Standing Seam Roof Panel Forming Machine Features:
This Standing seam roof panel forming machine is used to form the pre-painted sheet/GI/GA and aluminum material. It is composed of the uncoiler, guide feeder, roll forming machine, hydraulic cutting machine, PLC control sys tem,hydraulic starion,output tables,auto seamer, and curving machine (Option)
Applications
The finished products are used as the roof and walls of gymnasiums, airports, theatres, factories, warehouses, garages, exhibition centers etc.
Process Flow
Uncoiling — feeding — roll forming — cutting — output — seaming — curving(option)
Machine Configurations
1. Uncoiler |
2. Guide feeder
|
3. roll former |
4. Hydraulic cutting machine
|
5. PLC control system |
6. Hydraulic station
|
7. Output conveyor |
8. Auto seamer
|
9.Curving machine (option) |
Profile Drawings for Reference
Photos for Reference
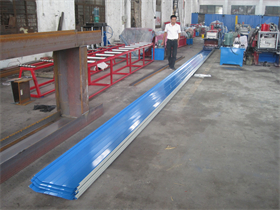
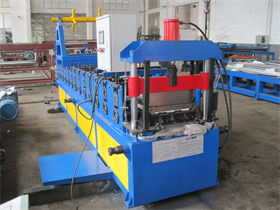
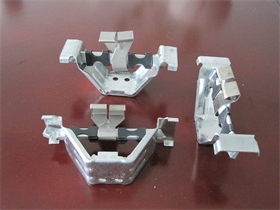
What is standing seam roll forming machine?
A standing seam roll forming machine is a specialized piece of equipment used in the construction industry to manufacture standing seam metal roof panels. Standing seam roofs are popular for their durability, weather resistance, and aesthetic appeal. They consist of vertical metal panels that are connected by interlocking seams, providing a watertight and secure roofing system.
The roll forming machine is designed to form flat metal coils into the desired standing seam profile. It typically consists of a series of rollers and dies that gradually shape the metal as it passes through the machine. The machine operates in a continuous process, where the metal coil is fed into the machine, and the formed panels are cut to the desired length.
The key features of a standing seam roll forming machine include:
- Entry section: This is where the flat metal coil is fed into the machine for processing.
- Rollers and dies: The metal coil passes through a series of rollers and dies that gradually bend and shape the metal into the desired standing seam profile.
- Panel cutting system: Once the panels are formed, the machine incorporates a cutting system to trim them to the desired length.
- Control system: The machine is equipped with a control panel that allows operators to set parameters such as panel dimensions, seam profiles, and cutting lengths.
- Material handling system: The machine may include systems for coil loading and unloading, as well as mechanisms for guiding and supporting the metal during the forming process.
By using a standing seam roll forming machine, roofing manufacturers can produce high-quality, custom-length standing seam panels with consistent dimensions and profiles. This machine significantly reduces labor costs and improves production efficiency compared to traditional manual methods of forming standing seam panels.
how to use standing seam roof panel roll forming machine?
Using a standing seam roof panel roll forming machine typically involves the following steps:
- Set up the machine: Ensure that the machine is properly installed and securely positioned. Make sure all safety precautions are in place, such as emergency stop buttons and safety guards.
- Prepare the metal coil: Load the flat metal coil onto the machine’s coil holder or feeding system. Ensure that the coil is properly aligned and positioned for smooth feeding into the machine.
- Adjust the machine settings: Use the control panel or interface to set the desired parameters for the standing seam panels. This includes specifications such as panel width, seam profile, and cutting length. Follow the manufacturer’s instructions for the specific machine you are using.
- Start the machine: Once the machine is set up and the parameters are adjusted, start the machine’s operation. The metal coil will begin to feed into the machine, and the rollers and dies will gradually form the metal into the standing seam profile.
- Monitor the operation: During the operation, carefully observe the machine’s performance and the quality of the formed panels. Check for any abnormalities or issues that may arise, such as misalignment or deformation of the panels.
- Cut the panels: After the desired length of the standing seam panels is formed, the machine will have a cutting system to trim the panels. Ensure that the cutting mechanism is properly adjusted and aligned to cut the panels accurately and cleanly.
- Collect the finished panels: Once the panels are cut, they will be discharged from the machine. Collect the finished panels and stack them in a safe and organized manner.
- Repeat the process: If there are additional metal coils to be processed, repeat the above steps for each coil. Make sure to monitor the machine’s performance throughout the operation and address any issues promptly.
It’s important to note that the specific steps and procedures may vary depending on the manufacturer and model of the standing seam roll forming machine. Always refer to the machine’s user manual and follow the manufacturer’s instructions for safe and efficient operation. Additionally, proper training and familiarity with the specific machine are essential to ensure optimal results.
application of snap lock standing seam roll forming machine
A snap lock standing seam roll forming machine is specifically designed to manufacture snap lock standing seam roof panels. Snap lock standing seam roofs are a variation of standing seam roofs, where the panels interlock together without the need for separate fasteners or clips. The panels “snap” into place, creating a secure and watertight connection.
The application of a snap lock standing seam roll forming machine is primarily focused on producing snap lock standing seam roof panels for residential, commercial, and industrial buildings. Some key applications of snap lock standing seam roofs include:
- Roofing: Snap lock standing seam roofs are commonly used as a roofing solution for various types of buildings. They provide a sleek and modern appearance and offer excellent weather resistance and durability.
- Residential buildings: Snap lock standing seam roofs are popular for residential properties, including houses, apartments, and condominiums. They can enhance the curb appeal of a home while providing long-lasting protection.
- Commercial and industrial buildings: Many commercial and industrial structures, such as warehouses, factories, and office buildings, opt for snap lock standing seam roofs. These roofs offer exceptional strength and can withstand the rigors of commercial applications.
- Architectural projects: Snap lock standing seam roofs are often chosen for architectural projects where aesthetics play a significant role. Their clean lines and contemporary look can contribute to the overall design and visual appeal of a building.
- Retrofitting: Snap lock standing seam roofs can be used for retrofitting existing buildings. They provide an opportunity to upgrade the roofing system with improved performance and energy efficiency.
The snap lock standing seam roll forming machine enables efficient and precise production of snap lock panels, ensuring consistent quality and dimensions. By utilizing this machine, manufacturers can streamline the manufacturing process and meet the demand for snap lock standing seam roof panels in various construction projects.
Reviews
There are no reviews yet.