Introduction
Welcome to a comprehensive guide on roller shutter door roll forming machines. In this article, we will delve into the world of roller shutter doors and explore the crucial role that roll forming machines play in their production. Whether you’re a business owner, an industry enthusiast, or simply curious, join us as we uncover the fascinating intricacies of this technology.
Understanding roller shutter door roll forming machine
Roller shutter doors are a common sight in commercial and industrial settings. These versatile doors offer security, insulation, and space optimization benefits. They consist of horizontal slats that are hinged together, allowing them to roll up neatly into a compact coil when opened. Roller shutter doors find applications in warehouses, garages, storefronts, and more.
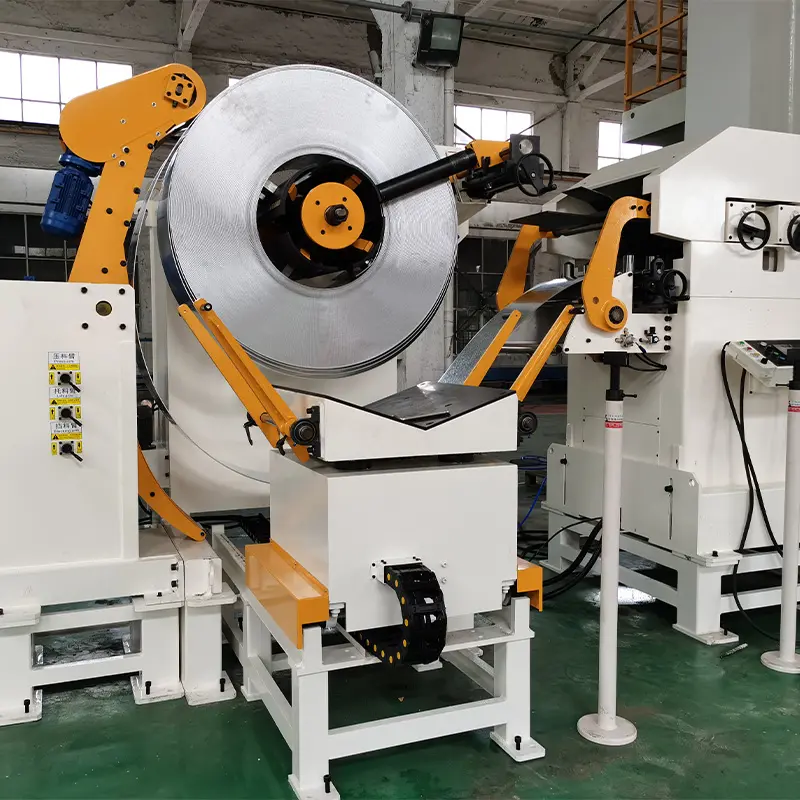
The Role of roller shutter door roll forming machine
- Roll Forming Process: The machine employs a roll forming process, which involves feeding a continuous strip of metal (usually steel or aluminum) through a series of rollers and forming stations. Each station gradually shapes the metal into the desired profile. In the case of roller shutter doors, the roll forming process shapes the metal into the distinctive slat or panel design that is used to create the door curtain.
- Profile Customization: Roller shutter doors come in various sizes, designs, and materials to suit different applications. The roll forming machine can be adjusted to produce different profiles and dimensions based on the specific requirements of the roller shutter door being manufactured. This flexibility is essential to meet the diverse needs of customers.
- Precision and Efficiency: The roll forming machine ensures high precision and consistency in the production process. The carefully calibrated rollers and forming stations maintain uniformity in the shape, size, and dimensions of the slats or panels, resulting in roller shutter doors that operate smoothly and reliably.
- High Production Volume: Roller shutter doors are often used in commercial and industrial buildings, which may require a significant number of doors. The roll forming machine’s automated and continuous production process enables the efficient manufacturing of large quantities of slats or panels in a relatively short period.
- Material Handling and Feeding: The machine features mechanisms for handling and feeding the raw material (metal strip) into the forming process. This automation reduces the need for manual labor and increases overall production efficiency.
- Quality Control: Modern roller shutter door roll forming machines often incorporate quality control measures, such as sensors and monitoring systems, to detect any inconsistencies or defects in the manufactured components. This helps maintain a high standard of product quality.
- Integration with Assembly Process: The components produced by the roll forming machine are then used in the assembly of the complete roller shutter door. The slats or panels are typically connected to each other using hinges or interlocking mechanisms to form the door curtain. The roll forming machine’s accurate production of these components ensures smooth assembly and proper functionality of the final product.
Key Components of a Roller Shutter Door Roll Forming Machine
Roller shutter door roll forming machines consist of several essential components:
- Uncoiler: This component holds the metal coil that will be fed into the machine.
- Feeding System: It transports the metal strip into the forming section.
- Rollers: The heart of the machine, these rollers gradually shape the metal into the desired profile.
- Cutting System: This system cuts the formed profile to the required length.
- Control System: Modern machines feature advanced control panels for automation and customization.
Advantages of Using Roll Forming Machines for Roller Shutter Doors
roller shutter door roll forming machine offer numerous benefits:
- Precision: High-quality and consistent profiles are produced every time.
- Speed: The automated process is much faster compared to manual methods.
- Cost-Efficiency: Reduced labor and material wastage lead to cost savings.
- Versatility: Machines can create a variety of profiles to meet different needs.
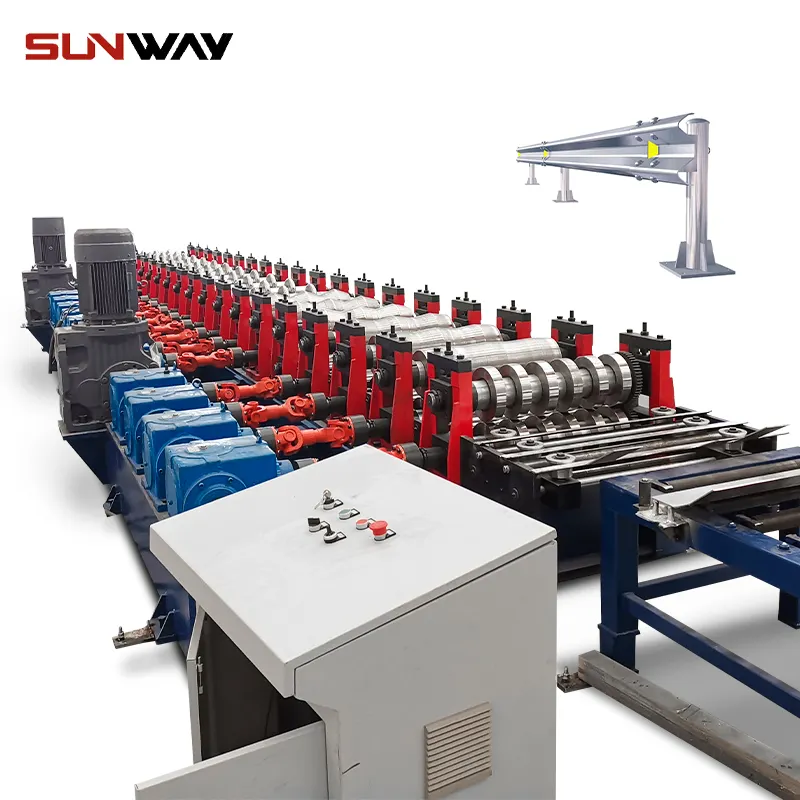
Factors to Consider When Choosing a Roll Forming Machine
When selecting a roll forming machine for roller shutter doors, consider:
- Material Compatibility: Ensure the machine can handle the required metal types and thicknesses.
- Profile Customization: Choose a machine that allows flexibility in creating different door profiles.
- Automation Level: Decide on the desired level of automation and control features.
- Maintenance and Support: Opt for machines backed by reliable technical support.
Maintenance and Care of Roll Forming Machines
- Regular Inspection: Perform routine visual inspections of the machine to identify any signs of wear, damage, or misalignment. This can help catch issues early before they escalate into major problems.
- Lubrication: Keep the machine’s moving parts well lubricated to reduce friction and wear. Refer to the manufacturer’s guidelines for recommended lubricants and lubrication intervals. Over-lubrication should be avoided as it can attract dust and debris.
- Cleaning: Regularly clean the machine, including its rollers, forming stations, and other components. Built-up dirt and debris can affect the quality of the formed profiles and cause damage to the machine over time.
- Tightening Bolts and Fasteners: Check and tighten bolts, nuts, and other fasteners regularly. Vibration and use can cause them to loosen over time, potentially leading to misalignment and other issues.
- Alignment and Calibration: Ensure that the machine’s rollers, forming stations, and other components are properly aligned and calibrated according to the manufacturer’s specifications. Misalignment can result in inconsistent profile shapes and dimensions.
- Wear Parts Replacement: Roll forming machines have wear parts such as rollers, cutters, and guides that need replacement over time. Keep a schedule for replacing these parts to maintain consistent product quality.
- Electrical Components: Inspect electrical components, wiring, and connections for signs of wear, damage, or overheating. Keep electrical components clean and free from dust and debris.
- Safety Measures: Follow all safety protocols and guidelines when performing maintenance tasks. Ensure the machine is properly locked out and de-energized before conducting any maintenance work.
- Operator Training: Ensure that operators are properly trained in the operation and maintenance of the machine. Well-trained operators are more likely to identify potential issues and perform routine maintenance effectively.
- Documentation: Maintain records of maintenance tasks, repairs, and any issues encountered. This documentation can provide valuable insights into the machine’s performance over time and help in diagnosing recurring problems.
- Scheduled Maintenance: Develop a scheduled maintenance plan that includes regular tasks such as lubrication, cleaning, and inspections. Also, plan for more in-depth maintenance at specified intervals based on the manufacturer’s recommendations.
- Professional Support: If you encounter complex issues or problems that require specialized expertise, don’t hesitate to reach out to the manufacturer or a qualified technician for assistance.
- Environment: Keep the machine in a clean and suitable environment, free from excessive dust, humidity, and extreme temperatures. These factors can impact the machine’s performance and longevity.
Innovations in Roller Shutter Door Manufacturing
The industry continues to evolve with innovations such as:
- Smart Technology: Integration of sensors, remote operation, and monitoring.
- Energy Efficiency: Insulated profiles contribute to better thermal performance.
- Enhanced Security: Advanced locking mechanisms and tamper-resistant designs.
Future Trends in Roll Forming Technology
As technology advances, we can expect:
- More Automation: Increasingly automated machines with AI-driven features.
- Sustainable Materials: Adoption of eco-friendly metals and coatings.
- Customization Ease: Effortless switch between various door profiles.
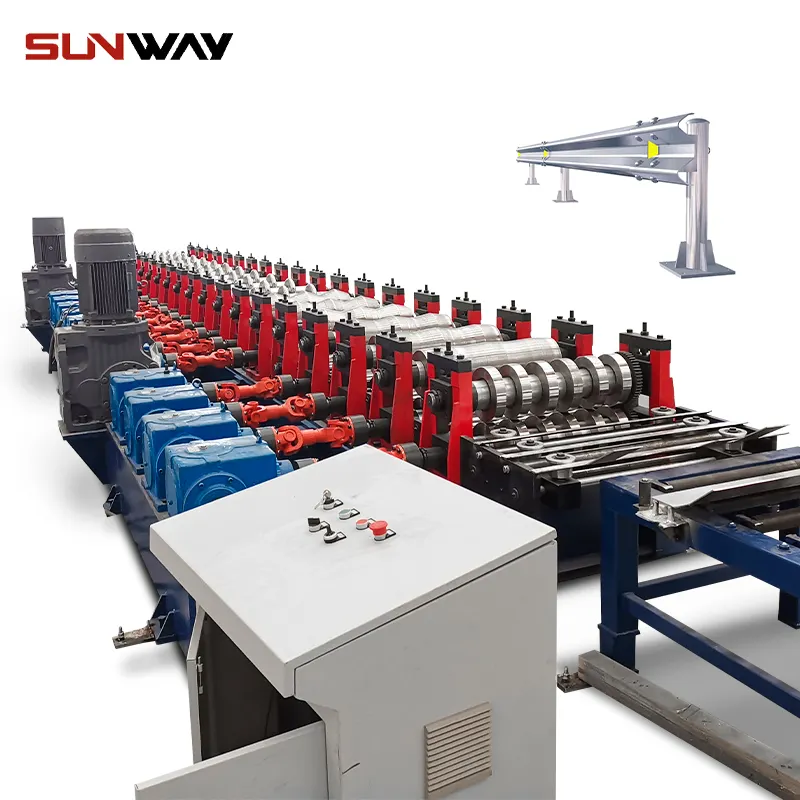
Conclusion
In conclusion, roller shutter door roll forming machines have transformed the way we manufacture these versatile doors. The precision, speed, and cost-efficiency they offer have significantly impacted various industries. As technology continues to advance, we can look forward to even more exciting innovations in the world of roller shutter doors and roll forming machines.
FAQs
What is a roller shutter door roll forming machine?
A roller shutter door roll forming machine is a specialized equipment that shapes metal into the consistent profiles needed for roller shutter doors.
Are roll formed roller shutter doors durable?
Yes, the uniformity achieved through roll forming enhances the durability and longevity of roller shutter doors.
Can I customize the design of roller shutter doors?
Absolutely! Modern roll forming machines allow easy customization of door profiles to suit your requirements.
Are roll forming machines hard to maintain?
With proper care and regular maintenance, roll forming machines can remain in optimal condition for years.
What does the future hold for roll forming technology?
The future promises more automation, sustainable materials, and seamless profile customization in roll forming technology.