A perforated cable tray roll forming machine is an essential equipment for manufacturers of cable trays used to support and protect electric cables, wires and piping in various industrial setups. This guide provides a comprehensive overview of perforated cable tray roll forming machine technology, working principles, design considerations, capabilities, suppliers, installation and maintenance.
Overview of Perforated Cable Tray Roll Forming Machine
A perforated cable tray roll forming machine uses a series of sequential roller dies and bending procedures to continuously form metal coil strips into perforated cable tray frames with customized shapes. Key highlights:
- Equipments for high volume production of cable trays up to 12 meters in length
- Forming speed up to 25 m/min with servo electric or hydraulic drive units
- Automated control of parameters through PLC and HMI touchscreens
- Roller dies customized for required cable tray dimensions and perforation patterns
- Additional punching, cutting and bending units for fabrication of accessories
- Powder coating lines and automated packaging integrated for complete production
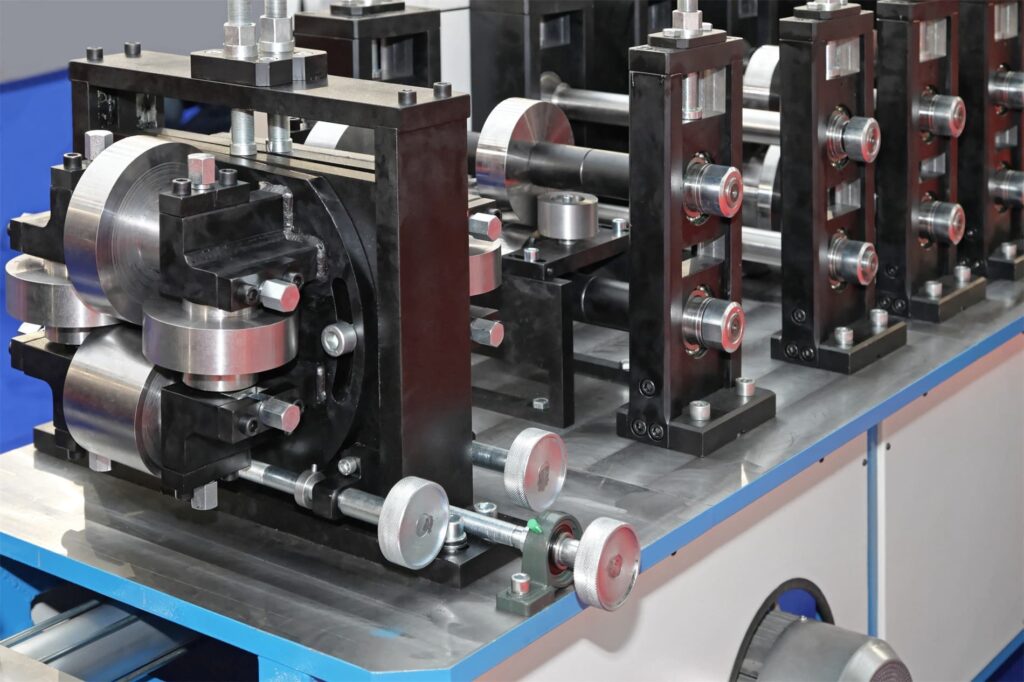
Perforated Cable Tray Roll Forming Machine Types
There are two primary classifications of perforated cable tray manufacturing lines:
Table 1: Perforated Cable Tray Roll Forming Machine Types
Type | Description |
---|---|
Ladder Type | Used for making standard ladder style cable trays with two side rails and transverse round rungs welded at regular spacing |
C & Z Purlin Type | Used for making cable trays with C or Z shaped purlin rails which connect the top and bottom rails for rigidity |
Roll formed cable trays provide an economical and customizable solution for varied cable management requirements in diverse industries.
Working Principle of Perforated Cable Tray Roll Forming Machine
The perforated cable tray profiles are created by feeding raw metal strips through a series of roller dies than bend and form the strips into the final tray shape with punched holes.
Figure 1: Working principle diagram of perforated cable tray roll forming machine
The key processes involved are:
- Decoiling – Feed metal coil loaded on a decoiler is straightened using rollers
- Feeding – Feed rollers equipped with servo motor consistently feeds the strip
- Punching – Initial punching station punches the strip for transverse slots
- Forming -successive Forming stations bend the strip to the final tray shape
- Cutting – Cutting station with rotating blades cuts formed trays to length
- Counting – Precision counting device to count cut lengths
The forming stations apply pressure using pyramid type rollers to bend the strip gradually without cracks through 8-12 progressive stations.
Advanced perforated cable tray roll forming machines include automatic oiling, edge milling, corner notching, accessories punching and inserting, robotic welding, and automated packing systems.
Roll Forming Process Parameters
The quality of finished cable trays and production efficiency depends on optimizing various interdependent parameters in the roll forming process:
Table 2: Roll Forming Process Parameters
Parameter | Role | Guidelines |
---|---|---|
Forming Speed | Production rate | 8-25 m/min based on thickness |
Material Thickness | Strength and load capacity | 1-3 mm thickness sheets |
Number of Stations | Forming quality | 8-12 stations needed for gradual bending without cracks |
Pre-punching | Avoid thinning during forming | 30-50% punching done before forming |
Roller Dimension | Profile dimensional accuracy | Precisely machined pyramid rollers |
Lubrication | Reduce friction; avoid wear and tear | Automated oiling at forming and cutting sections |
The machine is equipped with an HMI panel to control these parameters in real time for optimized performance.
Perforated Cable Tray Roll Forming Machine Design
Cable tray specifications regarding dimensions, perforation patterns, accessories, strength and load ratings are used to design customized roller dies and punches to manufacture the profiles.
Figure 2: Key design parameters for manufacturing perforated cable trays
Considering international standards regarding materials, working load limits, fire rating and offshore applications ensures the roll formed trays meet regulatory needs.
Materials for Cable Trays
Mild steel and stainless steel coils are commonly used materials for roll forming perforated cable trays:
Table 3: Cable Tray Materials
Material | Features | Applications |
---|---|---|
Mild Steel | Low cost; High strength | Indoor dry areas |
Stainless Steel | Corrosion resistance | Outdoor areas; Coastal regions |
Aluminum | Lightweight | Weight reduction needed |
Galvanized or powder coated strips provide additional anti-corrosion protection.
-
Rolling Shutter Slat Roll Forming Machine
-
Auto Size Changeable Sigma Purlin Roll Forming Machine
-
Auto Size Changeable C Z Purlin Roll Forming Machine
-
Auto Size Changeable Z Purlin Roll Forming Machine
-
Auto Size Changeable C U Purlin Roll Forming Machine
-
Light Keel Wall Angle Roll Forming Machine Protector Corners Wall Angle Forming Machine
-
Light Keel Corner Bead Making Machine V Keel Angle Iron Roll Forming Machine
-
Full Automatic C Z Purlin Machine Steel Metal Former Frame & Purlin Machines
-
Fully Automatic Hydraulic Easy Operation 80-300 Adjustable C Purlin Making Machine Roll Forming Machinery
Perforation Patterns
Various perforation shapes, sizes and open areas ranging from 30-60% are used in cable trays for ventilation and easy mounting of accessories.
Oval, round and square holes with diagonal slots and ladder designs provide optimal cable bearing surface.
Accessories and Customizations
- Foldable junction boxes
- Radius drops
- Cable entry boxes
- Mounting brackets
- Support bolts and nuts
- Side coupler plates
- Earthing links
Are roll formed or fabricated using separate punching and bending machines integrated in the production line.
Standards
The design, load capacity and fire ratings of cable trays must comply with national and international standards:
- IEC 61537 Cable tray systems and cable ladder systems
- NEMA VE-2 Cable Tray Installation Guidelines
- AS/NZS 3013 Electrical installations – Classification of the fire and mechanical performance of wiring system elements
Perforated Cable Tray Roll Forming Machine Capabilities
Modern perforated cable tray manufacturing lines offer extensive customization and automation capabilities:
Table 4: Perforated Cable Tray Machine Capabilities
Feature | Role | Parameters |
---|---|---|
Forming Speed | Production volume | Up to 25 meters per minute |
Length Capacity | Minimum order quantities | Up to 12 meter profiles |
Thickness Capacity | Strength and load capacity | 1-3 mm thickness |
Hole Punching | Ventilation; Accessory mounting | 30-60% perforation |
Profile Options | Dimensions | 50-600 mm widths available |
Auto Tool Change | Quick changeovers | 10-20 minute roller and punch change |
Online Radius Bending | Route trays on racks | Bend radius 600-1000 mm |
Robotic Welding | Strong ladder construction | Automated transverse rung welding |
Supporting Lines | Secondary processes | Corner notching, accessories fabrication, powder coating, packaging |
With a high degree of automation and short changeover times, perforated cable tray manufacturing lines can be quickly customized for new dimensions and hole patterns.
Perforated Cable Tray Roll Forming Machine Suppliers
There are over 50 global manufacturers supplying perforated cable tray roll forming machines.
Table 5: Major Perforated Cable Tray Machine Manufacturers
Company | Location | Contact |
---|---|---|
Cosmap | Italy | [email protected] |
FD Machinery | China | [email protected] |
EAE | Turkey | [email protected] |
ITV | Spain | [email protected] |
Formtek | Taiwan | [email protected] |
When selecting a supplier, ensure:
- Machines are CE marked and meet all safety standards
- Company has supplied similar lines in your country before
- Forming stations can make the required cable tray dimensions
- Roller changeover time allows fast production shift
- Local after-sales service and spare parts supply capability
Price Range
- Basic perforated cable tray roll forming machine – $150,000 to $250,000
- Fully automated line with accessories fabrication and packing – $500,000+
Country of origin, production speed, and width capacity determine prices. Get detailed quotes from shortlisted suppliers against the production requirements before ordering the line.
Perforated Cable Tray Roll Forming Machine Installation
- Check flatness of foundation using precision instruments
- Use anti-vibration pads between foundation bolts
- Keep forming stations perfectly level in a straight line configuration using lasers
- Ensure compressors, hydraulic power packs and electrical panels are easily accessible for maintenance.
- Keep sufficient working space for decoiling raw materials and collecting finished products behind the line.
Operation of Perforated Cable Tray Roll Forming Machines
- The main drive motor (15-30 kW) powers the rotating parts through shaft, gears, chains and variable speed drives
- Insert coil strips, threading through decoiler, forming stations, cutting unit following tooling guides
- Set process parameters like feeding, speed, stroke length, lubrication flow rates on the touch screen
- Start operation in jog mode, then switch to automatic mode once forms are coming out uniform
- Continuously collect formed trays and stack properly using handling equipment
Figure 4: Operator working on perforated cable tray roll forming machine
Safety Measures
- Ensure safety guards are in place during operation
- Ear protection and metal gloves should be worn while working
- Frequently inspect machine for oil leaks, loose electrical connections, wear of chains, bearings and gears.
Maintenance of Perforated Cable Tray Roll Forming Machine
Table 6: Maintenance Schedule
Activity | Frequency | Method |
---|---|---|
Cleaning | Daily | Remove metal dust and oil leaks |
Lubrication | Weekly | Grease bearings and oil chains |
Inspection | Monthly | Check alignment, wear of forming rollers & punches |
Spare Parts | Yearly | Replace gearboxes, chains, bearings based on running hours |
Train technicians on the following maintenance procedures:
- Methods for tightening foundation bolts, aligning shafts
- Removing rollers and other tooling items when worn out
- Electrical connections and control panel servicing
- Hydraulic systems and pneumatic system maintenance
- Replacing consumables like lubrication oils periodically
Choosing Between Perforated Cable Tray Roll Forming Machine Manufacturers
While shortlisting suppliers, compare the following aspects:
Table 7: Perforated Cable Tray Machine Supplier Comparison
Parameter | Machine 1 | Machine 2 | Machine 3 |
---|---|---|---|
Forming Speed | 15 m/min | 20 m/min | 25 m/min |
Profile Width | 100-400 mm | 100-600 mm | 50-600 mm |
Hole Patterns | Round; Oval | Round; Slotted | All patterns |
Roller Design | 8 stations | 10 stations | 12 stations |
Automation | Semi-auto | Fully-auto | Fully-auto |
Price | $170,000 | $210,000 | $260,000 |
Machine 3 with highest speed, profiling range, automatic features, and number of bending stations provides best value for investment considering long term production volumes.
Pros and Cons of Perforated Cable Tray Roll Forming Machine
Advantages
- High production rates up to 25 m/min
- Width adjustable from 50 mm to 600 mm through quick roller change
- Hole shapes and percentages can be easily customized
- Low tooling cost compared to conventional press brakes
- High strength seamless construction by gradual cold rolling bending
- Integration of robotic welding, notching, accessories fabrication
Limitations
- Initial forming roller design needs extensive calculations and simulation
- Require large factory space for equipment installation
- Trained technicians needed for specialized maintenance
- Locking fixtures needed for polishing and powder coating finished products
Perforated Cable Tray Roll Forming Machine – Verdict
The perforated cable tray roll forming machine enables efficient mass production of tray frameworks with customized dimensions and hole patterns to route cables safely in diverse industrial setups.
Investing in automated lines with high output rates results in quicker return on investment due to rising global demand for cabling infrastructure across sectors. By adopting advanced solutions that integrate raw material decoiling to finished product packing functionalities across 25-50 meters factory length, manufacturers can gain significant competitive edge.
Technical contacts between the buyer and equipment builder during design finalization is vital to optimize the production line delivering maximum working widths, speed rates and hole perforations matching the buyer application requirements.
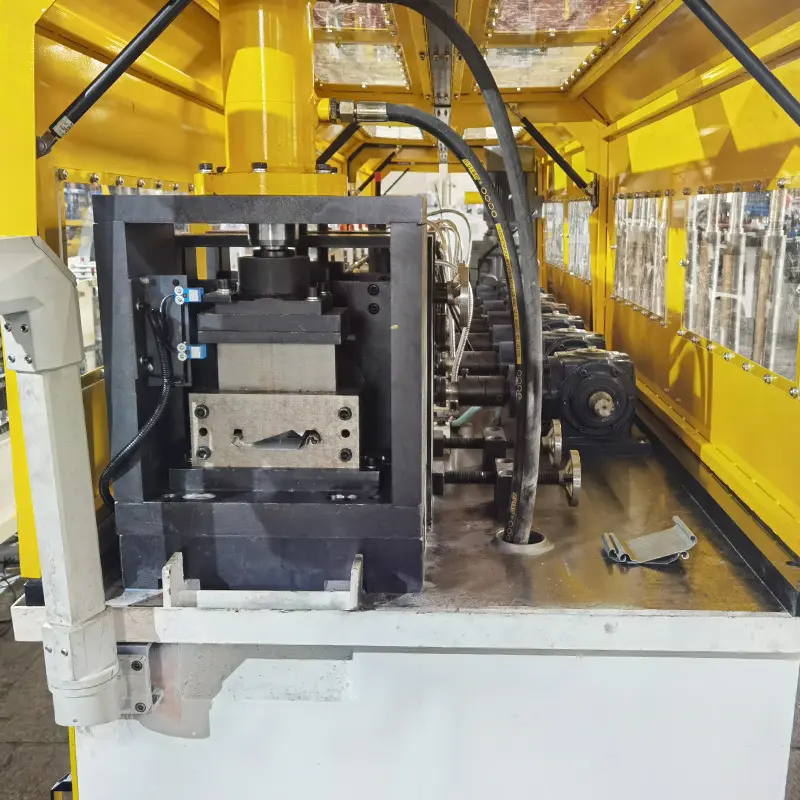
Frequently Asked Questions
Q: What are the forming roll materials used in the machine?
A: Forming rollers and related tooling are machined from wear-resistant alloys like petroleum coke alloy cast iron and hot worked tool steel for durability.
Q: Can a single machine make different perforated cable tray sizes?
A: Yes, advanced roll forming machines allow automatic setup changes within 15-20 minutes to form multiple widths and hole patterns.
Q: What defects can occur in perforated cable trays?
A: Waviness in sides, corner cracks, irregular hole sizes, dimensional deviations outside tolerance range arising from poor maintenance and worn-out bearing-rollers.
Q: Can special-shaped cable trays be produced?
A: Yes, custom profiles like horizontal S shapes for increased strength and aesthetic cable trays are possible through customized tooling.
Q: How to calculate power and raw material requirements for the machine?
A: Based on parameters like target output, material type, quality, thickness and product dimensions, technicians can derive power ratings and material coil quantity needed.