Roll forming machines are essential tools in the manufacturing industry, used to produce a wide range of metal products quickly and accurately. To ensure optimal performance and prolong the machine’s lifespan, it’s important to properly maintain the roll forming machine product line. In this post, we will provide tips for maintaining your roll forming machine product line, including cleaning, lubrication, inspection, and following a maintenance schedule. By following these tips, businesses can prevent costly downtime, reduce the likelihood of equipment failure, and ensure that their roll forming machine product line continues to operate at peak performance. Let’s dive into the key tips for maintaining your roll forming machine product line and learn how to properly care for this essential manufacturing equipment.
Cleaning Your Roll Forming Machine Product Line
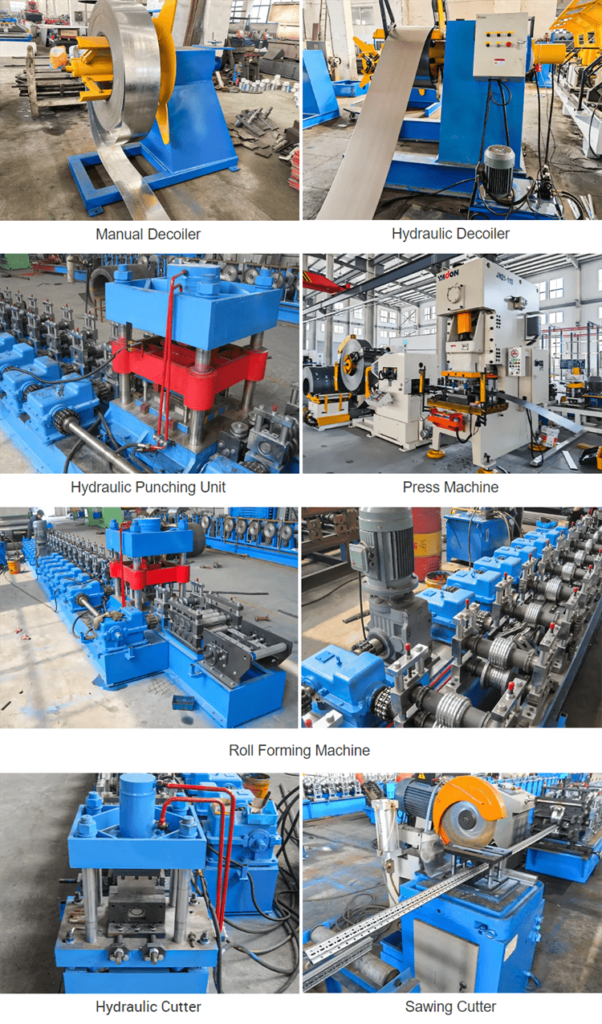
Keeping your roll forming machine clean is an essential part of maintaining its optimal performance and longevity. Here are some tips for cleaning your roll forming machine:
- Dust and Debris: Remove any dust, debris, or other loose materials from the machine’s surface and components. This can be done using compressed air, a soft brush, or a dry cloth.
- Oils and Grease: Remove any oil, grease, or other contaminants from the machine’s rollers, tooling, and other components. This can be done using a cleaning solution and a soft cloth. Be careful not to use harsh chemicals that could damage the machine’s components.
- Cooling System: Clean the cooling system regularly to prevent blockages and ensure that the machine stays cool during operation. This can be done using a specialized cleaning solution and following the manufacturer’s instructions.
- Electrical Components: Avoid using water or cleaning solutions on electrical components, as this could cause damage. Instead, use a dry cloth or compressed air to remove any dust or debris.
- Regular Cleaning Schedule: Create a regular cleaning schedule and follow it consistently to prevent the buildup of dirt and debris. A clean machine is less likely to malfunction, reducing the likelihood of costly downtime.
By properly cleaning your roll forming machine product line, you can avoid damage and improve performance, ensuring that the machine operates at peak efficiency for a longer period of time. A clean machine also reduces the risk of contamination and contributes to a safe and healthy work environment.
Lubrication for Your Roll Forming Machine Product Line
-
Vineyard Post Roll Forming Machine
-
Auto Size Changeable Sigma Purlin Roll Forming Machine
-
PV Mounting Bracket C Shape Profile Roll Forming Machine
-
C Z Purlin Channel Cold Roll Forming Machine Full Auto Galvanized Steel Profile
-
PV Mounting Bracket Roll Forming Machine (HAT / Omega Profile)
-
PV Mounting Bracket Z Shape Profile Roll Forming Machine
Proper lubrication is crucial for maintaining the optimal performance of a roll forming machine. Lubrication helps to reduce friction between the machine’s moving parts, including the rollers and gears, and prevent wear and tear. Here are some tips for proper lubrication of a roll forming machine:
- Choose the Right Lubricant: Select the appropriate lubricant for your roll forming machine product line based on the manufacturer’s recommendations. Different lubricants are designed for different applications and operating conditions.
- Lubricate Regularly: Establish a regular lubrication schedule and stick to it. Regular lubrication ensures that the roll forming machine product line’s moving parts stay well-lubricated, reducing friction and wear.
- Apply the Right Amount: Apply the right amount of lubricant to each moving part. Applying too little lubricant can lead to excess friction, while applying too much can lead to contamination and damage to the machine.
- Use the Right Method: Choose the right method for lubricating each part of the roll forming machine product line. Some parts may require manual lubrication with a brush or spray, while others may require automatic lubrication.
- Check for Leaks: Regularly check for leaks and make sure that the lubrication system is functioning properly. Leaks can lead to excess friction and damage to the machine’s components.
By properly lubricating a roll forming machine product line, businesses can extend the life of the machine and prevent costly downtime. Proper lubrication also helps to ensure that the machine operates at peak performance, reducing the likelihood of malfunctions and improving product quality. By following these tips for proper lubrication, businesses can ensure the optimal performance of their roll forming machine for years to come.
Inspection for Your Roll Forming Machine Product Line
Regular inspection of a roll forming machine’s components is essential for ensuring optimal performance and preventing equipment failure. Here are some tips for properly inspecting a roll forming machine:
- Establish a Regular Inspection Schedule: Set up a regular inspection schedule based on the manufacturer’s recommendations and the machine’s operating conditions. Inspect the machine product line at regular intervals, such as weekly or monthly.
- Check the Rollers: Check the rollers for wear and tear, and make sure they are properly aligned. Misaligned rollers can cause damage to the machine’s components and lead to poor product quality.
- Inspect the Tooling: Inspect the tooling for wear and tear, and make sure it is properly secured. Loose tooling can cause damage to the machine’s components and lead to poor product quality.
- Check the Electrical Components: Inspect the electrical components for signs of damage or wear, and make sure they are properly grounded. Damaged electrical components can cause malfunctions and pose a safety hazard.
- Document Any Issues: Document any issues or potential problems identified during the inspection process. This can help to identify trends and patterns that may require attention, and help to prevent future equipment failure.
By regularly inspecting a roll forming machine product line’s components, businesses can identify potential problems and prevent equipment failure. Regular inspections can also help to ensure that the machine operates at peak performance, reducing the likelihood of malfunctions and improving product quality. By following these tips for proper inspection, businesses can ensure the optimal performance of their roll forming machine for years to come.
Troubleshooting with roll forming machine product line
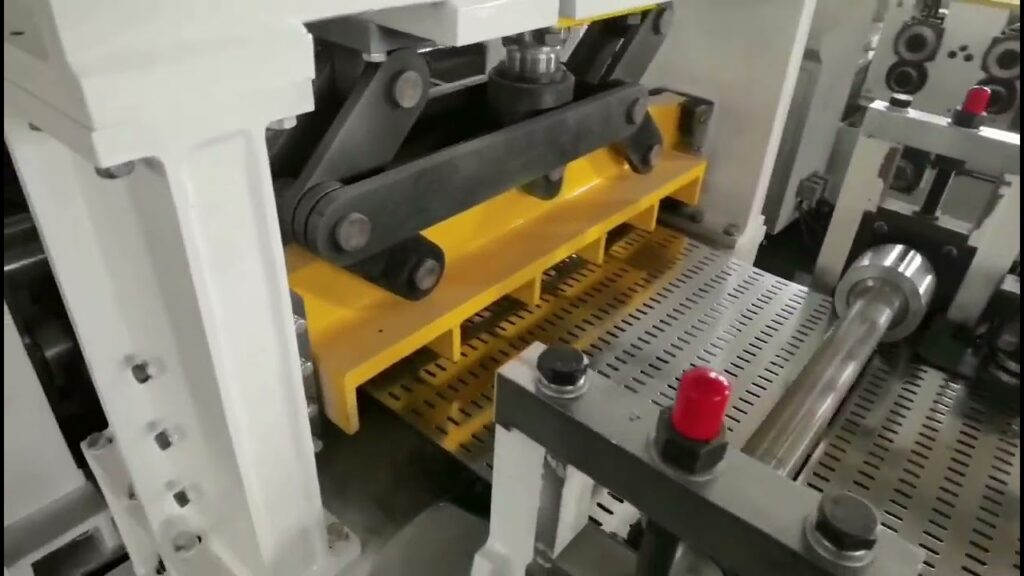
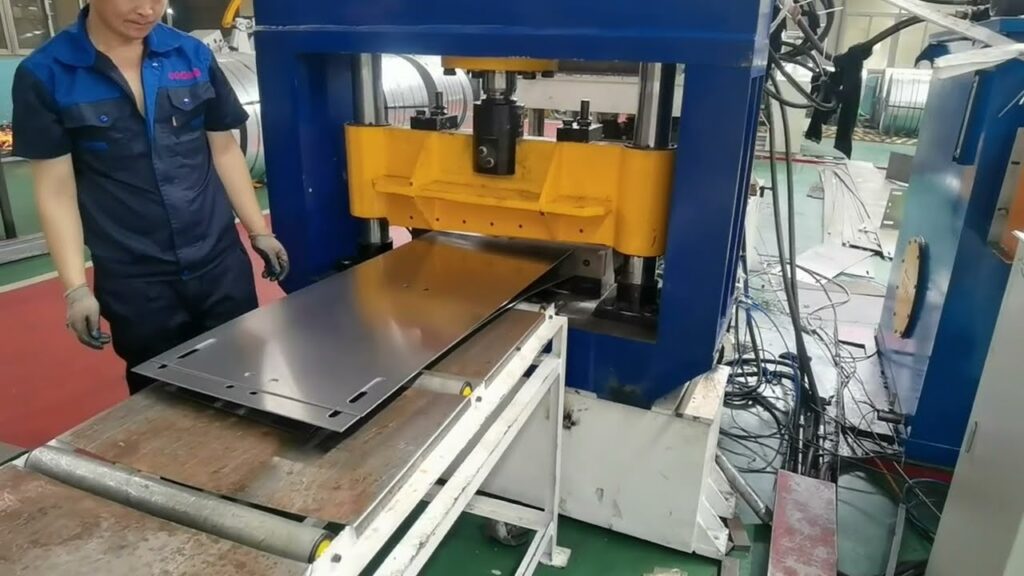
Roll forming machines can encounter various issues that can disrupt the production process and affect product quality. Here are some common issues that can arise with roll forming machines and tips for troubleshooting them:
- Material Jams: Material jams can occur when the roll forming machine’s rollers become clogged with material. To troubleshoot a material jam, stop the machine and clear the clogged material. It’s important to identify the cause of the jam to prevent it from happening again in the future.
- Misaligned Rollers: Misaligned rollers can cause damage to the machine’s components and lead to poor product quality. To troubleshoot misaligned rollers, stop the machine and check for any visible misalignments. Adjust the rollers as needed, and make sure they are properly secured.
- Electrical Problems: Electrical problems can cause malfunctions and pose a safety hazard. To troubleshoot electrical problems, check the machine’s electrical connections and make sure they are properly grounded. If there is a specific electrical component that is causing problems, it may need to be replaced.
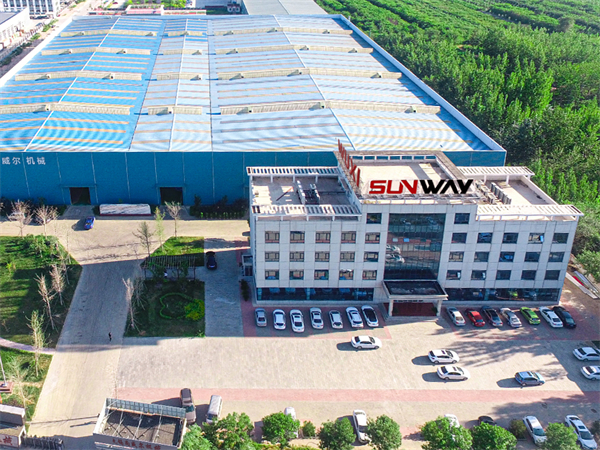
- Wear and Tear: Over time, roll forming machines can experience wear and tear on their components. To troubleshoot wear and tear, perform regular inspections and maintenance tasks. Replace any worn or damaged components as needed.
- Poor Product Quality: Poor product quality can be caused by a variety of factors, including misaligned rollers, worn tooling, or other issues with the machine’s components. To troubleshoot poor product quality, perform a thorough inspection of the machine and its components, and make any necessary adjustments or repairs.
By properly troubleshooting roll forming machine issues, businesses can prevent downtime, improve product quality, and ensure the optimal performance of their equipment. It’s important to address issues as soon as they arise to prevent further damage and minimize the impact on production.
Proper maintenance of roll forming machines is crucial for ensuring optimal performance and prolonging the machine’s lifespan. Regular cleaning, lubrication, inspection, and troubleshooting are essential to prevent costly downtime and improve product quality. By following these tips for maintaining a roll forming machine product line, businesses can ensure the machine operates at peak efficiency and prevent equipment failure. Proper maintenance also helps to ensure a safe and healthy work environment. By investing time and resources in the maintenance of a roll forming machine, businesses can maximize their return on investment and achieve greater productivity and profitability.