Shelf keel roll forming machines produce structural metal shelf brackets and supports in various profiles via continuous bending of strip steel feeds into specific angles. This guide provides an overview of configurations, components, capabilities, suppliers, and comparative assessment.
shelf keel roll forming machine Working Principle
Shelf keel roll formers utilize a series of roller dies to incrementally bend fed metal coil stock into bracket shapes:
Process | Continuous bending into progressive die forms by motorized flower rollers |
Metal Strip | Feeds through consecutive roll stations to shape profile |
Die types | Circle rounding, embossing, pre-cutting, punching, etc. |
Bending methods | Rotary bending through sandwiched top and bottom rollers |
Keel cutting | Pneumatic trimming knife slices formed parts at exit |
Typical metals | Hot rolled steel, cold rolled steel, stainless steel |
Synchronizing material feed, roller motions and cutting facilitates profile forming with precision control actuation.
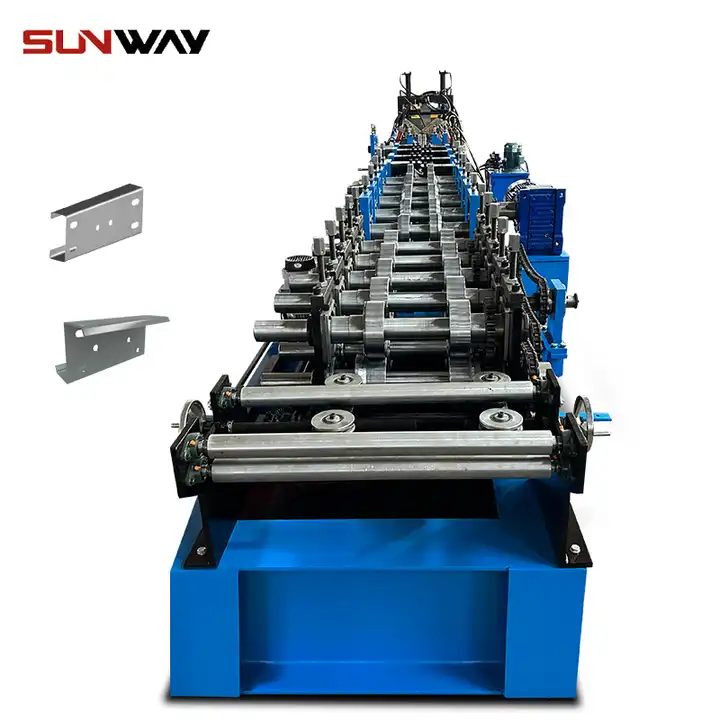
System Equipment
Component | Function |
---|---|
Decoiler | Feeds raw coil stock into line |
Straightener | Corrects initial strip curvature |
Feed table | Controls material speed and tension |
Tooling stations | Impart profile via flower roller dies |
Controls | Automate positioning, feed and cutting |
Hydraulics | Adjust roller pressure during bending |
Exit table | Catches finished parts |
Additional Modules: Hole punching, notching, part embossing, shearing offcut removal.
Production Capabilities
Part width | Up to 80mm for standard machines |
Thickness range | 0.5mm to 3mm metals |
Materials | Hot rolled, cold rolled, galvanized and stainless steels |
Profile types | Hat channel, Z shape, L bend, U channel |
Secondary operations | Hole punching, notching, stamping, beading |
Part length | Adjustable to 2500mm maximum |
System Suppliers
Company | Model Series | Cost Range |
---|---|---|
Formtek | Orion | $100,000-$450,000 |
SIPA | CARL150-300 S | $150,000-$550,000 |
EUROBEND | CRB | $200,000-$650,000 |
Jinhan | Snow Series | $250,000-$750,000 |
Quotes vary based on speed, width capacity, level of automation and secondary processing needs.
-
Vineyard Post Roll Forming Machine
-
Auto Size Changeable Sigma Purlin Roll Forming Machine
-
PV Mounting Bracket C Shape Profile Roll Forming Machine
-
C Z Purlin Channel Cold Roll Forming Machine Full Auto Galvanized Steel Profile
-
PV Mounting Bracket Roll Forming Machine (HAT / Omega Profile)
-
PV Mounting Bracket Z Shape Profile Roll Forming Machine
Operation and Maintenance
Activity | Description | Frequency |
---|---|---|
Decoiler inspections | Check strip alignment and tension | Start of coil |
Bearing lubrication | Grease key bearing points | Monthly |
Hydraulic inspection | Check fluid, cylinders, valves and seals | 6 months |
Tooling inspection | Verify roller dies condition | Yearly |
Control diagnostics | Validate sensors, actuators and sequences | As needed |
Proactive preventative maintenance enhances uptime productivity while minimizing breakdowns. Keep spare key tooling in stock.
Selection Considerations
Factor | Guidelines |
---|---|
Volume throughput | Size appropriately for daily production targets |
Material specification | Accommodate desired metal type, width and thickness |
Profile complexity | Balance secondary operations with changeover time |
Software capabilities | Flexibility for future profile programming |
Frame rigidity | Heavier frames sustain tighter tolerances |
Expandability | Plan for projected volume growth |
Reputation and support | Get references and ensure localized service |
Carefully evaluate specifications against requirements to avoid expensive modifications later on.
Key Takeaways
- Continuous roll forming efficiency ideal for high volume shelf bracket production
- Secondary operations like hole punching facilitate limited profile variation
- Parallel lines recommended to mitigate risk of downtime
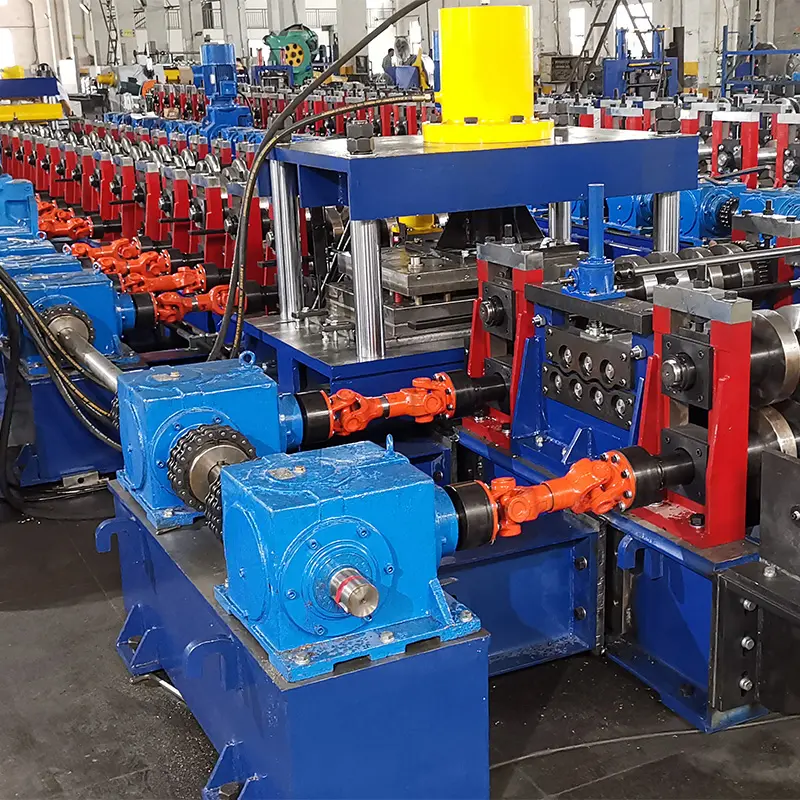
FAQs
Q: What types of steel can be roll formed into shelf brackets?
A: Hot rolled steel, cold rolled steel, galvanized steel and stainless steel are commonly formed into structural shelf keels and brackets.
Q: What tolerances are held on roll formed shelf parts?
A: Shelf keels usually require +/- 0.5mm tolerance including length, width, hole placement and straightness based on machine rigidity, controls capability and wear maintenance.
Q: How are holes and notches created in finished brackets?
A: Modular hole punch and notch cutting stations can integrate into the consecutive roller die forming line stages enabling secondary piercing operations.
Q: Can roll formed shelf brackets be powder coated?
A: Yes, inline powder coating stations or secondary coating lines provide durable decorative and protective finishes to painted to roll formed steel brackets.