Palisade roll forming is an efficient process for producing long lengths of metal palisade fencing profiles. This guide provides a comprehensive overview of palisade roll forming machine types, capabilities, working principles, suppliers, costs and other key details.
Overview of Palisade Roll Forming Machines
Palisade roll forming machines continuously form metal coil strip into various palisade fence post and pale profiles. The process involves sequentially bending and shaping the strip through a series of precision roll stations.
Benefits of palisade fencing produced by roll forming include:
- High production speeds and output
- Consistent quality along entire profile lengths
- Tight tolerances compared to other processes
- Excellent surface finishes free of defects
- Cost-effective for long production runs
- Minimal scrap and material waste
This guide covers the major types of palisade roll formers, configurations, features, working principles, and considerations for selecting equipment.
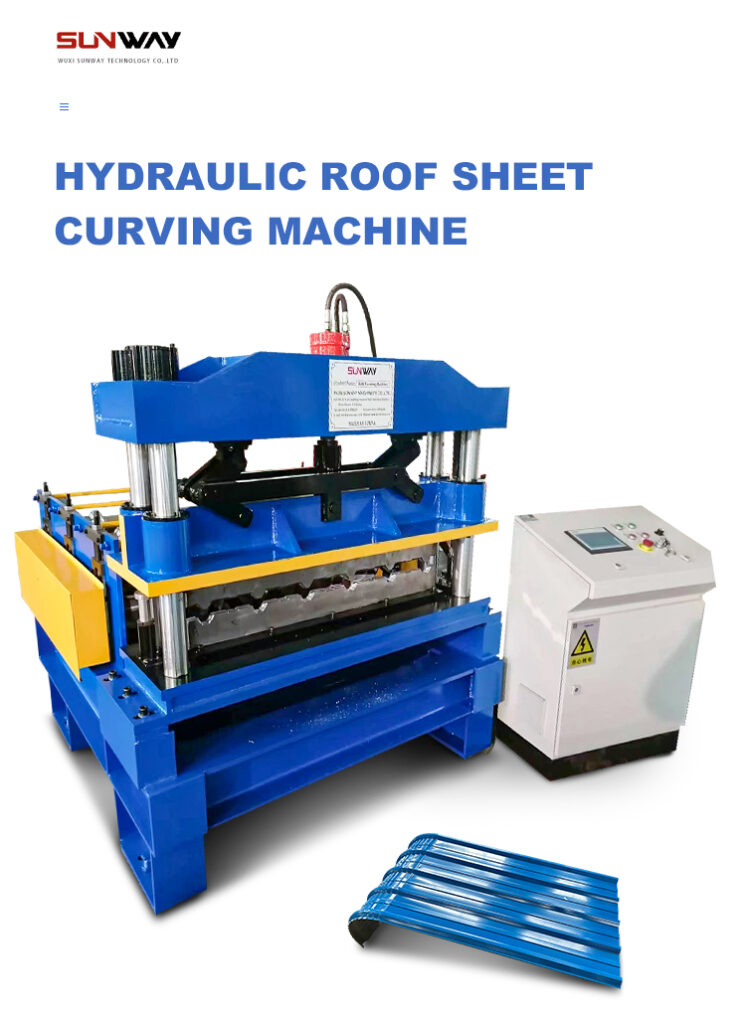
Types of Palisade Roll Forming Machines
There are two primary machine configurations used:
Horizontal Roll Forming Lines
- Material fed from a coil straightening machine
- Series of horizontal forming stands shape the strip
- Typical 10-16 stations depending on profile
- Produces long, straight fence lengths
- High production capacity for long runs
Vertical Roll Forming Lines
- Compact arrangement of 8-12 vertical forming heads
- Coil fed directly from an integrated de-coiler
- Mandrel holds coil for continuous production
- Shorter profile lengths produced
- Frequent profile changeovers
- Smaller batches and lower volume production
Additional Options
- Cut-off saws for cutting to length
- Hole punching units to add slots or holes
- Counting and bundling of finished posts
- Powder coating equipment for coating lines
Working Principle of Palisade Roll Forming
Palisade fence production involves progressively bending and shaping coil strip stock as it flows through multiple stands to form the final profile:
Process Steps
- Material feeding
- Accumulator controls strip tension
- Entry guides align strip
- Sequential bending and shaping through stands
- Calibration and sizing
- Cutting posts to length
- Output stacking
The number of stands, roller design, and temperature controls are tailored to the specific profile shape and material grade. Advanced 3D software simulates the bending sequence for optimal design.
Features and Capabilities of Roll Formed Palisade Fencing
Key benefits of palisade fencing produced via roll forming include:
- High speeds – Up to 100 ft/min production rate
- Superior consistency – Eliminates defects from manual processes
- Accuracy – Roll formed posts hold 1 mm dimensional tolerance
- Surface quality – Smoother surface than other processes
- Finishes – Can apply liquid or powder coatings
- Strength – Up to 20% stronger than simple bent posts
- Lower costs – Reduced labor and material savings
- Flexibility – Faster changeovers for alternate profiles
- Durability – Consistent quality improves product life
These advantages make roll forming ideal for palisade fencing production.
Materials Used for Roll Formed Palisade Fencing
Common materials include:
- Mild steel – Most widely used material grade
- Galvanized steel – Added corrosion resistance
- Stainless steel – Superior corrosion resistance
- Aluminum – Lightweight, good corrosion resistance
Steel thickness generally ranges from 16 gauge to 13 gauge (1.5mm to 2.5mm). Tooling enables forming thinner or thicker materials if needed.
Standard vs. Custom Palisade Profiles
Roll formers produce both standard and custom palisade profiles:
Standard Profiles
- Common post and pale sizes
- Pre-engineered tooling
- Lower cost
- High volume production
Custom Profiles
- Unique or specialized shapes
- Engineered tooling
- Higher initial tooling cost
- Lower order quantities
- Match custom fencing designs
Quick change tooling allows easy switching between standard and custom parts.
-
Vineyard Post Roll Forming Machine
-
Auto Size Changeable Sigma Purlin Roll Forming Machine
-
PV Mounting Bracket C Shape Profile Roll Forming Machine
-
C Z Purlin Channel Cold Roll Forming Machine Full Auto Galvanized Steel Profile
-
PV Mounting Bracket Roll Forming Machine (HAT / Omega Profile)
-
PV Mounting Bracket Z Shape Profile Roll Forming Machine
Design Considerations for Roll Formed Palisade Fencing
Roll forming places some design limitations:
- Constant cross-section – Profile must maintain uniform shape
- Bend orientation – Only transverse bends relative to material flow
- Bend radii – Limitations on achievable inside radii
- Wall thinning – Thickness reduction at tight radiuses
- Features – Limits on small details and geometry
Consulting early in the design process ensures manufacturability.
Suppliers of Palisade Roll Forming Equipment
There are many palisade roll former manufacturers worldwide. Some major suppliers include:
Company | Location | Machine Types |
---|---|---|
Samco Machinery | Canada | Combined straighteners and roll lines |
Shanghai Metal Corporation | China | High speed vertical roll forming |
T&H Lemont | USA | Customized roll forming lines |
Metform International | Turkey | Cut-to-length lines |
Zani Roll Forming | Italy | Powder coating integrated lines |
Bradbury Group | USA | Standard and custom palisade lines |
Both standardized and custom engineered machines are available to meet production needs.
Palisade Roll Forming Equipment Costs
Main roll forming line cost components include:
- Equipment – $50,000 to $500,000
- Tooling per profile – $5,000 to $15,000 for common shapes
- Installation – Approximately 15-25% of machine cost
- Training – 2-3 weeks recommended
- Maintenance – Around 5% of machine cost annually
Automated lines with higher throughputs provide faster payback on investment from labor and material savings.
Pros and Cons of Roll Formed Palisade Fencing
Advantages | Disadvantages |
---|---|
High production speeds | High initial capital investment |
Superior consistency and quality | Fixed tooling costs per custom profile |
Low scrap and material waste | Limitations on profile geometries |
Minimized labor requirements | Regular maintenance needed |
Adaptable automation features | Space required for equipment |
Ability to integrate steps like coating | Skilled operators required |
Palisade Roll Forming Applications
Main application areas include:
- Perimeter fencing at commercial properties
- Privacy fencing around residential yards
- Security fencing at utilities and infrastructure
- Architectural fencing for buildings
- Temporary fencing for construction sites
- Crowd control barriers and enclosures
Any application requiring linear feet of palisade fencing benefits from the consistency and efficiencies of roll formed production.
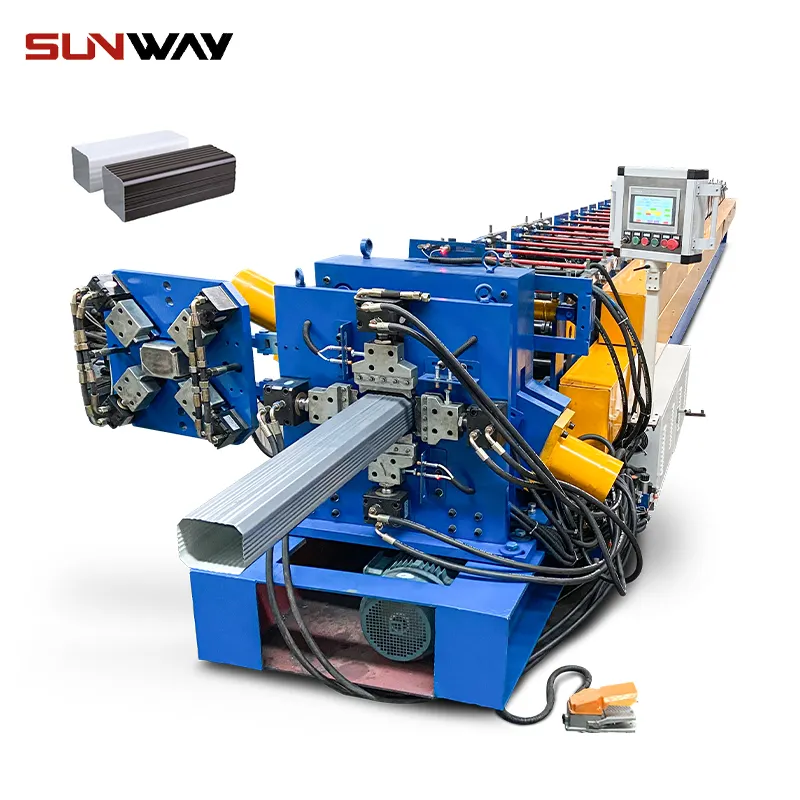
FAQ
Q: What thickness of metal is typically used?
A: For palisade fencing, thicknesses between 16 gauge (1.5mm) to 13 gauge (2.5mm) are typical. Custom tooling enables thinner or thicker material forming.
Q: What safety precautions are required?
A: Roll forming equipment contains hazards requiring proper safeguards, interlocks, grounding, and personal protective equipment.
Q: How long does it take to changeover between profiles?
A: With quick change tooling, skilled operators can change over profiles in 30-60 minutes. Without quick change features, several hours are typically needed.
Q: Can a powder coated finish be applied after roll forming?
A: Yes, powder coating after roll forming is commonly done and provides increased coating adhesion compared to coating a coil directly.
Q: Are roll formed palisade fences higher quality than other processes?
A: Roll forming eliminates defects resulting in superior consistency and quality along the entire profile length. Strength can be 10-20% higher than simpler bending methods.
Conclusion
Palisade roll forming provides an efficient automated process for producing fencing profiles with accuracy and repeatability. When properly engineered, roll formed palisade offers durability, material savings, and quality advantages over manual production methods.
With flexible changeover capabilities, palisade roll formers enable producers to meet varying project demands cost-effectively. Integrated finishing like powder coating further expands process benefits.