roll forming machine is an efficient, high-speed manufacturing process used to produce long sheets of uniform cross-section parts. A coil of sheet metal is fed through a series of roller dies that gradually shape the material into the desired profile. roll forming machine have applications across industries from construction and infrastructure to automotive, aerospace, appliances and more.
Overview of Roll Forming Process
Roll forming machines use a continuous and automated process to manipulate coiled sheet metal into custom parts with repeated bends and forms. The raw material, typically steel, aluminum or other alloy coils, is fed into the rolling mill equipment. The material passes through a line of roller dies set up in sequential stations, each performing incremental shaping operations. The final output is a continuous length part with uniform cross-section along its length.
Benefits of roll forming include:
- High productivity and efficiency
- Consistency and precision in long length parts
- Versatility to form varied, complex profiles
- Lower tooling costs compared to other processes
- Minimal material waste
Roll formed sections find use in panels, enclosure frames, roofing, racking, highway products, furniture, appliance housings, automotive frames and more.
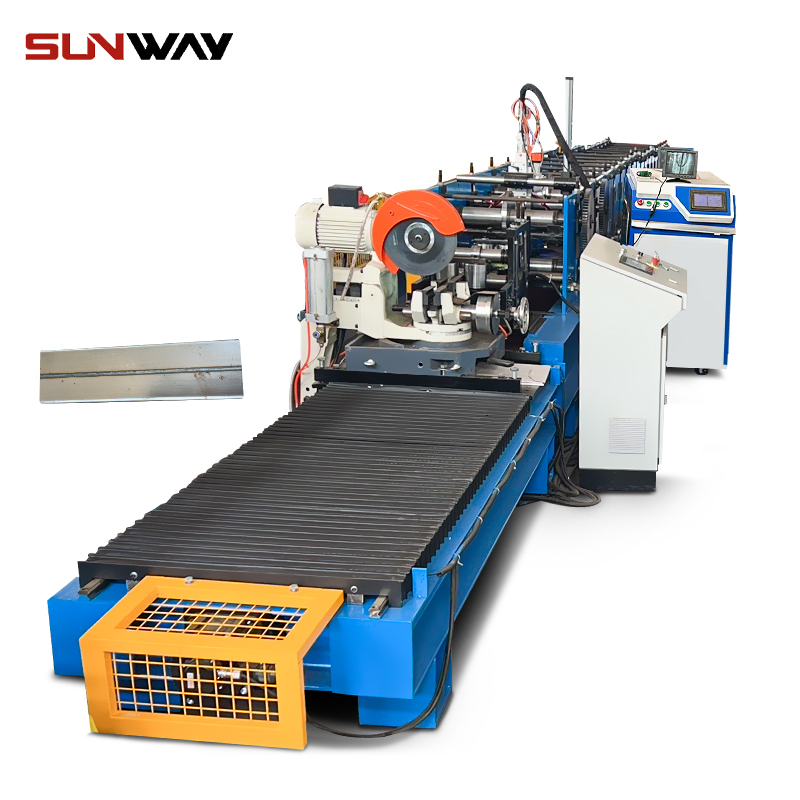
Roll Forming Equipment Types
There are several types of roll forming machine configurations including:
Table 1: Roll forming equipment types
Type | Description |
---|---|
Inline roll forming lines | Parts move inline through different roll station units in a straight line path |
Reversible roll formers | Sheet reversing after each stage, more compact line layout |
Continuous tube mills | Roller dies form flat strip into tubular sections |
Roll bending machines | Simple 2 or 3 roll benders for basic forms |
Portable roll formers | Manual units for onsite small part production |
Working Process of a Roll Forming Line
A typical inline roll forming system has these main components:
- Uncoiler: Decoils sheet metal from a cylindrical coil
- Feeding mechanism: Controls material speed into mill
- Forming sections: Series of roll stands shape material progressively
- Cutter: Shears finished parts to length
- Exit tables: Collects finished product
Additionally, punches, notchers, hole punching units, embossing stations can be integrated for secondary operations.
The forming process starts by loading a metal coil onto an uncoiler reel. The strip gets threaded through an initial set of guide rolls into the first set of forming rolls. As it passes through consecutive stands, the material shape gets further modified incrementally. The last few roller dies fine tune the final dimensional accuracy. Finally a flying cutoff saw shears the sections to desired length stacking them on the exit table.
Material Requirements
Roll formed parts can be produced from:
- Low carbon steel
- Stainless steel
- Aluminum
- Copper
- Brass
Other alloys and metal composites can also be roll formed with appropriate tooling design. Sheet thickness generally ranges from 0.15 mm to about 3 mm for common metals. The maximum coil width capacity for roll forming lines goes up to around 1500 mm.
Forming Capabilities
A wide range of uniform profile geometries can be shaped using rollers including:
- Basic arches, curved forms C-, Z-, hat-, U- sections
- Complex beads, ribs, fluted profiles
- Panels, highway rails, door frames
- Angles, tubes, rectangular ducting
- Open top and closed tubular sections
Advanced 3D roll forming allows asymmetrical forms with varying wall thicknesses along the parts length.
-
Standing Seam Roof Panel Curving Machine
-
Barrel Corrugated Roll Forming Machine
-
Stand Seaming Roof Panel Roll Forming Machine
-
Downspout Pipe Roll Forming Machine
-
Gutter Roll Forming Machine
-
Trapezoidal Panel Roll Forming Machine
-
Ridge Cap Roll Forming Machine
-
Double Layer Panel Roll Forming Machine
-
Roof Tile Panel Roll Forming Machine
Design Considerations
To create an optimal roll formed profile, these aspects need evaluation:
- Product design: Building finite element models informs profile selection considering strength needs and functionality.
- Material type: Metallurgical properties determine forming limits, springback allowances needed.
- Tool design: Roller geometries, clearances, layout based on progressive incremental bending steps.
- Process parameters: Feeding rate, number of passes and stations, separating forces all affect quality.
With tighter tolerances needed, annealing and post processing may also be required. Expert roll forming companies collaborate with customers across design, prototyping, testing, and post-production stages to deliver custom roll formed components.
Key Factors in Roll Forming
Table 2: Factors influencing roll formed part quality
Roll forming factors | Details |
---|---|
Number of forming stations | More roller passes distribute strain over several smaller increments |
Inter-station design | Additional operations like punching, notching, embossing stations |
Roll pass sequence | Efficient bend sequence avoids material cracking and wrinkling |
Roll tooling radii | Tool geometry design based on metal type, thickness, required profile |
Forming analysis | Advanced FEA simulation minimizes physical trial runs |
Suppliers of Roll Forming Equipment
There are roll forming machine manufacturers across geographies including:
Table 3: Major roll forming equipment suppliers
Company | Location |
---|---|
Schwarze-Robitec | USA |
Formtek | USA |
Dreistern | Germany |
E-Tec | Canada |
Samco Machinery | China |
Entry level roll former prices start around $30,000 going up to $500,000 for fully automated high capacity equipment. Custom built production lines with multiple value-added processes, quality checks and part handling automation fetch higher prices.
When evaluating suppliers, productivity needs, line speeds, quick die changeover capability and overall equipment cost play key roles.
Roll Forming Line Installation
Roll forming equipment requires these preparations:
Table 4: Roll former installation needs
Task | Details |
---|---|
Space | Line layout, scrap removal, craning paths |
Power | Sufficient AC supply, backup generators |
Compressed air | For machine automation control valves |
Foundations | Concrete anchor points to secure stands |
Safety | Guarding, access platforms, electrical safety |
The machine bases have to be leveled and positioned so the roller axes are perfectly parallel. This precision alignment is vital for quality roll formed parts.
Operation of Roll Forming Machines
The typical workflow involves:
- Order planning – material procurement, production scheduling
- Coil loading onto uncoiler
- Threading sheet into guide system
- Setting forming parameters – line speed, punches etc. based on job
- Running production batch
- Part cutoff and exit
- Quality checks during operation
- Tool maintenance checks
For quick product changeovers preset recipes automate rapid machine reconfiguration saving time and material when switching jobs.
Maintenance of Roll Forming Equipment
Regular upkeep activities cover:
Table 5: Roll forming equipment maintenance
Task | Frequency | Checks |
---|---|---|
Roller inspection | Monthly | Wear, cracks, grooves |
Bearings | 6 months | Play, smooth rotation |
Belt tension | Quarterly | Adjust if loose |
Lubrication | As needed | Reduce friction at pins, slides |
Hydraulics inspection | Yearly | Leakage, seal condition |
Electricals | Yearly | Contactor operation, wiring check |
This ensures maximum production uptime and product quality consistency.
Choosing a Roll Forming Machine Supplier
Consider these factors when selecting roll forming equipment vendors:
Table 6: Roll former supplier selection criteria
Parameter | Importance |
---|---|
Product range | Standard and custom solutions |
Line speeds offered | Match volumes needed |
Quick die change | For flexible production runs |
Profile complexity ability | As per part designs |
Quality certifications | ISO, CE marked |
Design assistance | For optimal form designs |
Value added processes | Needed secondary operations |
Automation capabilities | For productivity and precision |
After sales service | Installation help, maintenance support |
Operational training | For efficient working |
Reputed manufacturers provide end-to-end support from design, prototyping, to post order assistance.
Pros and Cons of Roll Forming
Table 7: Advantages and limitations of roll forming process
Pros | Cons |
---|---|
Fast production of long, uniform parts | High initial tooling expense |
Consistent precision along part lengths | Limited design flexibility vs other methods |
Lower costs than fabricating each piece | Roll design complexity for asymmetric forms |
Minimal material wastage | Straight line production restricts profile shapes |
Suitable for high quantity production | Regular roller maintenance needed |
Range of section geometries feasible | Skill needed for quality tool design |
If long lengths of the same profile are needed, roll forming excels over other processes due to its productivity and cost benefits.
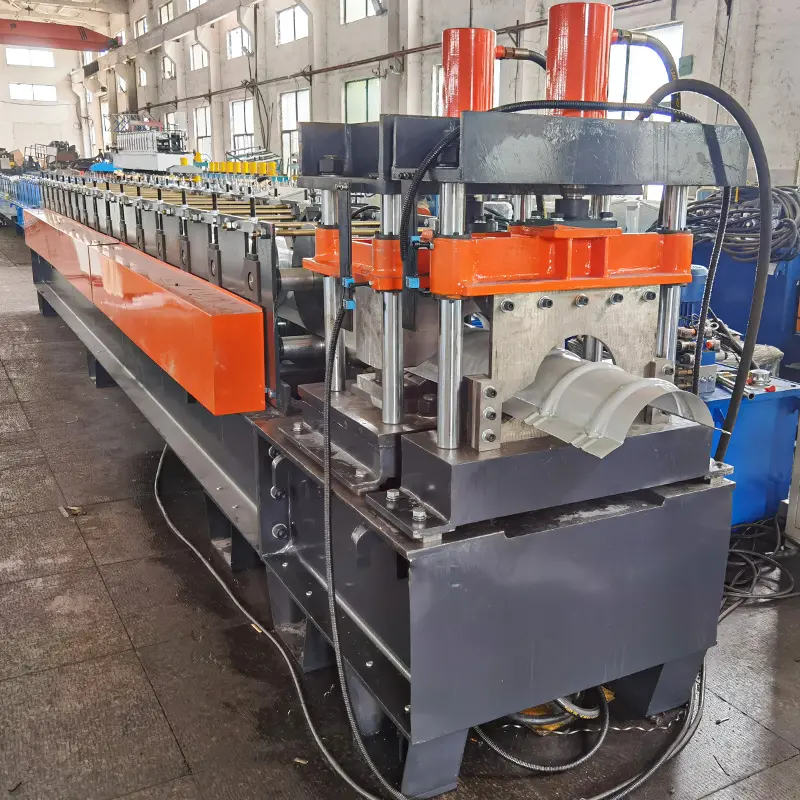
Applications of Roll Formed Sections
Major application areas include:
- Building facades, roofs, highway rails
- Automotive and railway car frames
- HVAC ducting
- Large storage racks, containers
- Electrical, telecom enclosures
- Furniture and shelving
- Agricultural equipment, trailers
- Appliance housings
Essentially any high volume application with linear components of fixed cross-section can employ roll formed parts.
FAQ
Q: What thickness of sheet metal can be roll formed?
A: Standard roll forming lines can produce parts from metal thickness ranging between 0.3mm to about 3mm. Specialized heavy gauge lines go up to 8mm thickness.
Q: What alloys besides steel can be roll formed?
A: Aluminum, copper, brass and other ductile alloys can be roll formed with appropriate roller tooling design. Even flexible composites are possible for certain profiles.
Q: Can a flat sheet be roll formed into a pipe section?
A: Yes, specialized tube rolling mills with bending dies can continuously form flat strips into hollow tubular profiles.
Q: What tolerances are achievable in roll forming?
A: Roll formed parts normally achieve profile dimensional tolerances between +/- 0.5% to +/- 1% depending on metal properties and tooling precision.
Q: Is secondary processing like punching possible during roll forming?
A: Yes, modern roll lines integrate additional in-line processes like piercing, notching, slotting and embossing by incorporating special stations.
Q: How are roll forming machine suppliers compared?
A: Build quality, offered line speeds, level of process automation, tool design expertise, value additions possible, and after sales service are key competitive factors between roll former manufacturers.