OEM double layer roll forming machines are industrial equipment used to bend metal sheets into customized profiles. This comprehensive guide provides a detailed overview of double layer roll formers covering working principles, main components, design considerations, customization options, suppliers, installation, operation, maintenance and more.
What are OEM Double Layer Roll Forming Machines?
OEM double layer roll forming machines continuously bend and form metal coils into customized profiles with two layered sections. They create complex symmetrical and asymmetrical shapes by progressively rolling sheets through a series of roller dies.
Key highlights of double layer roll formers:
- Produce two-layer wall panel profiles in one forming process
- Deliver high production efficiency and accuracy
- Automated operation for mass production scenarios
- Ideal for roofing, walling, façade and gate manufacturing
- Enable inline punching, drilling and other secondary processing
- Fully customizable end-profiles based on application
Table 1: Types of OEM Double Layer Roll Formers
Type | Description |
---|---|
Standard | Basic machine for general double layer profiles Fixed forming and processing modules |
Customized | Tailored configuration per profile design Interchangeable forming sections |
PLC Control | Touchscreen and PLC automation Monitoring, troubleshooting and parameter control |
Servo Motor | Advanced servo motor drive system Precise speed/tension control, quick roll changes |
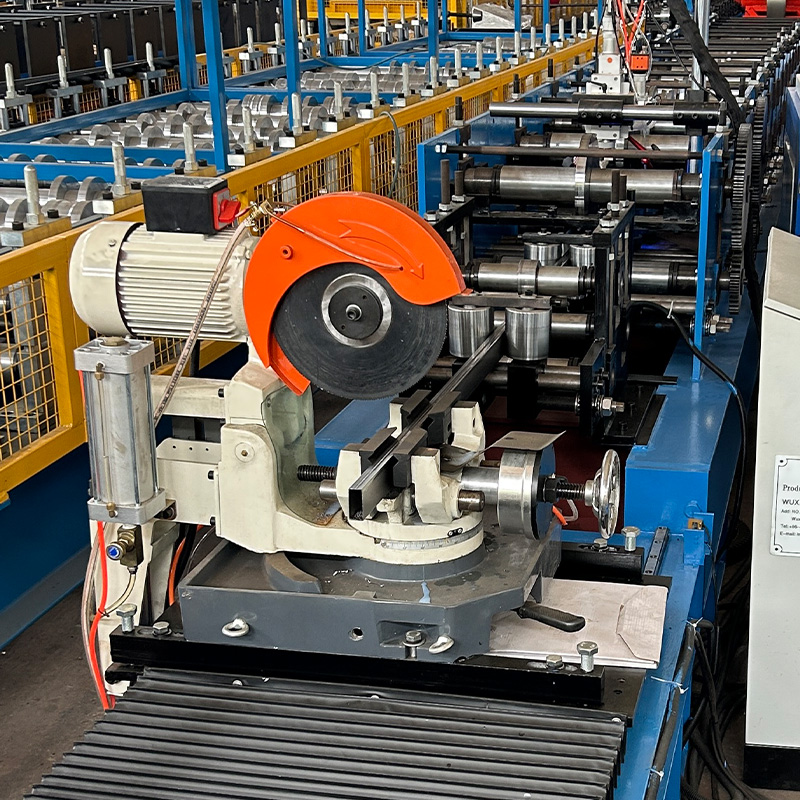
How Do Double Layer Roll Forming Machines Work?
Double layer roll formers bend and cut metal strips to create two separate C or U channels in one forming operation. They then bring together and interlock the channels to produce hollow, rigid profiles.
The step-by-step working process is outlined below:
- Material Feeding: Coiled raw material loaded onto a de-coiler which feeds into the forming sections at a controlled speed and tension.
- Pre-processing: Sheet goes through a series of punching, drilling, notching and embossing dies to add features.
- Primary Forming: The strip gets formed into a C or U shape using horizontal and vertical rolls.
- Secondary Forming: Separate set of rolls create a second C/U channel moving synchronously.
- Profile Joining: The two formed channels brought together and interlocked to create hollow final profile.
- Post-processing: Additional inline processes done like hole punching or embossing on final profile.
- Cutting: Profile cut to specified lengths by built-in cutoff press or flying shear system.
- Stacking: Conveyors transfer cut profiles for automatic stacking before final inspection.
Table 2: Main Components of Double Layer Roll Forming Machines
Component | Description |
---|---|
De-coiler | Feeds raw material into line from coils |
Variable speed drives | Controls material speed into the forming sections |
Punching units | Create holes or slots on the strips |
Forming rolls | Progressively bend metal sheet into C/U channels |
Joining Bridge | Brings together two formed channels and interlocks them |
Flying shear/Cutoff shear | Cuts final profile to length |
Hydraulic system | Applies precision pressure to forming rolls |
Control panel | Houses PLC and HMI for controlling devices |
Conveyor system | Transfers cut profiles for stacking/bundling |
Key Design Aspects and Customization
Double layer roll formers can be fully tailored to produce custom profiles based on specifications:
Table 3: Customization Options for OEM Double Layer Roll Forming Machines
Factor | Design Choices |
---|---|
Material type | Mild steel, stainless steel, aluminum etc. |
Material thickness | 20 gauges to 5 mm |
Profile dimensions | Per application standards |
Layer symmetry | Symmetrical/asymmetrical shapes |
Embossing patterns | Various aesthetic effects |
Processing tools | Punching, drilling, tapping, notching, deburring etc. |
Secondary operations | Corner welding, stud welding, spray painting etc. |
Length tolerance | As per precision requirements |
Debugging tools | Linear encoder, PLC data monitoring etc. |
Climate specifications | General, humid, coastal, desert etc. |
The profile design process involves:
- Finalizing product drawings and 3D models
- Calculating length of strip needed for each shape
- Mapping sequence of roller dies to achieve progressive bends
- Determining punching design, shear placement etc.
- Simulating forming process using software
- Building and testing tooling on sample materials
- Refining machine configuration for mass production
- Options like servo motor drives for quick roll changes
Choosing OEM Double Layer Roll Former Suppliers
Many heavy machinery manufacturers offer customizable double layer roll forming lines:
Table 4: OEM Double Layer Roll Former Manufacturers
Company | Location | Contact |
---|---|---|
SUNWAY | China | web: www.rollformingmachine.com email: [email protected] |
FONNTAI | China | web: fontai.cn email: [email protected] |
Shanghai Metal Corporation | China | web: www.shanghaimetal.com email: [email protected] |
ZHENGGONG | China | web: www.zgrollformingmachine.com email: [email protected] |
Key factors to evaluate potential suppliers on:
- Years of experience
- Domain expertise
- Design consultation process
- Flexibility for customization
- Tooling development capabilities
- Production capacity
- International quality certifications
- Scope of after-sales support
Table 5: Price Range of OEM Double Layer Roll Formers
Speed (m/min) | Forming Capability (mm) | Layers | Approximate Price Range |
---|---|---|---|
5 – 10 | 1.5 – 2.5 | Double layer | $30000 – $50000 |
10 – 40 | 1.5 – 3 | Double layer | $40000 – $80000 |
40 – 80 | 2.5 – 4 | Double layer | $50000 – $100000 |
Pricing varies based on factors like capacity, automation level, secondary processing capability etc.
-
Highway Guardrail End Terminal Forming Machine
-
Highway U/C Post Roll Forming Machine
-
2 Waves Highway Guardrail Roll Forming Machine
-
3 Waves Highway Guardrail Roll Forming Machine
-
C Section Bracing Omega Storage Rack Upright Post Roll Forming Machine
-
Steel Box Plate Making Roll Forming Machine
-
Box Beam Steel Roll Forming Machine For Shelf Column
-
Pallet Racking Step Beam P Beam Roll Forming Machine
-
Warehouse Shelf Upright Roll Forming Machine
Installation and Implementation
Installing an OEM double layer roll former requires extensive pre-planning:
Table 6: Roll Former Installation Procedure
Stage | Actions |
---|---|
Site Preparation | Ensure adequate space, level concrete floors to take heavy loads <br> Set up power supply lines, hydraulic piping, compressed air etc. |
Unpacking | Unload machine modules safely with cranes avoiding damage |
Position Alignment | Assemble sections perfectly aligned to each other to prevent skew |
Levelling | Precision levelling of entire line very important for proper material flow |
Commissioning Trials | Initial test runs with multiple adjustments to hydraulic pressure etc. |
Trial Production | Vary operating factors and fine tune for achieving design quality parameters <br> Observe deformations, thickness variations, twisting and rectify |
Final Alignment Check | Recheck alignment of de-coiler, roll stations, cutoff shear etc. |
Apart from mechanical factors, the forming quality depends heavily on:
- Sheet metal properties like hardness, rigidity, internal stresses etc. affecting response to rolling loads
- Surface preparation to enable smooth low-friction material flow
- Lubrication quality and temperature uniformity
- Automated feedback loops for precision monitoring and control
Maintenance Practices
Like any heavy machinery, regular preventive maintenance improves longevity and performance of double layer roll formers:
Table 7: Maintenance Schedule for Double Layer Roll Forming Machines
Frequency | Activities |
---|---|
Daily | Visual inspection of roll bearings, fluid levels Verify fastener tightness Monitor drive system temperature |
Weekly | Thorough cleaning of roll surfaces, scrapers Inspect key mechanical synchronizations |
Monthly | Lubricate bearings, gearboxes, shafts Calibrate sensors and gauges |
Quarterly | Check flatness of levelling pads Repair worn out roll bearings/rollers |
Yearly | Complete re-alignment checks Varnish electrical cabinets to prevent rusting Training programs for employees on safety procedures |
Proper storage of unused tooling also prevents deterioration when changing profiles frequently.
Key maintenance tips:
- Schedule downtime maintenance with production planning
- Ensure sufficient spares inventory
- Keep historical log of parameter changes
- Upgrade hydraulic, coolant and filtration systems
- Automate condition monitoring and diagnostics
- Treat as capital investment with continuous improvements
Operating Principles
Operators need training for working safely with OEM double layer roll formers:
Table 8: Operating Guidelines for Roll Forming Machines
Steps | Description |
---|---|
Safety Gear | Wear gloves, ear protection, covered shoes at all times |
Lockout/Tagout | De-energize all circuits before physical intervention |
Material Loading | Use proper equipment for lifting heavy coils |
Threading | Carefully pass strip through without scratches or buckles |
Startup Sequence | Turn auxiliary motors on first before engaging drive |
Idle Running | Let reach operating temperature; check for abnormalities |
Speed Control | Gradually accelerate to production speed monitoring strip flow |
Visual Monitoring | Observe strip scrolling for defects or deviations |
Parameter Changes | Vary factors like roller pressure/balance slowly |
Emergency Shutdown | Regularly test all stop and safety circuits |
Key operating principles:
- Allow proper machine warmup cycles during startup and after prolonged stops
- Ensure heads of fasteners are properly positioned before applying drive power
- Have detailed operating manuals from supplier onsite for reference
- Collect production quality data in standard formats for analysis
- Follow recommended parameters for lubrication, temperature zones etc.
- Maintain tidy work-space and steady material supply flows
Pros and Cons of Double Layer Roll Forming Machines
Table 9: Advantages of double layer roll forming process
Benefits | Details |
---|---|
High production rate | Up to 100 m/min with automated stacking |
Superior strength profiles | Double layers provide better reinforcement |
Built-in stiffeners | Interlocks between channels enhance rigidity |
Material savings | Less overlap and wastage during forming |
Shape intricacy | Capable of asymmetric and unconventional forms |
Secondary processing | Inline hole punching, notching possible |
Dimensional accuracy | Consistent tolerance control via automation |
Operator safety | Closed forming modules guard rotating parts |
Table 10: Limitations of double layer roll forming process
Drawbacks | Details |
---|---|
High tooling costs | Specialized roller dies needed for each profile |
Skilled labor for maintenance | Troubleshooting forming issues requires expertise |
Potential twisting | Improper joining can skew final shape |
Expensive changes | Significant rework for new profiles |
Floor-space requirements | Limitations for extremely long machines |
Limited bend radii | Restricts severely curved designs |
Noise hazards | Precautions needed against acoustic impacts |
While the double layer roll forming process has some inherent restrictions, OEM manufacturers continue to incorporate advanced servo control, quick-change tooling and monitoring sensors to mitigate limitations.
Applications of OEM Double Layer Roll Formed Profiles
Double layer roll forming technology enablesfolded metal structures ideal for:
Cladding and Wall Elements: Multi-layer wall panels, built-up roofing sheets etc.
Structural Framing: Lightweight purlins, channels, equipment racks used extensively in prefab buildings, solar mounts etc.
Furniture: Chairs, shelves, racks, lockers and storage units etc. gain durability.
Automotive: Railway carriage framing, truck body panels, commercial vehicle floors and compartments etc. benefit from interlocked hollow strength.
Storage Infrastructure: Warehouse partitions, mezzanine flooring, silo linings use these cold roll formed sections.
Agricultural Infrastructure: Grain silos, greenhouse structures, animal husbandry shelters etc. employ interlocking wall and roof cladding profiles.
Domestic Appliances: Air conditioner chassis, refrigerator panels etc. apply double layer frames.
Customized Gates and Railings: Ornamental entrance gates combine aesthetics along with intrusion resistance.
Multilayer roll formed components serve lightweight, high-strength demands across manufacturing industries.
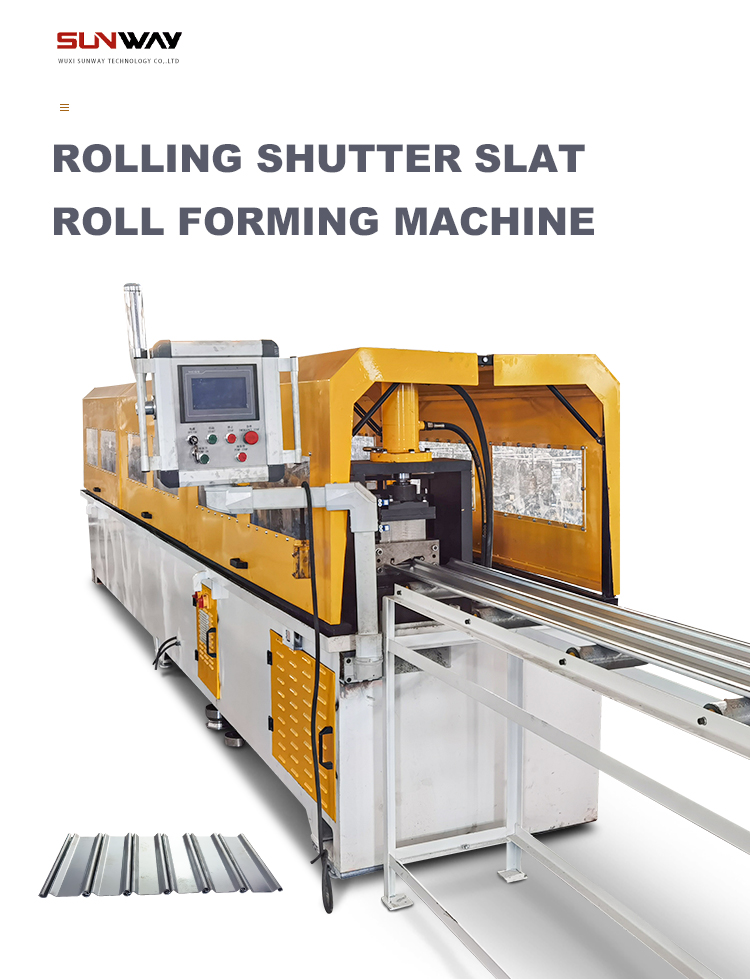
Frequently Asked Questions
Q: What thickness of sheets can be formed on double layer roll formers?
A: Standard machines accommodate material thickness from 0.7mm to 2.5mm. Heavy-duty lines go up to 8mm thickness. Customized tooling allows even thicker plates.
Q: How to decide appropriate production line speed?
A: Recommended operating speed falls between 10-100m/min depending on metal alloy type, thickness, desired product quality, and extent of secondary processing.
Q: What sheet metal types can be roll formed?
A: Mild steel is commonly used, but stainless steel, aluminum alloys, brass, copper etc. can also be easily formed. Special surface coatings or tempering may be required beforehand.
Q: What degree of profile customization is possible?
A: Complete custom profiles are possible matching 3D models. Limiting factors may be minimum bend radii, corner interlocks and avoiding shape distortions.
Q: Can standard catalog profiles be mass produced?
A: Yes absolutely. Standard window/door frames, roofing sheets, drywall profiles etc. can be mass produced at the highest volumes matching industry standards.
Q: How to minimize per piece cost for mass orders?
A: Automating stacking, bundling and integrating before downstream processes like welding/painting helps minimize cost by reducing manual labor significantly.
Q: What is the largest length that can be continuously formed?
A: Some leading manufacturers develop super-long machines exceeding 60 meters in forming length. But typically 25-30 meters is maximum before requiring special intermediate supports.
Q: How much space is required for installing these machines?
A: Approximate sizing guidelines:
- Length = Raw material supplier coil diameter + Machine length + Shearing buffers
- Width = Roll forming sections width + 1.5m minimum safe passageways on both sides
- Height = Tallest section height with 1m clearance
Provide 15-20% extra space for safe movement.