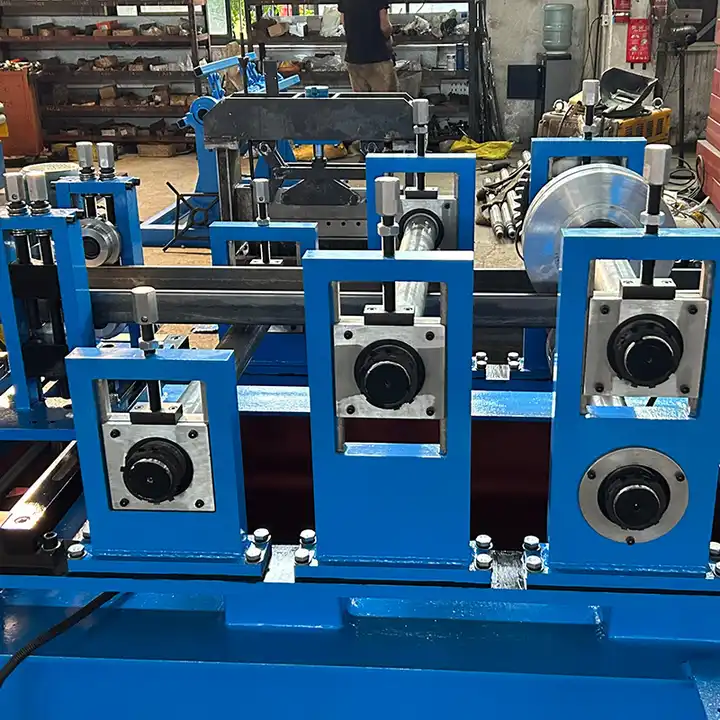
Main Components of steel floor decking roll forming machine
Table 1: Key Components of a Steel Floor Deck Roll Line
Component | Description | Purpose |
---|---|---|
Decoiler | Unwinds raw steel coils | Feeds strip stock into system |
Feed table | Supports strip before forming | Provides stability |
Forming stations | House profile shaping rolls | Incremental bending |
Flying shear | Cuts sheets off main strip | Chops sheets to length |
Delivery table | Catches cut sheets | Collects production |
- Decoiler: Pays off coil stock into the roll former
- Feed table: Pre-forming material guidance
- Forming stations: Progressively bend strip
- Flying shear: Cuts finished profiles from strip
- Delivery table: Gathers formed sheets
Profile Options for Steel Floor Decks
Typical decking profiles made by steel roll forming include:
Table 2: Common Steel Floor Deck Profiles
Profile shape | Description | Characteristics |
---|---|---|
Trapezoidal | Angled fluted cross-section | Good concrete bond |
Re-entrant | Inverted bottom ribs | Low structural depth |
Cellular | Fully enclosed bottom face | Increased load capacity |
Dovetail | Interlocking side hooks | Alignment of adjacent sheets |
Sinusoidal | Wavy profile | Composite interaction with concrete |
- Trapezoidal: Angled flutes provide mechanical keying
- Re-entrant: Bottom ribs enhance strength
- Cellular: Closed structure for robustness
- Dovetail: Edge geometry aligns overlapping sheets
- Sinusoidal: Curvature aids concrete bonding
Choosing suitable shapes boosts structural performance.
Technical Specifications
Key parameters for customizing steel floor deck roll lines are:
Table 3: Typical Specifications of Roll Formed Steel Floor Decks
Parameter | Range | Unit |
---|---|---|
Line speed | 10 – 35 | m/min |
Forming stations | 12 – 24 | Nos. |
Material thickness | 0.7 – 2 | mm |
Sheet width | 750 – 1500 | mm |
Sheet length | 500 – 8000 | mm |
Installed load | 15 – 60 | kW |
- Speed: Production rate capability
- Stations: Number of profile shaping stands
- Thickness: Raw material coil gauge
- Sheet size: Formed part dimensions
- Power needs: Electricity supply
The optimum specification combination depends on performance targets, space availability, and budget.
Strip Stock Feed Options
The common material inputs for steel floor decking are:
Table 4: Strip Stock Feeding Methods into Roll Lines
Method | Description | Suitability |
---|---|---|
Automatic coil carousel | Rotates multiple coils sequentially | Unmanned high-volume production |
Coil joining | Butt-welds tail of exhausted coil to new head | Mid-volume, non-stop input |
Manual loading | Operator replaces depleted coils | Low-volume batches, prototyping |
- Carousel: Allows automatic sequential coil changeovers
- Joining: Provides continuous welding of coil ends
- Manual: Operator replaces empty coils
Higher automation levels minimize downtimes needed for coil replenishment.
Post-Forming Secondary Operations
Typical post-roll forming processes are:
Table 5: Common Post-Forming Operations for Steel Floor Decks
Process | Method | Purpose |
---|---|---|
Cutting | Flying shear on exit end | Chops sheets from continuous strip |
Hole punching | Pneumatic hole punch station | Service holes or alignment gaps |
Embossing | Inkjet or laser marking | Sheet numbering, logos |
Stack handling | Mechanical arms, bins | Organize sheets before transport |
- Cutting: Separates sheets from continuous strip
- Punching: Punctures sheet for ducting access
- Embossing: Identification and traceability
- Stack handling: Systematic palletizing
Efficient post-processing avoids output bottlenecks after forming.
-
Electrical Cabinet Frame Roll Forming Machine
-
Din Rail Roll Forming Machine
-
Cable Ladder Roll Forming Machine
-
PV Mounting Bracket C Shape Profile Roll Forming Machine
-
Cable Tray Roll Forming Machine
-
PV Mounting Bracket Roll Forming Machine (HAT / Omega Profile)
-
PV Mounting Bracket Z Shape Profile Roll Forming Machine
-
Solar mounting strut channel roll forming machine
-
Strut Channel Roll Forming Machine
Global Manufacturers
Table 6: Leading International Steel Floor Deck Roll Former Manufacturers
Company | Headquarters | Contact |
---|---|---|
Gasparini | Italy | [email protected] |
Epic | USA | [email protected] |
Sigma | Turkey | [email protected] |
FZTechnik | Germany | [email protected] |
Joung Jin | South Korea | [email protected] |
- Gasparini: Robust European-built production lines
- Epic: Custom USA-made roll forming equipment
- Sigma: Reliable Turkish roll former OEMs
- FZTechnik: High-precision German engineering
- Joung Jin: Cost-effective Korean manufacturer
These companies offer turnkey deck roll forming equipment solutions.
Indicative Pricing
Table 7: Typical Price Ranges for Steel Deck Roll Lines
Production speed | Price range |
---|---|
10 – 20 m/min | $40,000 – $85,000 |
20 – 30 m/min | $85,000 – $170,000 |
30 – 40 m/min | $170,000 – $260,000 |
Influencing cost factors:
- Desired output rate and automation level
- Overall line length based on part sizes
- Type and number of ancillary modules
- Customization needs for profile and accessories
- Brand value of equipment OEM
- Taxes and shipment costs
Higher flexible lines enable rapid product changes but cost more upfront. Starting smaller and incrementally expanding production capacity keeps initial spends lower.
Installation and Commissioning
Key tasks in installing steel floor decking roll lines:
Table 8: Roll Line Installation Activities
Task | Description | Purpose |
---|---|---|
Site preparation | Floor flatness/leveling, access routes | Stable foundation |
Positioning | Set proper machine clearances | Smooth material flow |
Anchoring | Anchor to ground using bolts | Prevent vibrational drifts |
Alignment | Orient and level forming sections | Decentered rolls distort material flow |
Connection | Electrical, hydraulic, pneumatic systems | Actuate motors and actuators |
Safety | Guarding, emergency switches | Protect operators |
Trial runs | Validate performance before production | Reduce debug time losses |
Careful installation enhances equipment lifetime and avoids defects from component misalignment. Thorough testing during commissioning decreases faults occurring mid-production.
Maintenance Activities
Proactive servicing of steel floor deck roll lines involves:
Table 9: Recommended Maintenance Schedule
Frequency | Task | Purpose |
---|---|---|
Daily | Fluid level checks, leak fixes | Prevent unplanned stoppages |
Weekly | Sensor recalibration | Ensure correct strip tracking |
Monthly | Lubricate moving sub-assemblies | Reduce friction and wear |
Quarterly | Re-alignment if needed | Re-orient forming sections |
Annually | Oil changes for gearboxes | Extend mechanical lifetime |
As-needed | Worn component replacement | Restore normal function |
- Inspections: Early detection of issues
- Recalibration: Maintain output accuracy
- Lubrication: Smooth low-friction operation
- Re-alignments: Restore directionality
- Fluid changes: Keep oil contaminant-free
- Part replacement: Fix faulty components
Scheduled preventive servicing minimizes unplanned line stoppages and quality defects.
Supplier Selection Guidelines
The key parameters for evaluating steel deck roll former manufacturers are:
Table 10: Comparison Criteria for Steel Deck Line OEMs
Factor | Description |
---|---|
Experience | Successfully built reference plants |
Quality | Use branded components and robust fabrication |
Customization | Offer needed specification range |
Design support | Help optimize forming process |
Responsiveness | Quick issue resolution |
Delivery | On-time equipment availability |
Cost | Competitive pricing agreeing to budget |
- Experience: Domain expertise benefits product design
- Quality: Reliable equipment with longevity
- Customization: Meet production targets
- Design support: Ensure process optimization
- Responsiveness: Support post-order and during production
- Delivery: Prevent project delays
- Cost: Reasonable pricing and payment terms
Evaluating OEMs on these aspects minimizes project execution risks.
Benefits of steel floor decking roll forming machine
Table 11: Advantages and Limitations of Roll Forming Decks
Pros | Cons |
---|---|
High production speeds | Significant initial capital cost |
Continuous processing method | Complex programming for new profiles |
Consistent quality and precision | Limited raw material coil width constrains part sizes |
Lower operating costs through automation | Downtime for die changeovers during profile switches |
On-demand just-in-time supply | Require auxiliary equipment like decoilers, straighteners etc |
Compact equipment footprint | Skilled workforce needed for operation and maintenance |
Key Advantages:
- Fast forming rates reduce manufacturing costs
- Parameter controlled process ensures repeatable quality
- Lower long term overheads through automation
- Buffer inventory minimization with just-in-time production
- Scalable capacity upgrading through modular extensions
Major Limitations:
- Substantial initial investment requirement
- Multiple debugging iterations needed for new profiles
- Maximum sheet widths restricted by coil stock dimensions
- Production halts for die changeover during profile type switches
- Dependence on additional supporting equipment like decoilers, stackers etc.
- Specialized skill requirement for programming and maintenance
Understanding pros and cons allows suitable application of steel floor deck roll forming.
End Use Sectors
Typical buildings using steel floor decks:
Table 12: Major Building Types Using Roll Formed Steel Floor Decks
Sector | Application | Deck function |
---|---|---|
Warehouses | Distribution hubs | Platforms for storage racks |
High-rise | Office towers | Concrete floor slabs |
Bridges | Flyovers | Structural base |
Stadiums | Arenas | Multi-level stands |
Transport | Airport, metro stations | Terminals, elevated corridors |
- Warehouses: Structurally sound racking platforms
- High-rises: Reinforced heavy concrete floors
- Bridges: Load bearing structures
- Stadiums: Sloped spectator gallery slabs
- Transport hubs: Vast floor plates
Roll formed steel decks expedite construction across infrastructure sectors.
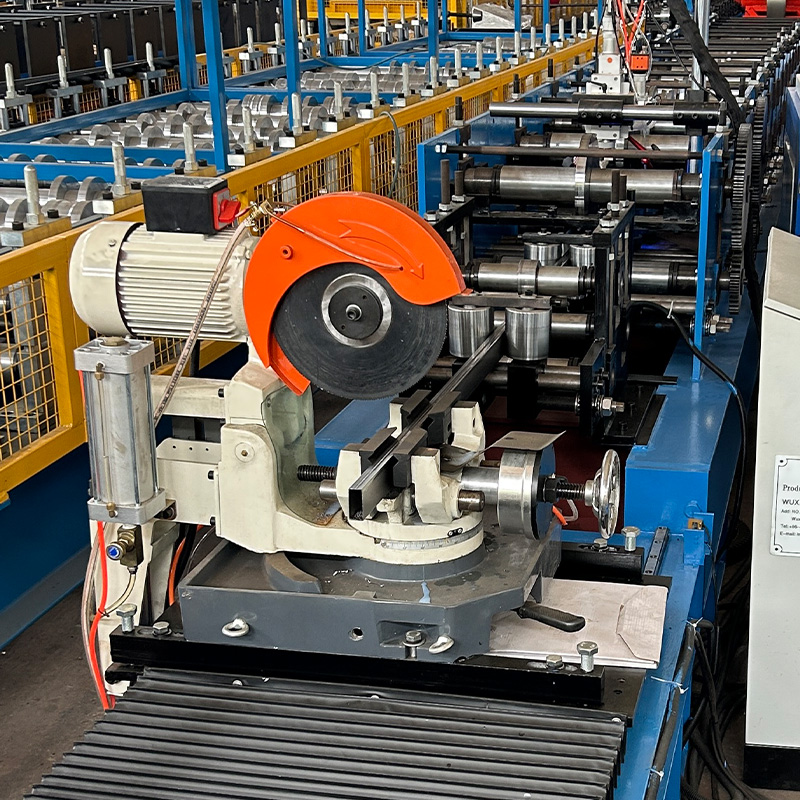
Frequently Asked Questions
Q: What type of steel is generally used for floor decks?
A: Hot-dip galvanized steel coils prevent deck corrosion and are commonly roll formed into floor decks.
Q: What thickness provides optimal strength?
A: Deck thicknesses between 0.9 – 1.2 mm offer adequate load capacity while avoiding excessive steel usage.
Q: How are deck sheets fixed to supporting structures?
A: Self-tapping concrete screws anchor overlapping deck sheets along the crest to purlins or beams before concrete topping.
Q: What special safety measures are needed when installing decks?
A: Permanent perimeter safety railing and temporary fall protection barriers safeguard workers placing decking sheets on elevated floors.
Q: Can custom patterns be incorporated on floor decks?
A: Yes, customized male-female roller dies can imprint specialized surface patterns inline during roll forming based on application needs.
Conclusion
Roll forming enables high volume manufacturing of various structural steel floor decking profiles. With comprehensive planning guided by this reference covering relevant equipment procurement aspects, manufacturers can gain strategic and economic benefits by adopting in-house deck production. The combination of efficiency, versatility and customizability makes roll forming ideal for developers needing large decking quantities.