Overview
Roof panel roll forming machines are the backbone of modern construction, particularly in the fabrication of metal roofing sheets. These machines transform metal coils into long, uniform panels used in roofing and siding applications. Whether you’re involved in large-scale construction projects or a DIY home renovation, understanding the intricacies of these machines can save time and resources while ensuring superior results.
In this article, we’ll delve into the specifics of roof panel roll forming machines, discussing everything from their types, working processes, key components, and efficiency, to customized parameters, applications, and maintenance. We’ll also compare various models, suppliers, and provide a comprehensive FAQ section to answer common queries.
Understanding Roll Forming Machines
Roll forming is a continuous bending operation in which a long strip of sheet metal, usually coiled steel, is passed through sets of rolls mounted on consecutive stands. Each set performs only an incremental part of the bend until the desired cross-section profile is obtained.
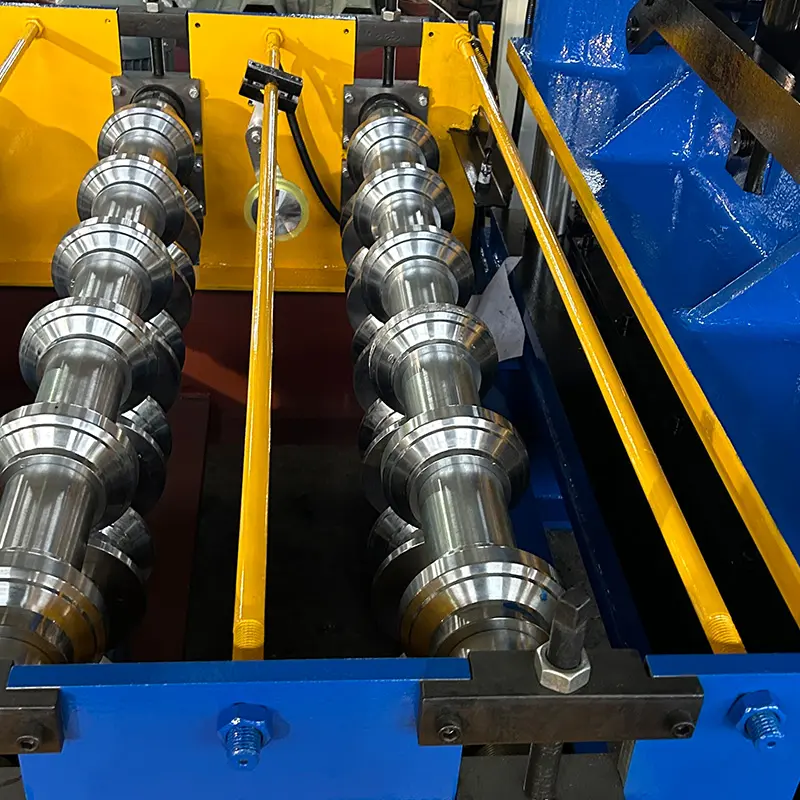
Precision Roll Forming Machine Types
Type | Description |
---|---|
Single Layer Roll Forming Machine | Produces one layer of roofing panels, ideal for small-scale projects. |
Double Layer Roll Forming Machine | Capable of producing two layers simultaneously, increasing efficiency for larger projects. |
Tile Roofing Roll Forming Machine | Specially designed to produce roof tiles, providing aesthetic and functional benefits. |
Corrugated Roof Roll Forming Machine | Creates corrugated panels, offering increased strength and durability for various applications. |
C-Z Purlin Roll Forming Machine | Manufactures C and Z-shaped purlins used in structural frameworks of buildings. |
Standing Seam Roll Forming Machine | Produces standing seam panels, known for their weather-tightness and sleek appearance. |
Floor Decking Roll Forming Machine | Creates panels used in flooring systems, adding strength and stability to structures. |
High-Speed Roll Forming Machine | Designed for high-speed production, significantly reducing manufacturing time. |
Customized Roll Forming Machine | Tailored to specific customer requirements, providing versatile and adaptable production solutions. |
Portable Roll Forming Machine | Mobile and easy to transport, ideal for on-site fabrication. |
Working Process of roof panel roll forming machine
High-speed roll forming machines streamline the manufacturing process by rapidly converting metal coils into finished panels. Here’s a step-by-step breakdown:
- Coil Loading: The metal coil is loaded onto the decoiler, which unwinds the coil and feeds it into the machine.
- Feeding and Guiding: The strip passes through a feeding mechanism that ensures it enters the machine smoothly and is aligned correctly.
- Roll Forming: The strip progresses through multiple sets of rollers, each set incrementally bending the metal until the desired profile is achieved.
- Cutting: Once the panel reaches the required length, an automated cutting system slices it to size.
- Stacking and Packaging: The finished panels are then stacked and packaged for distribution or immediate use.
Key Components and Their Functions
Component | Function |
---|---|
Decoiler | Unwinds the metal coil and feeds it into the machine. |
Feeding Guide | Ensures the metal strip is correctly aligned as it enters the machine. |
Rollers | Incrementally bend the metal strip into the desired profile. |
Cutting System | Automatically cuts the panels to the required length. |
Control System | Manages machine operations, including speed, length, and profile settings. |
Hydraulic System | Powers the cutting mechanism and other hydraulic components. |
Exit Table | Receives the finished panels and facilitates their stacking and packaging. |
-
Standing Seam Roof Panel Curving Machine
-
Barrel Corrugated Roll Forming Machine
-
Highway Guardrail End Terminal Forming Machine
-
Highway U/C Post Roll Forming Machine
-
2 Waves Highway Guardrail Roll Forming Machine
-
3 Waves Highway Guardrail Roll Forming Machine
-
Stand Seaming Roof Panel Roll Forming Machine
-
Downspout Pipe Roll Forming Machine
-
Gutter Roll Forming Machine
Machine Speed and Efficiency
Machine Type | Speed | Efficiency |
---|---|---|
Standard Roll Forming Machine | 15-30 meters per minute | Moderate efficiency suitable for standard production needs. |
High-Speed Roll Forming Machine | 60-120 meters per minute | High efficiency, ideal for large-scale manufacturing with time constraints. |
Customized Roll Forming Machine | Variable | Efficiency tailored to specific production requirements. |
Customized Mechanical Parameters
Parameter | Description |
---|---|
Material Thickness | Range of metal thickness the machine can handle. |
Profile Width | Width of the panels produced. |
Roller Stations | Number of roller stations in the machine, affecting profile complexity. |
Cutting Length | Customizable length settings for different panel sizes. |
Power Requirements | Electrical power specifications needed for operation. |
Applications and Uses
Application Area | Usage |
---|---|
Residential Roofing | Manufacturing of metal roof panels for houses. |
Commercial Roofing | Production of roofing materials for commercial buildings and warehouses. |
Industrial Buildings | Fabrication of durable panels for factories and industrial complexes. |
Agricultural Structures | Creating roofing and siding for barns, sheds, and other farm buildings. |
Infrastructure Projects | Use in bridges, tunnels, and other infrastructure developments. |
Portable Buildings | Panels for modular and portable structures. |
Installation, Operation, and Maintenance
Aspect | Details |
---|---|
Installation | Requires professional setup to ensure alignment and functionality. |
Operation | Operated via a control panel with settings for speed, profile, and cutting length. |
Maintenance | Regular checks and lubrication of moving parts, along with periodic calibration of rollers. |
Suppliers and Price Range Details
Supplier | Price Range |
---|---|
ABC Machinery | $50,000 – $150,000 |
XYZ Industries | $70,000 – $200,000 |
MNO Equipment | $60,000 – $180,000 |
PQR Manufacturing | $55,000 – $160,000 |
STU Tech | $80,000 – $220,000 |
How to Choose a Supplier
Choosing the right supplier is crucial for ensuring the quality and efficiency of your roll forming machine. Here are some factors to consider:
- Reputation and Reviews: Check the supplier’s reputation and customer reviews.
- After-Sales Support: Ensure they provide robust after-sales service and support.
- Customization Options: Look for suppliers who offer customization to meet your specific needs.
- Warranty and Guarantee: Verify the warranty and guarantee terms to protect your investment.
- Price vs. Value: Compare the price against the features and benefits offered.
Comparing Pros and Cons: Advantages and Limitations
Aspect | Advantages | Limitations |
---|---|---|
Single Layer Roll Forming Machine | Simplicity and ease of use. | Lower production capacity. |
Double Layer Roll Forming Machine | Higher efficiency, produces two layers simultaneously. | More complex operation and higher initial cost. |
Tile Roofing Roll Forming Machine | Produces aesthetically pleasing and functional roof tiles. | Specific to tile profiles, less versatile. |
High-Speed Roll Forming Machine | Fast production, ideal for large-scale projects. | Higher cost, requires more maintenance. |
Customized Roll Forming Machine | Tailored to specific requirements, versatile. | Longer lead time and higher cost. |
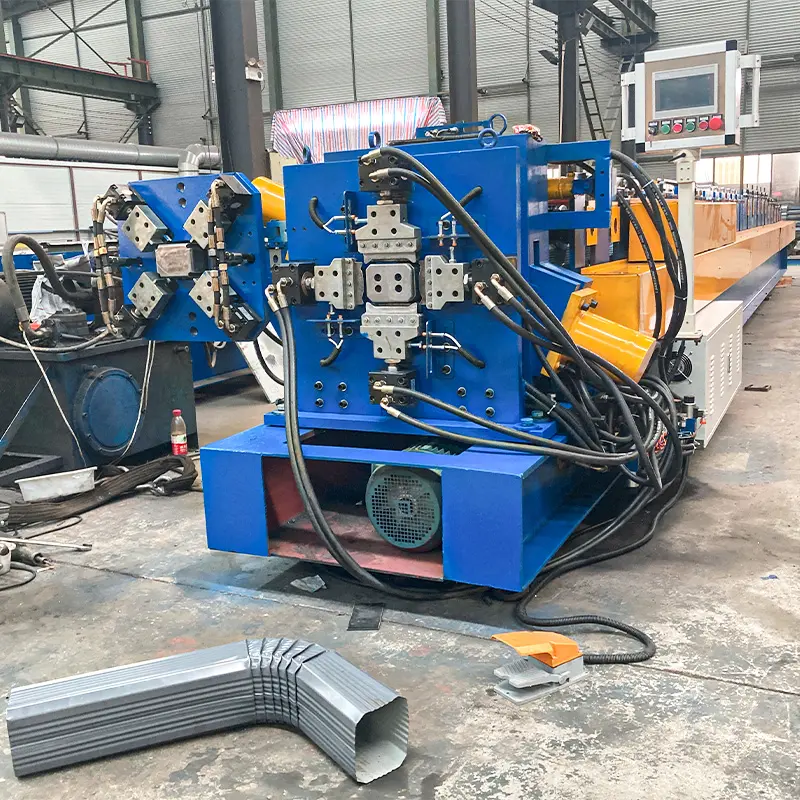
FAQs
Question | Answer |
---|---|
What is a roof panel roll forming machine? | A machine that transforms metal coils into uniform roofing panels through a continuous bending process using roller stations. |
How does a roll forming machine work? | It passes a metal strip through consecutive roller sets, each incrementally bending the metal until the desired profile is achieved. |
What are the key components? | Key components include the decoiler, feeding guide, rollers, cutting system, control system, hydraulic system, and exit table. |
What are the types of roll forming machines? | Types include single layer, double layer, tile roofing, corrugated roofing, C-Z purlin, standing seam, floor decking, high-speed, customized, and portable machines. |
How to maintain a roll forming machine? | Regularly check and lubricate moving parts, calibrate rollers, and ensure proper alignment during operation. |
Conclusion
Understanding roof panel roll forming machines is essential for anyone involved in the construction and manufacturing industries. These machines offer precision, efficiency, and versatility, catering to a wide range of applications from residential to industrial projects.