A trapezoidal roof panel making machine is an efficient roll forming system used to produce trapezoidal roof panels. These strong, lightweight panels with their distinctive shape are popular for industrial and commercial roofing applications.
This guide provides a comprehensive overview of trapezoidal roof panel making machines, including:
Types of Trapezoidal Roof Panel Making Machines
Machine Type | Description |
---|---|
Automatic | Fully automated operation for high-volume production |
Semi-Automatic | Manual feeding but automated forming |
C-N-C Operated | Computer numerical control for precision and flexibility |
Customized Design | Tailored to specific production requirements |
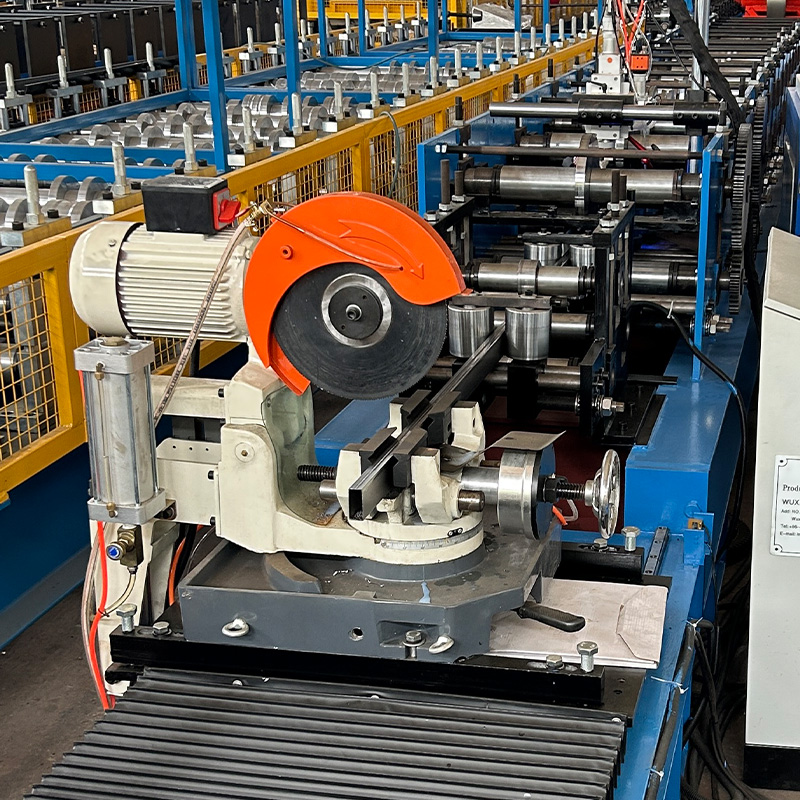
Working Process
Trapezoidal roof panel making machines work on the principle of roll forming. They transform metal coil into panels with a trapezoidal profile via an automated, continuous process:
- Coil fed into decoiler
- Passed through leveler machine
- Die cut to required width
- Enters forming stations to shape panel ribs and sides
- Cut to specified length
- Output as finished trapezoidal roof panels
Key components include feeder, pre-cutter, roll forming stations, post-cutter. The panels can have features like stiffening ribs, insulation, and protective coating applied.
Materials, Design and Customization
Parameter | Options |
---|---|
Materials | Mild steel, aluminum, zinc, galvanized steel, prepainted steel |
Sheet Width | Up to 2m wide coils can be processed |
Sheet Thickness | 0.5mm to 2mm |
Profile Shape | symmetric or asymmetric trapezoidal profiles |
Profile Height | 15mm to 105mm in increments of 15mm/30mm/45mm etc. |
Custom Profiles | bespoke trapezium dimensions per project specs |
These machines offer flexibility in materials used and dimensions possible for the trapezoidal shape. Common options are:
- 5 rib symmetrical trapezoidal profle
- 8 rib asymmetrical with higher central ribs
- Custom profiles to match existing roofing
Suppliers and Price Range
Supplier | Location | Price Range |
---|---|---|
ABC Machinery | China | $50,000 – $150,000 |
DEF Systems | Turkey | $80,000 – $250,000 |
GHI Manufacturing | India | $35,000 – $120,000 |
Reputable international brands supply trapezoidal panel making equipment at reasonable budgets suitable for most manufacturers. Exact pricing depends on:
- Automation level
- Production speed/monthly output
- Overall working width
- Type of material handled
- Additional integrated operations
Installation, Operation and Maintenance
Activity | Guidelines |
---|---|
Installation | Level concrete foundation Connect to utilities Align components |
Operation | Parameter setup Coil loading Panel profiling Length cutting |
Maintenance | Regular lubrication Inspect/replace wear items Software updates |
Proper installation by technical teams ensures smooth functioning. The user-friendly HMI touchscreen controls make operation straightforward. Following routine maintenance procedures optimizes performance.
Choosing the Right Trapezoidal Roof Panel Machine Supplier
Considerations | Description |
---|---|
Production Needs | Output rate, width, thickness etc |
Budget | Balance cost against quality and reliability |
Service Support | Installation, training, maintenance etc |
Certifications | ISO, CE marking indicates standards compliance |
Experience | Proven track record delivering similar projects |
Evaluating your production goals versus machine capabilities and supplier reputation is key for selecting this major capital equipment investment.
-
Vineyard Post Roll Forming Machine
-
Auto Size Changeable Sigma Purlin Roll Forming Machine
-
Auto Size Changeable C Z Purlin Roll Forming Machine
-
Auto Size Changeable Z Purlin Roll Forming Machine
-
Auto Size Changeable C U Purlin Roll Forming Machine
-
C Section Bracing Omega Storage Rack Upright Post Roll Forming Machine
-
Steel Box Plate Making Roll Forming Machine
-
Box Beam Steel Roll Forming Machine For Shelf Column
-
Pallet Racking Step Beam P Beam Roll Forming Machine
Advantages of Trapezoidal Roof Panel Machines
- Highly productive and cost-efficient
- Deliver consistent quality trapezoidal panels
- Flexible design customization possible
- Simple, user-friendly operation
- Rugged construction for durability
- Low maintenance requirements
Limitations of Trapezoidal Roof Panel Machines
- Large space needed for installation
- Substantial initial capital expenditure
- Limited to trapezium and similar profiles
- Setup changeover requires downtime
- Requires skilled personnel for maintenance
To summarize, trapezoidal roof panel making machines are advanced roll forming systems enabling efficient production of popular trapezoidal shaped metal roofing. This guide covers machine types, technical specifications, working process, customization options, suppliers, costs considerations and more to help manufacturers make informed decisions.
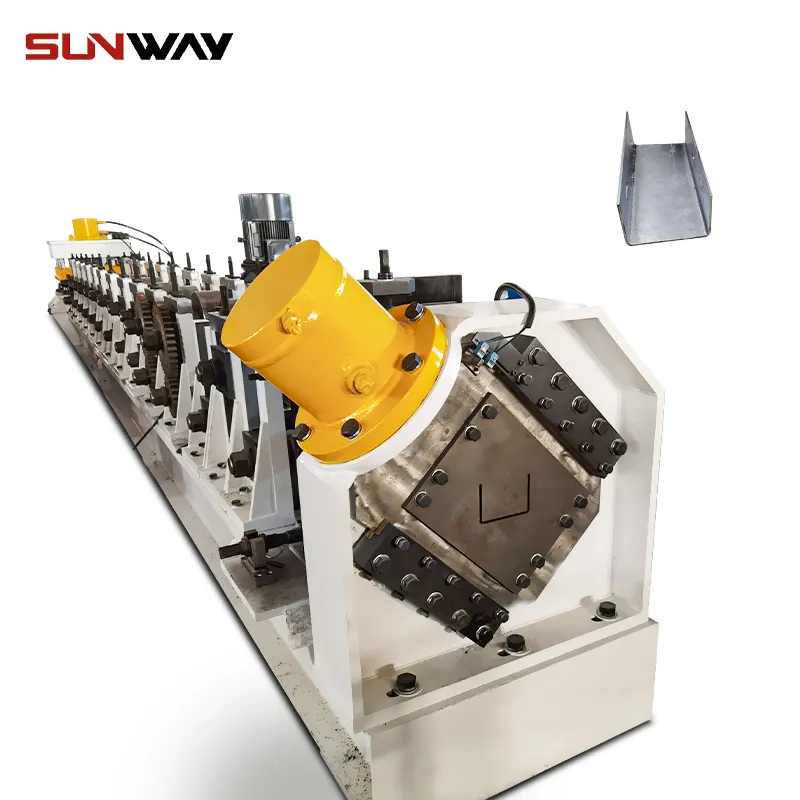
FAQ
Q: What thickness of sheets can be formed?
A: Typically 0.5mm to 2mm thickness is supported. Some models can handle up to 3mm thick coils.
Q: What other profiles can be produced besides trapezoidal?
A: These machines can produce varied ribbed panel profiles like sinusoidal, box ribbed and other wave-shaped sections.
Q: What automation levels are available in these machines?
A: Options range from basic manual feeding line to fully automated with coil loading, length cutting and stack unloading.
Q: What factors affect trapezoidal panel machine prices?
A: Key factors are production speed, width, material type/thickness, automation level and integrated operations like packaging.