Are you considering galvanized tin roofing for your next project? Maybe you’ve heard it’s durable, cost-effective, and offers that sleek metallic look. But, there’s so much more beneath the surface! Whether you’re a homeowner, builder, or architect, this guide breaks down everything from what galvanized tin roofing is, the specific materials involved, to the best installation methods and even supplier selection. Dive into this in-depth discussion on galvanized tin roofing, and by the end, you’ll be an expert ready to make an informed decision.
Overview of Galvanized Tin Roofing
Galvanized tin roofing is a popular choice for many construction projects, offering a balance between cost, durability, and performance. Essentially, galvanized roofing is made of steel or iron coated with a layer of zinc to prevent rust and corrosion. The term “tin” is often used colloquially, but in reality, it refers to a thin layer of zinc that protects the base metal from exposure to the elements.
Key Benefits of Galvanized Tin Roofing:
- Rust Resistance: Thanks to the zinc coating, galvanized metal resists rust, extending its lifespan.
- Durability: It stands up to harsh weather conditions, including heavy rain, snow, and wind.
- Cost-Effective: It’s one of the more affordable metal roofing options compared to alternatives like copper or aluminum.
- Versatile Design: Available in different styles and finishes to suit various architectural designs.
Now, let’s explore the details—starting with how these roofing sheets are formed.
Corrugated Galvanized Tin Roofing: The Go-To Sheet Guide
One of the most iconic looks of metal roofing is the corrugated galvanized tin sheet. The corrugation process gives the sheet added strength and flexibility while maintaining its lightweight nature. These sheets are highly recognizable due to their wavy pattern and are available in various thicknesses and dimensions.
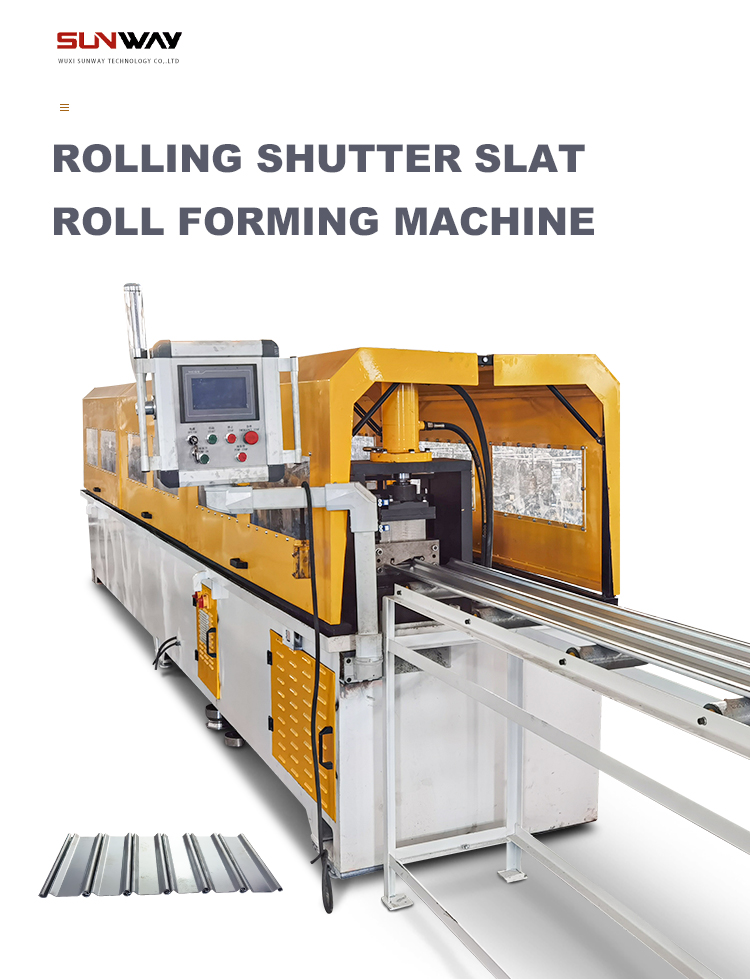
How Corrugation Enhances Roofing Strength
The corrugated design distributes weight and pressure evenly across the surface of the sheet. This feature makes them especially beneficial in regions prone to heavy rainfall or snow, as the water slides off easily. Corrugated sheets come in several profiles, including wave, box, and trapezoidal designs.
Popular Corrugated Galvanized Tin Models
Model Name | Description | Thickness (mm) | Width (mm) | Coating Type |
---|---|---|---|---|
CGI-100 | Standard corrugated sheet with wave profile. Ideal for general roofing applications. | 0.4 – 0.7 | 750 – 1000 | Hot-dip galvanized |
Box-Lite 200 | Features box-shaped corrugation, providing extra durability and strength in windy regions. | 0.45 – 0.8 | 850 – 1200 | Electro-galvanized |
WavePlus 350 | Offers deeper wave patterns for superior water runoff, perfect for high rainfall areas. | 0.5 – 0.9 | 700 – 950 | Hot-dip galvanized |
TrapZinc-500 | Trapezoidal profile for modern aesthetics and enhanced rigidity, common in industrial buildings. | 0.55 – 1.0 | 800 – 1000 | Hot-dip galvanized |
These sheets are only the beginning. Let’s dive into the working process and how galvanized tin roofing is produced.
The Working Process Behind Galvanized Tin Roofing
Producing galvanized tin roofing involves several key steps, each crucial to creating a durable and weather-resistant product.
Step-by-Step Manufacturing Process:
- Base Metal Preparation: The process begins with a steel or iron base, typically in the form of large coils. These metals are selected for their strength and malleability.
- Cleaning: The base metal is cleaned thoroughly using an alkaline solution to remove any impurities or oxides that could hinder the coating process.
- Galvanization: The cleaned metal is dipped into a bath of molten zinc, a process known as “hot-dip galvanization.” This step forms a protective layer over the metal surface.
- Cooling: After galvanization, the metal is cooled to harden the zinc coating, creating a resilient outer layer that shields the metal from rust and corrosion.
- Corrugation: The galvanized sheet is then passed through rollers that create the desired wave, box, or trapezoidal corrugated profile.
- Cutting: Finally, the sheet is cut to standard lengths, usually between 6 to 12 feet, though custom lengths are available for special projects.
Components and Their Functions in Galvanized Tin Roofing
Component | Function |
---|---|
Zinc Coating | Protects the steel from corrosion and rust. |
Base Metal (Steel) | Provides the structure and strength necessary to withstand weather and physical impacts. |
Corrugation | Enhances structural integrity by evenly distributing weight and preventing water pooling. |
Paint Finish (Optional) | Offers extra aesthetic appeal and additional protection against UV rays and corrosion. |
Fasteners and Screws | Ensure secure attachment to the roofing frame, preventing uplift during windstorms. |
Efficiency and Speed in Galvanized Tin Roofing Installation
When choosing roofing materials, it’s essential to consider not only the durability of the material but also how efficient and quick the installation process is. Galvanized tin roofing, particularly corrugated types, scores highly on ease of installation.
Machine Efficiency and Roofing Speed Comparison
Installation Machine/Tool | Efficiency Rating | Installation Speed (Sq. Meters per Hour) | Remarks |
---|---|---|---|
Manual Screwdriver | Low | 5 – 10 | Suitable for small DIY projects, but slow for large roofs. |
Electric Drill | Medium | 20 – 40 | Faster than manual but can lead to inaccuracies if not handled carefully. |
Automatic Fastener Machine | High | 50 – 100 | Best for large projects, ensures uniform attachment and speed. |
-
Carriage Board Roll Forming Machine
-
Highway Guardrail End Terminal Forming Machine
-
Highway U/C Post Roll Forming Machine
-
2 Waves Highway Guardrail Roll Forming Machine
-
3 Waves Highway Guardrail Roll Forming Machine
-
C Section Bracing Omega Storage Rack Upright Post Roll Forming Machine
-
Steel Box Plate Making Roll Forming Machine
-
Box Beam Steel Roll Forming Machine For Shelf Column
-
Pallet Racking Step Beam P Beam Roll Forming Machine
Customized Parameters for Galvanized Tin Roofing Sheets
Depending on the specific project requirements, galvanized tin sheets can be customized in terms of thickness, coating type, and profile shape.
Parameter | Options Available | Remarks |
---|---|---|
Thickness | 0.3mm to 1.2mm | Thicker sheets offer better durability but are heavier. |
Coating Thickness | 60gsm to 275gsm | Higher coatings increase corrosion resistance. |
Sheet Length | Custom lengths up to 12 meters | Longer sheets minimize joints, reducing leak risks. |
Profile Type | Wave, Box, Trapezoidal | Different profiles suit different architectural aesthetics and load-bearing needs. |
Where to Use Galvanized Tin Roofing? Common Applications
Galvanized tin roofing isn’t just for barns and sheds anymore! Its versatility makes it ideal for a wide range of applications:
Application | Details |
---|---|
Residential Homes | A sleek modern look, long-lasting, and energy-efficient. Suitable for both modern and rustic designs. |
Industrial Buildings | Durability and low maintenance make it a favorite for warehouses and factories. |
Agricultural Buildings | Popular for barns, silos, and livestock sheds due to its weather resistance and low cost. |
Commercial Spaces | Adds an industrial aesthetic to offices, retail spaces, and restaurants. |
Pergolas and Carports | Provides shade and protection with minimal weight. |
Installation, Operation, and Maintenance Guide for Galvanized Tin Roofing
When it comes to installation and upkeep, galvanized tin roofing is relatively low-maintenance, but it still requires some care to ensure longevity.
Aspect | Details |
---|---|
Installation | Requires a solid framework underneath. Can be installed using screws or nails with rubber washers to ensure a watertight seal. |
Operation | Minimal upkeep required; the zinc coating protects against rust, and its smooth surface reduces debris build-up. |
Maintenance | Regular cleaning with mild detergent and water is recommended. Inspect screws and fasteners periodically to prevent loosening. |
How to Choose the Right Supplier for Galvanized Tin Roofing
Choosing a supplier can be tricky, especially with so many options available. Here are some factors to consider when making your decision:
Factor | What to Look For |
---|---|
Price Range | Compare costs, but don’t sacrifice quality for price. Average costs are between $5 and $10 per square foot. |
Reputation | Check customer reviews and ask for recommendations from professionals in the industry. |
Product Range | Look for suppliers who offer a variety of profiles and thicknesses. |
Delivery Time | Ensure the supplier can meet your project deadlines, especially if you’re ordering custom lengths or profiles. |
Warranties and Guarantees | A good supplier will offer a warranty on both the material and coating. |
Comparing the Pros and Cons of Galvanized Tin Roofing
Before you settle on galvanized tin roofing, it’s essential to weigh the advantages and limitations to ensure it’s the right fit for your project.
Pros
- Durability: With the added protection of zinc, galvanized tin roofing can last 30-50 years.
- Cost-Effective: It’s one of the more affordable metal roofing options.
- Versatility: Available in various profiles and colors, suitable for different architectural designs.
- Low Maintenance: Requires minimal upkeep thanks to the self-healing properties of zinc.
Cons
- Weight: Galvanized steel can be heavier compared to other metal roofing materials like aluminum.
- Aesthetic Limitations: Some people prefer the look of more premium metals like copper or natural materials like tile or slate.
- Noise: During rainstorms, metal roofs can be louder than other types of roofing materials unless additional insulation is used.
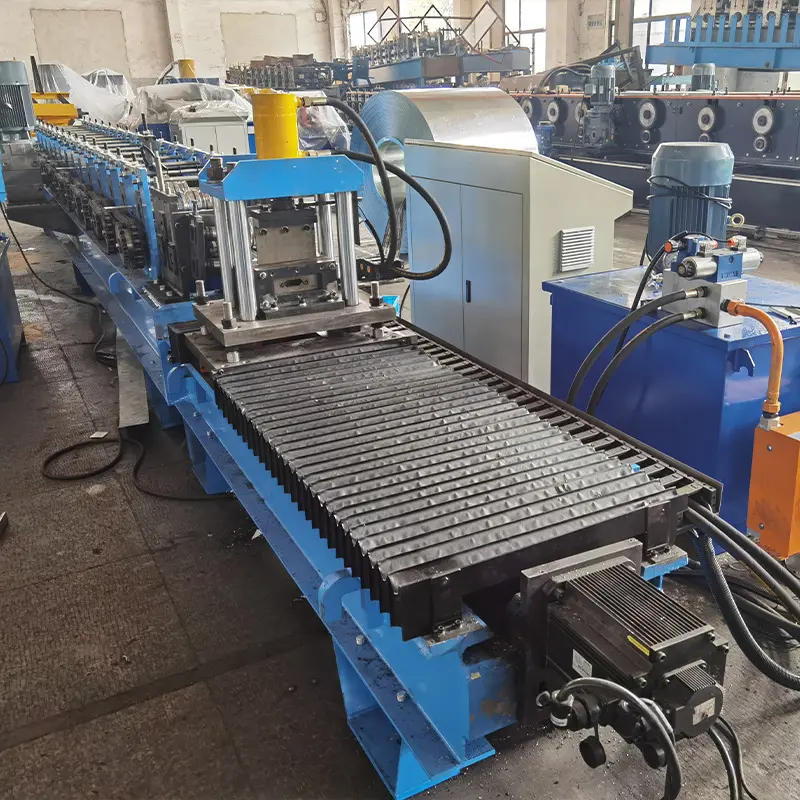
FAQ
Question | Answer |
---|---|
How long does galvanized tin roofing last? | Typically between 30-50 years, depending on environmental factors and maintenance. |
Is galvanized tin roofing noisy? | Yes, metal roofs can be noisy during rainstorms, but insulation can help reduce the noise. |
How does galvanized tin roofing compare to aluminum? | Galvanized tin is stronger and more durable, but heavier. Aluminum is lighter and more corrosion-resistant in coastal areas. |
Can galvanized tin roofing rust? | No, the zinc coating prevents rust. However, over time, if the coating wears away, rusting can occur. |
Is it easy to install galvanized tin roofing? | Yes, with the right tools and equipment, it’s a relatively easy DIY project for experienced builders. |
Does galvanized tin roofing need to be painted? | It doesn’t need to be, but adding a paint finish can enhance aesthetics and provide extra UV protection. |
Conclusion
Galvanized tin roofing offers a blend of affordability, durability, and versatility that few other roofing materials can match. Whether you’re roofing a home, barn, or commercial building, its rust resistance and long-lasting nature make it a top choice. By understanding the different types available, the installation process, and the suppliers, you can make an informed decision that meets both your budget and design needs.