Galvanized corrugated metal is an integral part of modern construction, known for its durability, strength, and corrosion resistance. But if you’re reading this, chances are you’re not just looking for a textbook definition. You want to know exactly what makes this material tick—what are its real-world applications, how it’s made, and what sets one model apart from another. Maybe you’re even considering using galvanized corrugated metal for a project and want to dive deep into the options available.
In this article, we’ll walk you through everything you need to know about galvanized corrugated metal. We’ll break down the types available, how it’s manufactured, and why it might be the perfect solution for your project. And yes, we’ll dive into some nerdy technical details along the way, but don’t worry—it’ll all make sense by the end. So, buckle up, grab a coffee, and let’s dive into the world of galvanized corrugated metal!
Overview of Galvanized Corrugated Metal
Galvanized corrugated metal is a type of sheet metal that has been coated with a layer of zinc to prevent corrosion. It’s most commonly used in roofing, wall cladding, and as a structural component in various industries like agriculture, construction, and even automotive. This material is prized for its high strength-to-weight ratio, resistance to rust, and its unique, industrial aesthetic.
You’ve probably seen galvanized corrugated metal more times than you realize—on barns, warehouses, or even in chic urban lofts where it’s used as an interior design feature. The zinc coating gives it a long life, even in environments exposed to moisture, making it ideal for both indoor and outdoor use.
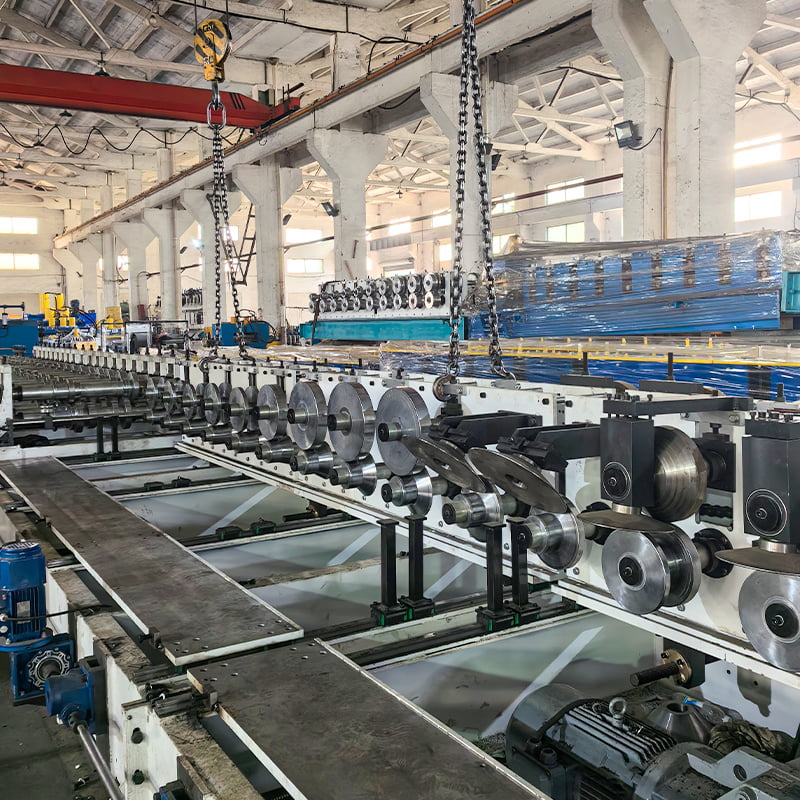
Corrugated Iron Sheets Guide
Corrugated iron sheets are the backbone of galvanized corrugated metal products. When we talk about galvanized metal, we’re often referring to sheets of iron or steel that have been pressed into a series of ridges and grooves—these “corrugations” increase the metal’s structural strength and rigidity.
The sheets themselves come in a variety of profiles, sizes, and thicknesses, each tailored for specific applications. Corrugated iron sheets can be flat, wavy, or more angular, depending on the aesthetic and functional requirements of the project. Let’s break down some of the key models on the market today.
Popular Corrugated Metal Models
Model | Material | Coating Thickness | Dimensions | Best Applications |
---|---|---|---|---|
Galvalume AZ50 | Steel with aluminum-zinc alloy coating | 0.50 mil | 36″ width, custom lengths | Roofing, siding |
G90 Corrugated Steel | Steel with zinc coating | 0.90 mil | 42″ width, custom lengths | Industrial roofing, walls |
PBR Panel | Galvanized steel | 0.80 mil | 36″ width, custom lengths | Warehouses, agricultural buildings |
R Panel | Galvanized steel | 0.70 mil | 36″ width, custom lengths | Commercial buildings, garages |
Corrugated Zinc | Pure zinc coating on steel | 1.00 mil | 39″ width, custom lengths | Decorative projects, sheds |
5V Crimp | Galvanized steel | 0.65 mil | 24″ width, custom lengths | Residential roofing, garages |
Standing Seam Panels | Galvanized steel | 0.75 mil | Custom widths and lengths | High-end residential projects |
Perforated Galvanized Sheet | Steel with zinc coating | 0.85 mil | Custom dimensions | Decorative walls, fencing |
Wave Panel | Galvanized steel | 0.70 mil | 36″ width, custom lengths | Commercial, industrial applications |
Corrugated Color Coated Steel | Zinc-coated steel with paint finish | 0.90 mil | 42″ width, custom lengths | Architectural designs, colorful roofing |
Types of Galvanized Corrugated Metal
There’s no one-size-fits-all when it comes to galvanized corrugated metal. Each type has its strengths and weaknesses, and understanding these nuances can make all the difference for your project. Below, we dive into some of the most common types available on the market.
1. Hot-Dipped Galvanized Corrugated Metal
Hot-dipped galvanized corrugated metal is created by submerging steel into molten zinc. This process provides a thick, durable zinc layer that offers excellent corrosion resistance. It’s widely used in roofing, wall cladding, and fencing.
Pros:
- Highly resistant to rust
- Thick zinc coating for increased longevity
- Suitable for outdoor applications
Cons:
- More expensive compared to electro-galvanized metal
- The surface can be less smooth
2. Electro-Galvanized Corrugated Metal
Electro-galvanizing involves applying a thinner layer of zinc through electroplating. While not as robust as hot-dipped varieties, electro-galvanized metal is still highly resistant to corrosion and is often used for interior applications or in environments that aren’t as harsh.
Pros:
- Smoother surface finish
- Lower cost than hot-dipped metal
- Great for indoor projects
Cons:
- Thinner zinc coating means less durability in harsh environments
3. Pre-Painted Galvanized Corrugated Metal
For projects where aesthetics matter, pre-painted galvanized metal offers both beauty and durability. The underlying steel is galvanized, then coated with layers of paint, providing extra protection against corrosion and an opportunity to customize the appearance.
Pros:
- Available in a wide range of colors
- Additional layer of protection against the elements
- Customizable for architectural designs
Cons:
- Paint can chip or fade over time
- Slightly more expensive due to the extra finishing process
Working Process of Galvanized Corrugated Metal
The process of creating galvanized corrugated metal is fascinating, and understanding how it’s made can provide valuable insight into why it performs so well in various applications.
Step 1: Sheet Metal Formation
The first step in the process is the formation of flat sheets of metal, typically steel or iron. These sheets are rolled out to the desired thickness and length.
Step 2: Corrugation
The flat metal sheets are then passed through a set of rollers that create the distinctive ridges and grooves. This “corrugation” increases the strength of the sheet without adding extra weight, which is why corrugated metal is so popular in applications where strength and lightweight materials are needed.
Step 3: Galvanization
Once the metal has been corrugated, the sheets undergo the galvanization process. This typically involves either dipping the sheet into molten zinc (hot-dipped galvanizing) or applying a zinc coating through electroplating.
Step 4: Coating and Finishing (Optional)
In some cases, the metal will receive an additional layer of paint or another type of finish. This is common in architectural projects where aesthetics are just as important as function.
-
Carriage Board Roll Forming Machine
-
Highway Guardrail End Terminal Forming Machine
-
Highway U/C Post Roll Forming Machine
-
2 Waves Highway Guardrail Roll Forming Machine
-
3 Waves Highway Guardrail Roll Forming Machine
-
Vineyard Post Roll Forming Machine
-
Auto Size Changeable Sigma Purlin Roll Forming Machine
-
Electrical Cabinet Frame Roll Forming Machine
-
Din Rail Roll Forming Machine
Key Components and Their Functions in Galvanized Corrugated Metal
Every component in galvanized corrugated metal plays a crucial role in its overall performance. Let’s break down the key parts and how they contribute to the sheet’s longevity and strength.
Component | Function |
---|---|
Steel/Iron Base | Provides the core strength of the material |
Zinc Coating | Protects the metal from rust and corrosion |
Corrugations (Ridges) | Adds structural strength and rigidity |
Paint Coating (Optional) | Adds extra aesthetic appeal and a layer of protection against the elements |
Machine Speed and Efficiency in Galvanized Corrugated Metal Production
Efficiency is key in the production of galvanized corrugated metal. Here’s a quick look at the machine speeds and efficiencies involved in this process.
Machine | Average Speed (ft/min) | Efficiency (%) |
---|---|---|
Corrugation Rollers | 100-300 | 90-95 |
Hot-Dip Galvanizing Line | 150-350 | 85-90 |
Electro-Galvanizing Line | 100-200 | 88-92 |
Painting/Finishing Line | 50-100 | 80-85 |
Customized Mechanical Parameters for Galvanized Corrugated Metal
For those looking to customize their galvanized corrugated metal to meet specific project needs, understanding the available mechanical parameters is crucial. Below is a table outlining some of the customizable features.
Parameter | Options Available |
---|---|
Thickness | 0.3 mm to 1.5 mm |
Width | 24 inches to 48 inches |
Coating Thickness | 0.3 mil to 1.5 mil |
Length | Custom lengths available |
Corrugation Depth | Varies by profile, up to 1 inch |
Finish | Pre-painted, zinc-only, or matte |
Applications and Uses of Galvanized Corrugated Metal
Galvanized corrugated metal is versatile and used in a variety of industries. Below are some common applications:
Industry | Use |
---|---|
Construction | Roofing, wall cladding, flooring |
Agriculture | Barns, silos, animal enclosures |
Automotive | Truck beds, trailers |
Industrial | Warehouses, factories, storage units |
Architectural | Decorative wall panels, modern design elements |
Residential | Garages, garden sheds, fences |
Installation, Operation, and Maintenance of Galvanized Corrugated Metal
Proper installation and maintenance are essential to ensure the long-term performance of galvanized corrugated metal. Here’s a guide to keep your metal in top shape.
Phase | Best Practices |
---|---|
Installation | Ensure proper overlap between sheets to prevent leaks, use high-quality fasteners |
Operation | Avoid excessive loads that could deform the metal |
Maintenance | Regularly inspect for rust or damage, clean with water and mild detergent, re-coat paint if necessary |
Suppliers and Price Range for Galvanized Corrugated Metal
Finding the right supplier can be a game-changer for your project. Here are some leading suppliers and their price ranges for galvanized corrugated metal.
Supplier | Price Range (per sq. ft.) |
---|---|
Metal Sales Manufacturing Corp | $5.00 – $8.00 |
Mueller, Inc. | $4.50 – $7.50 |
Steel Dynamics | $4.00 – $6.50 |
ASC Building Products | $5.50 – $9.00 |
McElroy Metal | $4.25 – $7.75 |
How to Choose the Right Supplier for Galvanized Corrugated Metal
Choosing the right supplier can be daunting, but there are several key factors to consider:
Criteria | Why It’s Important |
---|---|
Price | Ensure the price aligns with your budget, but beware of too-good-to-be-true offers |
Quality of Materials | Look for suppliers offering high-quality zinc coatings and durable steel |
Customization Options | If your project requires specific dimensions or finishes, make sure the supplier can accommodate |
Lead Time | Confirm how quickly the supplier can fulfill your order, especially if you’re on a tight deadline |
Reputation | Check reviews and testimonials to gauge customer satisfaction |
Advantages and Disadvantages of Galvanized Corrugated Metal
Let’s break down the pros and cons to give you a balanced perspective.
Aspect | Advantages | Disadvantages |
---|---|---|
Durability | Long-lasting due to corrosion resistance | Susceptible to scratches that can lead to rust |
Cost | Relatively inexpensive compared to other materials | Higher upfront cost for hot-dipped vs. electro-galvanized |
Aesthetic | Industrial look popular in modern designs | Can be difficult to paint or modify after installation |
Weight | Lightweight for easy installation | May dent under extreme pressure |
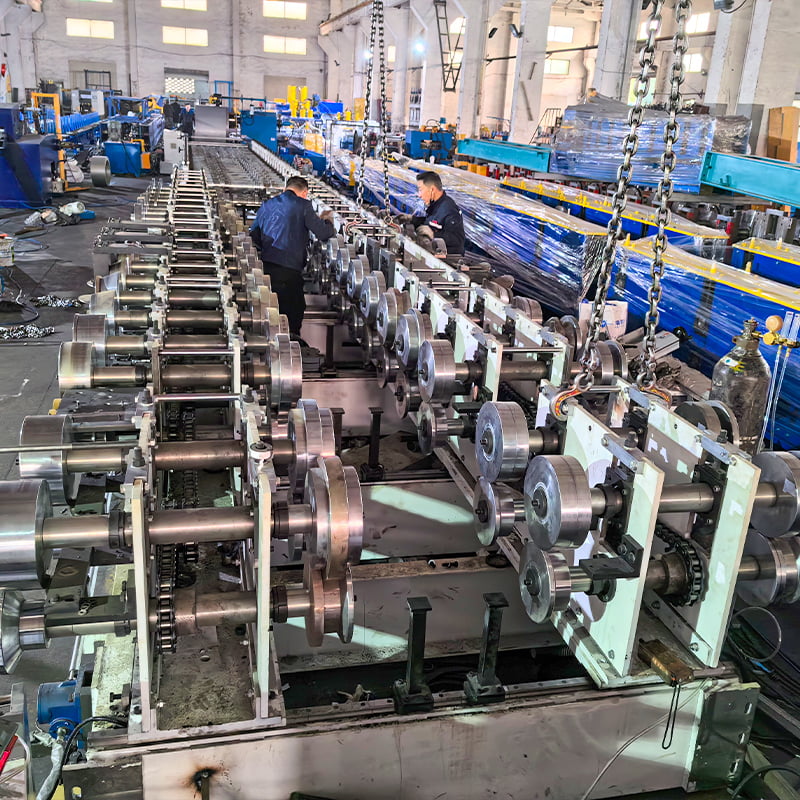
FAQ
Question | Answer |
---|---|
Is galvanized corrugated metal suitable for coastal environments? | Yes, especially hot-dipped varieties with thicker zinc coatings. |
How long does galvanized corrugated metal last? | Depending on the environment, it can last anywhere from 25 to 50 years. |
Can galvanized corrugated metal be painted? | Yes, but make sure to use paints compatible with zinc coatings. |
What’s the difference between galvalume and galvanized metal? | Galvalume is coated with an aluminum-zinc alloy, offering better resistance to corrosion than traditional galvanized metal. |
Is galvanized corrugated metal eco-friendly? | Yes, it is 100% recyclable and often made from recycled materials. |
In conclusion, galvanized corrugated metal offers an unbeatable combination of durability, versatility, and aesthetic appeal. Whether you’re building a barn, cladding a warehouse, or designing a modern home, it’s a material that stands the test of time. With the right supplier, proper maintenance, and a good understanding of your options, you’ll be well on your way to success. Happy building!