stainless steel roll forming machine produces structural and architectural metal products leveraging excellent roll formability, aesthetics and weather resistance properties of stainless alloys. Efficient stainless roll forming enables high speed fabrication of panels, roofing, railings and custom profiles meeting demanding specifications across industries.
This guide covers stainless product details, workings of roll former configurations, operational parameters, quality control factors, end-use applications and sourcing considerations when investing in steel roll forming machinery.
Typical Stainless Steel Products Made
Common roll formed sections:
Items | Alloys Used | Finishes |
---|---|---|
Roofing panels, gutters & trim | 201, 304, 316L | Mill finish, colored |
Door & window frames | 304, 316 | Mirror polish, patterns |
Hand rails, sign boards | 430, 304, 316L | Etched design, LED backlit |
Cladding, curtain walls | 201, 304 | Mechanically patterned |
Kitchen equipment | 430, 201, 304 | Scratch free #4 |
Precision custom profiles | 316L, 303, 17-7PH | As per design needs |
Match stainless alloy type – ferritic, austenitic, duplex etc. with mechanical properties, corrosion resistance, look and budget.
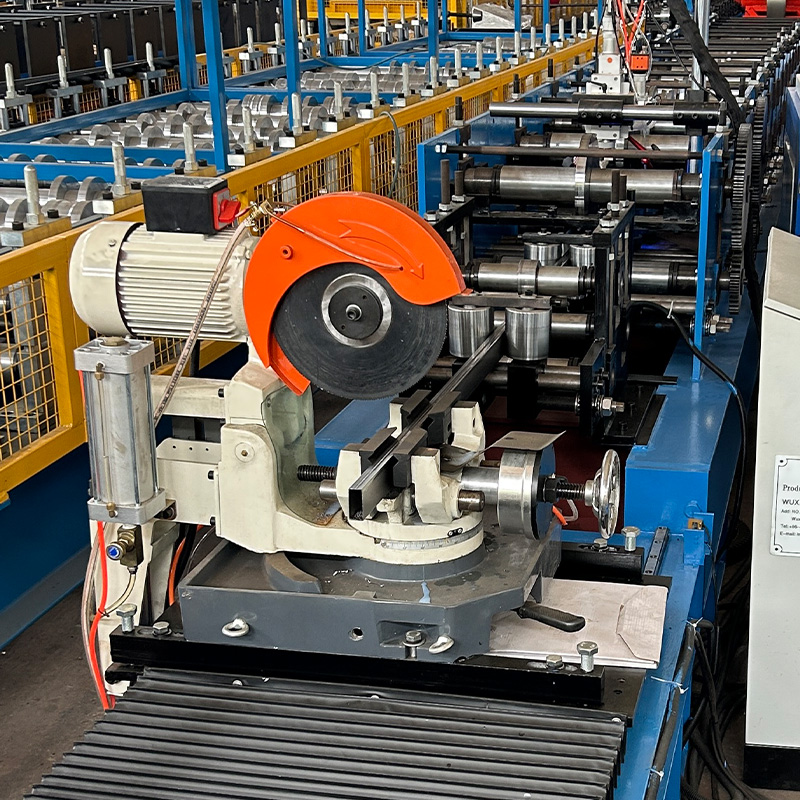
Working Principle of stainless steel roll forming machine
Key roll forming stages
- Decoiling – feeds sheet coil into equipment
- Feeding – powered rollers engage and straighten
- Pre-cutting – blanking shears for some products
- Forming – progressive stations gradually shape metal
- Punching – pierce holes or openings
- Stamping – emboss patterns simultaneously
- Severing – rotating shear or saw cuts to length
- Output conveyor – transports finished pieces
Controlled material feed coordination with progressive bending into designed profiles and integrated piercing, stamping delivers high quality stainless roll formed components.
stainless steel roll forming machine Types
Machine | Description |
---|---|
Standard | 10-16 stations, 600-1000kN capacity with basic controls |
Servo Electric | Precise independent servo roll drives, integrated punching and stamping, laser measuring |
Hybrid | Optimized mechanical/servo configurations balancing throughput and precision |
Tailor equipment automation level, speed vs precision tradeoffs and tooling flexibility relative to annual production volumes and end product variability.
Popular Configurations
- Decoiler -Programmable tension control
- Feed tables – with scale, gage stop
- Initial forming – 2-3 stands bending to pre-profile
- Main progressions – 10-12 roll stands for bending into final profile
- Punches/stamping units – inline holes, embossing as needed
- CNC Rotary shear – high speed cut-off
- Conveyor, auto-packing, labeling
- Touchscreen controls
Optional secondary finishing operations integrated before offloading:
- Corner notching, hole punching, trimming, beads
- Pattern stamping – brick, wood, custom motifs
- Powder coating epoxy paint spraying
Tailor production line capabilities to finished product range needed.
Key Machine Components
Unit | Purpose | Factors |
---|---|---|
Decoiler | Sheet payoff | Deflection compensation |
Feed table | Pulls metal into dies | Servo roll speed monitoring |
Roll housings | Bearing chocks with height adjustment | Precision machined with helical gearing |
Bending rolls | Progressively forms workpiece | Hardened tool steel, temper rolling |
Punches | Piercing, louvre patterns | Adjustable lower stripping |
Stamping inserts | Embossing motifs | Quick changeovers |
Controls | Operates line devices, stores recipes | Easy interface with diagnostics |
Review manufacturing and assembly quality certifications on key assemblies that directly impact product precision.
-
Electrical Cabinet Frame Roll Forming Machine
-
Din Rail Roll Forming Machine
-
Cable Ladder Roll Forming Machine
-
PV Mounting Bracket C Shape Profile Roll Forming Machine
-
Cable Tray Roll Forming Machine
-
PV Mounting Bracket Roll Forming Machine (HAT / Omega Profile)
-
PV Mounting Bracket Z Shape Profile Roll Forming Machine
-
Solar mounting strut channel roll forming machine
-
Strut Channel Roll Forming Machine
Customization Factors
Parameter | Options |
---|---|
Forming Size | 1m – 2.5m length standard |
Maximum Line Speed | 60m/min+ for high volume lines |
Dimension Ranges | 50mm – 800mm+ wide widths in a single line based on market |
Material Thickness | 0.4mm to 1.5mm aluminium; 0.4 to 2mm stainless; via roll changes |
Hole Patterns | Cater for various slotting, piercing, louvre designs |
Profile Styles | Hemmed edges, inclusion of stiffening folds and beads |
Material Surface | Accommodate various stainless finishes, pre-painted coil |
Automation | Laser measuring, servo roll control, recipe storage improves changeovers |
Discuss extent of customization flexibility needed relative to future order variability when specifying capabilities.
Production Quality Control
- First piece inspections after size changeovers
- Wall thickness gauging
- Cross-section profile checking fixtures
- Hole placement alignment checks
- Length accuracy monitoring
- Angularity, twist or camber minimization
- Labeling and protective film verification
- Visual surface and cleanliness inspection
Follow applicable quality specifications like ASTM A480 on broad stainless product standards.
End Use Application Areas
Roll formed stainless components see broad industrial utilization:
- Architecture – decorative building facades, signages, lighting
- Medical – carts, modular guard rails
- Marine – railings, walkways on ships and offshore platforms exposed to salt water
- Transportation – metro/rail car interiors, luggage racks
- Infrastructure – highway sound barriers, safety crash barriers
- Food sectors – kitchen equipment, cold room panels
- Furniture – hotel, office, mall interiors
Custom profiles add functionally and visually appealing metallic finishes across domains.
Purchasing Considerations
Parameter | Importance |
---|---|
Technical Expertise | High |
Production Throughput | Medium |
Changeover Flexibility | Medium |
Cost Factors | Low |
Cost Considerations
- $150,000 to $500,000 – machinery capital investment range depending on throughput, automation and width flexibility targets
- $4000+ per roll set – typical tooling costs for future profile variability
- 2-4% annually – recommended preventative maintenance
- ~3 year payback – via improved manufacturing productivity
Analyze total cost of ownership carefully over minimum 5 years when justifying stainless roll former investments.
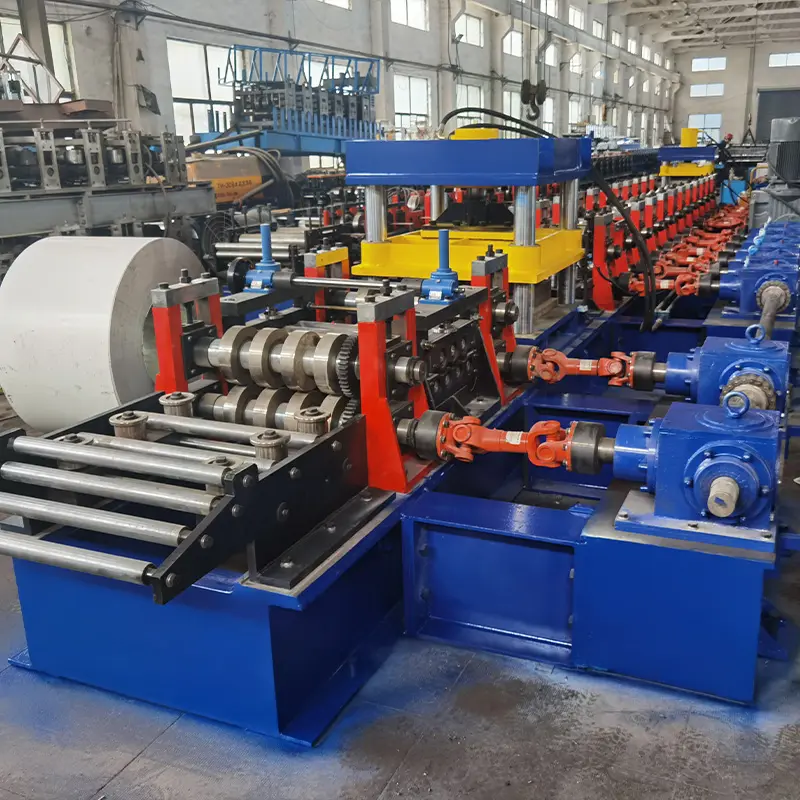
FAQs
Q: What type of stainless steel is typically roll formed?
A: Austenitic grades 304, 316L are commonly roll formed. Ferritic 430, 409 and 201 also offer good corrosion resistance at lower alloy costs. Match material to strength, formability, surface and longevity needs.
Q: What thickness range can stainless steels be roll formed?
A: Stainless steels from 0.3mm to 2mm can be reliably roll formed on properly configured machines. Thicker metals up to 3mm possible for special large radius bends. Use proper sized roll tooling, material hold down pressures and forming sequences.
Q: How fast can stainless steel be roll formed?
A: Mechanical stainless lines operate between 10-60m/min based on metal thickness and profile complexity. Servo electric lines with precision roll controls allow upward of 90m speeds with fast acceleration and deceleration between staged sections.
Q: What causes surface defects in stainless roll forming?
A: Surface marks occur mainly from feed scratches transferred from decoiler, fingerprints or oil residue not removed before forming. Roll hardening treatment, ongoing cleaning protocols and protective films minimize visual defects meeting customer expectations.