Stud and track machines, also called steel frame roll forming machines, produce studs and tracks for light gauge steel framing in buildings. Studs are vertical beam components while tracks are U-shaped channels.
What are Steel Studs and Tracks?
Steel studs and tracks are key components in the construction of interior and exterior walls, partitions, and ceilings in buildings. They are part of the framework that supports the building’s structure and serves as a framework for attaching drywall or other wall cladding materials. These components are typically made of galvanized steel and are known for their durability, strength, and versatility in various construction applications.
Here’s an explanation of steel studs and tracks:
- Steel Studs:
- Steel studs are vertical, load-bearing members used to create the wall’s structural frame.
- They are available in various sizes and thicknesses, allowing builders to choose the appropriate studs based on the wall’s height and load-bearing requirements.
- Steel studs come in two main profiles: C-shaped and U-shaped. The “C” profile is commonly used for walls, while the “U” profile is used for framing door and window openings.
- These studs are lightweight compared to traditional wood studs, making them easier to handle and transport.
- Steel studs are fire-resistant and less susceptible to rot, pests, or warping, which can be issues with wood studs.
- Steel Tracks:
- Steel tracks, also known as runners or channels, are horizontal members that run along the top and bottom of the wall.
- The top track is installed at the ceiling, while the bottom track is attached to the floor or subfloor.
- They provide stability and a base for attaching the steel studs and securing the wall structure.
- Like studs, tracks are available in various sizes to accommodate different wall heights and configurations.
- Steel tracks may also be used as headers or sills in door and window openings to support the framing around them.
Steel studs and tracks are typically used in commercial and residential construction because they offer several advantages, including:
- Consistency: Steel studs are manufactured with precision, ensuring uniform dimensions and straightness.
- Fire Resistance: Steel is non-combustible and offers improved fire resistance compared to wood.
- Termite and Mold Resistance: Unlike wood, steel studs are not susceptible to termites or mold growth.
- Space Efficiency: Steel studs are narrower than wood studs, allowing for more interior space within the walls.
- Sustainability: Steel is a recyclable material, making it an environmentally friendly choice.
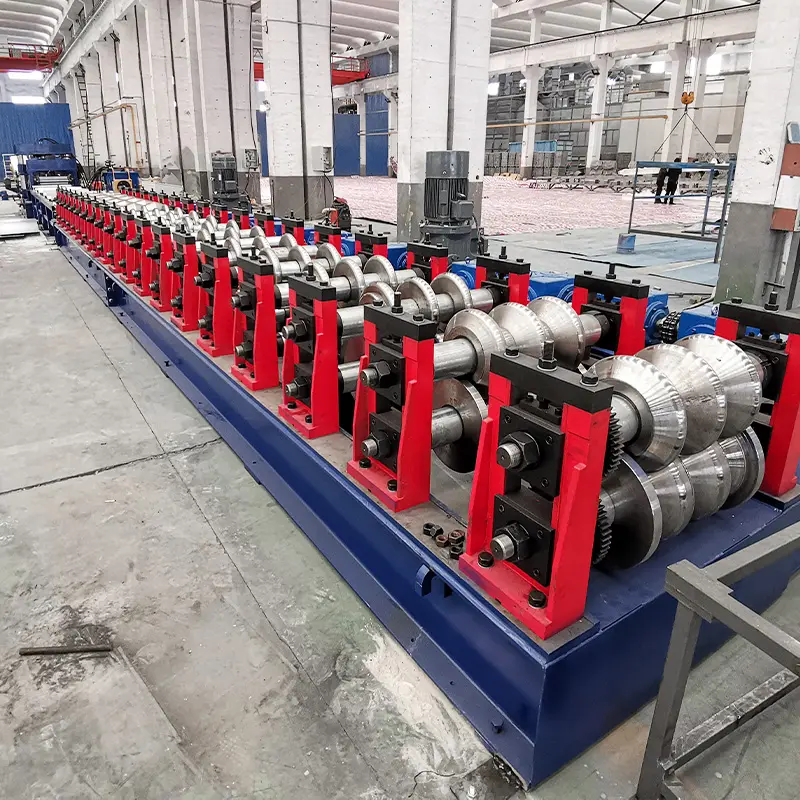
Key Details of Stud and Track Machines
- High speed production of different stud and track sizes
- Flexible quick changeover between various profiles
- Rolls frames, studs, tracks, braces and more
- Material thickness between 0.5 mm to 3 mm
- Fully automatic PLC controlled machines
- Production capacity up to 100 m/min
Working Principle
- Coiled steel strip fed for consistent forming
- Progressive stations shape strip into stud/track profiles
- Automated flying cut-off shears beam to length
- Conveyor stacks finished pieces
Main Components
- Decoiling unit
- Feed roll table
- Accumulator/Loop control
- Forming stations with upper/lower rolls
- Cutting unit
- Stacker
Types of Stud and Track Machines
Machine Type | Description |
---|---|
Standard | Fixed sizes; manual size changes |
Fully Automatic | Touch screen controls for all functions |
PLC Control | Pre-programmed forming parameters for sizes |
Customized | Special elements like punching, notching |
Working Process of Stud and Track Roll Forming
The stud and track roll forming process shapes flat steel strip into L/U/C profiles used for light steel framing:
- The decoiling unit feeds raw steel coil strip
- An accumulator controls the strip loop for stable feeding
- The strip passes through forming stations with shaped rollers
- Rollers bend the steel through progressive forming stages into stud or track
- Automated flying shears cut profiles to length
- Formed pieces placed on exit conveyor/stacker
Main Aspects of Stud and Track Forming
Material Feeding
- Cold-rolled galvanized steel coils
- Strip widths up to 2600 mm
- Thickness between 0.5 mm to 3 mm
- Decoiler with precision loop control
Profile Forming
- Up to 20 circular forming stations
- Stations have customized upper/lower rolls
- Rolls have different shapes at each stand
- Automated adjustment of all roll gaps
Cutting & Slicing
- Flying cutter shears U/C profiles
- Rotating shear blades for clean cuts
- Length range from 50 mm to 6000 mm
- Cutting tolerance within ±1 mm
Customization Capabilities
- Addition of hole punching, notching
- Special embossing/marking
- Tooling for new custom profiles
- Integration with auto-packing line
Technical Specifications
Model | Max Width (mm) | Thickness (mm) | Speed (m/min) | Power (kW) |
---|---|---|---|---|
Standard | 1200 | 0.5-2.0 | 40 | 37 |
Heavy-duty | 2600 | 1.5-3.0 | 80 | 132 |
Custom | 1500 | 0.8-2.5 | 60 | 75 |
-
Standing Seam Roof Panel Curving Machine
-
Barrel Corrugated Roll Forming Machine
-
Stand Seaming Roof Panel Roll Forming Machine
-
Downspout Pipe Roll Forming Machine
-
Gutter Roll Forming Machine
-
Trapezoidal Panel Roll Forming Machine
-
Ridge Cap Roll Forming Machine
-
Double Layer Panel Roll Forming Machine
-
Roof Tile Panel Roll Forming Machine
Suppliers and Price Range of Stud and Track Machines
Supplier | Location | Price Range |
---|---|---|
Manufacturer A | China | $40,000 – $250,000 |
Brand B | Europe | $100,000 – $500,000 |
Company C | India | $60,000 – $350,000 |
- Prices depend on speed, automation level and coil width
- Chinese machines are price competitive
- European brands offer high precision with certification
- Indian suppliers provide good value for money
- Budget about 20% extra for additional tooling
Installation, Operation and Maintenance
Stage | Details |
---|---|
Installation | – Civil, mechanical, electrical prep needed <br>- 1-2 weeks installation time |
Operation | – 1-2 semi skilled workers per shift <br>- Touch screen control parameters <br>- Easy changeover for sizes |
Maintenance | – Daily cleaning and oiling <br>- Inspect/replace forming rolls monthly <br>- Check hydraulics, electrics biannually |
- Detailed operator manual provided
- Online troubleshooting service offered
- Consumables include forming rolls, oils, blades
How to Select a Stud and Track Roll Forming Machine
Here are key considerations for selecting stud and track machines:
Application Requirements
- Types of light gauge profiles needed
- Dimensions and technical parameters
- Monthly production volume targets
Machine Capabilities
- Size range – min/max dimensions
- Material thickness capacity
- Production speeds match volumes
- Level of automation vs manual
Supplier Credentials
- Industry experience and clientele
- Responsiveness to inquiries
- Warranties and after-sales support
Budget Aspects
- Investment amount available
- Standard vs customized features
- Expected payback timeline
Clear specifications are essential before comparing alternative suppliers on cost, quality, service metrics.
Pros and Cons of Stud and Track Machines
Pros | Cons |
---|---|
– High production speeds – Easy operation – Low operating costs | – Large floor space – High capital investment – Regular roll maintenance |
Advantages
- Single machine produces all light gauge profiles
- High degree of automation possible
- Ideal for large volume requirements
- Produces studs and tracks for whole building
Limitations
- Regular forming roll replacement
- Not viable for small production batches
- Custom profiles need special tools
- Limited flexibility after installation
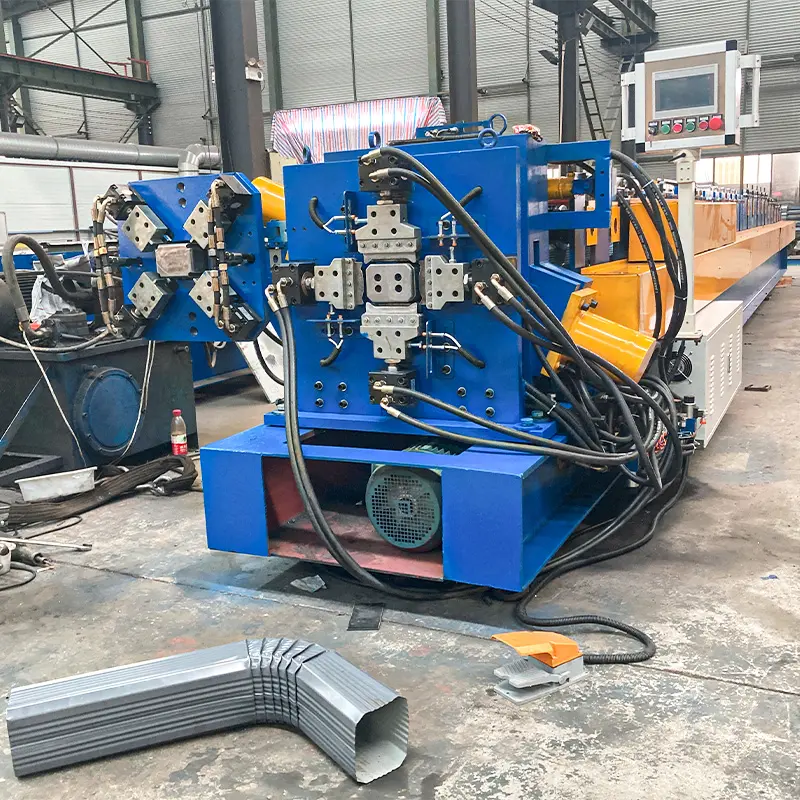
FAQ
Q: What is the typical warranty period for these machines?
A: Warranty is generally 12-18 months covering manufacturing defects under normal operation.
Q: What level of skilled manpower is optimal?
A: Machine operation has easy learning curve. One skilled technician can manage with 1-2 helpers.
Q: How quick is the changeover time between sizes?
A: On fully automatic machines, size changeovers take just 5-10 minutes through PLC programming.
Q: What kind of suspended powders can be handled?
A: Machines typically process cold-rolled and hot-rolled steel coils. Check with supplier for alloy capacity.
Q: What thickness range can these handle?
A: Standard input material thickness is 0.5 mm to 3 mm. Custom machines support up to 5 mm.