A purlin roll forming machine is used to continuously bend and form metal coils into customizable purlin profiles for the construction industry. Purlins provide structural support for roof and wall systems. This guide covers leading purlin roll forming machine manufacturers, working principles, main specifications, installation, operation, maintenance, and selection factors when choosing a supplier.
Overview
Purlin roll forming machines transform flat metal strips from coils into various structural C and Z type purlin shapes through a series of roller dies. Common materials used are galvanized steel, aluminium, and stainless steel. Custom profiles are possible based on design requirements.
Benefits of purlin roll formers include:
- High production efficiency and speeds up to 25 m/min
- Consistent and uniform purlin dimensions and quality
- Customizable to produce specialist purlin sections
- Continuous production directly from coils reduces labour
Main Components:
- Decoiler to hold and steadily feed in metal coil strips
- Guide rollers to smoothly transport strips through machine
- Forming rollers in sections to gradually shape strips into profiles
- Hydraulic system to apply precision forming pressure
- Flying cut-off saw to slice formed profiles into lengths
- Conveyor system and stacker for collection and stacking
Typical Specifications Range:
Parameter | Range |
---|---|
Forming Speed | 8 – 25 m/min |
Power | 5.5 – 18.5 kW |
Forming Force | 25 – 80 kN |
Metal Thickness | 1.5 – 3 mm |
Forming Width | 150 – 200 mm |
Profile Height | 100 – 300 mm |
Applications: Forming various purlin types for roof systems and cladding in industrial and commercial buildings:
- C, Z, Sigma, Omega and custom purlin profiles
- Wall girts and eave struts
- Structural channels, studs, and furring channels
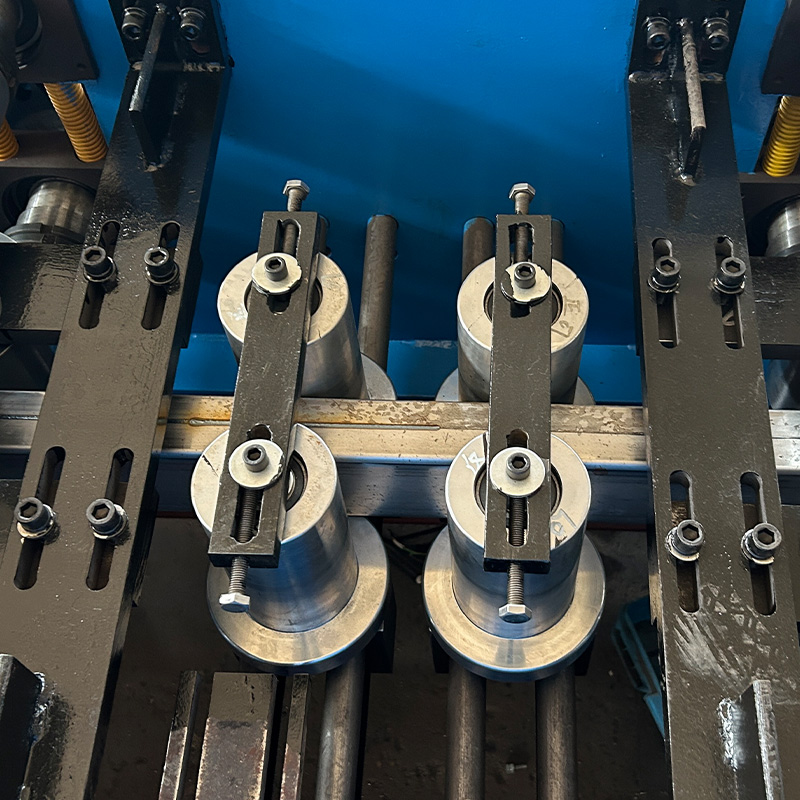
Working Principle
The purlin roll forming process involves:
- Loading metal coil onto powered decoiler
- Feeding strip through sets of roller dies to shape profile
- Progressively bending strip in stages with guide rollers
- Applying hydraulic pressure for precision forming
- Cutting formed sections into custom lengths
- Collecting cut profiles on exit conveyors & stackers
Controlling the feed speed, roller die sets, and cut lengths allows producing the desired purlin profile size. Modern purlin forming lines have automated this sequence for continuous production.
Specifications
Main parameters when selecting a purlin roll former include:
Material Feeding
- Type of metal – galvanized steel, stainless steel etc.
- Thickness range – 1 to 3 mm typically
- Coil size & weight capacity – 30 tons common
Forming Capability
- Profile dimensional range
- C, Z, Sigma and custom profiles
- Forming length per stroke
- Speed: 8 – 25 meters per minute
Design and Tooling
- Roller dies to produce target shape
- Quick die changeovers
- Profile consistency and dimensional tolerance
Slicing Device
- Flying cutoff saw for lengths up to 9 m
- Rotary shear for thickness under 2 mm
- Accuracy of cut: ± 1.5 mm
Customization
- Special forming passes
- Profile height and width
- Custom purlin and girt sections
- Additional punching, notching, hole punching
Suppliers and Price Range
Manufacturer | Location | Price Range |
---|---|---|
zhongli machinery | China | $10,000 – $50,000 |
Kingsland | China | $15,000 – $100,000 |
Mewa Singh | India | $25,000 – $150,000 |
Gasparini | Italy | $100,000 – $250,000 |
Purlin roll former cost depends on:
- Production speed and output
- Forming width
- Type of cutting device
- Level of automation
- Reputation of manufacturer
Higher priced European models focus more on precision and durability versus lower cost Chinese options. Installation and shipping expenses also add to costs.
Installation
Proper installation of a purlin forming machine requires:
- Level concrete foundation to handle machine loads
- Rigid frame support stands for precise alignment
- Securing decoiler unit in position
- Setting up roller box sections in sequence
- Mounting cutoff saw and exit conveyors
- Aligning conveyor system to support and stack finished pieces
- Testing hydraulics, electrics, and safety mechanisms
- Trial running machine without load
- Making adjustments and checking for vibrations
- Forming initial sample pieces and calibrating
Incorrect machine mounting can lead to misalignment and affect formed profile quality and accuracy. Hence precise installation is critical before starting production.
-
Corrugated Panel Roll Forming Machine
-
Light Gauge Steel Roll Forming Machine
-
C Section Bracing Omega Storage Rack Upright Post Roll Forming Machine
-
Steel Box Plate Making Roll Forming Machine
-
Box Beam Steel Roll Forming Machine For Shelf Column
-
Pallet Racking Step Beam P Beam Roll Forming Machine
-
Warehouse Shelf Upright Roll Forming Machine
-
Din Rail Roll Forming Machine
-
Omega Purlin Roll Forming Machine
Operation
Running a purlin roll former involves:
- Loading coil of specified material and thickness onto powered decoiler
- Feeding strip into entry guides aligned to first roller die section
- Setting parameters like feed speed, cutoff length via control panel
- Allowing machine to gradually form profile through roller die stages
- Monitoring cut sections exiting on conveyor system
- Checking if formed profiles meets design dimensions
- Automatically stacking finished pieces or collecting manually
- Ensuring smooth material flow without jams or misalignment
- Getting material tested periodically to validate mechanical properties
2-3 operators are needed to handle loading, running, and unloading. Automated versions require minimal supervision. Regular production sampling checks dimensions and shape accuracy.
Maintenance
Routine purlin machine maintenance includes:
- Cleaning: Remove metal dust and lubricating forming sections
- Inspection: Check rollers, hydraulic systems, sensors
- Lubrication: Oil/grease bearings, gears, chains periodically
- Adjustment: Align any misaligned components
- Part replacement: Fix/replace any damaged or worn parts like bands, gears, sensors etc.
Proper maintenance improves output, prevents breakdowns, and extends machine life. It should be done by qualified technicians as per manufacturer recommended schedule.
How to Choose purlin roll forming machine manufacturer
Key factors when selecting the best supplier:
- Machines meeting design specifications and production targets
- Ability to customize with special forming requirements
- Quick roller die changeovers to save time
- Advanced automatic leveling and feed systems
- Good consistency in formed profiles
- Reasonable accuracy of cut lengths
- High production speeds up to 25 m/min
- Durability and reliability: Bear minimum 3-4 years operation
- Strong R&D design capabilities
- Responsiveness to technical queries
- Experience supplying such machines globally
- Reasonable pricing and delivery times
- Strong after sales service support
Getting vendor references, site visits to inspect existing machines, and getting technical proposals evaluated by experts also helps make the optimum choice.
Pros and Cons
Pros | Cons |
---|---|
High speed continuous production | High initial purchase cost |
Labor cost reduction by 80% | Require extensive maintenance |
Uniform profile dimensions | Fixed tooling restricts profile shapes |
Low power consumption | Not ideal for small batch production |
Easy integration with other processing like punching and notching | Significant installation space needed |
Wide range of possible section sizes and pass variations |
FAQs
Q: What thickness of coils can be formed?
A: Typically 1.5 mm to 3 mm thickness is formed though some machines support up to 4 mm also.
Q: What length of purlins are produced?
A: Standard flying cutoffs slice at up to 9 meter lengths. Cut accuracy is ± 1.5 mm.
Q: What is the maximum strip width supported?
A: Around 200 mm width strips can be formed depending on number of vertical forming roll stations.
Q: What warranty and service support is provided?
A: Most established manufacturers provide 1 year warranty on machines. For after sales, they have dealer networks in local regions for service and maintenance.
Q: What is the production capacity?
A: Output efficiency depends on parameters set but around 300-400 meters per hour is typical. Higher speeds impact quality.