Introduction
When it comes to durable, weather-resistant, and aesthetically pleasing roofing solutions, metal roof panels have earned their place at the forefront. They offer unparalleled strength, longevity, and energy efficiency. In this article, we’ll delve into the world of metal roof panel roll forming machines, exploring their significance, benefits, types, features, and more.
Benefits of Metal Roof Panels
Metal roof panels have become a popular choice for commercial and residential properties alike. They offer exceptional benefits such as:
- Durability: Metal roof panels are built to withstand harsh weather conditions, including heavy rain, snow, and even hail.
- Longevity: These panels have a longer lifespan compared to traditional roofing materials, reducing long-term maintenance costs.
- Energy Efficiency: Reflective coatings on metal panels can help keep buildings cooler, leading to energy savings.
- Aesthetics: Metal roof panels come in various colors and profiles, providing versatility in design.
Understanding Roll Forming Machines
Roll forming machines are essential tools in the manufacturing process of metal roof panels. They shape flat metal sheets into the desired panel profile through a continuous bending process. This process ensures consistent quality and precision.

The Role of Metal Roof Panel Roll Forming Machines
Metal roof panel roll forming machines play a crucial role in the roofing industry. They allow for:
- Customization: These machines can create an array of panel profiles to suit different architectural styles.
- Efficiency: Roll forming machines can produce panels at high speeds, meeting project deadlines effectively.
- Cost Savings: The automated process minimizes labor costs and material wastage.
Types of Metal Roof Panel Roll Forming Machines
- Standing Seam Roll Forming Machine: This type of machine produces standing seam metal roof panels, which are known for their sleek appearance and concealed fasteners. Standing seam panels are characterized by vertical ribs and raised seams that interlock during installation. These panels are commonly used in commercial and residential applications.
- Corrugated Roll Forming Machine: Corrugated metal roof panels have a distinctive wavy pattern and are often used in agricultural, industrial, and residential settings. Corrugated panels are known for their strength and durability. The machine for producing corrugated panels forms the characteristic waves and shapes in the metal.
- IBR (Inverted Box Rib) Roll Forming Machine: IBR panels are widely used in commercial and industrial roofing due to their robustness and ability to handle water drainage effectively. The panels have an inverted box rib profile, which provides structural integrity and a clean appearance. IBR roll forming machines produce these panels with precision.
- Double Layer Roll Forming Machine: Double layer machines are capable of producing two different profiles of metal roof panels. This is useful when a project requires two different panel designs or sizes. The machine typically has two sets of roll forming tools to create the desired profiles.
- Snap-Lock Roll Forming Machine: Snap-lock panels are similar to standing seam panels, but they have a unique interlocking mechanism that allows the panels to snap together during installation, eliminating the need for mechanical seaming. Snap-lock machines form the panels with the necessary interlocking features.
- Tile Profile Roll Forming Machine: Tile profile metal roof panels mimic the appearance of traditional clay or concrete roof tiles while offering the benefits of metal roofing. These panels are popular in residential and commercial applications due to their aesthetic appeal and durability.
- C-Purlin and Z-Purlin Roll Forming Machine: While not exactly roof panels, C-purlins and Z-purlins are essential components of metal roofing systems. These roll forming machines produce purlins, which are horizontal support structures used in roofing and construction applications.
- Metal Deck Roll Forming Machine: Metal deck panels are used in composite steel deck roofing systems for multi-story buildings. These panels serve as both the structural support and the formwork for concrete floors. Metal deck roll forming machines create the profiles required for these panels.
- Curved Roof Panel Roll Forming Machine: For projects that require curved or arched metal roof panels, specialized curved roof panel roll forming machines are used. These machines can form metal panels to match specific architectural designs and curves.
- Accessories Roll Forming Machines: In addition to the main roof panels, there are various accessories that complement metal roofing systems, such as ridge caps, eave trim, flashing, and gutter components. Roll forming machines for these accessories ensure consistency in design and quality.
Key Features to Consider
When selecting a metal roof panel roll forming machine, certain features are crucial:
- Material Compatibility: Ensure the machine can handle the specific metal type and gauge you intend to use.
- Profile Versatility: Choose a machine that can produce various panel profiles.
- Automation Level: Decide between manual, semi-automatic, or fully automatic systems based on your production needs.
Advantages of Using Roll Forming Machines for Metal Roof Panels
- High Efficiency and Speed: Roll forming machines are designed for high-speed continuous production. They can process metal coils into finished roof panels in a single pass, minimizing the need for manual handling and reducing production time significantly.
- Consistent Quality: Roll forming machines ensure consistent and uniform dimensions, shapes, and profiles of the metal roof panels. This consistency in quality reduces the likelihood of defects and variations in the finished products.
- Versatility: Roll forming machines can produce a wide range of complex shapes and profiles for different types of metal roof panels. This versatility allows manufacturers to meet various design requirements and customer preferences.
- Cost-Effective: While the initial investment in a roll forming machine might be higher, the long-term operational costs are generally lower compared to other manufacturing methods. The high efficiency and minimal scrap generation contribute to cost savings over time.
- Minimal Material Waste: Roll forming machines generate minimal material waste during production. The design of the machine ensures efficient utilization of the raw material, reducing scrap and contributing to cost savings and environmental sustainability.
- Automation and Labor Savings: Roll forming machines are highly automated, requiring minimal operator intervention. This reduces the need for a large workforce, saving on labor costs and improving workplace safety by minimizing manual handling.
- Quick Setup and Changeover: Modern roll forming machines often come equipped with quick-change systems that allow for rapid adjustments and profile changes. This flexibility is crucial for accommodating different panel designs and minimizing downtime between production runs.
- Precision and Accuracy: Roll forming machines use precise tooling and guided forming processes to achieve accurate dimensions and tight tolerances. This precision results in high-quality metal roof panels that fit perfectly during installation.
- Scalability: Roll forming machines can be scaled up or down to accommodate different production volumes. This scalability makes them suitable for both small-scale and large-scale manufacturing operations.
- Reduced Manual Labor: The automated nature of roll forming machines reduces the reliance on skilled labor for complex bending and forming operations. This can help address the skilled labor shortage often encountered in traditional manufacturing methods.
- Low Maintenance: Roll forming machines are designed for durability and minimal maintenance requirements. This ensures consistent production over extended periods without frequent interruptions for maintenance.
- Flexibility in Material Selection: Roll forming machines can work with a variety of metals, including steel, aluminum, and copper, giving manufacturers the flexibility to choose the material that best suits their project requirements.
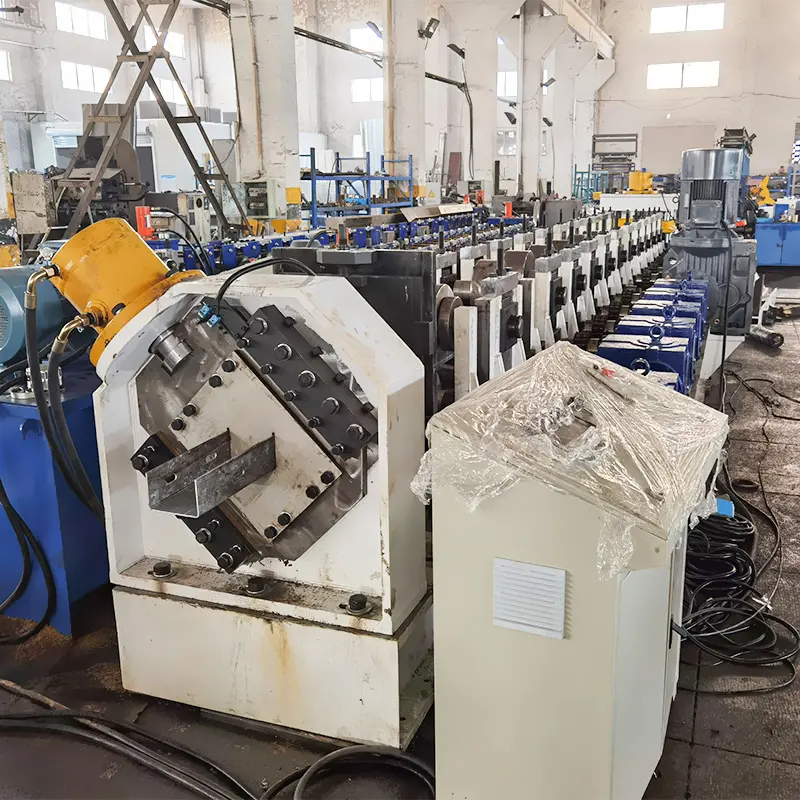
Factors to Consider When Choosing a Roll Forming Machine
Selecting the right roll forming machine requires attention to the following factors:
- Budget: Determine a suitable budget for your machine investment and operating costs.
- Space: Consider the available workspace for machine setup and operation.
- Maintenance and Support: Ensure the manufacturer offers reliable technical support.
Proper Maintenance and Care
To ensure the longevity of your metal roof panel roll forming machine:
- Regular Inspection: Periodically inspect the machine for signs of wear or damage.
- Lubrication: Keep all moving parts well-lubricated to prevent friction-related issues.
- Cleaning: Maintain a clean environment to prevent debris from affecting machine performance.
Industry Applications
Metal roof panel roll forming machines find applications in various industries:
- Construction: Providing roofing solutions for commercial and residential buildings.
- Agriculture: Creating durable structures for farm buildings.
- Automotive: Producing panels for automotive workshops and showrooms.
Future Trends in Metal Roof Panel Roll Forming
The roll forming industry is evolving, with trends such as:
- Advanced Automation: Integration of AI and robotics for enhanced efficiency.
- Green Initiatives: Developing eco-friendly materials and processes.
- Digitalization: Implementing data-driven practices for better production control.
Case Study: Successful Implementation
Explore a case study showcasing the successful implementation of a metal roof panel roll forming machine, highlighting the benefits reaped by the company.
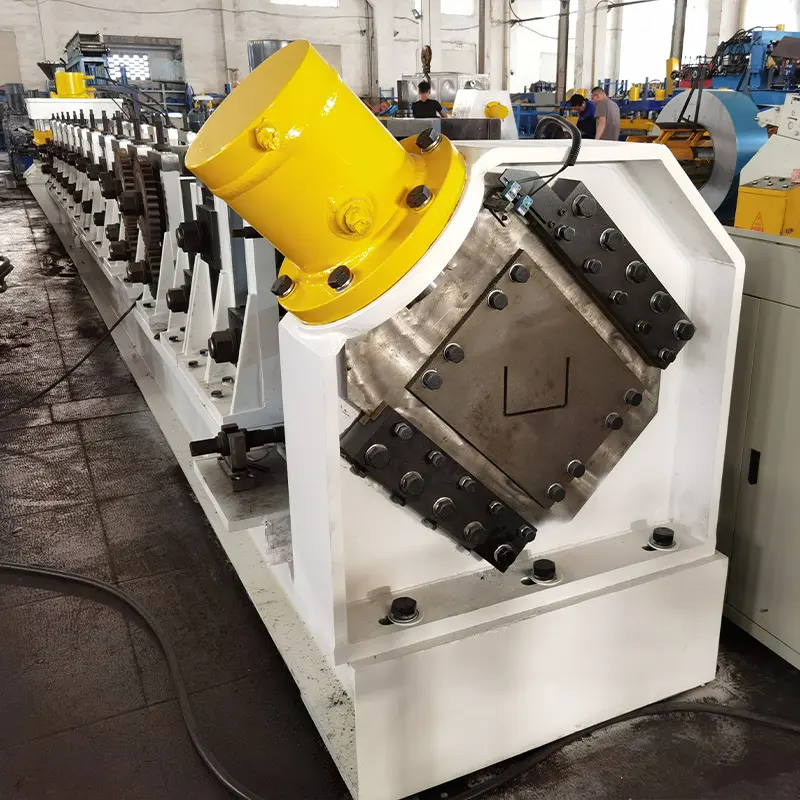
Conclusion
In conclusion, metal roof panels are a reliable and aesthetically pleasing roofing solution. Metal roof panel roll forming machines play a pivotal role in their production, enabling efficient, precise, and cost-effective manufacturing. Choosing the right machine and providing proper maintenance are essential for long-term success in the roofing industry.
FAQs
- What materials are commonly used for metal roof panels? Metal roof panels are often made from steel, aluminum, copper, or zinc.
- Are metal roof panels suitable for all types of climates? Yes, metal roof panels are highly durable and can withstand a wide range of climates.
- Can roll forming machines create custom panel designs? Yes, roll forming machines can produce a variety of custom panel profiles.
- What is the typical lifespan of metal roof panels? Metal roof panels can last 40 years or more, depending on the material and maintenance.
- Are roll forming machines suitable for small-scale production? Yes, there are roll forming machines designed for various production scales, including small-scale operations.