Tile roll forming machines are essential equipment for tile manufacturers. This guide provides a comprehensive overview of OEM (original equipment manufacturer) tile roll forming machines, including working principles, types, processes, selection factors, suppliers, prices, pros and cons, and more.
What is an OEM Tile Roll Forming Machine?
An OEM tile roll forming machine is a specialized machine designed specifically for tile production. It creates tile profiles by bending, cutting, and forming metal coils into the desired tile shapes.
OEM stands for “original equipment manufacturer,” indicating the machine is made by the tile manufacturer rather than purchased from another company. OEM tile machines are customized to the exact specifications required by the manufacturer.
Benefits of OEM tile machines:
- Fully customized for specific tile designs
- Optimized for efficiency and quality
- Tailored production process
- Flexibility for future adaptations
In contrast, purchasing generic tile making equipment often requires additional customization efforts. Opting for an integrated, purpose-built OEM tile machine streamlines manufacturing.
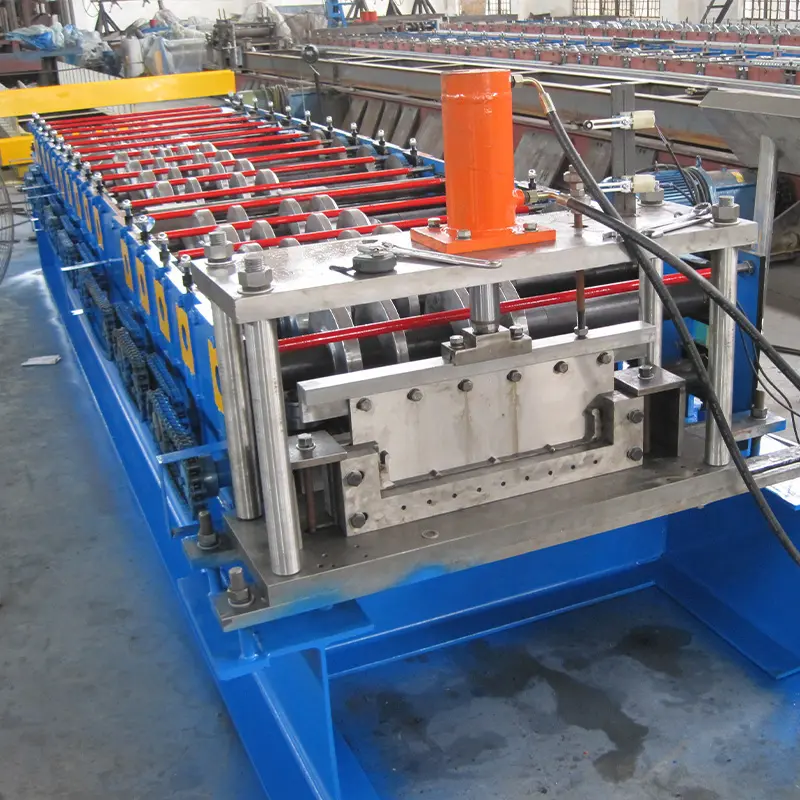
How an OEM Tile Roll Forming Machine Works
A tile roll forming machine works by feeding metal coil stock through a series of roller dies that progressively shape the material into the final tile profile through bending and pressure forming.
The process consists of three main stages:
1. Feeding – Coiled steel or aluminum is placed on an uncoiler and fed through feed rollers into the forming section.
2. Forming – The strip passes through a series of roller dies that apply pressure to shape the metal into wave-like tile profiles.
3. Cutting – Formed tiles move through a running cutoff press to cut profiles to length based on specifications.
Other additional processes like punching holes, embossing designs, or adding protective coatings can also be integrated, depending on the machine capabilities and tile requirements.
The key components that enable the forming process are the roller dies. Their number, designs, materials, and setup directly impact the profiles produced. Dies can create small overlapping waves or large distinct ribs with drainage channels between them.
Computerized controls regulate the feed rate, roller pressures, and cutoff locations to ensure consistency. Some OEM tile machines also incorporate inline quality checks using sensors to inspect tile dimensions and reject defective pieces.
Types of OEM Tile Making Machines
OEM tile machines fall into three main categories:
Sheet Tile Lines
- Designed for tiles made from metal sheets instead of coils
- Use hydraulic or mechanical presses for forming instead of rollers
- Lower capacities around 600 tiles/hour
- Suitable for small-scale production
Single-Profile Roll Forming Lines
- Produce simple, single-type tile designs
- Typically max around 5000-6000 tiles/hour
- Lower tooling costs
- Offer quicker changeovers between jobs
High-Speed Multi-Profile Roll Forming Lines
- Output intricate tile shapes at over 10,000 tiles/hour
- Automated controls for efficiency
- Advanced tooling allows profile changes
- Higher equipment costs but very high throughput
Tile Material Handling Considerations
- Stainless steel and aluminum coils are commonly used
- Thickness ranges from 0.15mm to 0.8mm
- Some machines handle double coils for fewer changeovers
- Tile widths between 200mm to 1000mm
- Consider coil size, weight limits, feed speeds
-
Highway Guardrail End Terminal Forming Machine
-
Highway U/C Post Roll Forming Machine
-
2 Waves Highway Guardrail Roll Forming Machine
-
3 Waves Highway Guardrail Roll Forming Machine
-
Corrugated Panel Roll Forming Machine
-
Light Gauge Steel Roll Forming Machine
-
Steel Box Plate Making Roll Forming Machine
-
Electrical Cabinet Frame Roll Forming Machine
-
Din Rail Roll Forming Machine
Key Tile Making Production Processes
OEM tile roll forming machine lines integrate various inline production processes to transform raw coil stock into finished roofing and wall tiles:
Table 1: Key Tile Making Production Processes
Process | Description |
---|---|
Uncoiling | Sheet metal coil is loaded onto a powered unwind mandrel. |
Feeding | Feed rollers grip and pull the strip through the line. |
Roll Forming | Forming stations shape strip into wave profiles. |
Embossing | Textured roller patterns add decorative embossed finishes. |
Punching | Punch dies cut venting holes and installation slots. |
Profile Cutting | Running cutoff presses slice formed tiles to length. |
Stacking | Formed tiles are neatly stacked for easy handling. |
Coating | Liquid coatings add weather protection and color. |
Curing | Formed tiles pass through curing ovens to dry coatings. |
Quality Inspection | Sensors check tile dimensions and reject defects. |
Packaging | Tiles placed in protective wrapping for transport. |
These processes can be combined in different sequences or done inline or offline to produce the desired tile products.
Choosing an OEM Tile Roll Forming Machine
Selecting the optimal tile making machine depends on required production volumes, tile sizes, design complexity, changeover needs, and budget.
Key factors to consider:
Table 2. OEM Tile Machine Selection Factors
Parameter | Details |
---|---|
Production Volume | Impacts machine speed, automation, and tooling needs. |
Tile Sizes | Width capacity ranges from 200mm to 1000mm typically. |
Tile Designs | More forming stations needed for complex profiles. |
Changeover Speed | Modular tooling enables faster profile changes. |
Line Integration | Assess offline vs inline processes requirements. |
Control Systems | Automatic monitoring improves efficiency. |
Tooling Materials | Hardened metals withstand high production. |
Budget | Multi-profile machinery has higher capital costs. |
Production Standards | Ensure system can meet quality benchmarks. |
Future Expansion | Consider potential to handle more volumes or products later on. |
Analyzing these parameters helps match available OEM tile making machine specifications to manufacturing needs and goals.
OEM Tile Machine Suppliers and Costs
Many specialized machinery manufacturers offer OEM tile production lines globally. Below are some of the leading international suppliers and price ranges:
Table 3. OEM Tile Machine Manufacturers and Prices
Supplier | Location | Price Range |
---|---|---|
Kingsun Machinery | Zhejiang, China | $100,000 – $500,000 |
MTC | Istanbul, Turkey | $200,000 – $1,000,000 |
Metform | Ontario, Canada | $300,000 – $800,000 |
Dioxipe | Shanghai, China | $150,000 – $600,000 |
Sigmatech Engineering | Gujarat, India | $250,000 – $750,000 |
Pricing varies based on:
- Production capacity
- Automation level
- Profile complexity
- Line customization
- Additional equipment
Larger OEM tile making systems with high output volumes, quick changeovers, and multiple processes integrated cost over $1 million. Smaller semi-automatic lines start around $100,000.
Installation, Operation, and Maintenance
Table 4. OEM Tile Machine Installation, Operation, and Maintenance
Activity | Description |
---|---|
Site Preparation | Ensure adequate space, power supply, compressed air lines. |
Installation | Machinery positioned and fastened per plan. Connected to utilities. |
Commissioning | Testing machine functions without production. Calibrating components. |
Operation | Running system as per specifications once production starts. |
Control Parameters | Setting feed rates, pressure levels, tempos to meet standards. |
Maintenance | Daily cleaning and lubrication. Inspecting parts for wear. |
Tooling Maintenance | Replacing forming rollers and dies when worn. |
Operator Training | Learning startup, shutdown, troubleshooting procedures. |
Proper installation and maintenance keeps OEM tile machines running optimally. Staff should undergo equipment operation and safety training.
Benefits of OEM Tile Roll Forming Technology
Investing in customized OEM tile making machinery has many advantages over purchasing generic equipment:
Table 5. Benefits of OEM Tile Machines
Benefit | Description |
---|---|
Higher Efficiency | Purpose-built for specific volumes with ideal speeds. |
Quality Output | Integrated inline processes prevent defects. |
Consistency | Automated monitoring aids uniform finished products. |
Profile Flexibility | Interchangeable modular tooling allows design changes. |
Scalability | Output can be increased with upgraded tooling. |
Better Pricing | Large capacities provide economies of scale. |
Faster Delivery | Direct from manufacturer avoids third-party delays. |
Responsiveness | OEM builder can easily adapt machine to new customer needs. |
The made-to-order nature of OEM tile equipment results better productivity, consistency and responsiveness compared to standardized machinery.
Limitations of OEM Tile Roll Formers
However, OEM tile making lines also come with the following drawbacks:
Table 6. OEM Tile Machine Limitations
Limitation | Description |
---|---|
High Initial Capital | Heavily-customized equipment demands substantial upfront investment. |
Long Lead Times | Can take 6+ months from order to delivery. |
Proprietary Components | Custom-made parts may have sourcing issues if supplier goes out of business. |
Lack of Support History | As pioneer systems, troubleshooting help can be limited. |
Modularity Constraints | Extensive rebuilds needed to incorporate major production changes. |
Scalability Challenges | Adding secondary lines often easier than altering core machine. |
While offering efficiency through customization, OEM tile machinery can pose business continuity risks and adaptation limitations not found in standard equipment.
Choosing an OEM Tile Machine Supplier
Due diligence during supplier selection is vital to get an OEM tile line that meets manufacturing objectives.
Table 7. OEM Tile Machine Supplier Selection Criteria
Parameter | Details to Consider |
---|---|
Industry Experience | Years of tile machinery expertise preferred. |
Production Capabilities | Assess if supplier facility can actually manufacture the line per specifications. |
Design Expertise | Evaluate engineering team skills to identify and avoid potential issues. |
Component Quality | Ensure high-grade parts will be used, not lower-cost copies. |
Commissioning Support | Supplier assistance required for proper on-site machine set up. |
Post-installation Support | Clear agreement needed on continued technical support terms. |
Financial Stability | Choose established company with healthy financial track record. |
Reference Checks | Speak to current machine owners on performance satisfaction. |
Thoroughly vetting and selecting the tile making OEM machinery builder improves outcomes and long-term equipment reliability.
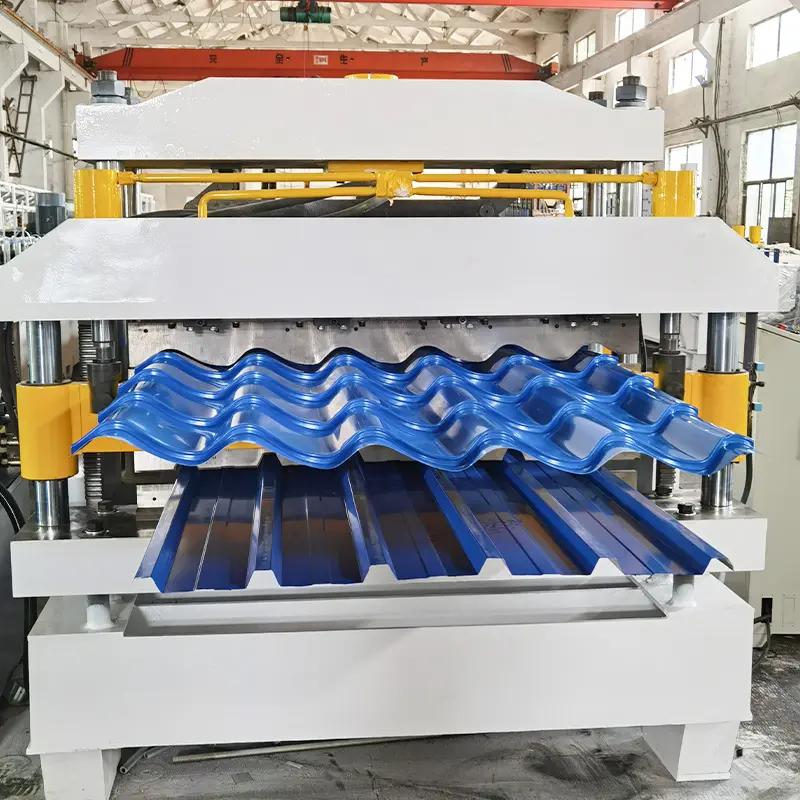
FAQ
Q: What expertise is needed to operate an OEM tile roll forming machine?
A: OEM tile machines require trained technicians for operation and maintenance. Most suppliers provide instruction for machine operators. Key skills needed include mechanical competence, troubleshooting abilities, quality control awareness, and computer literacy for the digital components.
Q: Can OEM tile machines make different types of tiles?
A: Modular tooling concepts allow interchangeable roller dies to create different profiles. However, major tile material changes between metals or incorporating ceramics require extensive machine alterations. It is best to specify all planned tile varieties upfront for the widest flexibility.
Q: How to improve efficiency of OEM tile production line?
A: Using automatic feeding systems instead of manual loading, integrating inline quality inspection, monitoring production metrics, and scheduling regular maintenance help optimize efficiency. Upgrading to quicker dies or adding secondary processes in parallel can further boost output.
Q: What safety measures are required for OEM tile machines?
A: Tile production involves hot, heavy machinery, so extensive precautions are vital. Key measures consist of enclosure guards, emergency stops, lockouts, warning indicators, operational signals, protective gear, and defined safety zones. Regular safety reviews should also occur.
Q: How much technical support comes with OEM tile machinery?
A: Most OEM suppliers provide documentation on equipment use guidelines. Many also assign technical specialists to support installation, testing, and initial production. Longer-term service contracts may be available too covering online/phone assistance or on-site visits as required for troubleshooting and repairs.
Conclusion
Investing in customized OEM tile roll forming capabilities enables manufacturers to achieve high-quality, mass production of tiles with maximum efficiency and consistency.
Carefully developing machine specifications based on full consideration of required capacities, tile varieties, production processes, and potential for future expansion or adaptations allows creating an optimized tile making system tailored for current and upcoming needs.
Vetting suppliers thoroughly based on industry expertise, design skills, build quality, and ongoing support ensures reliable equipment performance for years to come.
While requiring considerable initial capital expenditure, integrating automated OEM tile technology offers rapid returns on investment through substantially elevated and flexible manufacturing output.