C channel roll forming machines are used in a variety of industries to produce high-quality, consistent C-shaped channels. These machines are essential for businesses that require a high volume of C channels, such as those in the construction, automotive, and appliance industries. However, to get the most out of your C channel roll forming machine, it’s important to maximize its efficiency.
Efficiency is essential for any business that wants to remain competitive in today’s market. Maximizing the efficiency of your C channel roll forming machine can help you save time, reduce waste, and increase output, all of which can help improve your bottom line. By optimizing the performance of your C channel roll forming machine, you can produce more parts in less time, reduce material waste, and improve the overall quality of your products.
In this post, we’ll discuss some key strategies for maximizing the efficiency of your C channel roll forming machine. We’ll cover topics such as proper maintenance, material selection, roll design, feed accuracy, speed control, quality control, automation, and training and education. By implementing these strategies, you can help ensure that your C channel roll forming machine operates at its maximum potential, allowing you to produce high-quality, consistent C channels in the most efficient way possible.
Proper Maintenance for C channel roll forming machine
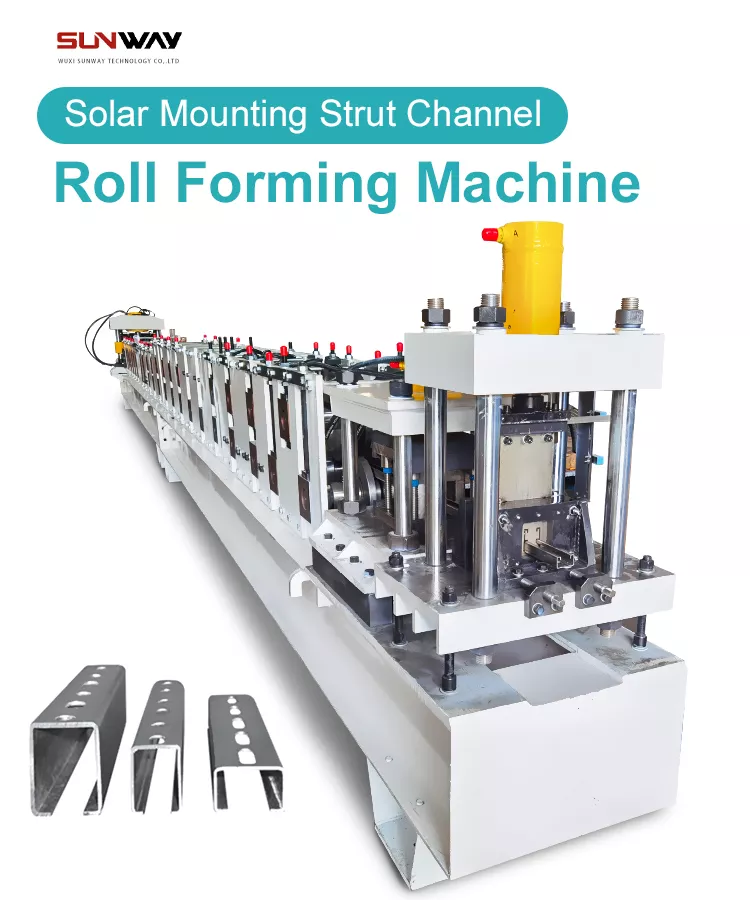
Proper maintenance is critical for ensuring the optimal performance of your C channel roll forming machine. Regular maintenance helps prevent breakdowns, reduce downtime, and increase the lifespan of your machine. Here are some important maintenance practices to follow:
- Regular cleaning: Regular cleaning is essential for keeping your C channel roll forming machine in good condition. Dirt, debris, and other contaminants can cause wear and tear on the machine’s components, reducing its overall efficiency. Clean the machine regularly, including the rollers, guides, and other components.
- Inspection of components: Inspect the machine’s components regularly, looking for any signs of wear, damage, or misalignment. This includes the rollers, guides, bearings, and other moving parts. Identifying and repairing problems early can help prevent more significant issues down the line.
- Lubrication: Proper lubrication of the machine’s components is critical for ensuring smooth operation and preventing excessive wear. Follow the manufacturer’s recommended lubrication schedule and use the correct type of lubricant for each component.
- Replacement of worn or damaged parts: Replace any worn or damaged parts as soon as possible. Worn or damaged parts can cause the machine to operate inefficiently, resulting in lower quality products and increased downtime.
- Calibration: Calibrate the machine regularly to ensure it is operating within the specified tolerances. This includes checking the machine’s alignment and making any necessary adjustments.
By following these maintenance practices, you can help ensure that your C channel roll forming machine operates at its maximum potential. Regular maintenance can help prevent breakdowns, reduce downtime, and increase the lifespan of your machine, resulting in higher quality products and increased efficiency.
Roll Design of C channel roll forming machine

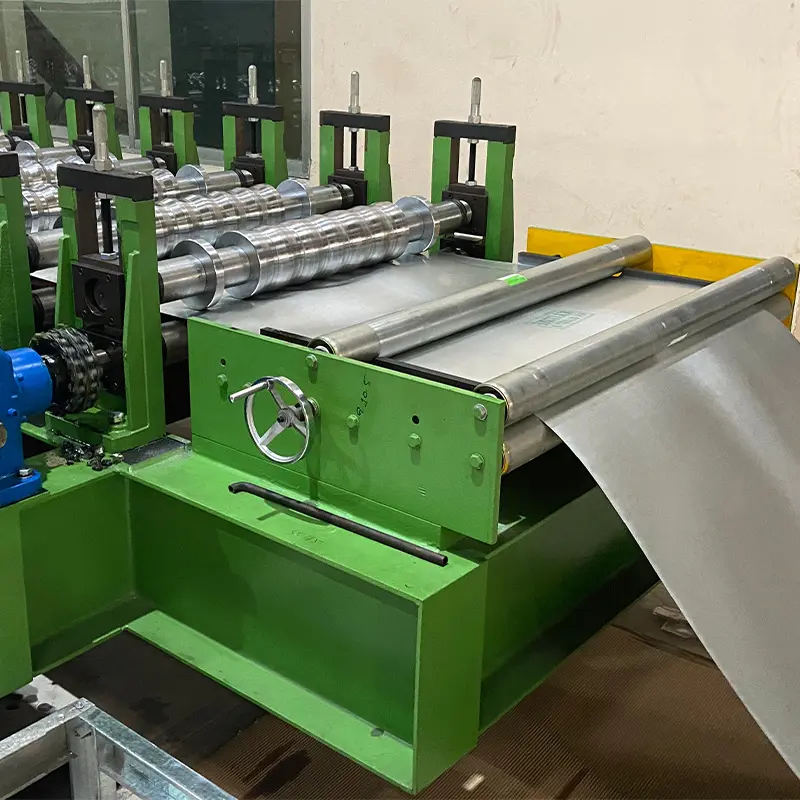

The design of the rolls is a critical factor in determining the efficiency of your C channel roll forming machine. The rolls shape and configuration affect the quality of the finished product, the rate of material usage, and the overall efficiency of the machine. Here are some key considerations for roll design:
- Roll Configuration: The roll configuration determines the shape and profile of the C channel being produced. Choosing the right roll configuration can significantly impact the efficiency of your machine. For example, using rolls with too many forming steps can slow down the machine and increase scrap material.
- Material Selection: The type and gauge of material being used will determine the size and shape of the rolls needed to achieve the desired profile. The rolls should be designed to minimize the amount of material used while maintaining the required tolerances and quality.
- Alignment: Proper alignment of the rolls is critical for ensuring efficient operation of the machine. Misaligned rolls can cause material to be pulled unevenly through the machine, leading to poor quality and wasted material.
- Material Lubrication: Lubrication of the rolls is essential to prevent material from sticking or binding to the rolls. Proper lubrication can help reduce wear on the rolls and minimize scrap material.
- Roll Material: Choosing the right material for the rolls is critical for their durability and performance. The rolls should be made of high-quality materials that can withstand the pressures and stresses of the roll forming process.
By selecting the right roll configuration, ensuring proper alignment, and using high-quality materials, you can maximize the efficiency of your C channel roll forming machine. By minimizing scrap material and producing high-quality channels in less time, you can increase your machine’s output and reduce costs. Proper roll design is crucial for ensuring that your machine operates at its maximum potential, leading to improved efficiency and higher quality products.
Feed Accuracy improve the efficiency of C channel roll forming machine
Maintaining accurate and consistent material feeding is essential for maximizing the efficiency of your C channel roll forming machine. Inaccurate material feeding can lead to inconsistent product quality, increased scrap material, and reduced machine output. Here are some key considerations for maintaining accurate material feeding:
- Proper Adjustment of Feeding Mechanism: The feeding mechanism should be properly adjusted to ensure consistent and accurate material feeding. The machine’s feed rollers should be set at the correct tension, and the distance between them should be adjusted to match the thickness of the material being fed.
- Monitoring Material Thickness: Monitoring the thickness of the material being fed is crucial for maintaining accurate and consistent feeding. Use a thickness gauge to check the material thickness regularly and adjust the feeding mechanism as needed.
- Material Straightness: The material should be straight and free from any kinks or bends before it is fed into the machine. Bent or kinked material can cause uneven feeding and result in poor quality products and increased scrap material.
- Material Quality: The quality of the material being fed into the machine can impact the efficiency of the roll forming process. High-quality material is less likely to jam or cause other issues, leading to smoother feeding and increased machine output.
- Consistent Feed Rate: Maintaining a consistent feed rate is essential for producing high-quality, consistent products. Use the machine’s controls to maintain a consistent feed rate, and adjust the feeding mechanism as needed to ensure optimal performance.
By maintaining accurate and consistent material feeding, you can improve the efficiency of your C channel roll forming machine. This includes proper adjustment of the feeding mechanism, monitoring material thickness, ensuring material straightness, using high-quality material, and maintaining a consistent feed rate. By minimizing scrap material and producing high-quality channels in less time, you can increase your machine’s output and reduce costs.
In conclusion, maximizing the efficiency of your C channel roll forming machine requires attention to several critical factors. Proper maintenance, material selection, roll design, feed accuracy, speed control, quality control, automation, and training and education are all essential for ensuring that your machine operates at its maximum potential. By following these strategies, you can reduce waste, increase output, and produce high-quality, consistent C channels in the most efficient way possible. Ultimately, maximizing the efficiency of your C channel roll forming machine can help your business remain competitive in today’s market and improve your bottom line.