Keel/Truss/C/U/Omega/Stud Steel Roll Forming Machine with a small dimension, easy to transport. The speed can be up to 60m/min transmission, so the working will be more stable. We can also supply the customized machines.
Light Keel Corner Bead Making Machine Details
High Speed
Our high speed C/U/Omega stud roll forming machine speed can up to 60m/min. Normally, C//UOmega stud roll forming machine’s speed is around 45m/min
High speed C/U/Omega stud roll forming machine adopts cast steel roller fixer
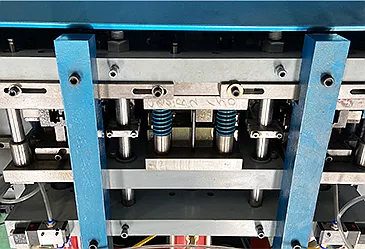
High speed C/U/Omega stud roll forming machine adopts PLC system. Customer can set production quantity, production speed on control cabinet.
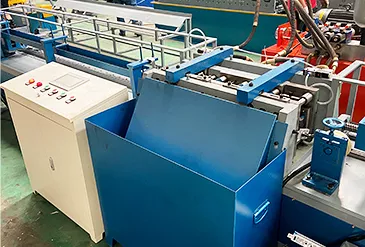
Senior and experienced engineer control the whole process for your customize.
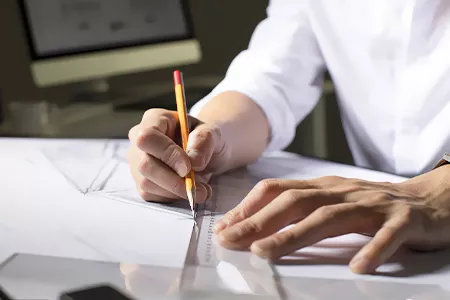
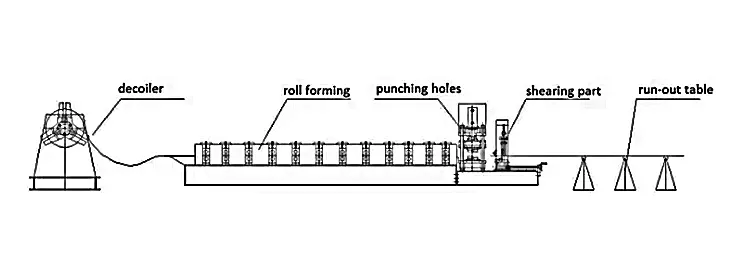
Light Keel Corner Bead Making Machine Parameters
Raw Material | Galvanized Sheet Or PPGI, PPGL |
Thickness Of Sheet (mm) | Customized |
Operation | Fully Automatic |
Transmission | By Chain/Gear |
Roller Material | Cr12 |
Shaft Diameter | 50mm Or As Per Profile |
Roller Station | 10-16 Stations |
Cutter | Hydraulic Servo Cutting With High Speed |
What is light keel roll forming machine?
A light keel roll forming machine is a type of machinery used in the construction industry to produce light steel keel profiles. Light steel keels, also known as light gauge steel frames or metal studs, are thin, lightweight structural components commonly used in non-load-bearing walls, partitions, ceilings, and other interior applications.
The roll forming machine is designed to continuously shape and transform flat metal coils, usually made of galvanized steel or other alloys, into specific cross-sectional profiles. The machine consists of a series of rollers and forming stations that gradually bend and shape the metal strip according to the desired keel profile. These rollers and stations are adjustable to accommodate different profile designs and dimensions.
The process starts with a decoiler that feeds the metal coil into the machine. The coil passes through a series of rollers and forming stations, where it undergoes gradual bending, punching, and cutting operations. The final product is a continuous length of light steel keel with the desired shape and dimensions.
Light keel roll forming machines are typically automated and controlled by computer systems, allowing for precise control of the forming process and high production efficiency. They are capable of producing light steel keels in various sizes and profiles, such as C-shaped studs, U-shaped tracks, and other custom shapes required for specific construction applications.
These machines play a crucial role in the efficient and cost-effective production of light steel keels, offering versatility, accuracy, and rapid production rates. They are widely used in the construction industry for both residential and commercial projects, where lightweight, durable, and easy-to-install interior framing systems are required.
advantage of China light keel roll forming machine
China has become a prominent manufacturer and exporter of light keel roll forming machines. Some advantages of China-made light keel roll forming machines include:
- Cost-effectiveness: China is known for its competitive manufacturing costs, resulting in more affordable prices for light keel roll forming machines compared to machines produced in other countries. This affordability makes Chinese machines an attractive option for businesses looking to invest in such equipment.
- Quality and reliability: Chinese manufacturers have significantly improved the quality and reliability of their products over the years. Many Chinese light keel roll forming machines now meet international quality standards and undergo rigorous testing to ensure their performance and durability.
- Technological advancements: Chinese manufacturers have embraced technological advancements in the field of roll forming machinery. They incorporate modern technologies, such as computerized control systems, servo motors, and advanced tooling, to enhance the precision, speed, and efficiency of their machines.
- Customization options: Chinese manufacturers often offer a wide range of customization options for light keel roll forming machines. This allows buyers to specify their desired features, dimensions, and profiles to meet their unique production requirements.
- Quick delivery times: With a well-established manufacturing infrastructure, Chinese suppliers can often provide shorter lead times and quicker delivery of light keel roll forming machines compared to manufacturers in other regions.
- After-sales support: Chinese manufacturers increasingly focus on providing comprehensive after-sales support to their customers. This includes technical assistance, spare parts availability, and maintenance services to ensure smooth machine operation and minimize downtime.
- Market experience: China has a long history of manufacturing roll forming machines, including light keel roll forming machines. Chinese manufacturers have accumulated extensive market experience and expertise, which allows them to continuously improve their products and cater to the specific needs of customers worldwide.
It’s important to note that while Chinese light keel roll forming machines offer several advantages, it’s essential to conduct thorough research, review customer feedback, and evaluate the reputation and credentials of specific manufacturers to ensure the desired quality and reliability of the machine.
function of light steel keel roll forming machine
The light steel keel roll forming machine serves several important functions in the production process of light steel keels. Here are the key functions of the machine:
- Material Feeding: The roll forming machine features a decoiler that holds and feeds the metal coil into the machine. It ensures a continuous supply of the flat metal strip, which is the raw material for producing light steel keels.
- Roll Forming: The primary function of the machine is to transform the flat metal strip into the desired cross-sectional shape of the light steel keel. This is achieved through a series of rollers and forming stations along the machine’s length. The rollers gradually bend and shape the metal strip according to the predetermined profile design.
- Profile Shaping: The machine’s rollers and forming stations are adjustable to accommodate different profile designs and dimensions. By configuring the positions and dimensions of the rollers, the machine can produce various types of light steel keels, such as C-shaped studs, U-shaped tracks, L-shaped angles, and other custom profiles.
- Punching and Cutting: Depending on the specific requirements of the light steel keels, the roll forming machine may include additional stations for punching holes or slots along the length of the profile. These holes or slots serve various purposes, such as facilitating wiring, plumbing, or attaching other components. The machine may also incorporate a cutting mechanism to shear the light steel keels into the desired lengths.
- Control and Automation: Modern light steel keel roll forming machines often feature computerized control systems and automation technologies. These systems allow for precise control of the machine’s operation, including speed, roller adjustments, and synchronization of various stations. The automation streamlines the production process, improves accuracy, and reduces manual labor.
- High-Speed Production: Light steel keel roll forming machines are designed for high-speed production, enabling efficient and cost-effective manufacturing. The machines can produce light steel keels at a rapid rate, ensuring a steady supply for construction projects.
- Customization and Flexibility: The roll forming machine provides flexibility in terms of customization and adaptability to different profile designs and dimensions. Manufacturers can adjust the machine settings and tooling to meet specific customer requirements, allowing for a wide range of light steel keel options.
By performing these functions, the light steel keel roll forming machine plays a crucial role in the efficient and precise production of light steel keels, which are essential components for interior framing in the construction industry.