Cold roll forming machines are used to produce steel sheets that are used in the automotive and construction industries. The machine starts by cutting a large sheet of steel into smaller pieces, which are then fed one at a time through a series of rollers to reduce them to the desired thickness. This article is about the basics of a cold roll forming machine. It is also about what the different types of cold roll formers are and how they work.
What is a cold roll forming machine?
A cold roll forming machine is a type of construction equipment used to form metal sheets into desired shapes. The process of cold roll forming involves passing a strip of metal through a series of rollers, each of which progressively bends the metal until it takes the desired shape. Cold roll forming machines can be used to create various types of products, including roofing panels, wall panels, floor joists, and beams. In most cases, cold roll forming machines are used to create parts for the automotive, construction, and appliance industries.
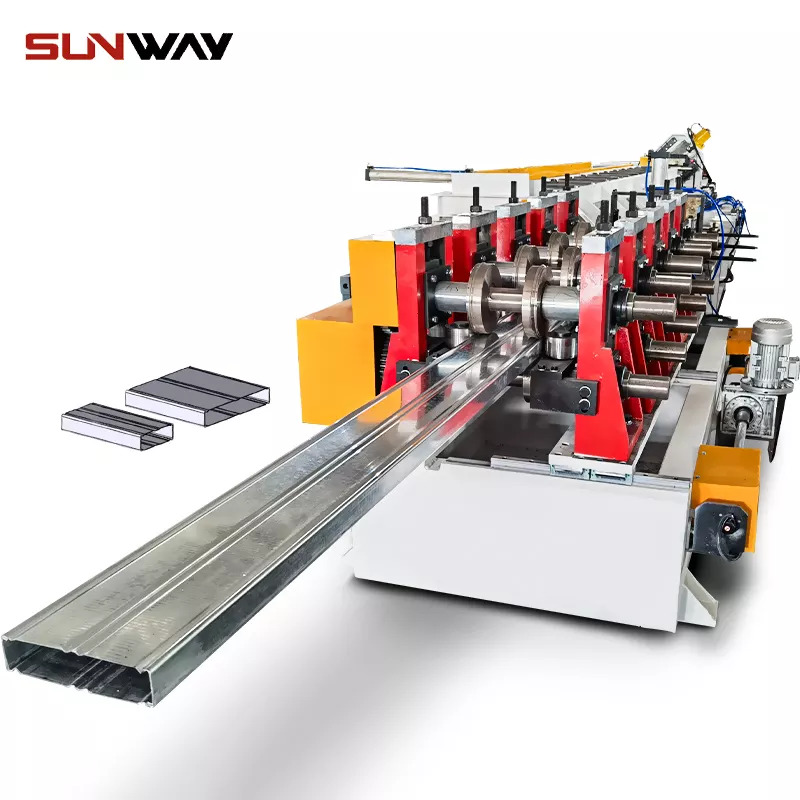
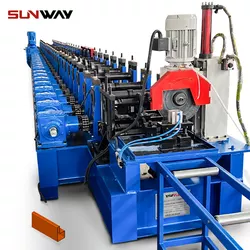
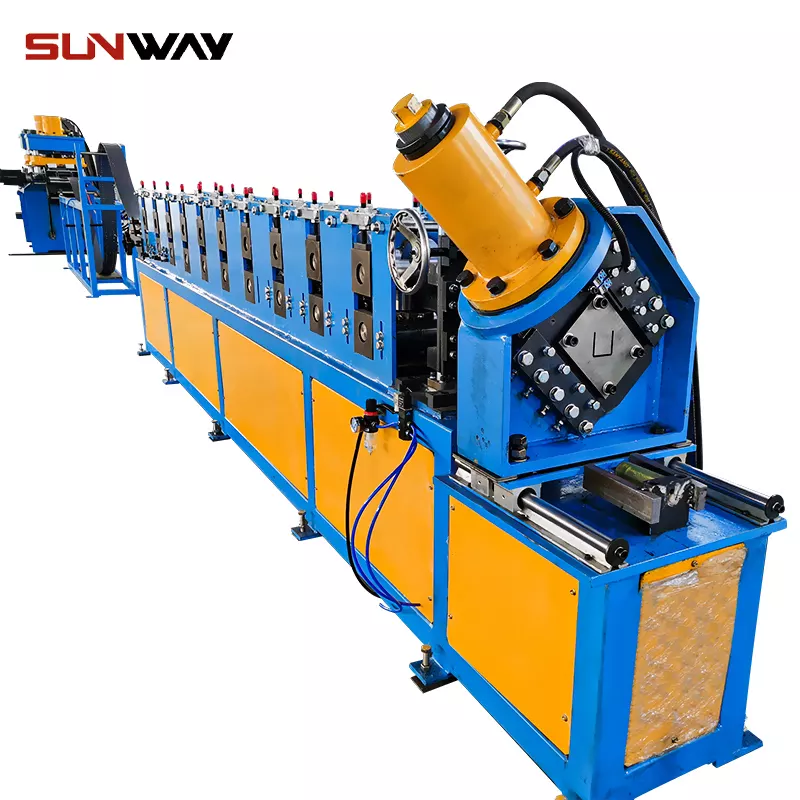
Types of Cold Roll Forming Machines
A cold roll forming machine is a machine that forms metal at room temperature. Cold roll forming is a process in which a strip of metal is passed through a series of rollers to form a desired shape. The strip of metal is fed into the rollers at an angle, and the rollers gradually deform the metal into the desired shape.
There are several different types of cold roll forming machines:
- Cold pilger rolling machine: This type of machine is used to reduce the diameter of a workpiece by plastic deformation.
- Three-roll bending machine: This machine is used to bend a workpiece by passing it through three rolls.
- Four-roll bending machine: Similar to the three-roll machine, but with four rolls instead of three.
- Wire drawing machine: This machine is used to draw a wire or rod through a die to reduce its diameter.
Pros and Cons of a Roll Forming Machine
Roll forming machine can be a great addition to your business, but there are some things you should consider before making your purchase. Here are some of the pros and cons of owning a roll forming machine:
Pros:
- Increased Strength: Roll forming machines formed parts are typically stronger than parts that are stamped, cast, or machined from solid stock. This is due to the process of work hardening that occurs during cold roll forming.
- Improved Dimensional Accuracy: Roll forming machines can achieve very tight tolerances, making it an excellent choice for critical applications.
- Greater Flexibility: Roll forming machines can be quickly and easily reconfigured to produce different shapes and sizes of parts. This makes them ideal for prototyping or small-batch production runs.
- Enhanced Surface Finish: The smooth, consistent surface finish of cold rolled parts is often superior to that of parts made with other methods. This can be a significant advantage in applications where appearance is important.
- Cost-Effective: Roll forming machine is a highly efficient process that generally requires less material than other methods such as stamping or machining. This can result in significant cost savings, especially for larger or complex parts.
Cons:
- Initial Investment – Roll forming machine is a significant initial investment, so you’ll need to make sure it fits into your budget.
- Training & Maintenance – As with any new piece of equipment, you’ll need to invest time in training yourself and your employees on how to use the machine properly. Additionally, regular maintenance is necessary to keep your machine running smoothly.
-
Carriage Board Roll Forming Machine
-
Standing Seam Roof Panel Curving Machine
-
Barrel Corrugated Roll Forming Machine
-
Highway Guardrail End Terminal Forming Machine
-
Highway U/C Post Roll Forming Machine
-
2 Waves Highway Guardrail Roll Forming Machine
-
3 Waves Highway Guardrail Roll Forming Machine
-
Hydraulic Roof Sheet Curving Machine
-
Stand Seaming Roof Panel Roll Forming Machine
Different Uses for Cold Roll Forming Machines
A cold roll forming machine is a versatile piece of equipment that can be used for a variety of applications. Some common uses for cold roll forming machines include creating metal roofing, gutters, fascia, soffits, and flashing. Cold roll forming machines can also be used to create HVAC ductwork, window and door frames, and trim.
Metal roofing is one of the most popular applications for cold roll forming machines. These machines can quickly and easily create metal roof panels in a variety of sizes and shapes. Cold roll forming machines can also be used to create gutters, fascia, soffits, and flashing.
HVAC ductwork is another common application for cold roll forming machines. These machines can create round or rectangular ductwork in a variety of sizes. Cold roll forming machines can also be used to create window and door frames. And finally, cold roll forming machines can be used to create trim for both interior and exterior applications.
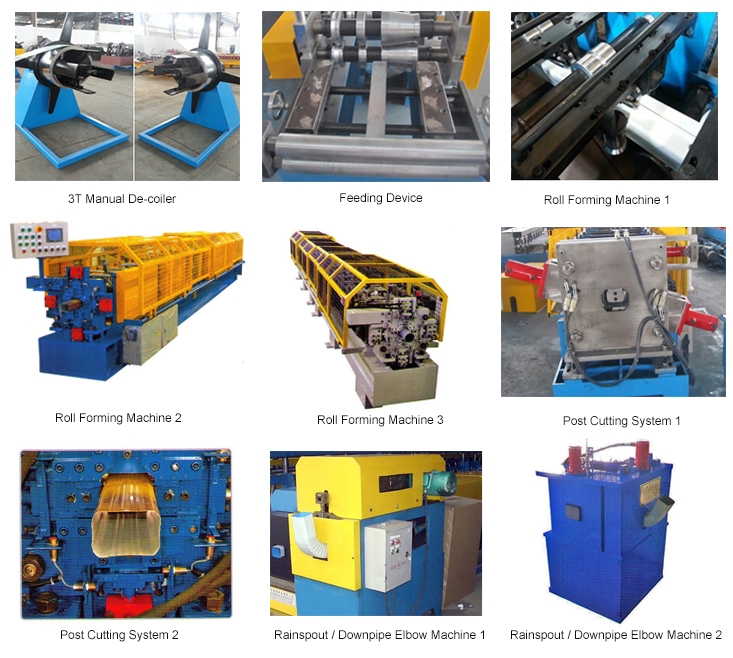
Conclusion
A cold roll forming machine is a versatile piece of equipment that can be used to create a variety of parts and components. In this article, we’ve looked at what a cold roll forming machine is, how it works, and some of the benefits it offers. If you’re looking for a way to increase efficiency and productivity in your manufacturing process, a cold roll forming machine could be the answer.
FAQ
What is cold roll forming?
Cold forming – often known as cold roll forming – is a forging technique used to shape metal materials at near room temperature. Forming metal at cooler temperatures retains or enhances the tensile strength of the material while still allowing high levels of intricate manipulation.