Introduction
In the ever-evolving world of manufacturing, automation continues to play a pivotal role in enhancing efficiency, productivity, and accuracy. One such innovation that has transformed the metalworking industry is the fully automatic roll forming machine. This article delves into the concept of a fully automatic roll forming machine, its working principles, applications, benefits, and key factors to consider when choosing the right machine for your business.
What is a Fully Automatic Roll Forming Machine?
A fully automatic roll forming machine is a cutting-edge piece of equipment used to create metal profiles with high precision and speed. It takes coiled metal sheets or strips and passes them through a series of roller stations to gradually form the desired profile. Unlike manual or semi-automatic machines, this automated solution requires minimal human intervention during the production process.
How Does a Fully Automatic Roll Forming Machine Work?
The operation of a fully automatic roll forming machine involves a sequence of precise steps. Initially, a decoiler feeds the metal coil into the machine, followed by a leveling process to ensure flatness. The metal then passes through sets of rollers, each designed to shape specific portions of the profile. An integrated cutting system ensures accurate cutting of the formed profiles to the required length.
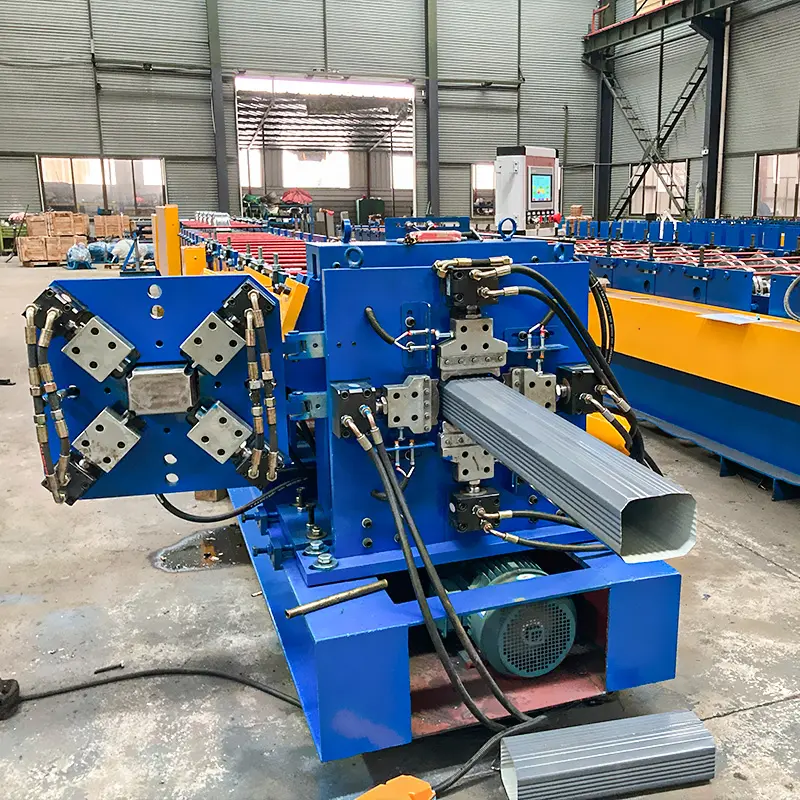
Advantages of Using a Fully Automatic Roll Forming Machine
Increased Production Efficiency
The automation of the roll forming process significantly enhances production efficiency. The machine’s continuous operation and rapid forming capabilities allow for higher output rates compared to traditional methods.
Consistent and Accurate Output
Fully automatic roll forming machines deliver unmatched precision and consistency in the profiles produced. This eliminates variations and ensures the final products meet strict quality standards.
Cost Savings in Labor
With reduced reliance on manual labor, businesses can save significantly on labor costs while increasing overall productivity.
Applications of Fully Automatic Roll Forming Machines
The versatility of fully automatic roll forming machines makes them indispensable across various industries. Some of the primary applications include:
Automotive Industry
In the automotive sector, these machines are used to fabricate structural components, roof rails, and other customized profiles required for vehicle assembly.
Construction Industry
Fully automatic roll forming machines play a crucial role in producing metal profiles used in constructing walls, roofs, and other structural elements.
HVAC Industry
For heating, ventilation, and air conditioning systems, these machines create air ducts and other specialized profiles with precise dimensions.
Electrical Industry
In the electrical sector, fully automatic roll forming machines are employed to manufacture cable trays, conduit pipes, and other electrical enclosures.
Types of Profiles Formed by Fully Automatic Roll Forming Machines
Fully automatic roll forming machines can create various profiles to suit specific requirements. Some common types of profiles include:
C-Channel Profiles
These profiles have a shape resembling the letter “C” and find applications in various structural and manufacturing projects.
Z-Channel Profiles
Z-channel profiles have a unique “Z” shape and are ideal for use as supporting elements and framing structures.
U-Channel Profiles
U-channel profiles are characterized by their U-shaped design and are commonly used as edging and trim components.
Custom Profiles
Apart from standard profiles, fully automatic roll forming machines can be programmed to produce custom-designed profiles as per specific customer needs.
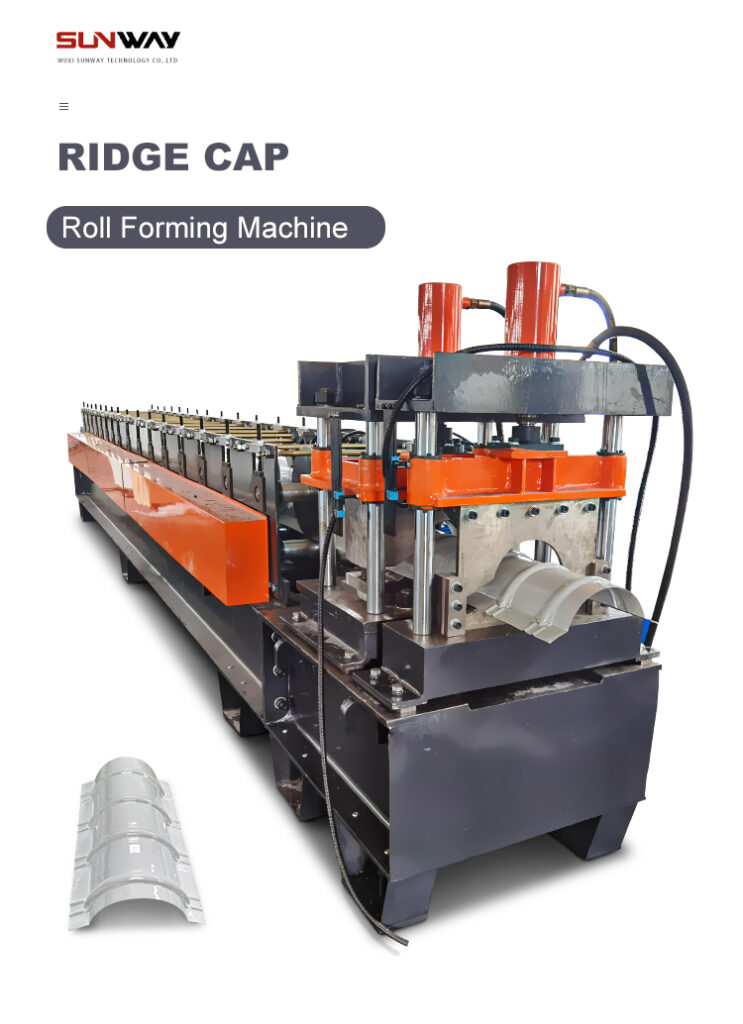
Features to Consider When Choosing a Fully Automatic Roll Forming Machine
Selecting the right machine for your business requires careful consideration of the following features:
Material Thickness and Width Capacity
Ensure the machine can handle the material thickness and width required for your intended profiles.
Number of Stations
More roller stations allow for greater profile complexity and can accommodate a broader range of products.
Speed and Production Rate
Consider the production speed of the machine and evaluate whether it aligns with your production requirements.
Control Systems
Modern machines come with advanced control systems, offering user-friendly interfaces and efficient programming capabilities.
Post-Cut or Pre-Cut System
Choose between post-cut and pre-cut systems based on your preferences and production needs.
Maintenance and Care of Fully Automatic Roll Forming Machines
Regular maintenance is essential to ensure the longevity and optimal performance of your fully automatic roll forming machine. This includes routine inspections, lubrication, and addressing any issues promptly.
Troubleshooting Common Issues with Fully Automatic Roll Forming Machines
Understanding and troubleshooting common problems can minimize downtime and keep your production running smoothly. Some common issues include:
Material Jamming
Detect and resolve material jamming to avoid damage to the machine and ensure continuous production.atGPT
Inconsistent Profile Dimensions
Identifying and rectifying inconsistencies in profile dimensions is crucial to maintaining the quality of the end product. Check for misalignments, worn-out rollers, or any other issues that may affect the precision of the forming process. Regular calibration and adjustments can help mitigate this problem.
Excessive Noise and Vibration
Excessive noise and vibration may indicate mechanical issues or misalignment within the machine. Conduct thorough inspections to identify the source of the problem and perform necessary repairs or replacements.
Safety Precautions When Operating a Fully Automatic Roll Forming Machine
Operating a fully automatic roll forming machine requires strict adherence to safety protocols. Ensure the safety of operators and workers by implementing the following precautions:
Training and Proper Instruction
Provide comprehensive training to operators and personnel involved in operating the machine. Proper understanding of the equipment and safety procedures reduces the risk of accidents.
Personal Protective Equipment (PPE)
Enforce the use of appropriate personal protective equipment, such as safety goggles, gloves, and ear protection, to safeguard against potential hazards.
Machine Guards and Safety Interlocks
Install safety guards and interlock systems to prevent access to moving parts during operation, reducing the risk of injuries.
Regular Inspections and Maintenance
Regularly inspect and maintain the machine to ensure its safety and optimal performance. Address any issues promptly to avoid potential accidents.
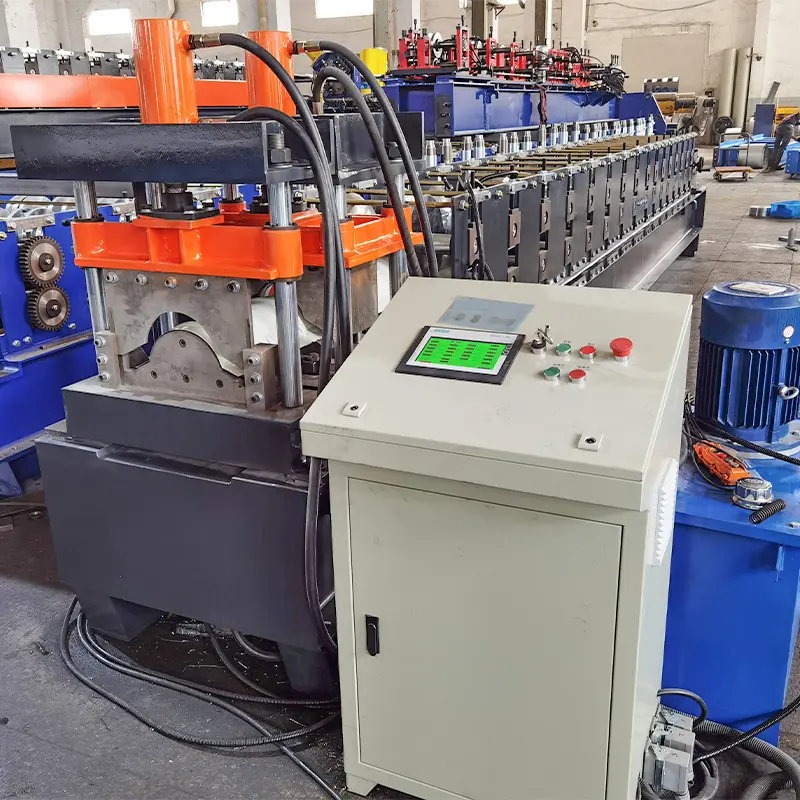
How to Choose the Right Fully Automatic Roll Forming Machine for Your Business
Selecting the most suitable fully automatic roll forming machine is a critical decision for your business. Consider the following factors when making your choice:
- Production Requirements: Determine the volume of profiles you need to produce and choose a machine that can meet your production demands.
- Profile Complexity: If you require intricate and custom profiles, opt for a machine with a higher number of roller stations.
- Material Compatibility: Ensure that the machine is compatible with the materials you plan to work with, whether it’s steel, aluminum, or other metals.
- Automation Features: Look for advanced automation features, such as computer numerical control (CNC), to enhance precision and ease of operation.
- Manufacturer Reputation: Research the reputation and track record of the manufacturer to ensure you invest in a reliable and reputable machine.
Conclusion
The advent of fully automatic roll forming machines has revolutionized the metalworking industry, providing unmatched precision, speed, and efficiency in producing metal profiles. Their versatility makes them indispensable across numerous sectors, from automotive and construction to HVAC and electrical industries. When choosing the right machine, consider factors like production requirements, profile complexity, material compatibility, and manufacturer reputation. By adhering to safety protocols and conducting regular maintenance, businesses can maximize the benefits of fully automatic roll forming machines, streamlining production and delivering high-quality profiles.
FAQs
What is the difference between manual and automatic roll forming machines?
The main difference lies in the level of automation. Manual roll forming machines require significant human intervention during the forming process, while automatic machines operate with minimal human involvement, streamlining production and increasing efficiency.
Can fully automatic roll forming machines handle different materials?
Yes, fully automatic roll forming machines can handle various materials, including steel, aluminum, copper, and more, depending on the machine’s specifications and capabilities.
What factors can affect the production speed of a fully automatic roll forming machine?
Factors such as the complexity of the profile, material thickness, and the number of roller stations can influence the production speed of the machine.
Is operator training required for using a fully automatic roll forming machine?
Yes, operator training is essential to ensure safe and efficient machine operation. Proper training helps operators understand the machine’s functions, safety protocols, and troubleshooting techniques.
How do I know which type of profile I need for my specific application?
To determine the appropriate profile for your application, consult with roll forming experts or manufacturers who can assess your requirements and recommend the best solution.