Floor deck roll forming machines are used to produce corrugated floor decks from metal coils. OEM (Original Equipment Manufacturer) floor deck roll formers are built to order for the customer’s requirements. This guide provides a detailed overview of OEM floor deck roll forming machine capabilities, working principles, suppliers, costs, installation, operation and maintenance.
oem floor deck roll forming machine Overview
Floor decking sheets are an important structural component in concrete floor slab construction. Corrugated profiles provide strength and act as permanent concrete formwork. Roll formed metal floor decks are lightweight and fast to install compared to wood or other alternatives.
OEM roll forming lines are custom built to specification so buyers can get capabilities matching their exact floor deck product requirements. Key parameters that can be customized include:
- Table: OEM Floor Deck Roll Former Customization Options
Parameter | Customization Options |
---|---|
Material | Steel coils, stainless steel, aluminum |
Thickness | 0.7mm to 3mm |
Width | Up to 1500mm |
Profile | Trapezoidal, reentrant, dovetail, custom shapes |
Features | Embossing, holes, drainage channels |
Coating | Pre-painted, galvanized |
Speed | Up to 35 m/min |
Automation | Coil loading/unloading, stackers |
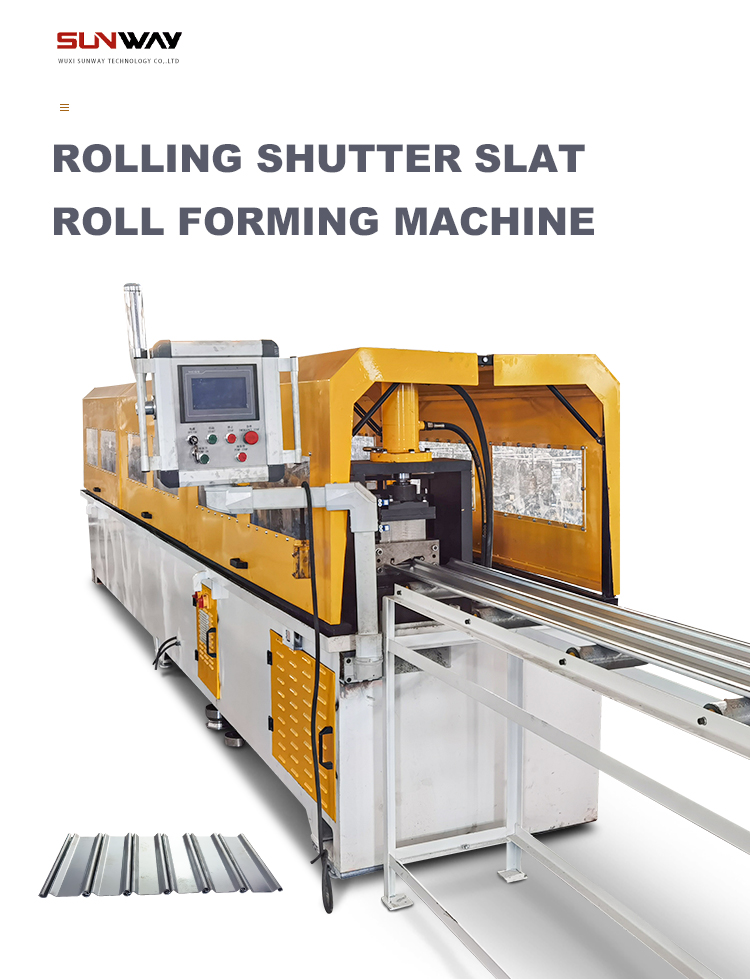
Main Components of oem floor deck roll forming machine
An OEM floor deck roll forming system contains the major components below:
- Uncoiler: Feeds metal coil stock into the roll former
- Feeding tables: Support and guides the strip
- Roll forming stations: Progressively bend metal strip into designed profile
- Hydraulic system: Provides power for bending and calibration
- Cut-off press: Cuts profiled sheet to length
- Stacker: Stacks finished floor deck sheets
Table: Main Components of Floor Deck Roll Forming Line
Component | Role |
---|---|
Uncoiler | Feeds metal coil into system |
Feeding tables | Guide strip through machine |
Roll forming stations | Bend strip into floor deck profile |
Hydraulic system | Power for forming process |
Cutting system | Trims sheets to length |
Stacker | Stacks produced floor decks |
oem floor deck roll forming machine Working Principle
Floor deck sheet production utilizes continuous cold roll forming technology. Metal coil stock is unrolled and passed through a series of roller stations. The rollers have machined contours that progressively bend the strip into the desired corrugated shape.
Step-by-Step Process
The oem floor deck roll forming machine functions via the steps below:
- Uncoiling – Coil mounted on a powered unwind mandrel. Strip feeds into machine.
- Feeding – Guide tables support and align the strip through the roll former
- Forming – Roller stations bend the strip in stages into floor deck profile
- Critical forming – Last stations finalize shape accuracy
- Calibration – Hydraulic cylinders apply pressure to calibrate
- Cutting – Shearing blade trims sheet to length
- Stacking – Conveyors move done sheets for counting and stacking
Correct forming requires precision machined rollers, precise gap settings between stations, proper strip feed and tensioning pressure. The last stations provide critical calibration to achieve dimensional and shape accuracy per specifications.
OEM Floor Deck Profile Design Capabilities
OEM roll former lines offer extensive profile design flexibility for floor decking production. Common profiles include:
- Trapezoidal: Most popular shape with inclined flanges
- Re-entrant: Flanges bend inwards for composite concrete interaction
- Dovetail: Improves concrete bonding for higher performance
In addition, custom shapes can be produced for specialized applications:
- Embossing: For improved concrete grip
- Perforations: Allow conduits and services to pass through
- Stiffening folds/lips: Enhance strength
- Drainage channels: Prevent water pooling on roof decks
Experienced OEMs have extensive roll forming knowledge to produce proven profiles or develop new custom shapes matching project requirements.
oem Floor Deck Materials, Sizes and Finishes
OEM equipment allows configuring floor deck parameters like:
- Materials: Steel, stainless steel, aluminum coils
- Thickness: 0.7mm to 3mm
- Width: Up to 1500mm
- Coatings: Pre-painted, hot dip galvanizing, organic coatings
Certain specialized materials like weathering steel or corrosion resistant alloys can also be formed.
OEM Floor Deck Roll Former Automation Features
Standard OEM floor deck roll forming lines have basic automated functions:
- Powered uncoiler: Reduces labor for coil loading
- Servo feed system: Ensures smooth strip feed
- Flying cut-off: Cuts sheets without stopping production
- Exit tables/conveyors: Transfer done sheets
Optional enhancements for higher automation include:
- Fully automated coil loading and unloading
- In-feed guides/straighteners for coil strips
- Automatic stackers to neatly pile finished sheets
- Length cutoff systems with counting functionality
- Programmable PLC controls for parameter adjustment
- Production data monitoring systems
Determining correct automation level depends on production volumes, labor costs and budgets. OEMs can provide guidance on ideal setup.
OEM Floor Deck Roll Former Suppliers
Many custom metal processing equipment manufacturers offer floor deck roll forming machines. When selecting an OEM supplier, key aspects to evaluate include:
- Table: OEM Floor Deck Roll Former Selection Criteria
Parameter | Importance |
---|---|
Profile precision | High – Ensures floor deck accuracy |
Roller machining | High – Complex profiles need high precision |
Line speed | Depends on output targets |
Quick tooling change | Medium – For future profile adjustments |
Automation features | Depends on labor costs |
International certifications | Medium – Sign of quality management |
Experience record | High – Proven ability to execute projects |
Customization flexibility | High – For special requirements |
Budgetary quote | High – Important to compare affordability |
Reputable OEMs provide a design phase with engineering drawings, FEM analysis and iterations before manufacturing. They also offer complete floor deck production solutions including auxiliary equipment like slitters, stackers, benders and software.
Installing OEM Floor Deck Roll Forming Machines
Proper installation is key for operational efficiency and safety. OEMs provide complete guidance, but major aspects involve:
- Civil structure: Level concrete foundations to mount the equipment
- Assembly: Bearings, stations and subsystems assembled as per drawings
- Power: Connect electrical supply lines and hydraulics
- Trial runs: Check functioning of all working parts
- Safety: Install guarding, emergency stops and interlocks
Most modern machines have quick install designs. Precision roller stations and tooling utilize quick change systems or easy dismantling for maintenance. Allen bolts allow straightforward assembly and alignment.
Some best practices during installation:
- Have technicians from the OEM supervise for best results
- Keep assembly area clean to avoid dust ingress
- Follow torque specs for bearings and hydraulic fixtures
- Adjust alignment precisely using laser systems
- Apply lubrication during assembly to critical moving joints
Operating OEM Floor Deck Roll Forming Machines
After installation, equipment is optimized for best performance. Steps include:
- Feed material coil matching design specs
- Set parameters like sheet length, line speed
- Initialize strip through the stations slowly
- Test roll former producing a few sheets
- Check formed profile accuracy dimensions
- Adjust roller gaps, pressure as needed
- Run machine to rated speed and test full capability
- Inspect sample sheets dims, finish quality
For peak efficiency, comprehensive operator training from OEM technicians is highly recommended during commissioning. Proper machine operation principles linked to the custom equipment capabilities optimizes production.
Maintenance of OEM Floor Deck Roll Forming Equipment
Preventative maintenance is vital for maximum roll former uptime. General upkeep tasks include:
Component | Maintenance Frequency | Tasks Performed |
---|---|---|
Rollers | Monthly | Inspect surface wear; Replace if needed |
Bearings | 3 months | Lubricate; check set screws; replace if worn |
Hydraulics | 6 months | Inspect lines, cylinders & pumps; replace seals if leaking |
Drive systems | Yearly | Check motors, gearboxes, clutches & chains; Lubricate chains |
Structural | Yearly | Re-torque loosened station bolts; Weld cracks; touch up paint |
Controls | As needed | Calibrate sensors; Check wiring; replace fuses & relays |
Table: Recommended Maintenance Schedule
Unexpected downtime is hugely expensive – lost production + repair costs. That is why scheduled maintenance budgets save money long term.
Modern flexible designs allow replacing only damaged components. Most stations have replaceable wear items. Qualified technicians can respond promptly for breakdown repairs or preventative work.
Choosing the Right OEM Floor Deck Roll Former
Evaluating options to pick the ideal OEM floor deck roll forming system involves:
Application Requirements
- Floor deck sizes, materials, annual output targets
- Site conditions – available space, power, labor
- Budget constraints
Equipment Capabilities
- Profile accuracy standards guaranteed
- Speed versus needed volumes
- Automation features to match labor availability
- Overall quality and OEM reliability
Ancillary Equipment
- Options like sheet stackers, sheet splitters, sheet straighteners
- Software for production monitoring
Cost Considerations
- Per metric ton equipment cost
- Operating costs – labor, maintenance, consumables
- Freight and taxes to import equipment
- Payment terms – upfront or installment options
Carefully balancing these aspects ensures procurement of the ideal OEM roll former matching floor deck requirements now and in the future.
Pros and Cons of OEM Floor Deck Roll Forming Technology
Advantages
- High production volumes possible
- Lightweight finished sheets for construction
- Smooth surfaced uniform profiles
- Consistent quality monitored via custom software
- Flexibility – can adjust parameters easily
- Low maintenance and operation cost
Limitations
- High initial equipment purchase cost
- Complex customization needs experienced OEM
- Installation space required
- Auxiliary material handling equipment needed
Applications of Roll Formed Metal Floor Decks
OEM roll formed floor decks serve varied applications:
- Concrete floor slab reinforcing layers in buildings
- Metal decking with concrete topping in offices
- Stair or balcony platforms in high rise projects
- False ceiling roofing support for lights, ducting
- Floor and roof drainage channels
- Mezzanine flooring structures in warehouses
- Container and trailer bed platforms
Floor deck sheets provide strength performing as structural formwork while being lightweight and faster to install than alternatives.
Most Effective Application Areas
Roll formed floor decks are extremely effective for:
- Commercial buildings needing flat soffits
- Industrial spaces with long clear spans sought
- High rise projects where weight reduction needed
- Metal composite concrete flooring systems
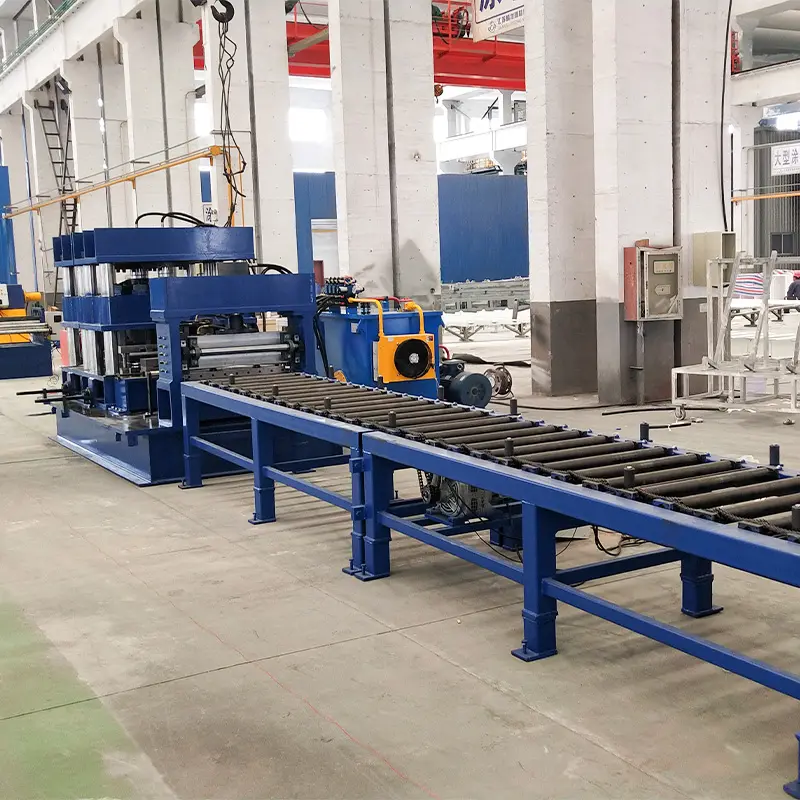
Total Cost Analysis for 500,000m2 Floor Deck Project
Roll formed floor decking is usually compared to traditional material alternatives. Let’s analyze sample total cost metrics for 500,000 m2 of 0.9mm thick galvanized steel floor decking:
Cost Component | Wood Formwork | Other Permanent Systems | Roll Formed Steel Deck |
---|---|---|---|
Material cost | High | High | $750,000 |
Construction labor | High labor intensity | Medium | Low – easy fixing |
Formwork handling cost | High | Medium | None |
Concrete usage saving | None | None | 10% less concrete needed |
Construction time saving | None | Minimal | 40% faster completion |
Environmental impact | High | Medium | Low |
Recycling value | Low | Low | High scrap value for steel |
Table: Sample Total Cost Comparison on Major Metrics
The above metrics make a strong case for choosing roll formed floor decks for large area projects due to substantial savings in time, cost and environmental impact.
FAQ
Q: What materials can use roll formed into floor decking?
A: Most common is galvanized steel coil feeds, but stainless steel, aluminum and other metal coils are also formed into corrugated decking sheets .
Q: Can floor deck roll forming lines make different profiles?
A: Modern OEM equipment allows tooling setups for different shapes like dovetail, trapezoidal and reentrant profiles within an hour using quick change roller stations.
Q: What thickness range is possible for floor decks?
A: Normal thickness range is 0.7mm to 2mm though some producers offer lighter or heavier gauges on request based on application structural needs.
Q: What parameters are monitored on a PLC control system?
A: PLC allows controlling and monitoring key parameters like line speed, sheet length counter, strip tension values, hydraulic pressure and allows troubleshooting faults.
Q: Does the machine require foundation or civil work?
A: A level concrete foundation as per OEM drawings is ideal. Otherwise floor needs to withstand machine loads and vibrations which affects accuracy.
Q: How much operator training is needed to run the machine?
A: A week of supervised hands-on operation by technicians during commissioning ensures operators understand the working principle and key aspects like strip feed, maintenance steps etc.
Q: What auxiliary equipment would be needed with the roll former?
A: Common additions like sheet stackers at the exit, sheet straighteners at entry, slitting machines to trim coil width are integrated for total floor deck production.
Q: What is the production capacity range possible?
A: Output depends on machine width, speed and operation duration. Typically 25,000 sqm to 100,000 sqm per month range is offered. Yearly capacity upto 500,000 sqm is possible.
Q: What is the warranty period provided?
A: OEM warranty normally covers one year. Extended warranty, AMC contracts after commissioning are advisable for continued support.