Roll forming is a metal forming process used to produce long steel profiles with complex cross-sections. Steel frame roll forming machines are designed to continuously bend a flat strip of sheet metal into the desired cross-sectional profile through consecutive roll stations. Roll formed steel frames are widely used for roof trusses, building frames, car chassis, steel doors, and many other applications that require customized long steel profiles.
This comprehensive guide provides a detailed overview of steel frame roll forming machine technology, types, working principles, major components, design considerations, and suppliers. It also compares the benefits of roll forming versus other profile bending methods.
Overview of Steel Frame Roll Forming Process
Roll forming creates longitudinal profiles through incremental bending in a series of roll stations. The process involves coiling a flat strip of steel sheet through a series of rolls, each positioned progressively to bend the sheet a fraction more to achieve the desired profile shape.
The main advantages of roll forming steel frames are:
- Continuous production of longitudinal profiles up to 50 m long
- High production output up to 120 m/min
- Consistent and accurate profile dimensions
- Low tooling costs compared to other processes
- Capability to form complex asymmetric shapes
- Minimal material wastage
- Low heat input protects material properties
Steel frame roll forming is ideal for producing straight or tapered profiles in medium to high production volumes with shorter lead times compared to press braking or fabrication.
Key Benefits of Steel Frame Roll Forming
Parameter | Advantage |
---|---|
Production Speed | Up to 10x faster than press braking |
Profile Accuracy | Consistent tolerance +/- 1 mm |
Flexibility | Fast changeover between profiles |
Material Savings | Up to 30% less wastage versus fabrication |
Part Length | Continuous profiles up to 50 m |
Lead Time | Roll tools made in 2 weeks |
Process Cost | Lower capital investment |
Product Variety | Suits small to large custom profiles |
Roll Forming vs Other Bending Methods
Process | Description | Typical Applications |
---|---|---|
Roll Forming | Continuous bending through roller stations | Roofing, racks, chassis, steel doors |
Press Braking | Discrete bending at single press brake | Small custom enclosures, brackets |
Fabrication | Cutting and welding steel sections | One-off large structures |
Extrusion | Forcing heated steel through die | Standard sections like I-beams |
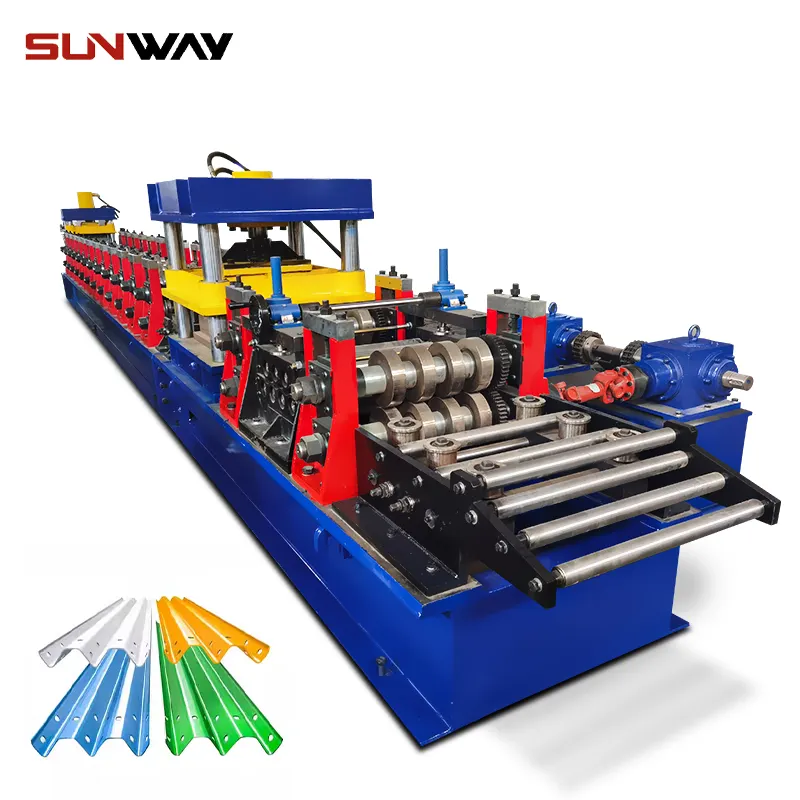
Types of Steel Frame Roll Forming Machines
There are two main types of roll forming machine configurations – in-line and orbital forming.
In-Line Roll Forming Machines
In-line roll formers feed the strip material straight through the inline series of roll stations to incrementally form the profile.
Advantages:
- Compact layout
- Simpler material feeding
- Faster production speeds
Limitations:
- Fixed part lengths
- Size limited by number of roll stations
Typical Applications:
Ideal for high volume production of fixed length steel profiles up to 12 m long, such as racking, solar framing, steel doors.
Orbital Roll Forming Machines
Orbital machines rotate the strip material around a central forming mandrel to pass through roll stations sequentially.
Advantages:
- Continuous production of unlimited lengths
- Ability to produce tapered profiles
- Simpler forming of complex shapes
Limitations:
- Larger footprint
- Slower production speed
Typical Applications:
Best suited for long variable length profiles or irregular shapes like curved trusses, cones, and cylinder shells.
Roll Forming Systems Comparison
Machine Type | Production Speed | Part Length | Profile Shape |
---|---|---|---|
In-line Roll Former | Higher <br>(Up to 100 m/min) | Shorter <br>(Up to 15 m) | Constant cross-section |
Orbital Roll Former | Slower <br>(Up to 40 m/min) | Continuous <br>(Unlimited) | Tapered or complex shapes |
Main Components of a Roll Forming Machine
A steel frame roll forming system contains several key equipment modules:
Uncoiler
- Feeds flat steel coil strip into the roll former
- Capacity up to 10 tonnes
- Powered recoiler to support heavy coils
Roll Forming Stations
- Series of roll tool sets that bend sheet incrementally
- 10 – 25 stations depending on profile
- Roll groove geometry defines bending amount
Punching Units
- Optional CNC punch for holes or notches
- Allows cut-outs in frame profile
Shearing Cutoff
- Shears profile to desired length
- Rotary or guillotine style cutters
Stacker
- Collects formed profiles and stacks
- Optional driven conveyors for part handling
Typical Roll Forming Line Layout
Overview of main modules in a steel frame roll forming machine line
Roll Forming Machine Features
Modern steel frame roll formers include additional features and capabilities to improve productivity, precision and final product quality:
- Servo electric drives on each station for speed and position control
- Automatic gauging to measure profile during running
- Quick-change tooling for faster size changeovers
- Decoiler cassette with powered arm and mandrel for easier coil loading
- Robotic or gantry part handling systems for stacking formed profiles
- Vision systems to check formed profile dimensions
- Roll bending correction systems to automatically adjust roller positions
- CAD programming software to simulate profile forming process
Roll Forming Machine Design Considerations
Key factors to consider when selecting a steel frame roll forming machine:
1. Production Volume Requirements
Required hourly or daily production rate determines machine speed and features.
2. Product Shape and Complexity
More complex bend shapes need more roller stations. Orbital configuration suits complex profiles.
3. Part Length
In-line rollers suit shorter fixed lengths. Orbital allows continuous variable lengths.
4. Available Floor Space
In-line machines have smaller footprint than orbital machines.
5. Coil Width and Thickness
Check machine capacity matches steel coil dimensions.
6. Material Type
Ensure machine rigidity and power for high strength materials like stainless steel.
7. Automation Needs
Consider coil handling, part stacking, and correction automation features.
Roll Former Selection Guide Based on Key Requirements
Requirement | Recommended Machine Type |
---|---|
High speed production | In-line roll former |
Complex profiles | Orbital roll former |
Short fixed lengths | In-line roll former |
Continuous variable lengths | Orbital roll former |
Limited factory space | Compact in-line roll former |
Thick high strength material | Heavy-duty orbital machine |
Frequent product changeovers | Quick-change tooling |
Automated production | Servo drives, auto-gauging, robotic part handling |
Steel Frame Roll Forming Machine Suppliers
There are many roll forming machine manufacturers globally that offer steel frame production lines. The table below outlines some of the major suppliers:
Leading Steel Frame Roll Forming Machine Manufacturers
Company | Location | Machine Types | Max. Speed |
---|---|---|---|
Formtek | USA | In-line, Orbital | 100 m/min |
Samco Machinery | Canada | In-line, Orbital | 80 m/min |
Bradbury Group | UK | In-line | 120 m/min |
Shanghai Rollforming | China | In-line, Orbital | 100 m/min |
Metform | Turkey | In-line, Orbital | 80 m/min |
Kirby Building Systems | USA | In-line | 100 m/min |
BSM | Taiwan | In-line, Orbital | 80 m/min |
Jupiter Rollforming | India | In-line | 60 m/min |
Price Range
Steel frame roll forming machines range from $100,000 to $500,000 depending on speed, size and features. Typical pricing for common configurations:
- Entry-level in-line roll former – $100,000 to $150,000
- High speed in-line roll former – $200,000 to $300,000
- Heavy-duty orbital roll former – $300,000 to $500,000
Second-hand reconditioned machines are available around 40% cheaper.
Leading manufacturers like Formtek, Samco and Shanghai Rollforming offer custom roll forming solutions specific to customer requirements. They also provide line integration, installation services and operator training.
Factors Affecting Steel Frame Roll Forming Machine Cost
- Speed and throughput
- Number of roll stations
- Automation features
- Material thickness capacity
- Made in USA versus imported
- Custom versus standard machine
- Manual versus powered material handling
- New versus used machine
Cost Saving Tips
- Consider reconditioned used equipment to save 40%
- Standard machines cheaper than custom machines
- Imported machines cost 20-30% less than US built
- Only opt for features needed for application
- Manual material handling cheaper than automated
- Get quotes from multiple suppliers to compare pricing
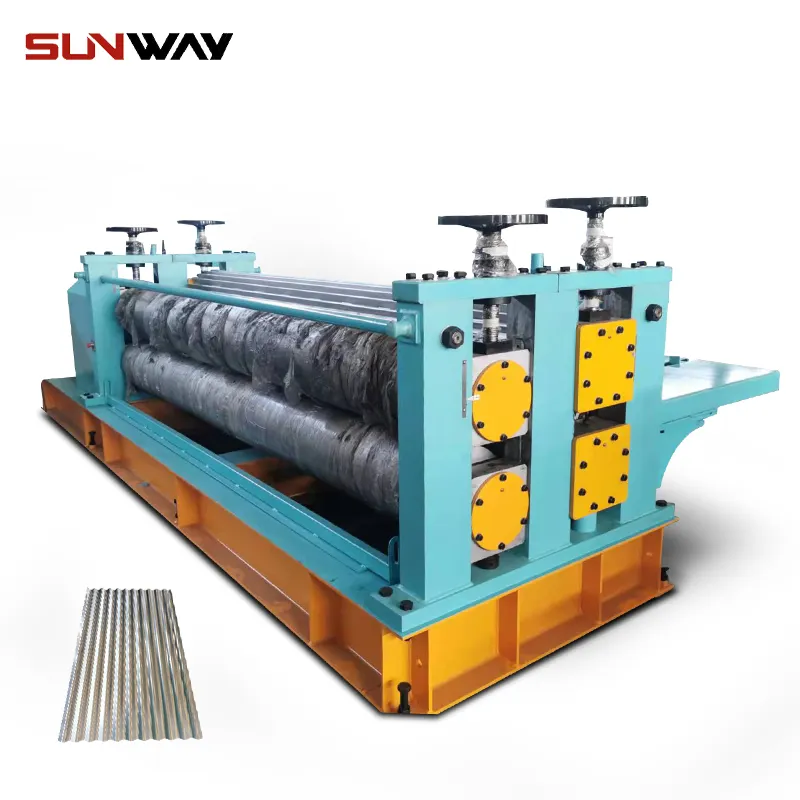
How to Choose a Steel Frame Roll Forming Machine Supplier
Follow these steps when selecting a roll forming machine supplier:
- Evaluate suppliers based on reputation, experience, and proximity
- Check they offer the required machine type and features
- Review case studies and visit facilities if possible
- Get proposals from multiple suppliers for comparison
- Ask about production rate guarantees and tolerances
- Request references from existing customers
- Clarify after-sales service and technical support provided
- Ensure local availability of spare parts and tooling
- Understand payment terms and lead time required
- Negotiate best pricing package based on total value
Reputable manufacturers like Formtek, Samco and Shanghai Rollforming with decades of experience provide the complete solution from design to delivery to meet customers’ roll formed profile requirements. Checking multiple references helps validate quality and reliability.
Roll Forming Machine Operation and Maintenance
Proper operation and preventive maintenance ensures optimum performance and life of a steel frame roll forming system.
Daily Operation Checklist
- Inspect formed parts for defects
- Check roll tool condition and lubrication
- Monitor drive loads and temperature
- Inspect cutting tools for wear
- Ensure guides and guards are in place
- Verify hydraulic fluid levels
- Check conveyor belt condition and tracking
- Clean accumulated metal particles
Preventative Maintenance Schedule
Activity | Frequency |
---|---|
Roll tool inspection | Weekly |
Hydraulic system inspection | Monthly |
Bearing lubrication | Quarterly or 500 hours |
Belt replacement | Annually or per manufacturer |
Roll tool regrind | As needed based on gauge |
Machine calibration | Every 2 years |
A stringent maintenance program as per the equipment supplier’s guidelines ensures optimal performance and minimum downtime. Keep sufficient spare parts stock on hand.
Advantages and Limitations of Roll Forming Process
Advantages
- High production speeds up to 100 m/min
- Continuous production of long profiles
- Accuracy up to +/- 1 mm tolerance
- Repeatability for consistent quality
- Low tooling cost compared to other processes
- Minimal material waste
- Ideal for high strength materials
- Low power consumption
- Simple operating principles
Limitations
- Not suited for short parts below 3 m
- Limit on profile size based on machine capacity
- Sequential operations limit flexibility
- Fixed part cross-section
- Roll tools require periodic replacement
- Loud noise generation requires protection
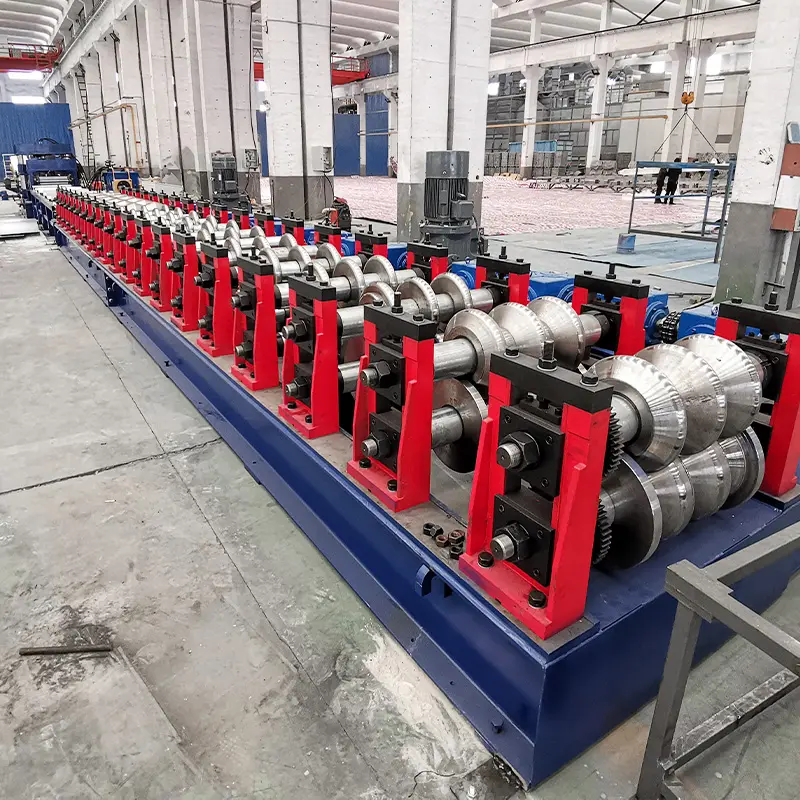
FAQ
Q: What types of steel can be roll formed?
A: Most structural and sheet steel grades can be roll formed including mild steel, high strength steel, stainless steel and aluminum up to 10 mm thickness.
Q: What profile lengths can be produced?
A: In-line roll formers can produce fixed steel frame lengths up to 15 m long. Orbital machines offer continuous lengths with no theoretical limit.
Q: How fast is the roll forming process?
A: Production speeds range from 10 to 100 m/min depending on machine size. Typical speeds are 30-50 m/min.
Q: What tolerances does roll forming achieve?
A: Roll formed steel frame accuracy is typically +/- 1.0 mm over full profile length. Precision of 0.5 mm is possible.
Q: How quickly are roll tools produced?
A: After design approval, roll tools can be manufactured in 2 to 3 weeks for delivery. Quick-change sets allow fast profile changeover.
Q: What expertise is needed to operate a roll former?
A: Roll forming machines are designed for ease of use. Typical operator training time is 1-2 weeks depending on automation level.
Q: What safety measures are required?
A: Roll formers contain many safeguards like barriers, E-stops and interlocks. Users must provide protocols and PPE.
Q: What is the typical return on investment period?
A: Depending on production scale, ROI can be achieved within 1-2 years through efficiency gains versus other processes.
Conclusion
Roll forming provides a high productivity and precision method to produce customized steel frame profiles. In-line roll formers are ideal for short fixed length parts needed in high volumes, while orbital machines allow unlimited profile lengths.
Leading roll forming machine manufacturers offer standard or custom machines from 50-150 m/min with capacities up to 10 mm thickness and 1000 mm width. Roll formed steel frames have dimensional accuracy up to +/- 1.0 mm and provide material savings versus other bending techniques.
Carefully evaluating production volume, product dimensions, line speed, floor space and budget assists in selecting the optimal roll forming solution for a specific steel frame application. Effective maintenance and operation procedures ensure maximum performance. With the right machine and setup, roll forming provides a cost-effective way to produce straight or tapered steel profiles with complex cross-sections.