Overview
An OEM purlin roll forming machine is a specialized industrial equipment system used to continuously mass produce long length metal purlins and girts from coiled steel feedstock for use in original equipment manufactured steel buildings and structures.
Purlins act as structural Z, C or U-shaped roof and wall framing members that support exterior covering materials in metal building systems. Roll formed purlin sections optimize strength-to-weight rations with their vertical web and flange cross-sectional shape.
This guide provides a comprehensive overview of OEM purlin roll former technology, including:
- Machine types and components
- The purlin roll forming process
- Design factors and building standards
- Purlin framing applications
- Cost analysis
- Comparisons with other framing methods
- Leading global manufacturers
Gaining technical insight into OEM purlin roll former capabilities and structural framing assists engineers, contractors and architects evaluating optimized building solutions.
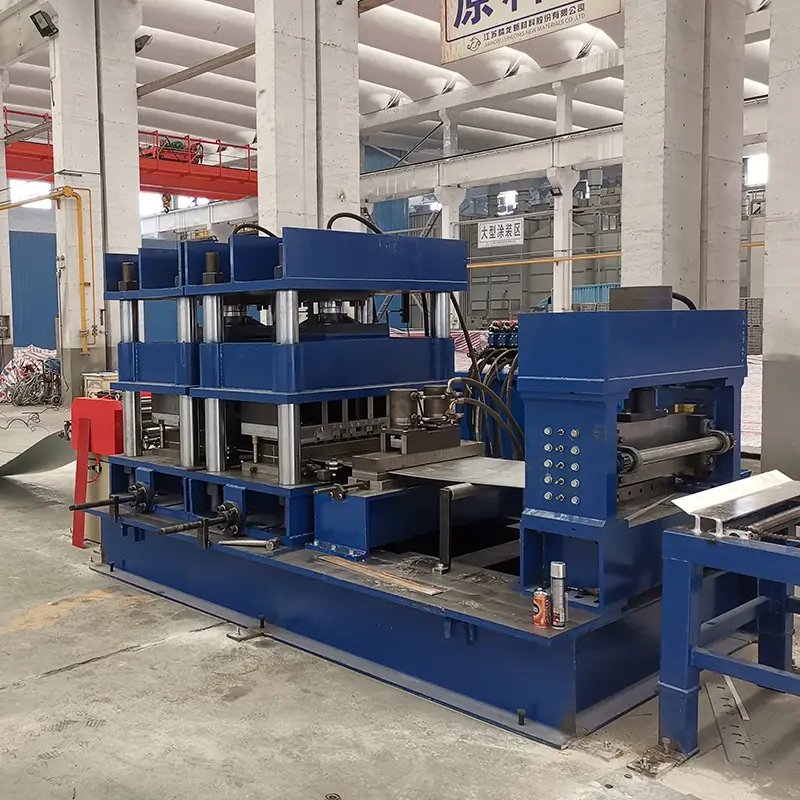
Types of OEM Purlin Roll Forming Machines
There are two primary machine configurations used for high volume OEM purlin production:
Pyramid-Type Purlin Roll Formers
- Typically 10-16 forming stations in decreasing diameter tiers
- Compact layout, smaller footprint
- Slower production speeds
Inline Purlin Roll Formers
- Stations horizontally inline
- Longer line lengths
- High volume capacity
- Faster cycle times
Main Components of a Purlin Roll Former
A typical OEM purlin roll forming line integrates these key sections:
Coil Payoff Reel
- Holds raw steel coil
- Powered unwind
Entry Guides
- Straighten and align strip
- Optimize material feed
Accumulator / Bridle
- Creates back tension zone
- Smooths flow variations
Forming Stations
- Progressive die rollers shape strip
- Number & type determine profile
Cutter
- Pneumatic or servo shear
- Trims finished purlins
Exit Conveyor Table
- Transfers finished lengths
- Supports long products
Automation Controller
- Touchscreen HMI
- Stores recipes
- Production data feedback
How Purlin Roll Forming Machines Work
The OEM purlin roll forming process shapes steel coil strip into C or Z-shaped roof and wall framing sections by bending and forming the feed material incrementally as it passes through a series of roller die stations:
- Powered coil payoff reel feeds raw coiled steel into entry guides
- Guides align strip and feed into initial roller stations
- Rolling dies at each station make gradual precision bends
- Strip exits each stand slightly more formed
- Finished purlin profile emerges at end of line
- Pneumatic shear cuts to length
- Exit conveyor tables transfer finished lengths
The number of roller die stands determines possible purlin profile complexity. Quick change tooling allows fast production changeovers.
-
Vineyard Post Roll Forming Machine
-
Auto Size Changeable Sigma Purlin Roll Forming Machine
-
C Section Bracing Omega Storage Rack Upright Post Roll Forming Machine
-
Steel Box Plate Making Roll Forming Machine
-
Box Beam Steel Roll Forming Machine For Shelf Column
-
Pallet Racking Step Beam P Beam Roll Forming Machine
-
Warehouse Shelf Upright Roll Forming Machine
-
PV Mounting Bracket C Shape Profile Roll Forming Machine
-
C Z Purlin Channel Cold Roll Forming Machine Full Auto Galvanized Steel Profile
Key Design Factors for Purlin Roll Forming
Equipment specifiers evaluate numerous characteristics when selecting OEM purlin roll formers:
Building Type
- Pre-engineered steel structures
- Agricultural & commercial spans
- Residential metal roofing
Purlin Type
- Zee, Zed, Sigma
- Narrow flange Cee
- Structural tees
Material
- Low carbon steel
- High strength steel
- Galvanized coatings
Thickness
- 16 gauge to 7 gauge
- 1.2mm to 4mm+
Profile Height
- 75mm to 400mm+
- 3” to 18”+
Line Speed
- 10 to 35 m/min
- 33 to 115 ft/min
Changeover
- Quick change tooling
- Secondary fab stations
Framing Standards for OEM Purlins
While often custom engineered for specific buildings, these standards guide commercial purlin designs:
Standard | Description |
---|---|
AISI S100 | North American cold-formed steel framing |
AS/NZS 4600 | Australian / New Zealand cold-formed steel structures |
BS 5950 | British cold rolled steel sections |
EN 1993-1-3 | European cold-formed steel structural framing |
IS 801 | Indian standard purlin sections |
Typical Purlin Framing Applications
Common structural framing applications utilizing OEM roll formed steel purlins include:
Roof Purlins
- Metal building roofing support
- Standing seam roofing
- Single skin systems
Wall Girts
- Exterior metal panel backing
- Curtain wall framing
- Interior divide framing
Platform Framing
- Supporting floors
- Structural bridging
- Platform roofs
Structural Racking
- Warehouse racks
- Mezzanines
- Equipment platforms
Agricultural Buildings
- Pole barns
- Grain bin rings
- Storage sheds
Purlin Specifications
Metric | Typical Range |
---|---|
Height | 75 mm – 400 mm |
Flange Width | 30 mm – 100 mm |
Thickness | 1.5 mm – 4 mm |
Length | 2 m – 13 m |
Load | 3 kN/m – 10 kN/m |
Span | 1.5 m – 8 m |
Leading OEM Purlin Roll Former Manufacturers
Top international OEM purlin roll former producers include:
Company | Location |
---|---|
Formtek | USA |
Epicenter Machinery | China |
BOTOU Xianfa | China |
Gasparini | Italy |
Metform | Turkey |
Pricing
Machine | Average Cost (USD) |
---|---|
Basic Pyramid Roll Former | $92,000 |
Inline 20-Station Machine | $185,000 |
High Capacity Servo Line | $430,000 |
Purlin | Average Cost Per Foot (USD) |
---|---|
12” 18 Gauge Zee | $1.15 |
8” 14 Gauge Cee | $1.75 |
4” 11 Gauge Sigma | $2.40 |
Advantages of OEM Purlin Roll Forming
Benefits
- High production speeds
- Precision tolerances
- Quality consistency
- Minimal fabrication
- Lower material cost
- Reduced building construction time
Limitations
- High machine capital costs
- Mainly long, straight shapes
- Can require secondary punching
- Fixed tooling less flexible
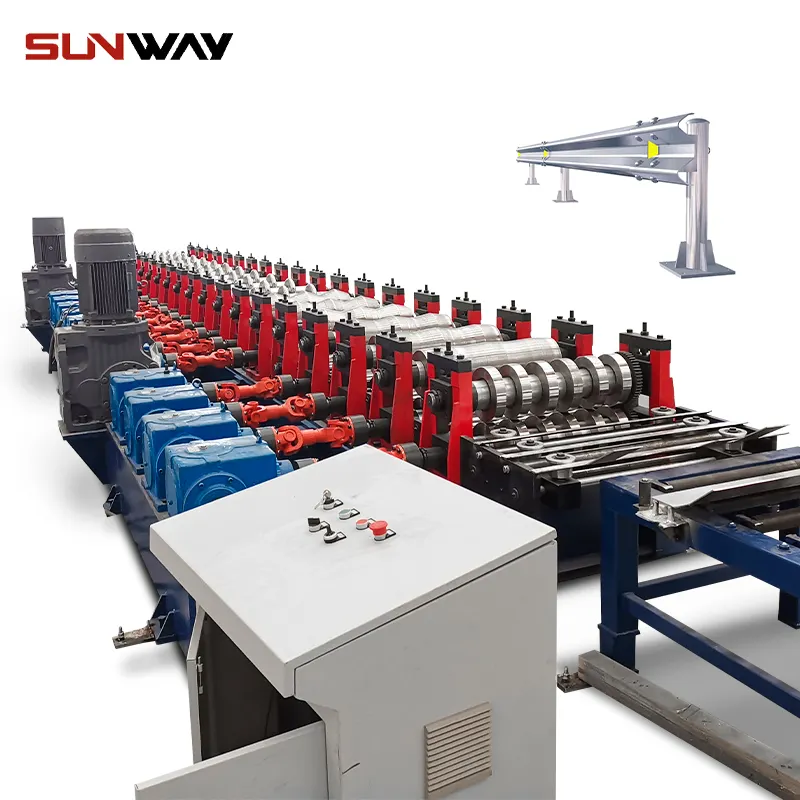
FAQ
What is the maximum length of OEM roll formed purlins?
Standard exit conveyor tables allow continuous forming of purlins up to 40′ (12 m). Custom extra long beds can produce sections approaching 65′ (20 m).
What metals can use roll forming for purlins?
All common building steels including low carbon, high strength alloy steels, corrosion resistant alloys as well as lightweight aluminum framing grades.
What if secondary holes or clips are needed in the purlins?
Inline punching presses, drilling machines and clip insertion equipment can be integrated on the exit conveyor to add holes or mounting features.
What is the thickest gauge purlin an OEM roll former can produce?
Average max thickness is around 7 gauge steel or 4mm plate. Heavy duty custom machines can produce structural shapes from 3 gauge steel and beyond.