
PV Mounting Bracket Roll Forming Machine Profile Drawings

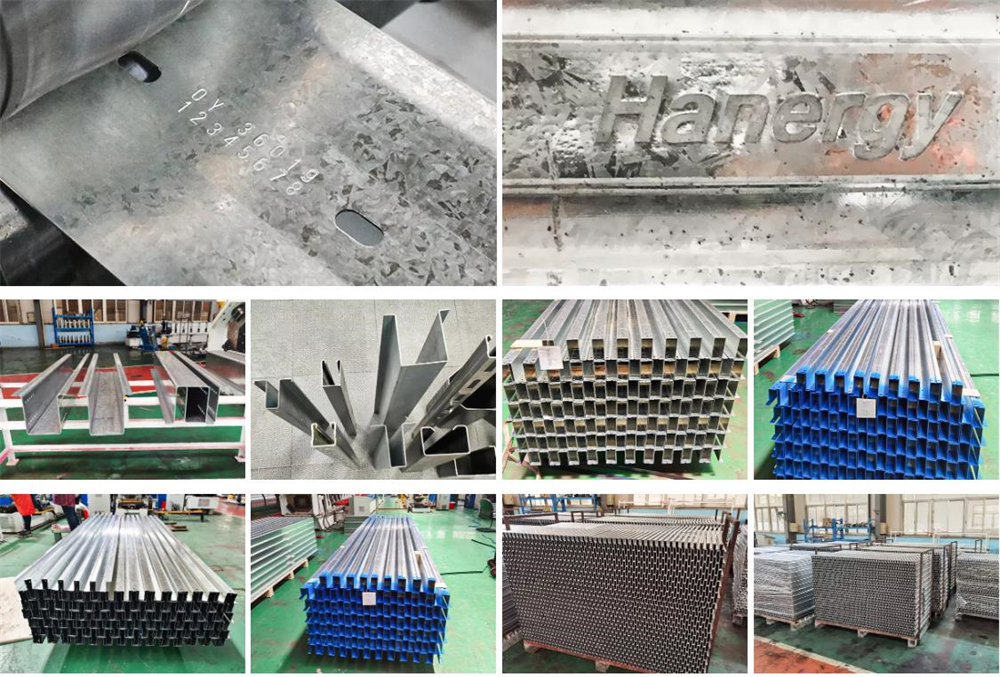
PV Mounting Bracket Roll Forming Machine Production Line
PV Mounting Bracket Roll Forming Machine Details
PV Mounting Bracket Roll Forming Machine Parameters
PV Mounting Bracket (HAT / OmegaProfile) Roll Forming Machine | ||
Machinable Material
|
A) Hot-rolled And Cold Rolled Steel |
Thickness(MM): 1.5-2.5 or up to 3mm. Can customize as per your thickness and profile.
|
B) Hot-dip Galvanized Sheet | ||
C) Pre-Galvanized Steel | ||
D) Mill(Plain/Black) Steel | ||
Yield strength | 235 – 345 Mpa | |
Tensil stress | G250 Mpa-G350 Mpa | |
Decoiler | Hydraulic Decoiler
Manual Decoiler |
2 in 1 Decoiler With Leveler And Servo Feeder (Optional) |
Punching System : | Hydraulic Punching Station (Individual) | * Punching Press (Optional) |
Forming Station | About 20 | * According To Your Profile Drawings |
Main Machine Motor Brand | Reducer + Motor | * Servo Motor (Optional) |
Driving System | Chain Drive | * Gearbox Drive (Optional) |
Machine Structure | Wall Panel | * Forged Iron station (Optional) |
Line Forming Speed | 0-15 (M/MIN) | * According To Final Configuation |
Rollers’ Material | 45# | * GCr 15 (Optional) |
Cutting System | Post-cutting, Machine Stop To Cut | * Tracking Servo Cutter (Optional) |
Frequency Changer Brand | Yaskawa | |
PLC Brand | Panasonic | |
Power Supply | 380V 50Hz 3ph | * Or According To Your Requirment |
Machine Color | Industrial Blue | * Or According To Your Requirment |
PV Mounting Bracket Roll Forming Machine Basic working principle and components
PV Mounting Bracket Roll Forming Machine is an automated production equipment used for producing solar mounting brackets, frames, and structural components. It consists of several components, including:
Hydraulic uncoiler: used for feeding the raw materials (such as steel coils) into the production line.
Servo feeder: used for accurately controlling the feeding speed and length of the raw materials.
Punch unit/individual punch unit: used for punching holes and other processing of the raw materials.
Roll former: used for bending, folding, and other processing of the raw materials to form the desired shape and size.
Servo tracking cutter: used for cutting the finished products to the required length.
Electrical and hydraulic system: used for controlling the operation and adjustment of the production line.
The basic working principle of the PV Mounting Bracket Roll Forming Machine is to feed the raw materials into the production line through the uncoiler, which is then fed and punched by the servo feeder and the punch unit/individual punch unit, respectively. Then, the raw materials are formed and processed by the roll former to create the desired shape and size. Finally, the finished products are cut to the required length by the servo tracking cutter. Throughout the production process, the electrical and hydraulic system controls the operation and adjustment of the production line to ensure its stability and efficiency.
PV Mounting Bracket Roll Forming Machine Advantages
Advantage | Description | |||||||||||
Increased Production Efficiency | Produces components faster than manual methods, leading to increased production efficiency and output. | |||||||||||
Reduced Labor Costs | Automation reduces the need for manual labor, leading to reduced labor costs and increased profitability. | |||||||||||
Consistent Product Quality | Produces components with consistent quality, reducing defects and waste and increasing customer satisfaction. | |||||||||||
Customizable Production | Can produce customized components, allowing for flexibility in design and construction. | |||||||||||
Cost-Effective | Reduces labor costs, minimizes defects and waste, and increases productivity, making it a profitable investment. |
PV Mounting Bracket Roll Forming Machine VS. Traditional Processing
Factor | Traditional Processing | PV Mounting Bracket Roll Forming Machine |
Labor | Requires large amounts of manual labor for production, leading to higher labor costs. | Requires minimal manual labor due to automated production, reducing labor costs. |
Production Cycle | Longer production cycle due to manual processing, leading to slower turnaround times. | Shorter production cycle due to automated production, leading to faster turnaround times. |
Product Quality | Product quality may vary due to human error and inconsistency. | Product quality is consistent due to automated production, reducing defects and waste. |
Customization | Limited customization due to manual processing. | Allows for greater customization through the use of computer-aided design and automated production. |
Cost | Higher costs due to labor-intensive processing and longer production cycles. | Lower costs due to reduced labor and faster production times. |
PV Mounting Bracket Roll Forming Machine Application
PV Mounting Bracket Roll Forming Machine is widely used in the solar energy field for producing various components such as solar mounting brackets, solar panels, solar street lights, and other structural parts. The machine can produce customized shapes and sizes according to the specific needs of solar energy systems, ensuring a perfect fit for various solar panels and installations.
One of the major applications of the PV Mounting Bracket Roll Forming Machine is in the construction of solar mounting structures, which are essential for mounting solar panels on rooftops, ground, or other surfaces. The machine produces mounting brackets and frames that are specifically designed for different types of solar panels and installations, ensuring a secure and stable connection between the panels and the support structures.
Moreover, the PV Mounting Bracket Roll Forming Machine can also produce various structural components for solar energy systems such as brackets, rails, clamps, and connectors. These components are necessary for the assembly and installation of solar panels, inverters, batteries, and other equipment in a solar energy system.
Another application of the PV Mounting Bracket Roll Forming Machine is in the manufacturing of solar street lights. The machine produces brackets and frames that are used to mount the solar panels and light fixtures on poles or other surfaces, providing an independent source of energy for street lighting.
Overall, the PV Mounting Bracket Roll Forming Machine plays a crucial role in the solar energy field, providing high-quality and customized components that are essential for the construction, assembly, and installation of solar energy systems.
what is omega profile roll forming machine?
The Omega profile roll forming machine is a type of industrial machinery used in the metalworking industry for the production of Omega-shaped profiles. Roll forming is a continuous bending operation in which a long strip of metal is passed through a series of rollers to gradually shape it into the desired profile.
The Omega profile refers to a specific cross-sectional shape that resembles the Greek letter “Ω.” This profile is commonly used in various applications, including the construction of steel buildings, roofing systems, and structural supports.
The Omega profile roll forming machine consists of a series of roll stands, which are equipped with rollers that progressively shape the metal strip. The machine typically includes a decoiler, which holds the metal coil, and a cutoff mechanism that cuts the formed profiles to the desired lengths.
During the roll forming process, the metal strip is fed into the machine and guided through the rollers, which bend it into the Omega shape. The rollers are designed with specific contours and dimensions to gradually form the desired profile accurately. The process is continuous, allowing for high-volume production of Omega profiles with consistent quality.
The machine can be automated and computer-controlled, enabling precise control over the forming process and various parameters such as speed, roller pressure, and cutting length. This automation contributes to increased productivity and efficiency in manufacturing operations.
Is z purlin roll forming machine different from omega roll forming machine?
Yes, the Z purlin roll forming machine and the Omega roll forming machine are two different types of roll forming machines used for producing different profiles.
- Z Purlin Roll Forming Machine: The Z purlin roll forming machine is designed specifically for manufacturing Z-shaped profiles. Z purlins are widely used in the construction industry as structural components for roof and wall systems. The machine is equipped with a series of rollers that gradually shape the metal strip into the Z profile. It typically includes a decoiler, roll stands, a cutoff mechanism, and other components necessary for the roll forming process.
- Omega Roll Forming Machine: The Omega roll forming machine, as mentioned earlier, is used for manufacturing Omega-shaped profiles. The Omega profile resembles the Greek letter “Ω” and is commonly used for various applications, including the construction of steel buildings, roofing systems, and structural supports. Similar to the Z purlin roll forming machine, the Omega roll forming machine consists of rollers that gradually shape the metal strip into the desired Omega profile.
While both machines are used in the roll forming process and share similarities in their basic functioning, they are specifically designed for different profile shapes. The Z purlin roll forming machine is specialized for Z-shaped profiles, whereas the Omega roll forming machine is dedicated to producing Omega-shaped profiles.
It’s worth noting that roll forming machines can be customized and adapted to produce different profiles by changing the tooling or rollers. However, if you specifically need to manufacture Z purlins or Omega profiles, you would require the corresponding dedicated machine for optimal efficiency and accuracy.
application of roll forming machine for solar structure
A roll forming machine for solar structures is a specialized piece of equipment used to produce components and structures used in solar energy systems. These machines are designed to manufacture specific profiles and shapes required for solar panel installation and mounting.
Here are some key components and structures that can be produced using a roll forming machine for solar structures:
- Solar Panel Mounting Rails: These rails are used to support and secure solar panels on rooftops or ground-mounted systems. The roll forming machine can produce rails with specific cross-sectional shapes, such as C-shaped or U-shaped profiles, which provide strength, stability, and ease of installation.
- Solar Panel Support Structures: The roll forming machine can produce various structural components used to support solar panels, such as purlins, beams, and columns. These components are designed to withstand the weight of solar panels, wind loads, and other environmental factors.
- Racking Systems: Racking systems are used to assemble and install solar panels in an organized and secure manner. The roll forming machine can produce the necessary components, including brackets, clamps, and connectors, required for the racking systems.
- Solar Tracker Components: Solar trackers are devices that orient solar panels to track the sun’s movement throughout the day, maximizing energy generation. The roll forming machine can manufacture components used in solar tracker systems, such as tracking arms, brackets, and frames.
These roll forming machines for solar structures are equipped with specific tooling and rollers designed to produce the required profiles and shapes accurately. The machines can be automated and computer-controlled, allowing for precise control over the forming process, dimensions, and tolerances.
Reviews
There are no reviews yet.