Overview
Roll forming is an efficient, continuous process for forming light steel sections like studs, battens, roofing, decking, panels and other profiles from coiled sheet. Automated light steel roll forming lines provide high productivity and precision in producing structural framing members and architectural cladding products.
This guide covers the working principles, main components, configurations, specifications, manufacturers, costs, installation, operation and maintenance for modern light steel roll forming equipment. Helpful comparison tables summarize technical details to assist buyers in selecting the right roll former.
Investing in automated light steel roll forming systems allows manufacturers to boost speed, quality consistency and labor productivity. By understanding the technical factors involved, producers can choose equipment matched to their output needs.
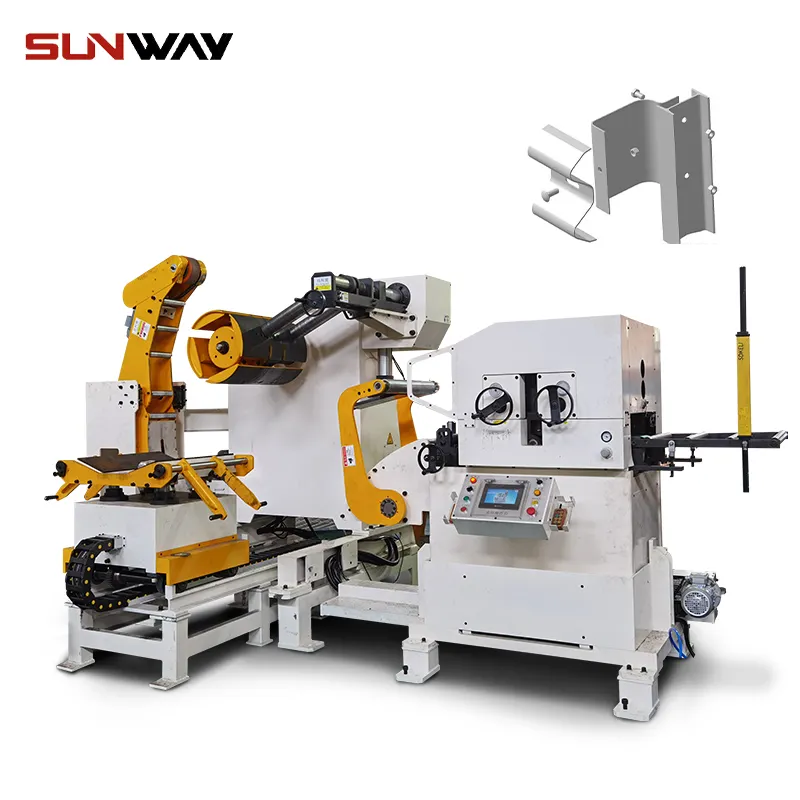
Light Steel Roll Former Machine Types
Roll formers for light steel products are available in several standard configurations:
Light Steel Roll Former Machine Types
Machine Type | Description | Typical Output | Main Components |
---|---|---|---|
Inline roll former | Stations arranged in a straight line | Up to 16 pieces/min | Uncoiler, punch, rolls, cutoff |
Orbital roll former | Forming stands positioned in an oval | Up to 10 pieces/min | Uncoiler, rolls, cutoff, exit conveyor |
Shuttle roll former | Shuttles feed sheet incrementally | Up to 20 pieces/min | Uncoiler, shuttle, rolls, cutoff |
Wheel roll former | Rolls mounted on rotating wheel | Up to 5 pieces/min | Coil carousel, wheel with rolls, cutoff |
Higher production speeds possible with custom machine design and multistation capabilities.
Working Principle
Roll formers shape flat steel strip into structural sections by incrementally bending the material through a series of stations:
Light Steel Roll Forming Process Steps
- Uncoiling – Sheet coil is unwound and entered into the line
- Feeding – Powered rolls advance the strip
- Punching – Holes punched if needed
- Forming -Contour rolls progressively shape the profile
- Cutting – Formed section cutoff to length by shear
- Exit – Conveyor collects finished parts
Precise servo electric actuation coordinates the material feed, punching and cutoff motions.
Key Machine Components
Common components of light steel roll forming lines include:
Main Components of Light Steel Roll Forming Machines
- Decoiler or uncoiler
- Feed tables with pinch rollers
- Punching die stations (optional)
- Forming roll stands
- Rotary or guillotine cutoff shear
- Exit tables and part stackers
- PLC control system and HMI
- Safety guarding and fencing
Machines are designed for high duty cycle operation during large volume production runs.
Forming Capabilities
Typical light steel profiles produced on roll forming equipment:
Light Steel Profiles Formed on Roll Forming Lines
- Stud wall framing members
- Metal roofing panels
- Wall girts and roof purlins
- Floor joists and rafters
- Drywall track and studs
- Architectural fascia and cladding
- Solar panel frames
- Storm shelters and safe rooms
- Agricultural building parts
Interchangeable roll sets allow producing different structural sections by changing tooling.
Configuring Roll Stations
Careful roll design and positioning are required to achieve the desired profile:
Roll Forming Line Configuration Factors
- Number of progressive bending stations
- Bend angle and location at each station
- Material type, thickness and hardness
- Controlling material springback
- Positioning of punching stations
- Rolls precision ground to specifications
- Roll densification and sizing
- Lubrication of rolls and strip
The force applied by each roll must be balanced across stands. Complex programming coordinates the sequential timing.
Customization Options
Light steel roll formers can be customized via:
Customization Options for Light Steel Roll Forming Lines
- Infeed and exit conveyor lengths and designs
- Single or dual payoff reel configurations
- Additional punching or hole piercing stations
- Quick roll change capability
- Safety guarding and fencing
- Communication interfaces and data logging
- Powered section shears and bundlers
- Custom section designs and tooling
- Integration with downstream operations
Experienced suppliers can provide optimized solutions tailored for specific production scenarios.
Light Steel Roll Former Specifications
Typical technical specifications for light steel roll forming machines:
Light Steel Roll Former Machine Specifications
Parameter | Typical Range |
---|---|
Forming speed | 16 – 65 ft/min |
Drive power | 3 – 7.5 HP |
Material thickness | 26 – 16 gauge (0.5 – 1.5 mm) |
Material type | Low carbon steel, stainless steel, aluminum |
Width capacity | 1.5 – 14 inches |
Length capacity | 10 – 40 feet |
PLC control | Allen-Bradley, Siemens, Mitsubishi |
Weight | 1500 – 8000 lbs |
Specifications depend on production volumes, material sizes, options and line configuration.
Light Steel Roll Former Manufacturers
Leading global suppliers of light steel roll forming equipment include:
Light Steel Roll Former Manufacturers
Company | Location | Equipment Types |
---|---|---|
Form Process Engineering | USA | Specialists in light steel roll formers |
Metform | International | Complete roll forming lines |
Formtek | USA | Precision light steel roll formers |
Gensco Equipment | USA | Light duty roofing, flooring and wall panel lines |
DahChyang Machinery | Taiwan | Value engineered roll forming |
Rollvis | France | Roofing panel lines and cutoff saws |
Look for extensive roll forming experience with light steel when selecting suppliers. Evaluate production speeds, flexibility, and robustness.
Light Steel Roll Former Costs
Turnkey automated light steel roll former system costs range:
Light Steel Roll Former Price Ranges
Machine Type | Typical Price Range |
---|---|
Light-duty infeed roll former | $50,000 – $150,000 |
Medium-duty exit roll former | $80,000 – $200,00 |
Heavy-duty cutoff roll former | $120,000 – $350,000 |
High-speed cutoff roll former | $200,000 – $500,000 |
Pricing depends on speed, power, material width, and features. Quotes from several suppliers are recommended.
Roll Forming Machine Installation
Proper foundations, space, and utility connections are required:
Light Steel Roll Former Installation Needs
- Reinforced concrete flooring with good drainage
- 3 phase electrical supply and 480V connection
- Compressed air line with filtration
- Enough linear space for machine plus infeed and exit tables
- Material loading capability – overhead crane or coil lift
- Ceiling height for coil loading and conveyors
- Climate control for consistent material properties
Work closely with your supplier to prepare the installation site and connections.
Maintenance of Light Steel Roll Formers
Consistent maintenance maximizes production uptime:
Light Steel Roll Former Maintenance Best Practices
- Daily cleaning of rollers and material path
- Lubricating bearings, chains, guides and moving parts
- Monitoring belt tension and hydraulic pressures
- Inspecting controls, wiring and connections
- Verifying roll alignment and adjustment
- Following recommended preventative maintenance schedule
- Promptly replacing any damaged or worn components
- Keeping spare parts inventory on hand
Thorough training of personnel on proper operation, safety, cleaning and maintenance is critical.
Buying Considerations for Light Steel Roll Formers
Key factors to consider when purchasing roll formers:
- Annual production volume targets by product
- Variety of structural profiles to be produced
- Material specifications like thickness, width and grade
- Standard vs custom profile requirements
- Line speed and feed rate needs
- Operator skill level and maintenance expertise
- Available installation space and layout
- Total budget expectations and ROI goals
- Options for future expansions or modifications
Getting expert input from an experienced supplier simplifies the equipment selection process.
Benefits of Light Steel Roll Forming Machines
Advantages of Automated Light Steel Roll Formers
- High production speeds and consistency
- Ability to run lights out with minimal supervision
- Handles a range of structural section geometries
- Reduced labor compared to manual fabrication
- Adaptable to future profile design changes
- Lower material waste versus other bending methods
- Scales easily from pilot to full production
Automated roll forming standardizes output quality and reduces costs.
Limitations of Light Steel Roll Forming Machines
Limitations of Automated Light Steel Roll Formers
- Large initial capital expenditure required
- Permanent factory floorspace footprint
- Single purpose equipment with limited material/profile flexibility
- Skilled maintenance and operation required
- Potential bottlenecks around cutoff and secondary operations
- Significant changeover time between different profiles
- Long lead times for engineering and build
- Hard tooling modifications needed for design changes
Roll formers have fixed material and profile range once built.
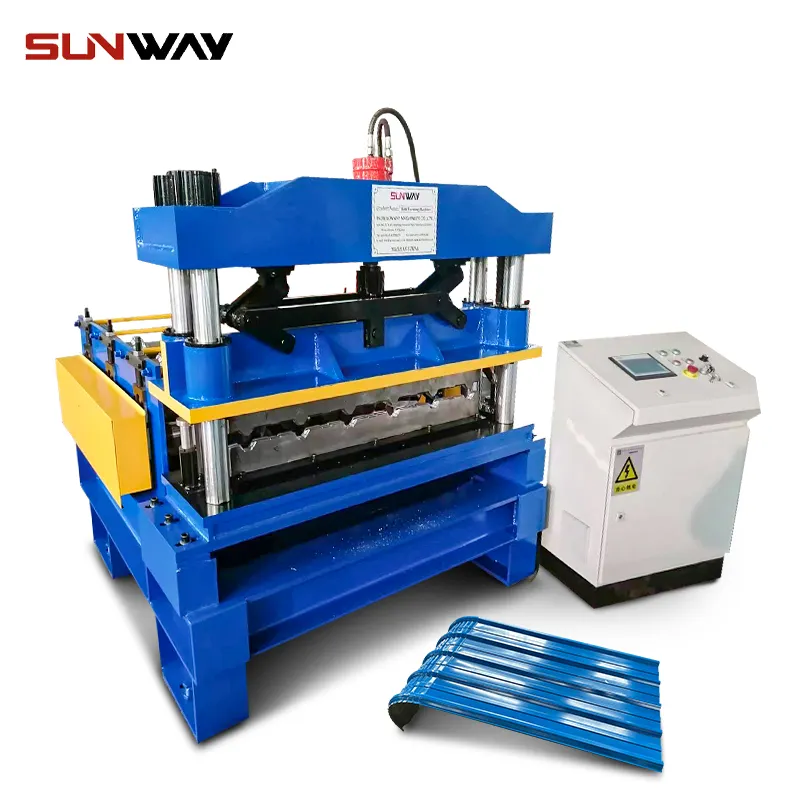
FAQs
What thickness range can be reliably roll formed?
Standard gauges from 16 gauge (1.6 mm) to 26 gauge (0.5 mm) can be formed on most roll formers. Specialized machines handle up to 3/16″ (4.8 mm) plate.
How long does it take to changeover to a new profile?
With tooling staged and machine preparations complete, typical profile changeover takes 30-60 minutes. Complex changes require more time.
What determines the maximum forming speed?
Main constraints are material thickness, number of bending stations, overall machine length, and cutoff method. More stations and thicker material restrict feed rate.
How often do roll forming rollers need replacement?
Sharpening or replacement is typically needed every 4-6 months depending on hours run and maintenance. Better roll materials, coatings and lubrication extend service life.
Can a roll former make creative tapered or curved profiles?
Yes, specialized machine designs with articulating heads or swirling stands can produce tapered, conical or helical formed sections.
How should I handle and store roll formed parts after production?
Banding bundles together, using protective end caps, and keeping dry helps maintain straightness. Avoid outside storage which can lead to corrosion.
Conclusion
Automated light steel roll forming machines improve efficiency, throughput and consistency for high volume structural section production. Their flexible and scalable configurations form diverse profiles from coiled steel. By understanding the technical considerations, manufacturers can invest in light steel roll forming systems that boost productivity versus manual methods. Ongoing advances in changeover, automation and roll design continue to expand adoption across many industries.