Overview
Precision roll forming is a crucial manufacturing process used to create precise, consistent, and high-quality metal components. It involves the continuous bending of a long strip of sheet metal (typically coiled steel) into a desired cross-section. This method is renowned for its efficiency, versatility, and ability to produce complex shapes with tight tolerances.
In this comprehensive guide, we will delve into the specifics of precision roll forming machines, explore various models, understand the working process, and provide detailed comparisons to help you choose the best machine for your needs. We’ll also cover installation, operation, maintenance, and discuss the best suppliers and price ranges. Let’s get started!
What is a Precision Roll Forming Machine?
A precision roll forming machine is a specialized piece of equipment used to shape metal strips into specific profiles through a series of carefully designed rollers. These machines are essential in producing consistent and accurate metal parts used in various industries, including automotive, construction, aerospace, and more.
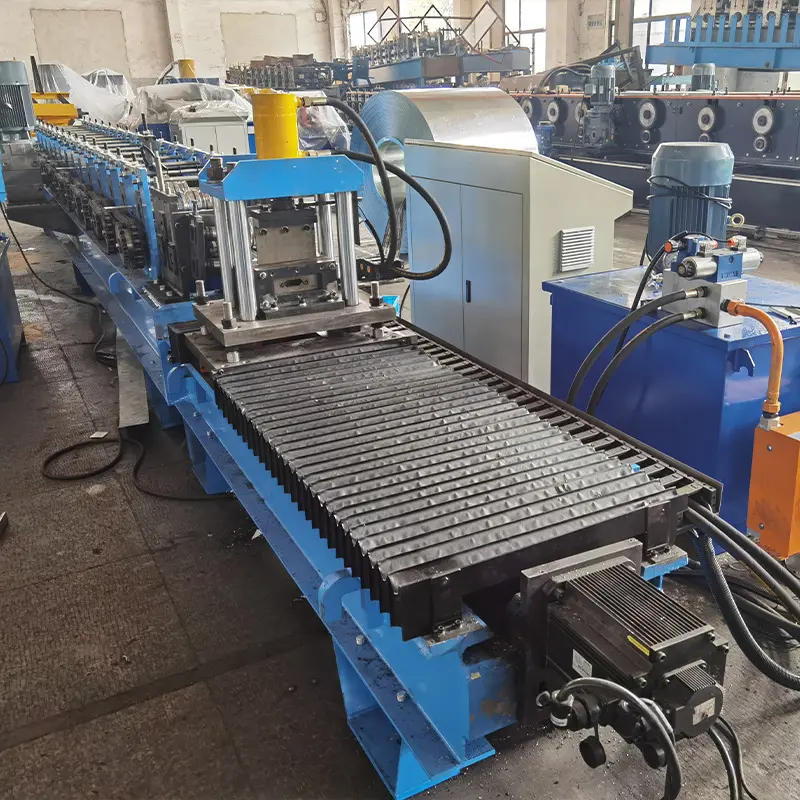
Types of Precision Roll Forming Machines
There are several types of precision roll forming machines, each designed to cater to different manufacturing needs. Here’s a detailed look at some popular models:
Model | Description |
---|---|
Bradbury QTR-Plus | Known for its quick tool change feature, enabling rapid profile adjustments. Ideal for high-mix, low-volume production. |
Dahlstrom 801 Series | Offers precision forming with a robust design, suitable for heavy-duty applications. Comes with advanced control systems for enhanced accuracy. |
Samco Machinery Z-Purlin | Specifically designed for producing Z-shaped purlins used in construction. Features adjustable rollers for various sizes. |
Yoder M-Series | Versatile and modular design, allowing for customization based on specific production requirements. Highly efficient for producing complex profiles. |
ASC Standard-Duty RF | Ideal for standard duty applications, this machine provides excellent precision and reliability. Equipped with user-friendly interfaces for easy operation. |
Hayes International SR | High-speed roll forming machine with advanced safety features. Perfect for large-scale production runs requiring consistent quality. |
GASPARINI METAL ROLL 22 | Known for its energy efficiency and precision, this machine is designed for high-volume production with minimal waste. |
Formtek B&K Series | Offers exceptional precision and repeatability, suitable for manufacturing complex profiles with tight tolerances. |
Roll-Kraft Custom Roll Form | Provides custom roll forming solutions tailored to specific industry needs. Known for high accuracy and durability. |
Tishken 50 Roll Form Line | A high-capacity machine designed for heavy-duty applications, featuring advanced control systems for precise forming and minimal downtime. |
Working Process of High-Speed Roll Forming Machines
The roll forming process involves several key steps to transform a flat metal strip into a desired profile:
- Material Feeding: The metal strip, usually supplied in coils, is fed into the roll forming machine.
- Roll Forming: The strip passes through a series of rollers that gradually shape the metal into the desired profile. Each set of rollers performs a specific bend or shape, ensuring precision and consistency.
- Cutting: After the metal strip is formed, it is cut to the required length using either a flying cutoff saw or a post-cut die.
- Quality Control: The final products are inspected to ensure they meet the required specifications and tolerances.
Key Components, Machine Speed, Efficiency, and Customization
To understand what makes precision roll forming machines efficient and customizable, let’s take a look at their key components and features:
Component | Function |
---|---|
Uncoiler | Holds and feeds the metal coil into the machine. |
Roll Stands | Houses the rollers that shape the metal strip. |
Rollers | Sequentially shape the metal into the desired profile. |
Cutoff Unit | Cuts the formed metal strip to the specified length. |
Control System | Manages the machine’s operations, ensuring precision and efficiency. |
Hydraulic/Electric System | Powers the machine, enabling smooth and efficient operation. |
Safety Guards | Ensures the safety of operators by protecting them from moving parts. |
-
Rolling Shutter Slat Roll Forming Machine
-
Auto Size Changeable Sigma Purlin Roll Forming Machine
-
Auto Size Changeable C Z Purlin Roll Forming Machine
-
Auto Size Changeable Z Purlin Roll Forming Machine
-
Auto Size Changeable C U Purlin Roll Forming Machine
-
C Section Bracing Omega Storage Rack Upright Post Roll Forming Machine
-
Steel Box Plate Making Roll Forming Machine
-
Box Beam Steel Roll Forming Machine For Shelf Column
-
Pallet Racking Step Beam P Beam Roll Forming Machine
Applications and Uses
Precision roll forming machines are used in various industries due to their ability to produce high-quality metal profiles. Here are some common applications:
Industry | Application |
---|---|
Automotive | Manufacturing body panels, chassis components, and structural parts. |
Construction | Producing roofing sheets, wall panels, and structural beams. |
Aerospace | Creating lightweight yet strong components for aircraft. |
Furniture | Forming metal frames and components for office and home furniture. |
Electrical | Manufacturing cable trays, enclosures, and conduits. |
Solar Energy | Producing mounting systems and structural components for solar panels. |
Installation, Operation, and Maintenance
Proper installation, operation, and maintenance are crucial for the efficient functioning of precision roll forming machines. Here’s a guide to help you through these processes:
Aspect | Details |
---|---|
Installation | Ensure the machine is set up on a stable surface, with adequate space for material feeding and product output. |
Operation | Operators should be trained to use the control system and safety features. Regular checks on roller alignment are necessary. |
Maintenance | Regular lubrication of moving parts, inspection for wear and tear, and timely replacement of worn-out components. Ensure the control system is updated. |
Suppliers and Price Range Details
When selecting a precision roll forming machine, it’s important to consider various suppliers and their price ranges. Here’s a comparison of some popular suppliers:
Supplier | Price Range | Special Features |
---|---|---|
Bradbury Group | $50,000 – $500,000 | Offers robust machines with quick tool change capabilities. |
Samco Machinery | $75,000 – $450,000 | Known for customizable machines and excellent customer support. |
Yoder | $100,000 – $600,000 | Provides modular designs with high efficiency and precision. |
ASC Machine Tools | $60,000 – $400,000 | Specializes in user-friendly interfaces and reliable performance. |
Hayes International | $80,000 – $550,000 | Features advanced safety mechanisms and high-speed operation. |
GASPARINI | $90,000 – $700,000 | Renowned for energy-efficient machines with minimal waste production. |
Roll-Kraft | Custom Pricing | Tailored solutions to meet specific industry needs with high accuracy. |
Tishken | $110,000 – $750,000 | High-capacity machines designed for heavy-duty applications with minimal downtime. |
How to Choose the Right Supplier
Choosing the right supplier for your precision roll forming machine is crucial. Here’s a guide to help you make an informed decision:
Factor | Considerations |
---|---|
Reputation | Research the supplier’s reputation in the industry through reviews, testimonials, and case studies. |
Experience | Consider suppliers with extensive experience in manufacturing precision roll forming machines. |
Customization Options | Look for suppliers who offer customization to meet your specific production requirements. |
After-Sales Support | Ensure the supplier provides comprehensive after-sales support, including training, maintenance, and spare parts. |
Price vs. Value | Compare the price range with the features and capabilities offered to ensure you get the best value for your investment. |
Comparing Pros and Cons: Advantages and Limitations
It’s important to weigh the pros and cons of using precision roll forming machines to understand their benefits and limitations.
Aspect | Advantages | Limitations |
---|---|---|
Precision | High accuracy in producing complex profiles with tight tolerances. | Initial setup and calibration can be time-consuming. |
Efficiency | Continuous operation ensures high productivity and minimal material waste. | Requires regular maintenance to ensure optimal performance. |
Versatility | Capable of forming various shapes and sizes to meet diverse industry needs. | Customization can increase the cost of the machine. |
Cost-Effectiveness | Reduces labor costs due to automation and efficiency. | Higher initial investment compared to simpler metal forming methods. |
Quality Control | Consistent production quality, reducing the likelihood of defects. | Dependence on skilled operators and proper training for maintaining quality standards. |
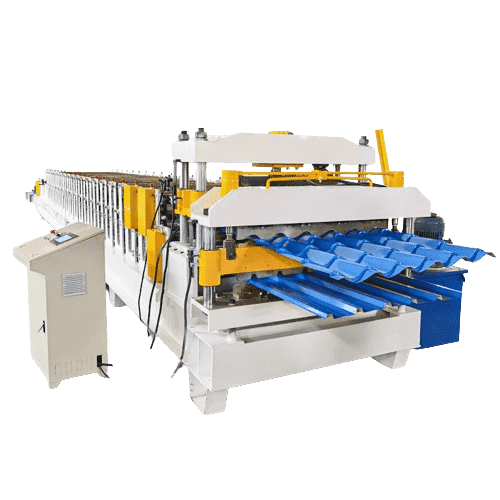
FAQs
What materials can be processed with precision roll forming machines?
include steel, aluminum, copper, and other metals with sufficient ductility to be formed without cracking or breaking.
How long does it take to set up a roll forming machine
Setup time can vary depending on the complexity of the machine and the profile being produced, but it typically ranges from a few hours to a full day.
Can these machines produce custom profiles?
Yes, precision roll forming machines can be customized to produce a wide range of profiles, from simple shapes to highly complex geometries.
What is the typical lifespan of a roll forming machine?
With proper maintenance, a precision roll forming machine can last several decades, making it a long-term investment.
How does roll forming compare to other metal forming methods?
Roll forming offers higher efficiency, better precision, and lower material waste compared to other methods like stamping or extrusion, but it may require higher initial investment.
Conclusion
Precision roll forming machines are indispensable in modern manufacturing, offering unparalleled accuracy, efficiency, and versatility. Whether you’re in automotive, construction, aerospace, or any other industry requiring precise metal components, these machines can significantly enhance your production capabilities. By understanding the various models, their working processes, key components, and the considerations for choosing the right supplier, you can make an informed decision that best suits your needs. Invest in the right precision roll forming machine and take your manufacturing process to the next level.