Roll forming machines are a crucial part of the production process for many industries – from manufacturing to packaging, and food processing. They are responsible for shaping sheets or coils into specific shapes and sizes that can be used in different processes. This blog article will break down what the key parts of roll forming machine are so that you know exactly what you need in order to run one properly!
What is a Roll Forming Machine?
A roll forming machine is a type of industrial machinery used to create custom-shaped metal or plastic products. The basic components of a roll forming machine are a die, an extruder, and a press. Together, these components form the basis for creating products such as parts for engines, car doors, and toys.
The die is the main component of a roll forming machine. It’s basically a large plate with holes in it that can be heated up to very high temperatures. The extruder is the part of the machine that feeds the die with metal or plastic sheet material. The press is what applies pressure to the sheet material as it’s being formed into a product.
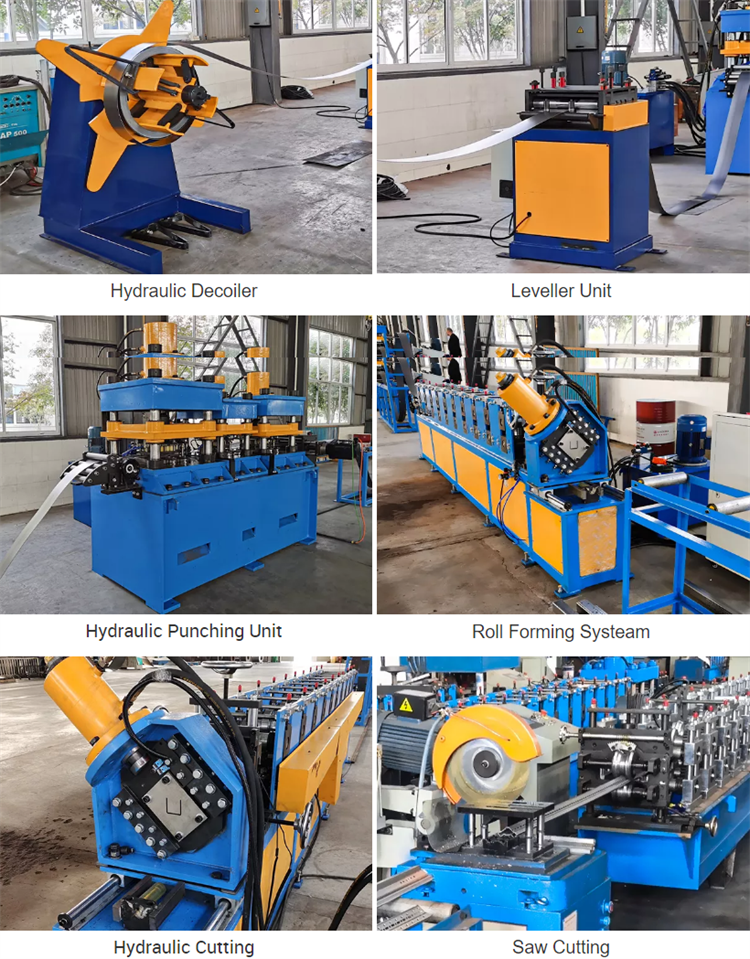
How Does a Roll Forming Machine Work?
A roll forming machine is a type of manufacturing machine used to create long, narrow objects from a single piece of material by rolling it into a desired shape. The basic components of a roll forming machine include the die, the mandrel, and the motor.
The die is a tool that is used to form the object being created. It typically includes one or more sharp edges that are used to cut the material being rolled into shape. The mandrel is a cylindrical rod that helps guide the material as it is rolled and forms the final shape. The motor is responsible for moving the die and mandrel around and causing them to interact with each other in order to create the desired product.
-
Standing Seam Roof Panel Curving Machine
-
Barrel Corrugated Roll Forming Machine
-
2 Waves Highway Guardrail Roll Forming Machine
-
3 Waves Highway Guardrail Roll Forming Machine
-
Hydraulic Roof Sheet Curving Machine
-
Stand Seaming Roof Panel Roll Forming Machine
-
Downspout Pipe Roll Forming Machine
-
Gutter Roll Forming Machine
-
Trapezoidal Panel Roll Forming Machine
The Parts of Roll Forming Machine
A roll forming machine, also called a web forming machine, is a type of industrial machinery used to create objects by pressing a sheet of material into a desired shape. The most common application for a roll forming machine is in the manufacture of automobile body panels, but they are also used to produce other products such as glass and aluminum.
The heart parts of roll forming machine are the die or presser bar. This bar slides back and forth over the workpiece, causing the material to be pressed into shape. The die can be either manual or automated, and must be able to accommodate different shapes and sizes of sheets. Additional parts of roll forming machine include the movable dies and pressure plates that help hold the sheet in place while it is being formed, as well as the feeder system that brings in the material.
Other parts of roll forming machine include:
-The drive mechanism which controls how fast the presser bar moves along the workpiece;
-The clamps which attach the workpiece to the presser bar;
-The gearbox which helps convert torque from the motor into linear motion;
-The tensioning system which ensures that the material remains tight during rolling;
-The cooling system which keeps both the die and presser bar operating at their optimal temperatures;
-And finally, the operator’s station which includes all of the necessary controls for running the machine.
5 different types of roll forming machines
There are five different types of roll forming machines: die-casting, CNC (computer numerical control), hydraulic, air pressure, and screw. Die-casting machines use a mold to create the part. CNC machines use a computer to create the part. Hydraulic machines use pressurized fluid to form parts. Air pressure machines use compressed air or nitrogen to form parts. Screw machines use screws to form parts.
Die-casting machines are the oldest type of roll forming machine and use a mold to create the part. The part is placed in the mold and then heated until it melts. The molten part is then forced into the mold cavity and solidifies around the outside of the mold. Die-cast parts can be very difficult to remove from the molds because they are so rigid.
CNC (computer numerical control) machines use a computer to create the part. The computer creates a 3D model of the part before cutting it out with a saw or laser cutter. The parts that are cut out are then moved by a motorized system onto a worktable where they can be shaped with various tools using CAD (computer-aided design). CNC machines are much more accurate than die-casting machines and produce less waste products such as plastic shavings.
Hydraulic Machines use pressurized fluid to form parts. Parts are placed in an open chamber where hydraulic pressure is used to squeeze them together until they reach their desired shape. Hydraulic machines are very accurate and produce very high-quality parts. However, they are relatively slow compared to other types of roll forming machines.
Air pressure machines use compressed air or nitrogen to form parts. Parts are placed in a chamber where air pressure is used to squeeze them together until they reach their desired shape. Air pressure machines are very fast and produce very high-quality parts. However, they are less accurate than other types of roll forming machines.
Screw Machines use screws to form parts. Parts are placed on a rotating screw machine where the screws are used to create the desired shape. Screw machines are very accurate and produce very high-quality parts. However, they are relatively slow compared to other types of roll forming machines.
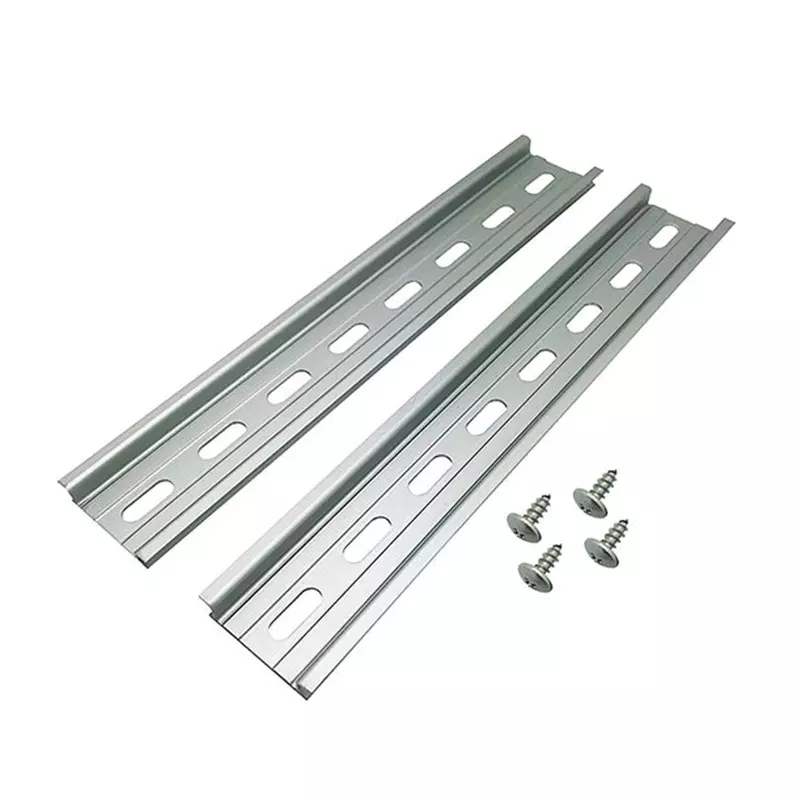
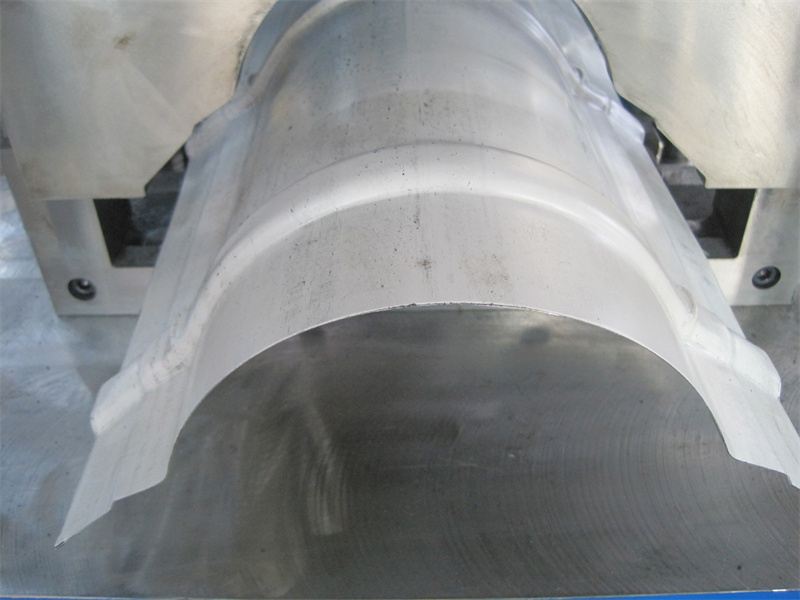
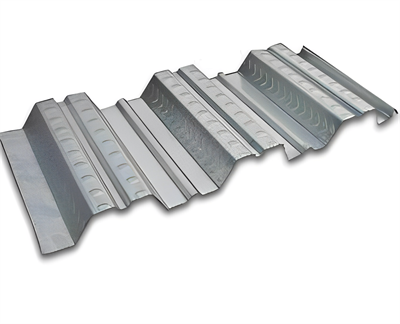
Conclusion
If you’re looking to start a business that involves roll forming, then it’s important to understand the different parts of roll forming machine. By understanding the basics of how these machines work, you’ll be able to make better decisions when selecting one for your business.
FAQ
What is the principle of rolling?
Principles of rolling. Rolling is a process used to shape metal into a thin long layer by passing it through a gap of two rollers rotating in different directions (clockwise and anti-clockwise) .