A steel curving unistrut roll forming machine continuously cold forms metal coil strip into curved open channel structural sections like U-channel, furring channel and other framing members used for infrastructure and construction systems.
Overview of Steel Curving Unistrut Roll Forming Machines
Steel curving unistrut roll formers produce continuous lengths of shaped and curved metal open profiles from steel coil feedstock through a series of progressive die bending stations with efficient, automated production.
Key characteristics:
- Forms coils into various curved open channel shapes
- Adjustable curving from straight to fully curved
- Easy profile and size changeovers
- Used for studs, track, infrastructure framing
- Higher volumes and lower costs than fabrication
- PLC programmable for automation
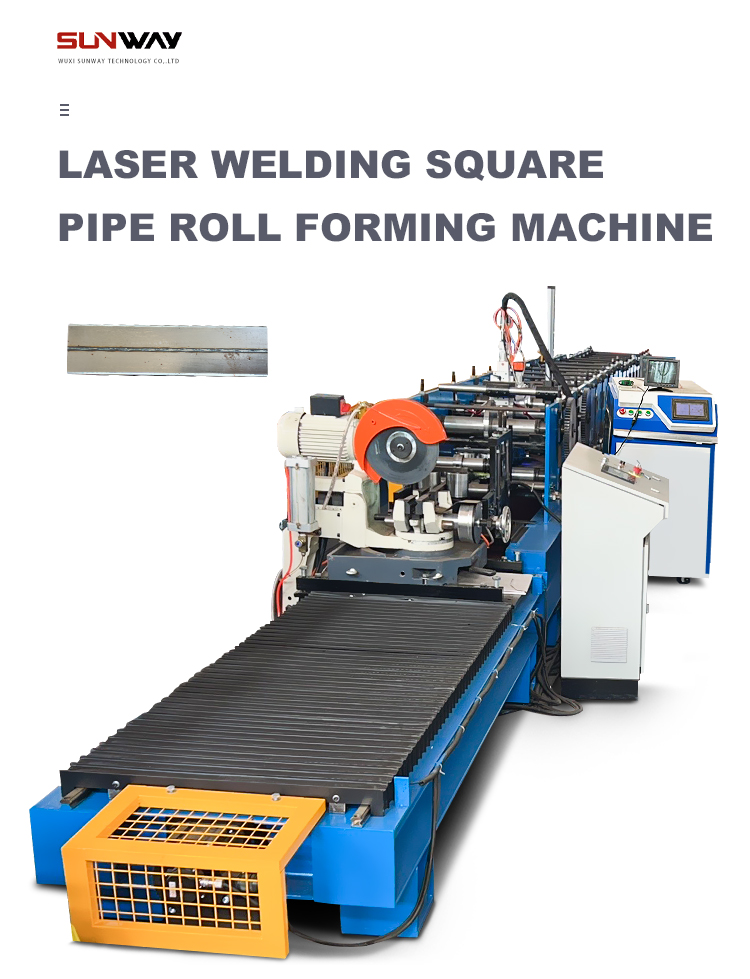
Types of Steel Curving Unistrut Roll Forming Machines
Type | Description |
---|---|
C-stud and track roll former | Wall framing channels |
Furring channel curving machine | Interior wall supports |
Curved strut roll former | Structural infrastructure channels |
Custom profile curving | Special architectural shapes |
Working Principle of Steel Curving Unistrut Roll Forming
How steel curving unistrut roll forming works:
- Coil strip pre-treated for optimal bendability
- Infeed guides align strip into roll former
- Forming stations gradually shape strip
- Top and bottom rolls perform progressive bending
- Adjustable rolls control curving amount
- Cutoff knives slice formed profiles
- Formed parts exit on conveyors
- PLC coordinates production
Features of Steel Curving Unistrut Roll Forming Machines
Feature | Details |
---|---|
Forming stands | Up to 20 for optimal shaping |
Rolls | Hardened or coated for wear resistance |
Decoilers | 5 ton capacity handles large coils |
Material feed | Servo motor with precision control |
Curving | Adjustable from straight to fully curved |
Flying cutoff | Rotary knives for square slicing |
Stacker | Automatic counting and bundling |
Materials for Steel Curving Unistrut Roll Forming
Suitable coil feedstock materials:
- Hot rolled steel – common baseline material
- High strength steel – for structural framing
- Galvanized steel – corrosion protection
- Prepainted steel – prefinished aesthetic
- Stainless steel – ultimate corrosion resistance
- Aluminum – lightweight framing
Profile Options for Steel Curving Unistrut Machines
Typical structural shape range includes:
- C-studs – 50 to 300 mm heights
- U-channels – 1″ to 12″ (25-300 mm)
- Furring channels – 3/4″ to 2-1/2″ (20-60 mm)
- Round tube – 1/2″ to 6″ diameter
- Square tube – 1″ to 12″ sizes
- Custom profiles
Quick Die Change Design for Steel Curving Unistrut Machines
Tooling designed for rapid profile changeovers:
- Two-piece split dies
- Hydraulic power clamps
- Assist cylinders on roll sets
- Preset length adjustment slots
- Color coded tools
- Minimal re-calibration needed
Additional Processing Options for Curved Roll Formed Parts
Optional integrated secondary processing:
- Hole punching
- Slot punching
- Embossing logos
- Component welding
- Corner notching
- Length cutting
- Powder coating
-
Electrical Cabinet Frame Roll Forming Machine
-
Din Rail Roll Forming Machine
-
Cable Ladder Roll Forming Machine
-
PV Mounting Bracket C Shape Profile Roll Forming Machine
-
Cable Tray Roll Forming Machine
-
PV Mounting Bracket Roll Forming Machine (HAT / Omega Profile)
-
PV Mounting Bracket Z Shape Profile Roll Forming Machine
-
Solar mounting strut channel roll forming machine
-
Strut Channel Roll Forming Machine
Global Manufacturers of Steel Curving Unistrut Roll Formers
Manufacturer | Location |
---|---|
ZHQ Roll Forming Machinery | China |
Gasparini | Italy |
Shanghai Rollwell | China |
Formtek | USA |
DIMECO | USA |
Top international suppliers with heavy industry experience.
Steel Curving Unistrut Roll Former Pricing
Production Class | Price Range |
---|---|
Light-duty | $55,000 – $95,000 |
Medium-duty | $75,000 – $120,000 |
Heavy-duty | $95,000 – $150,000 |
Costs vary based on speed, automation features, material flexibility, and integrated secondary processing. Significant regional differences exist.
Installation and Operation of Steel Curving Unistrut Machines
Proper installation helps ensure production quality and uptime. Operators should receive thorough procedural training.
Installation Best Practices
- Fixed, leveled mounting with vibration damping
- Sufficient power supply wiring
- Pneumatic lines with moisture separators
- Material decoiler capacity
- Safety guarding around all hazards
- Control panel positioned for convenience
- Lighting for visual inspection
- Shield curtains containment
Operational Procedures
- Review equipment safety procedures
- Ensure area is obstruction-free
- Verify electrical disconnect is locked open
- Energize hydraulic power units
- Set line speed and curving parameters
- Thread coil material through machine
- Initiate controlled startup sequence
- Monitor forming quality continuously
- Perform regular tooling inspections
- Log production output data
Follow all manufacturer instructions precisely.
Preventative Maintenance for Steel Curving Roll Machines
- Schedule periodic maintenance downtime
- Lubricate bearings every 40 hours
- Inspect pneumatic elements
- Check hydraulic fluid cleanliness
- Examine chains, sprockets, belts
- Touch up paint deterioration
- Maintain inventory of common spare parts
Extends equipment lifetime and prevents premature failures.
Purchasing Selection Factors for Steel Curving Unistrut Machines
Key considerations when investing in new roll forming production equipment.
Qualifying Roll Former Manufacturers
Factor | Description |
---|---|
Experience | Years in business and installations delivered |
Testing | Validation data for machines |
Materials | Metals successfully processed |
Engineering | Design skills and analysis expertise |
Support | Installation assistance offered |
Training | Operator instruction provided |
Questions to Ask Potential Suppliers
- What international quality standards do you meet?
- Will you share baseline production data?
- How customizable is your curving function?
- What level of support is included?
- Do you offer virtual demonstrations?
- Where are key bought-in components sourced?
- Can upgrades or enhancements be added later?
Benefits and Challenges of Steel Curving Unistrut Roll Forming
Advantages
- High production efficiency
- Consistent quality parts
- Volume production economies
- Lower operational labor
- Small equipment footprint
- Flexibility for product changes
- Integrated secondary processing
Disadvantages
- Higher initial capital investment
- Potential roll damage risks
- Skilled PLC programming necessity
- Inventory racking requirements
- Limited extremely heavy gauge capabilities
- Perception of simpler fabrication
When requirements fit process window, roll forming provides speeds and economies exceeding conventional steel channel fabrication methods.
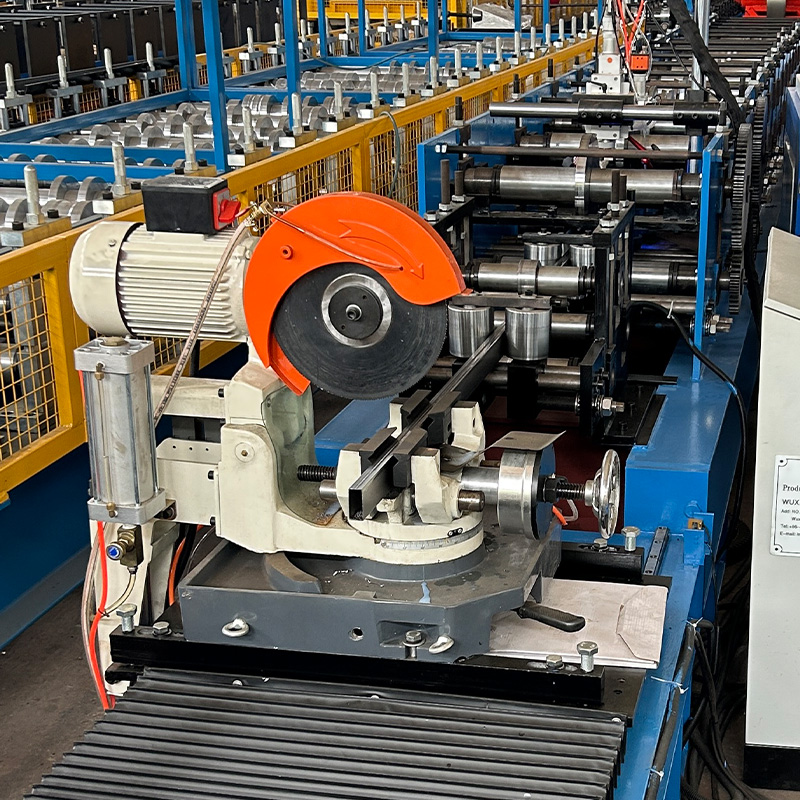
Frequently Asked Questions
What types of cutting can be integrated with curving unistrut roll formers?
Rotary flying knife cutting evenly spaces cut lengths for automated bundling and stacking. Abrasive cutoff wheels also possible for mitering or trimming if needed. Band saw slicing alternative.
What level of curving adjustment flexibility is typical for unistrut machines?
Tooling designs often allow adjustable curving from completely straight formed sections to fully curved up to 180 degrees for producing radially shaped architectural profiles. Specific ranges depend on metal properties.
What factors influence the load ratings of curved structural framing members?
The cross section dimensions, steel yield rating, fastener locations, end bracket stiffness, installation alignment precision and minor diameter limits determine published gravity and lateral building loads meeting various codes and specifications.
How many forming passes are needed for common unistrut channel profiles?
8-12 passes are typical for basic C and U channel profiles. More complex radii or unconventional shapes can require 14-18 stands. Software simulates material flow paths optimizing station quantities.
How does the curving function mechanically work on adjustable roll formers?
Curving arises from independent servo drives enabling asymmetric elevation positioning control between upper and lower tooling sets along the length allowing differential bending. Edge guide supports assist material tracking.
What special handling precautions should be taken with prefinished feedstock coils?
Reinforced spacers minimize risks of surface damage, dunnage separates wrap layers during handling. Climate controlled storage with humidity regulation helps prevent white rust corrosion which can penetrate tightly wound coils while awaiting processing.
Where are variable frequency drives utilized throughout curving roll former lines?
VFDs coordinate the main pull speed motor encoder follower configuration, cut to length index stroke, and upper curl stations adjacent to progressive steps where primary bending forms the changing material cross sections with velocity fine-tuning sensitivity.
How should technicians safely clear occasional steel jams inside roll formers?
After engaging emergency halts, strictly follow deenergization lockout tagout confinements before approaching pinch regions wearing protective equipment to gently manipulate jutting strip sections preferably using specialized hands tools, while exercising extreme diligent caution.
What prevents machine crash incidents when feed loss signals trigger?
Automated safety circuits immediately halt pulling motors and retract potential pressing hazards then notify operators prompted for visual verification ensuring full clearances prior to ladder logic requiring reset sequences after manually clearing any remnants before restoration of operation modes.