Floor deck roll forming machines are an efficient and cost-effective way to produce floor decks for buildings. Floor decks are corrugated steel sheets that are used to make the floors in buildings. Floor deck roll forming machines form the steel coils into the corrugated deck profile through a continuous and automated process. Using a floor deck roll forming machine provides many advantages compared to other floor deck manufacturing methods.
Fast Production Speeds
One of the biggest advantages of floor deck roll forming machines is their fast production speeds. These machines can produce floor decks at very high linear feed rates, up to 130 feet per minute. This allows a single machine to produce thousands of square feet of floor decks per hour. The fast production speeds are achieved through the continuous roll forming process and automated features of the machine.
As the steel coil is fed into the machine, it passes through a series of roller stations. Each roller station progressively forms the steel into the corrugated deck profile. This continuous process eliminates the start and stop of other manufacturing methods. The automated features of the machine, such as coil payoff and recoilers, also improve efficiency over manual methods. The high volumes of floor decks that can be produced by these machines make them ideal for large construction projects or floor deck manufacturers.
Consistent Quality and Accuracy
Another big advantage of floor deck roll forming machines is their ability to produce floor decks with very consistent quality and accuracy. The roller stations in the machines are machined to precise specifications so that each deck profile is formed exactly the same. This ensures the quality and structural integrity of the floor deck.
The automated features of the machines also improve accuracy over manual methods. For example, the coil payoff uses powered unwinders to keep the feed of material consistent. The punching and shearing stations use precision dies to cut the deck to length with exact tolerances. All of these automated features result in floor deck that meets strict quality standards.
Flexible Production Capabilities
Floor deck roll forming machines provide manufacturers with flexible production capabilities. One machine can produce floor decks with different rib profiles, depths, and widths. This is achieved by changing out the roller stations to match the desired profile. It allows manufacturers to switch production runs quickly to meet changing customer demands.
The machines can also accommodate different steel coil widths and gauges. Coils from 18 inches to 5 feet wide and gauges from 22 to 14 can be run. This flexibility enables manufacturers to produce a wide range of floor decks without being limited to certain sizes or coil parameters. The versatile production abilities make these machines a good investment for manufacturers.
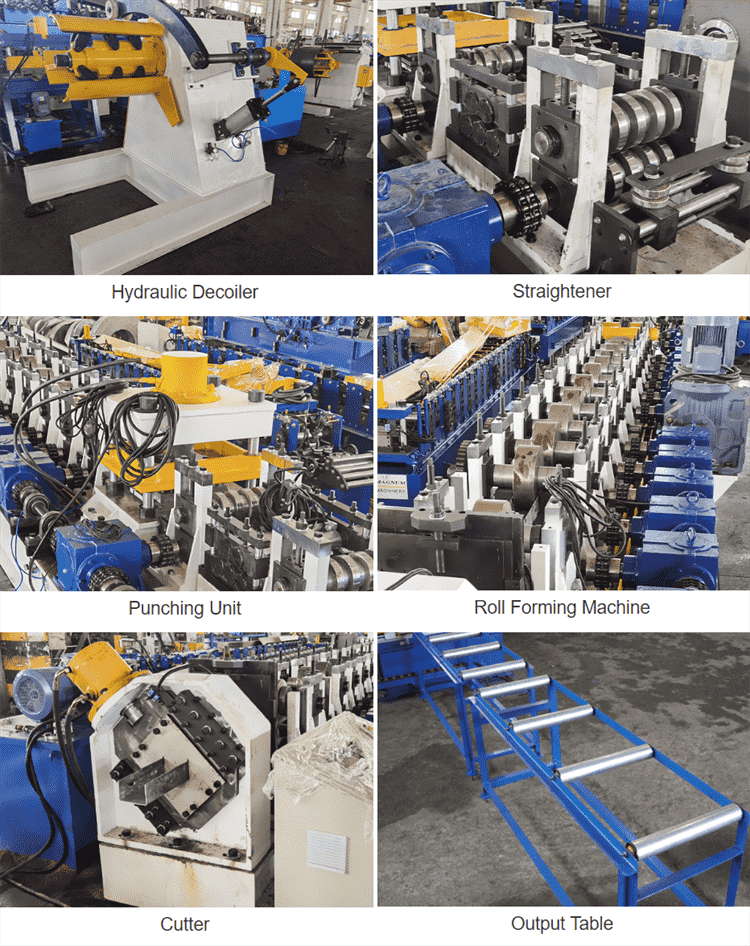
Efficient Material Usage
Floor deck roll forming machines maximize material usage and minimize waste. First, the continuous roll forming process converts 100% of the steel coil into the finished floor deck product. There is no loss from cutting patterns or stamping forms.
The machines also nest the floor deck profiles tightly together within the coil width. This optimizes the material usage across the coil. Any edge trim scrap can be automatically re-fed into the system to produce more floor deck.
For custom deck lengths, the punching and shearing stations can cut the profiles with minimal scrap loss between pieces. Overall, the whole roll forming process converts more of the steel coil into usable finished floor deck compared to other methods. This provides cost savings for manufacturers.
Lower Labor Requirements
Floor deck roll forming machines require much less labor than other deck manufacturing methods. Most of the roll forming process is automated with powered unwind and recoilers, self-feeding rollers, and numerical control. This reduces the need for workers to handle the steel coils or perform manual forming and cutting operations.
Most floor deck roll forming machines only require 1 to 2 workers to monitor the machine and do auxiliary tasks like tying off finished bundles. This is a big advantage compared to more labor-intensive methods like pressing brakes or flexible fabrication. The automation lowers overall labor costs and safety risks for manufacturers.
Safer Working Conditions
The high level of automation and safety features on floor deck roll forming machines also make them a safer deck manufacturing method. Workers do not have to perform strenuous or repetitive tasks that often lead to injuries. The machines have safety guards around the rollers and other moving parts.
Many modern machines have advanced safety monitoring systems too. This includes things like e-stop buttons, pull cords, and remote emergency stops. The automation and safety systems minimize risks and create a safer working environment compared to older manufacturing methods. This benefits both workers and manufacturers.
Lower Energy Consumption
Floor deck roll forming machines are an energy efficient way to manufacture floor decks. The electric motor and drive system that powers the rolling stations only needs to overcome the friction of forming the steel coils. This low resistance allows the motors to operate with relatively low energy use.
Other manufacturing methods like hydraulic presses have much higher energy demand from the force needed to form each individual piece. The continuity of the roll forming process spreads the energy usage over higher material volumes. When combined with the nesting and scrap reduction, roll forming is one of the most energy efficient metal forming processes. This saves on energy costs for manufacturers.
Smaller Factory Footprint
The compact footprint of floor deck roll forming machines allows manufacturers to set up deck production without needing huge factories. A typical machine has a length around 100 feet. Some machines can produce multiple deck profiles in an even smaller space.
Other methods like stamping presses require much larger spaces between presses, material staging areas, and inventory storage. The compact nature of roll forming technology enables deck manufacturing with lower facility costs. Manufacturers can set up operations in smaller buildings and require less material handling equipment. This can provide big savings versus larger production shops.
Lower Investment Costs
The purchase price of floor deck roll forming machines is lower than other deck manufacturing equipment. Individual machines cost a few hundred thousand dollars depending on their size and production speeds. This is much more affordable than large stamping press systems that can cost millions.
For manufacturers doing lower to medium production volumes, the investment costs of roll forming equipment is within reach. The automated nature of the equipment also lowers the operating costs for labor, energy, and material waste. This combination of lower investment and operating costs makes roll forming an economical choice for many manufacturers. The potential profits on deck production offset the capital outlay.
Quick Installation and Set Up
Installing and setting up floor deck roll forming machines is a quicker process compared to heavy production lines. Most roll forming machines are delivered as complete systems that just need utilities connected. This reduces the installation time versus constructing complete press beds and stamping systems.
The modular design of roll formers also speeds up set up. Each roller station is individually adjusted and set for the desired profile. The coil payoff, shear, and exit tables are then aligned before production starts. This process takes days versus weeks or months for large production systems. Manufacturers can get their roll forming line up and running very quickly.
Better Finished Quality and Consistency
The roll forming process results in higher quality finished floor decks versus other manufacturing methods. As the steel passes through the successive rolling stations under controlled tension, the corrugations are formed precisely and uniformly. This leads to a deck with very consistent rib shapes and flatness along its length.
Press brake or press forming can leave slight variations through the deck from the individual forming of each piece. Roll formed decks have no these variations, giving them better finish quality. The process also cold works and hardens the steel more than pressing. This increased hardness helps the decks maintain their shape during handling and installation. Overall, roll formed decks have quality advantages over other manufacturing techniques.
Environmentally Friendly Process
Roll forming is one of the most environmentally friendly metal processing technologies available. It generates almost no waste compared to other methods because 100% of the coil gets converted into finished product. Presses and stamping lose material to scrap pieces and holes punched out.
The enclosed roll forming process also produces no oil run off or other pollution. The electric motor drives produce low emissions when powered with clean electricity. Roll formed products can even be made from recycled steel coils. Overall, it is much more sustainable than older industrial processes that generate lots of scrap and waste. This environmental benefit is increasingly important for manufacturers and their customers.
High Production Scalability
Roll forming technology offers high scalability to match increasing production demands. Manufacturers can run 2 or 3 shifts per day on a machine to immediately boost output as needed. The modular design also lets line capacity be increased by adding additional roll forming stages or running multiple machines in tandem.
With space planning, a manufacturer could double or triple their initial production capacity in the same factory simply by adding more equipment. This level of scalability is difficult and expensive to achieve with large press or stamping systems that require whole new production lines. The scalability of roll forming gives manufacturers much more production flexibility and future growth potential.
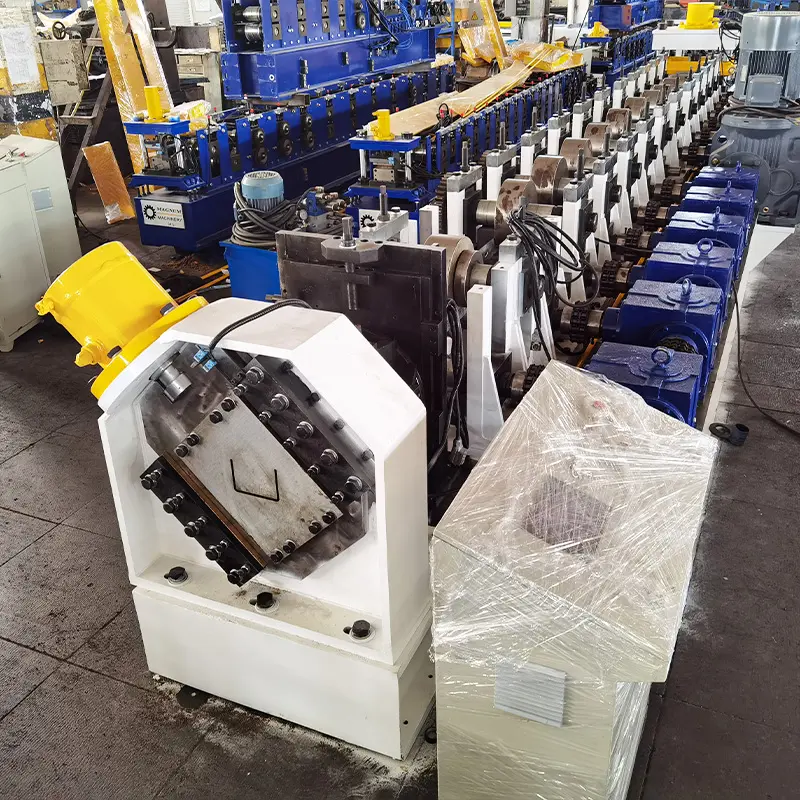
Ability to Integrate with Other Processes
Floor deck roll forming machines can be integrated with other processing stations to create complete production systems. Decoilers and feeder stations can be added to handle material delivery from storage racks and automatically feed the coils into the roll former.
Exit tables and stackers can automate the collection and bundling of the finished decks. Conveyors can link processes like deck embossing/patterning together with the roll former. This total system integration improves efficiency and reduces the amount of handling required.
The modular design of roll formers makes it simple to create customized production lines optimized for specific deck products. This integration potential increases throughput for manufacturers while keeping equipment footprints compact.
Lower Maintenance Requirements
Compared to heavy stamping presses and fabrication machinery, floor deck roll forming machines have much lower maintenance needs. The electric motors and drive trains are very reliable with long service lives before major repairs are needed.
The roller stations have sealed bearings that only require infrequent lubrication. The stations are positioned along the sides of the machine, making them easily accessible for maintenance. Tooling is minimal with only profile rolls and a few slitters/punches that can be changed out when worn. Keeping roll formers running is straightforward for manufacturers.
High Uptime and Reliability
Properly maintained floor deck roll forming machines provide very high uptime and reliability. The typical simple mechanical design and rugged construction mean these machines can run for years without breakdowns. Critical components like gearboxes, rollers, and motors are oversized and over-designed for long life cycles.
Unplanned downtime is minimized through layouts that avoid material jams and allow quick clearing if they occur. Diagnostics help catch issues before failure. The reliable design translates to machines that deliver consistent production volumes day after day. This steady output is essential for manufacturers that need to meet construction project demands.
Long Service Life
Floor deck roll forming machines represent capital equipment investments that provide decades of reliable production. With their heavy-duty construction and reliable components, these machines often outlast other shorter-lived production equipment. Their service life can exceed 20 years or more.
Upgrading and refurbishing roll formers is also more feasible compared to replacing complex stamping presses. This extends their usefulness even farther. The long service life and upgrade potential provide excellent return on investment for manufacturers. The versatility of roll formers allows producing different products over their lifetime as demands change. This longevity makes roll forming equipment a wise manufacturing investment.
Superior Production Efficiency
The combination of fast production speeds, low operating costs, and reliability means floor deck roll forming machines offer superior production efficiency. Manufacturers can achieve the highest throughput of quality floor decks using the least amount of facility space, labor, energy, and maintenance.
The savings continue because roll formed decks require less inventory storage thanks to just-in-time production. And the automated nesting minimizes wasted material. Across all metrics, roll forming machines provide excellent performance and economics. This production efficiency gives manufacturers advantages in productivity, quality, and profitability over other floor deck manufacturing methods.
Flexibility for Design and Material Changes
An additional advantage of floor deck roll forming machines is their flexibility to accommodate product design changes and material variations. Switching to a new rib profile simply requires changing the profile rolls in the roller stations to match the new shape. This can be accomplished in hours without needing new press tooling or dies that take weeks to obtain.
Material thickness changes can also be managed by adjusting the roller gaps and support guides. This allows roll forming lines to handle a range of steel coil parameters beyond just a fixed gauge. Manufacturers can implement deck design updates and material changes much faster than with fixed press lines. This keeps roll forming technology adaptable as product specifications evolve.
Ability to Add Secondary Processing
Roll formed floor decks can be automatically processed through additional inline stations to add further enhancements or features. Common secondary capabilities include:
- Embossing – Adds raised diamond, grid, or other patterns to the deck surface for increased grip and aesthetics.
- Hole punching – Punches small holes for attaching insulation supports, utilities, or other items to the underside of the deck.
- Shear stud punching – Cold punches holes and inserts shear studs for composite decking used in construction systems.
- Curving – Imparts a slight longitudinal curve to the deck for arched building designs.
- Corrugation rolling – Further flattens and crisps the deck profile.
- Marking – Inkjets printing, logos, identification numbers, or other information right on the deck.
These secondary processes can be easily integrated into roll forming lines thanks to their modular nature. This allows manufacturers to create high-quality enhanced deck products beyond just basic flat sheets.
Summary of Benefits
Floor deck roll forming machines offer numerous technology, efficiency, quality, and cost advantages to manufacturers:
- Fast production speeds up to 130 feet per minute enable high volumes of deck.
- Automated processes ensure consistent deck quality and accuracy.
- Flexible production to make different width/gauge decks through roller and coil changes.
- Efficient material usage with minimal waste compared to other methods.
- Low labor requirements – typically 1 to 2 workers to operate.
- Safe working conditions from machine guarding and safety systems.
- Energy efficient forming process has lower demand than presses or stamping.
- Compact footprint fits into smaller factory spaces.
- Affordable equipment investment versus large press lines.
- Quick installation since machines come as complete systems.
- Quality advantages from precision cold roll forming process.
- Environmentally clean process with no oil waste or pollution.
- Scalable production through added shifts or extra machines.
- Integrates with other material handling and processing stations.
- Simple mechanical design requires minimal maintenance.
- Reliable performance provides high uptime and long service life.
- Excellent efficiency with low operating costs and high output.
- Flexible to design/material changes by adjusting tooling and settings.
- Ability to add secondary processing like embossing inline.
With all of these technology, quality, efficiency, and cost benefits, floor deck roll forming machines are the premier solution for high production floor deck manufacturing. Their advantages over alternative manufacturing methods make roll forming the ideal choice for both high-volume producers and smaller manufacturing shops. If your company needs an automated, versatile, and profitable solution for manufacturing floor decks, floor deck roll forming machines should be the leading equipment candidate. Their benefits truly maximize productivity, quality, and profitability for floor deck manufacturing.
FAQ
What types of floor deck profiles can be made on these machines?
Floor deck roll formers can produce many different rib profiles including standard wide rib, intermediate rib, narrow rib, compartmentalized, and cellular decks. The profile is controlled by the roll dies in each successive rolling station along the machine. These dies can be changed out to switch profiles if needed.
What sizes of floor deck can be made?
Typical sheet widths range from 18 inches up to 5 feet wide to match common coil sizes. Lengths usually range from 8 feet to 24 feet but can go longer. Thicknesses of .014″ to .075″ (14 gauge to 22 gauge) steel coil can be run. Machines can handle lighter or heavier gauges if configured appropriately.
How fast is the production rate?
Production speeds range from 75 to over 130 linear feet per minute depending on the machine. This equates to over 10,000 square feet per hour for a 5 foot wide machine running at 100 fpm. Speeds can be varied to balance throughput and profile quality.
How much steel coil does the machine hold?
The coil payoff can hold multiple coils with total weight over 30,000 pounds. As one coil is exhausted, the next is automatically welded on-the-fly to the sheet so production continues uninterrupted. This allows for extended runs before reloading coils.
What safety features are included?
Guards around all moving parts, emergency stop buttons and pull cords along the length, tension and alignment monitoring, and electrical disconnects/motor brakes are some typical safety features. Newer machines can have advanced features like remote monitoring and diagnostics.