Scaffolding plank forming machines create wooden scaffolding planks used for construction purposes and access in construction and infrastructure projects. This equipment rolls forms wooden planks quickly and efficiently, offering advantages over traditional plank production methods.
Overview
Scaffolding plank forming machines take raw wooden boards or timber as input and produce robust finished scaffolding planks through an automated rolling and pressing process. The formed planks have excellent strength properties required for load-bearing scaffolding structures.
These flexible roll forming lines create planks of consistent quality in large volumes. Their high production speed, reliability, and low maintenance needs make them ideal for scaffolding manufacturing units. This guide helps buyers understand this equipment and choose the right model.
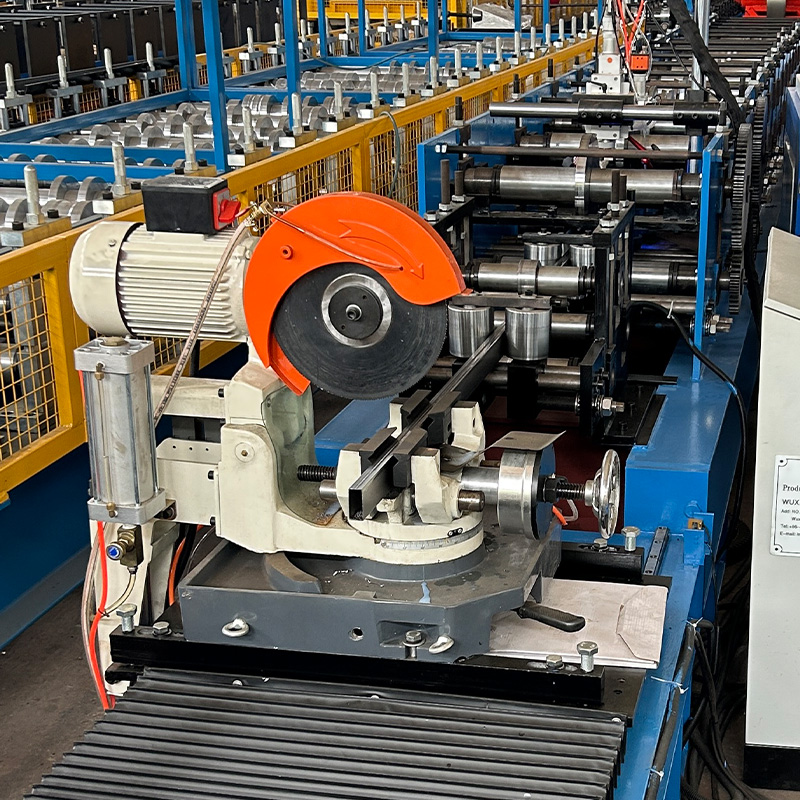
Types of Scaffolding Plank Forming Machines
Machine Type | Description |
---|---|
Manual | Basic manually-operated plank forming presses for small-batch production |
Hydraulic | Feature hydraulic power for forming pressure for high automation |
Automatic | Fully-automated production lines with PLC-based control systems |
Customized | Tailored solutions with varying degrees of automation for specific output requirements |
Working Process
The scaffolding plank forming process has three main steps:
Input Material Loading: Raw wooden boards are fed into the feeder system based on width, thickness, and length parameters
Forming and Pressing: Boards pass through automated pressing rollers that bend and form them into shaped scaffolding planks
Output Plank Handling: Formed scaffolding planks with reinforced edges are cooled, trimmed and collected at the output
Key Features and Customization
Feature | Details |
---|---|
Feeding | Manual loading or automated feeding systems for boards of varying sizes |
Forming Rolls | Interchangeable rolls in various profiles for I-beam, L-beam, T-beam, and custom plank shapes |
Pressing Pressure | Achieved via manual, mechanical, hydraulic or servo-electric power for uniform plank formation |
Trimming | Automated trimming saws for cutting planks to precise lengths |
Conveying | Roller conveyors, chain conveyors to move planks during processing |
Automation Features | Sensor-based systems, PLCs and HMIs to enable automated forming, material handling and quality control |
Buyers Guide – How to Choose the Right Forming Machine
Parameter | Details |
---|---|
Type of Planks | Depends on plank shapes needed – I-beam, rectangular, or custom profiles |
Production Volume | Higher automation for large volumes, manual for lower batches |
Power Options | Manual, hydraulic, servo-electric power based on force needed |
Feeding Method | Automatic or manual material loading systems |
Level of Customization | Standard design or customized features |
Automation Extent | Manual, semi-auto, fully-automatic based on production needs and budgets |
Additional Features | Conveying, stacking, trimming, testing systems to enhance automation |
After-sales Service | Installation, operator training, maintenance and parts supply |
-
Auto Size Changeable Sigma Purlin Roll Forming Machine
-
Auto Size Changeable C Z Purlin Roll Forming Machine
-
Auto Size Changeable Z Purlin Roll Forming Machine
-
Auto Size Changeable C U Purlin Roll Forming Machine
-
C Section Bracing Omega Storage Rack Upright Post Roll Forming Machine
-
Steel Box Plate Making Roll Forming Machine
-
Box Beam Steel Roll Forming Machine For Shelf Column
-
Pallet Racking Step Beam P Beam Roll Forming Machine
-
Warehouse Shelf Upright Roll Forming Machine
Industrial Applications
- Manufacture of scaffolding planks for construction industry
- Infrastructure projects needing temporary access platforms
- Mining platforms, suspended scaffolding, tower cranes in various industries
- Concrete prefab factories, shipbuilding, offshore applications
Suppliers and Price Ranges
Manufacturer | Location | Price Range | Models Available |
---|---|---|---|
Shandong Guangyu Metal Forming Machinery Co. | China | $5000 to $50000 | Manual, hydraulic and fully-automatic lines |
Wuxi Zhenqun Machinery Manufacture Co. | China | $10000 to $100000 | Horizontal and vertical hydraulic plank forming presses |
Mtb Matic | Italy | $50000 to $200000 | High-speed automated production lines |
SAE Systems | USA | $100000 to $500000 | Customized forming solutions |
Note: Indicative price ranges only. Get latest quotes from shortlisted suppliers.
Installation Tips and Precautions
- Carefully transport equipment to avoid damage
- Follow manufacturer’s instructions for installation sequence
- Ensure sufficient space around the machine for safe operation
- Provide strong foundations and anti-vibration pads
- Connect power, utilities and compressed air correctly
Operation, Maintenance and Precautions
- Follow safety procedures – guards, emergency stops, PPE
- Only trained personnel should operate the equipment
- Perform preventive maintenance as per schedule
- Lubricate moving parts, keep press structure rigid
- Ensure interlocks, sensors and controls function properly
Pros and Cons of Scaffolding Plank Forming Machines
Pros | Cons |
---|---|
Fast, efficient production of scaffolding planks | High initial purchase cost of automated lines |
Consistent quality and structural performance | Complex maintenance for some models |
Adaptable to varying production needs | Limitations in plank dimensions for manual presses |
Low manpower requirement for automated lines | Require careful material loading for inline processes |
Compact equipment footprint | Challenging retrofits or upgrades in future |
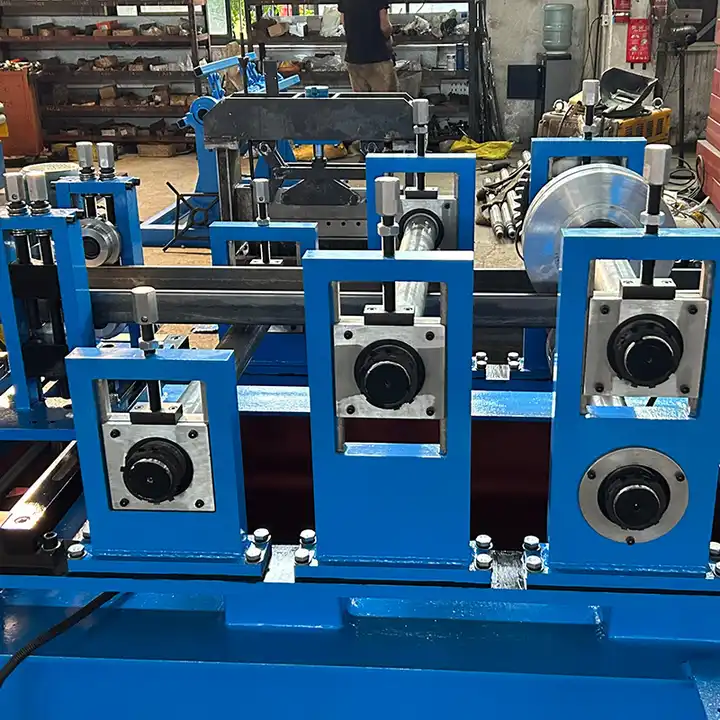
FAQs
Q: What raw materials can be used for scaffolding plank formation?
A: Pine, fir, oak and poplar wood boards meeting minimum strength criteria are typically used based on cost, availability and finished plank properties needed.
Q: What should be the minimum order quantity for buying machines?
A: This varies across suppliers but five to ten machines per order is commonly seen for imported automated lines whereas single unit orders are accepted for manual and hydraulic presses. Local representation also minimizes order volumes.
Q: What level of operator skill is needed for running these machines?
A: Fully-automatic lines require just supervision level skills whereas manual and hydraulic presses need trained operators for core plank forming functions. Semi-automatic systems need operators mainly for feeding stations. In general, scaffolding manufacturers should consider their workforce capabilities and level of automation desired while purchasing forming equipment.
Q: How to lower costs for initial purchase and operation?
A: Starting with basic hydraulic or manual presses allows minimizing initial capital employed while still supporting some automation in the forming process. Production volumes can be initially managed and then automated lines added subsequently once utilization levels justify further investment. Such multi-stage capacity expansion is easier to manage financially for small and medium plank manufacturers.
Q: What service life should be expected from these machines?
A: While the equipment is robustly constructed, 15-20 years of reliable service life can realistically be expected for such capital equipment subject to appropriate installation, operation and preventive maintenance practices. Critical parts may require replacement at intervals – manufacturers’ guidelines should be followed to avoid unplanned downtime which affects production and profits.