Introduction
Roll forming is a metalworking process that involves gradually bending a long strip of sheet metal into a desired cross-sectional profile. It is an efficient and cost-effective way to manufacture parts with consistent accuracy and quality. Automatic roll forming machines play a crucial role in modern manufacturing by automating the production of metal components for a wide range of industries.
This article will provide an in-depth look at automatic roll forming technology, including how it works, its key components, and the many benefits it offers over manual roll forming methods. We’ll also examine some of the most common applications of automatic roll forming machines and the evolving capabilities that are expanding their usefulness. By understanding the technology and applications of these machines, manufacturers can determine if implementing automated roll forming is right for their production needs.
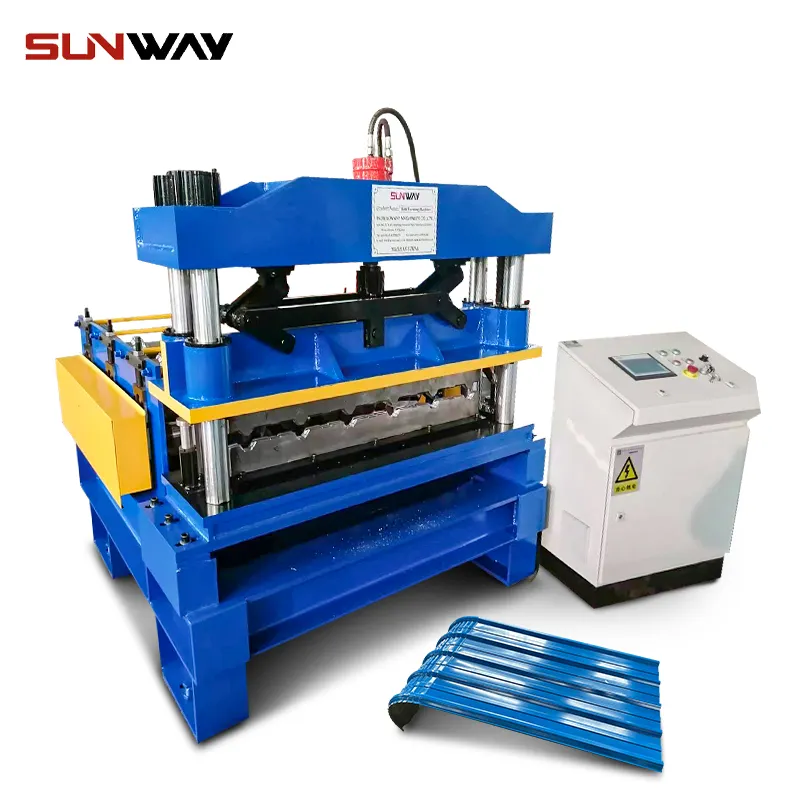
How Automatic Roll Forming Machines Work
Automatic roll forming utilizes a series of consecutive pairs of contoured rolls that gradually shape sheet metal stock into the desired form as it passes through the machine. The process involves continuously feeding a flat strip of sheet metal through a series of rolling stations. Each rolling station incrementally forms the material closer to the target profile.
The key components and functions of an automatic roll forming machine include:
- Uncoiler: A large spool that holds the coiled sheet metal to be formed. It steadily unrolls and feeds the material into the first station.
- Feeding mechanism: Controls the precise feed rate of the material through each successive rolling station. Common feeding methods include pinch rolls, caterpillar drives, and servo motor drives.
- Forming stations: Each station consists of a stand holding a matched set of contoured rolls. The rolls have matching profiles that progressively form the material as it passes through. The number of stations required depends on the complexity of the final profile.
- Supporting rolls: Provide additional support and guidance to the material between forming stations.
- Cut-off press: Cuts the continuously formed product into desired lengths. Can be manual, pneumatic, or servo-electric powered.
- Controller: Computerized control system that coordinates all machine movements and sequences. Allows for quick roll set changes and adjustments.
The rolls in the forming stations do the actual bending and shaping of the material. The top and bottom rolls have matching contours and turn in opposite directions to grip and form the strip. The gradual incremental formation at each station eliminates stretching and thinning of the material that occurs with sharp 90° bends.
Roll forming machines can be horizontal or vertical in orientation. Horizontal machines take up less floor space while vertical machines allow gravity to assist with material feed. All the key components are essentially the same for both configurations.
Benefits of Automatic Roll Forming
Automating the roll forming process with advanced machines offers a number of significant advantages over manual roll forming:
High Production Speeds
- Modern high-speed roll forming lines can produce up to 16,000 feet of material per hour. This allows high volume production that would not be feasible with manual methods.
Improved Accuracy and Consistency
- Automated machines precisely control the material feed rate and roll station sequences. This removes variability from human operators and ensures every part meets specifications.
Flexible and Easily Adjustable
- Quick roll set changes allow fast transitioning between different profiles. The programmable controls also make it easy to modify machine parameters for new products.
Safer Working Environment
- Removing direct human interaction with the dangerous rolling machinery greatly improves operator safety. The machines also reduce accident risks by eliminating handling of heavy rolls.
Reduced Labor Requirements
- Automating the roll forming process minimizes the direct labor needed. One operator can simultaneously manage multiple machines.
Ability to Integrate Post-Forming Operations
- Automated production lines can include integrated cutting, punching, welding, and other secondary processing operations. This improves efficiency and minimizes material handling.
Lower Long-Term Costs
- Despite higher initial capital costs, automated roll forming machines offer better productivity, labor savings, and operating costs compared to manual operations.
By transitioning from manual operations to automated roll forming technology, manufacturers can enjoy higher and more consistent production volumes along with significant cost and safety improvements.
Common Applications of Automatic Roll Forming
Automatic roll forming machines are highly versatile and can produce metal profiles for many industries and applications. Here are some of the most common uses:
Building Construction
- Roofing panels, wall panels, drainage components, studs, track, joists, trusses
Automotive Manufacturing
- Body panels, frames, supports, brackets, rails, pillars, tubes
Appliances
- Housings, frames, ducts, shelving, tubing, spun rings
Furniture
- Legs, frames, supports, arms, back braces
Shelving and Racking
- Upright supports, beams, braces, decking
Electrical and HVAC
- Conduit, heat shields, ducts, enclosures, lighting fixtures
Agricultural Equipment
- Frames, supports, chutes, tubes, hardware
Office Furniture
- Legs, supports, cubicle parts, wire management, shelving
This diverse range of applications highlights the versatility of roll formed components. The flexible production capabilities of automated roll forming machines allow manufacturers to meet the metal part needs of many industries.
Evolving Roll Forming Technology
In recent years, advanced technologies have expanded the capabilities of automated roll forming equipment. Ongoing innovations are opening up new opportunities and allowing manufacturers to gain even more benefits from these machines. Some notable new developments include:
Servo-Electric Machine Actuation
- Using servo motors instead of hydraulic systems allows more precise control over the rolls and material feed. This improves forming accuracy and allows higher production speeds.
In-Line Twist Forming
- Special twist-capable machines can form complex profiles involving rotation of the material, such as square/rectangular tubes, special beams, and spiral ductwork.
Quick Changeover Features
- New roll sets utilizing cartridge designs or quick-connecting tooling reduce roll changeover time, allowing faster transitions between profiles.
Advanced Monitoring Systems
- Upgraded computer controls monitor production in real-time and automatically make adjustments to prevent quality issues. Some systems can even track tool wear to optimize maintenance.
Integration of Secondary Operations
- Automated punching, cutting, drilling, bending, welding, and other operations are being integrated into unified production lines along with roll forming. This creates complete production cells with minimal handling.
Specialized Component Handling
- Improved part offloading systems, stackers, and conveyors allow efficient handling of finished parts up to 40 feet long.
Technology for Small Production Batches
- Programmable servo-motor drives allow fast profile changes for short production runs. This makes automated roll forming viable even at lower volumes.
The drive to leverage Industry 4.0 technologies will further the capabilities of automated roll forming machinery. Ongoing enhancements in flexibility, intelligence, and integration will expand the applications where these machines provide ideal production solutions.
Implementing Automated Roll Forming
Manufacturers looking to implement automated roll forming technology should carefully evaluate their production volumes, product mix, available space, and labor considerations. Seeking guidance from qualified roll forming equipment suppliers is also essential to identify the right machine capabilities and optional features.
The following are some of the key factors to consider when adopting automated roll forming equipment:
- Production volumes – Higher volumes offset the capital costs and allow maximizing the efficiency benefits. But configurable machines can support lower volumes as well.
- Product width/gauge variations – Review material requirements and determine if quick-changeover features are needed.
- Type of secondary operations required – Integrating operations like punching, cutting and hardware insertion improves throughput.
- Available facility space – Length and configuration requirements depend on production line design.
- Labor factors – Automated equipment can help offset labor shortages and reduce reliance on operator skills.
- Safety – Ensure the system is designed to the latest safety standards and guards dangerous areas.
- Total Cost of Ownership – Weigh capital cost, projected operating expenses, maintenance, and labor savings over the lifespan of the equipment.
With careful planning guided by expert input, manufacturers can implement automated roll forming equipment that delivers maximum productivity, flexibility, and return on investment.
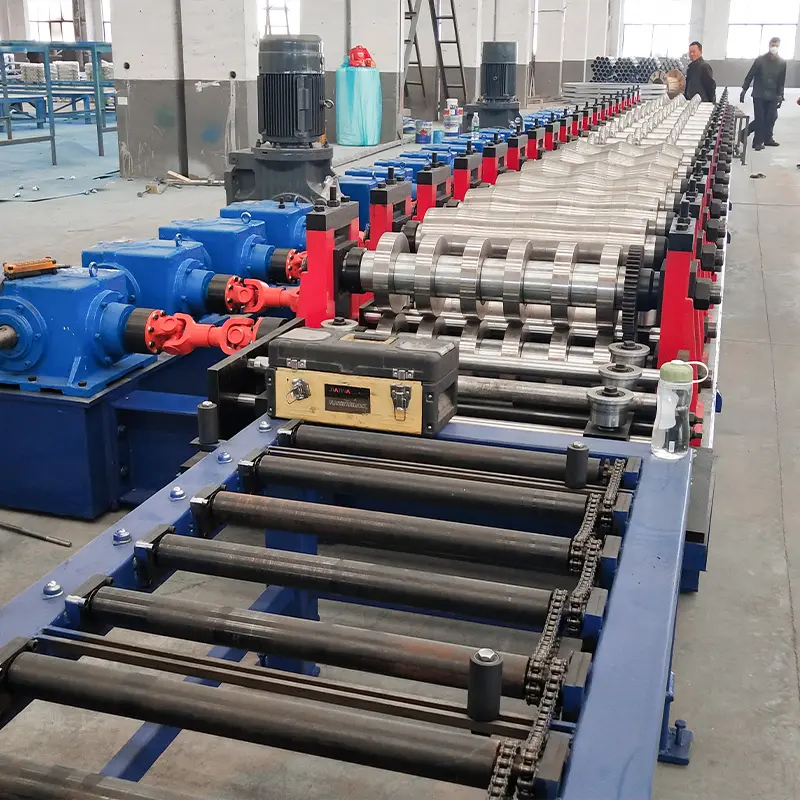
Conclusion
Automatic roll forming machines provide transformative benefits for producing metal parts with unmatched efficiency and precision. By automating the incremental forming process, roll formed components can be manufactured at high volumes with great accuracy and consistency. Ongoing advances are expanding the capabilities of these versatile machines.
Roll forming is now being applied to an ever-wider range of components for industries from building construction to automotive manufacturing. The flexibility, improved quality, and labor savings of automated roll forming make it an increasingly attractive production method. Manufacturers who leverage this technology will gain key advantages in meeting demand for metal parts and staying competitive.
Frequently Asked Questions About Automatic Roll Forming Machines
Here are some common questions about automatic roll forming machines and technology:
Q: What types of metals can you roll form?
A: The most commonly roll formed metals are steel, aluminum, and copper alloys. Steel is used for the majority of roll formed parts. Any ductile metal that can hold its shape after bending can be roll formed.
Q: How do you design parts for roll forming?
A: Designing parts requires close collaboration between the manufacturer and equipment supplier. Complex profiles may need multiple forming stations and secondary operations. Simpler, open profiles are usually easiest to roll form.
Q: How long does it take to set up roll forming machines for new parts?
A: On older machines, roll changes could take many hours. Modern quick changeover designs allow changing complete roll sets in under 10 minutes in some cases. Servo-driven machines also help speed profile changeovers.
Q: What are the limitations of roll forming versus other processes?
A: Roll forming is ideal for high volume production of parts up to 10 feet wide from coiled stock. It has more limitations forming small batches, thick material, or complex 3D shapes. The capital cost can also be high for low volume production.
Q: How do you maintain roll forming equipment?
A: Preventive maintenance involves regular greasing, inspection for leaks, checking roll and guide wear, and replacing fluids/filters per the manufacturer’s schedule. Operators also need to watch for issues during production.
Q: Can you add secondary operations to a roll forming line?
A: Yes, integrating punching, cutting, bending, welding, and hardware insertion after roll forming is a growing trend. This automates production of finished parts without handling between processes.
Q: Are there safety concerns with roll forming machinery?
A: All moving components must be guarded to protect workers from hazards like pinch points. Newer machines have interlocked guards and emergency stops. Noise exposure and lifting rolls also needs addressing.