Introduction
Drywall, also known as gypsum board or plasterboard, is a widely used building material for interior walls and ceilings. The manufacturing process of drywall involves shaping and forming thin sheets of gypsum into the desired dimensions. One crucial tool in this process is the drywall roll forming machine, which plays a pivotal role in shaping metal components used in drywall assembly. In this article, we will explore the features, benefits, working principle, selection criteria, and operation tips for a drywall roll forming machine.
What is a Drywall Roll Forming Machine?
A drywall roll forming machine is a specialized piece of equipment used to manufacture metal components that are integral to the construction of drywall systems. It utilizes a continuous bending process to transform flat metal coils into specific profiles, such as studs, tracks, furring channels, ceiling channels, and corner beads. These profiles provide structural support and serve as frameworks for attaching drywall panels.
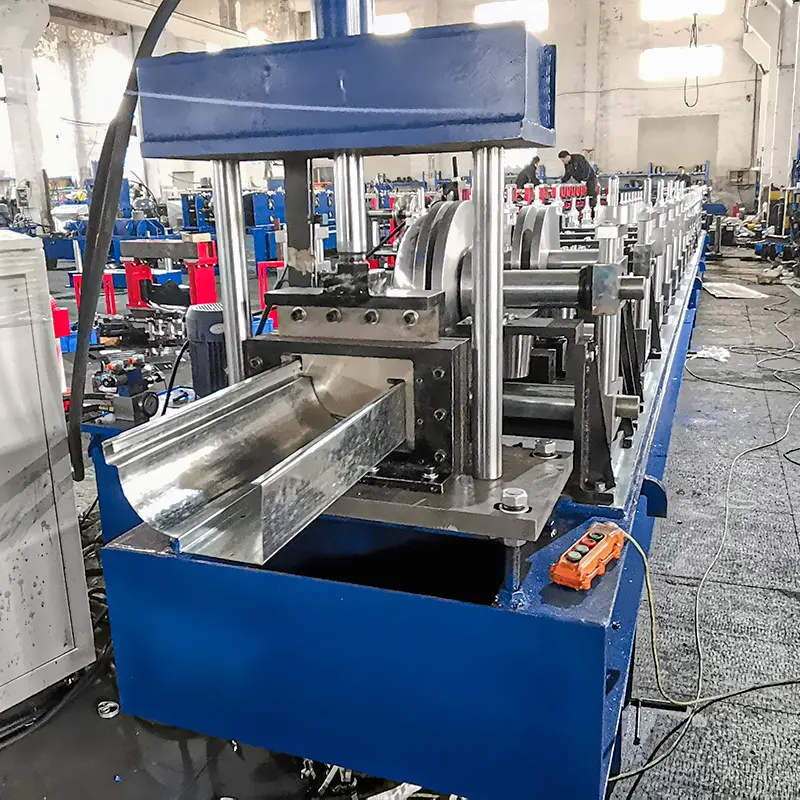
Benefits of Using a Drywall Roll Forming Machine
Using a drywall roll forming machine offers numerous benefits for construction projects. Let’s explore some of the key advantages:
- Cost and Time Efficiency: A roll forming machine can produce metal components at a high speed, significantly reducing production time and labor costs compared to manual fabrication methods.
- Consistency and Accuracy: The machine ensures precise shaping and uniformity of the metal profiles, leading to consistent results and avoiding variations in dimensions.
- Versatility: Drywall roll forming machines are adaptable and can produce a variety of profiles required for different drywall systems, accommodating various project needs.
- Material Optimization: Roll forming minimizes material waste by using coil stock efficiently, resulting in cost savings and sustainability benefits.
- Enhanced Strength: Roll-formed metal components possess increased strength and rigidity, providing improved structural integrity to the drywall system.
Types of Drywall Roll Forming Machines
There are several types of drywall roll forming machines available in the market, each designed to produce specific profiles. Let’s examine some common types:
Stud and Track Roll Forming Machine
The stud and track roll forming machine specializes in manufacturing metal studs and tracks. These components form the framework for drywall partitions and are crucial for structural stability.
Furring Channel Roll Forming Machine
Furring channels are used to provide support for the attachment of drywall panels to masonry or concrete walls. The furring channel roll forming machine produces these channels with precise dimensions and consistent quality.
Ceiling Channel Roll Forming Machine
Ceiling channels, also known as hat channels, are utilized in suspended ceiling systems. The ceiling channel roll forming machine manufactures these channels, ensuring accurate profiles that facilitate easy installation.
Corner Bead Roll Forming Machine
Corner beads are used to reinforce and protect the edges of drywall corners. The corner bead roll forming machine produces these components, offering durability and precise corner shapes.

Working Principle of a Drywall Roll Forming Machine
A drywall roll forming machine operates based on a continuous bending process. Here’s a simplified explanation of its working principle:
- Material Feeding: Flat metal coil stock is fed into the roll forming machine.
- Roll Forming Stations: The machine consists of a series of roll forming stations, each equipped with pairs of rollers. These rollers gradually shape the metal coil into the desired profile.
- Roller Design: The rollers are designed to create specific contours and shapes as the metal passes through them. The number and arrangement of stations vary depending on the profile being formed.
- Cutting and Shearing: Once the metal reaches the end of the roll forming process, the machine can incorporate cutting or shearing mechanisms to separate the formed component from the remaining coil.
- Collection and Stacking: The finished metal profiles are collected and stacked, ready for use in drywall assembly.
The working principle of a roll forming machine ensures efficient and precise production of drywall components.

Features to Consider When Choosing a Drywall Roll Forming Machine
When selecting a drywall roll forming machine, it’s essential to consider specific features that align with your production requirements and preferences. Let’s explore some key factors to evaluate:
Speed and Production Capacity
The machine’s speed and production capacity should match your project’s demand to ensure efficient manufacturing and meet deadlines.
Material Compatibility
Check whether the roll forming machine is compatible with the metal materials you intend to use, such as galvanized steel, stainless steel, or aluminum.
Customization Options
Consider whether the machine can be customized to produce profiles with specific dimensions, hole patterns, or other requirements unique to your project.
Machine Durability and Reliability
Ensure the machine is built with high-quality materials and components that offer durability and long-term reliability, minimizing downtime and maintenance costs.
Ease of Use and Maintenance
Look for user-friendly interfaces and features that simplify machine operation, setup, and maintenance, allowing operators to quickly adapt and troubleshoot when necessary.
How to Select the Right Drywall Roll Forming Machine for Your Needs
Selecting the appropriate drywall roll forming machine involves a systematic approach to assess your production requirements, research manufacturers, evaluate specifications, and consider long-term support. Let’s break down the selection process into key steps:
Assessing Your Production Requirements
Evaluate the expected output, desired profiles, material specifications, and other factors relevant to your project’s drywall assembly needs.
Researching and Comparing Manufacturers
Research reputable manufacturers of drywall roll forming machines. Look for manufacturers with a proven track record, positive customer reviews, and a wide range of machine options.
Evaluating Machine Specifications
Compare the specifications of different drywall roll forming machines, considering factors such as speed, production capacity, material compatibility, customization options, durability, and ease of use. Select a machine that aligns with your specific requirements and offers the desired features.
Considering Long-term Support and Service
Ensure that the manufacturer provides comprehensive customer support, including training, technical assistance, and spare parts availability. Consider warranties and after-sales service options to address any potential issues that may arise during machine operation.
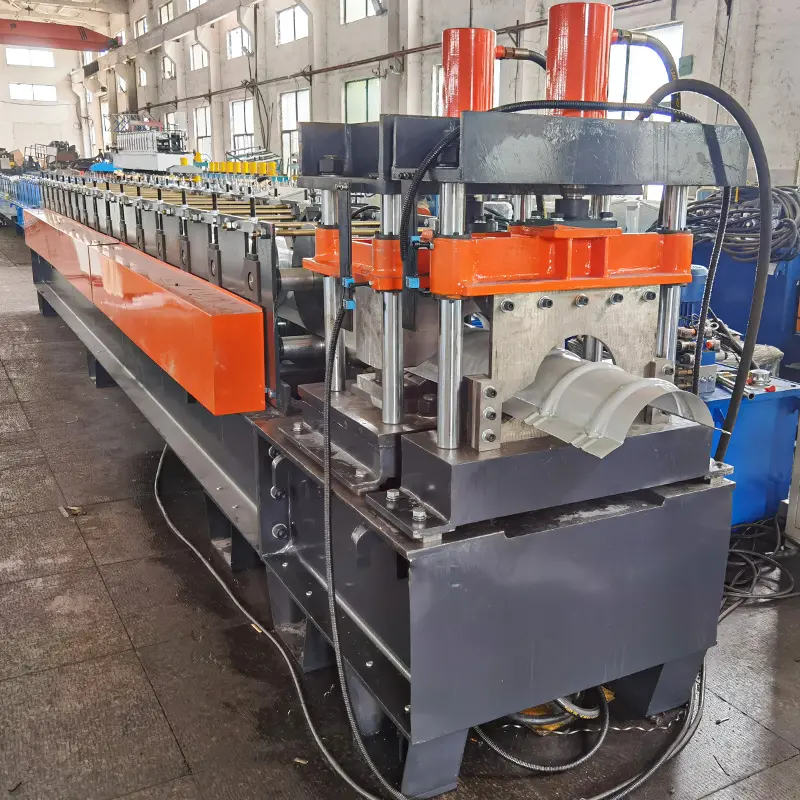
Tips for Operating a Drywall Roll Forming Machine
To maximize the efficiency and performance of your drywall roll forming machine, follow these essential tips for operation:
Safety Precautions
Always prioritize safety when operating the machine. Adhere to safety guidelines, use personal protective equipment (PPE), and ensure operators are properly trained in machine operation and safety procedures.
Proper Material Handling
Handle metal coils and finished profiles with care to prevent damage and injuries. Use appropriate lifting equipment and follow proper storage and handling procedures to maintain material integrity.
Machine Setup and Calibration
Set up the machine correctly, ensuring proper alignment of rollers, cutting mechanisms, and other components. Regularly calibrate the machine to maintain accuracy and precision in profile dimensions.
Regular Maintenance and Lubrication
Follow the manufacturer’s recommended maintenance schedule for the roll forming machine. Keep the machine clean and well-lubricated to prevent mechanical issues and prolong its lifespan. Regularly inspect and replace worn or damaged components.
Common Troubleshooting and Maintenance Issues
Despite regular maintenance, certain issues may still arise during the operation of a drywall roll forming machine. Here are some common troubleshooting and maintenance tips:
Material Jamming
If the machine experiences material jamming, stop the operation immediately. Clear the jammed material carefully, following proper safety procedures. Check for any misalignments or worn components that may be causing the issue.
Uneven Roll Forming
If the roll-formed profiles are inconsistent or uneven, check the alignment of the rollers and ensure they are properly adjusted. Verify that the material feed is smooth and steady, without any obstructions or interruptions.
Mechanical Component Wear and Tear
Regularly inspect the machine for signs of wear and tear, such as worn rollers or blades. Replace these components promptly to maintain the quality and accuracy of the roll-formed profiles.
Future Trends in Drywall Roll Forming Technology
As technology advances, drywall roll forming machines continue to evolve. Some future trends in the industry include:
- Integration of automation and robotics to enhance production efficiency and reduce labor requirements.
- Improved material handling systems for seamless coil feeding and profile collection.
- Advancements in machine controls and software for enhanced customization and precision.
- Integration of quality monitoring systems to ensure consistent and defect-free profiles.
These trends will contribute to further optimizing the drywall roll forming process, providing increased productivity and quality in the construction industry.
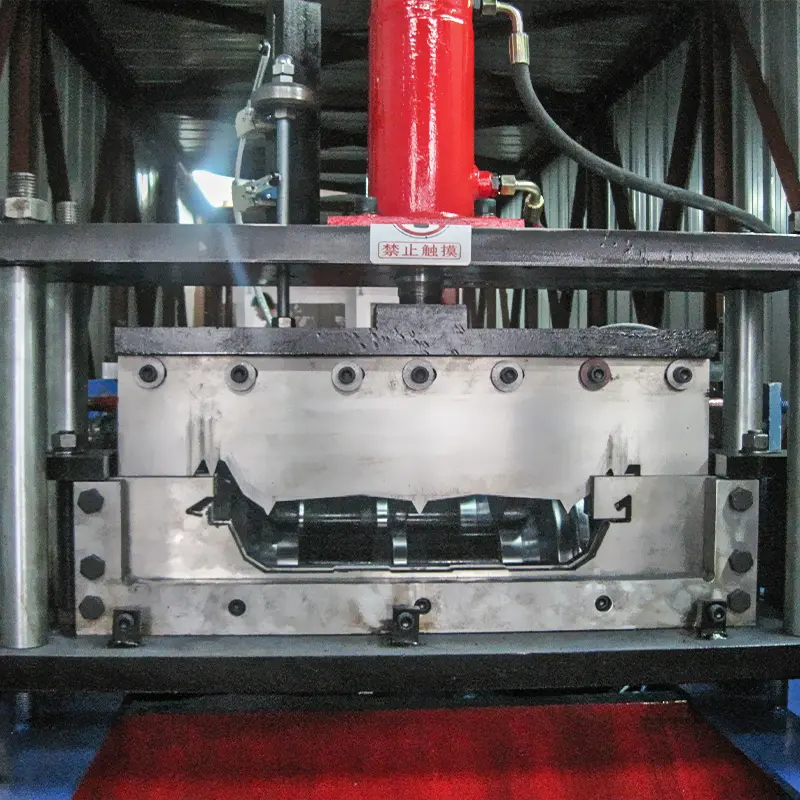
Conclusion
The drywall roll forming machine is an indispensable tool in the construction of interior walls and ceilings. Its ability to efficiently produce metal profiles for drywall systems offers numerous benefits, including cost and time savings, consistency, and material optimization. By considering factors such as machine features, selection criteria, and operation tips, you can choose the right drywall roll forming machine for your specific project needs. With proper operation, maintenance, and troubleshooting techniques, you can ensure optimal performance and longevity of the machine, contributing to successful drywall construction projects.
FAQs
Q1: Can a drywall roll forming machine produce customized profiles?
Yes, many drywall roll forming machines can be customized to produce profiles with specific dimensions, hole patterns, and other requirements. It’s important to check with the manufacturer regarding customization options.
Q2: How fast can a drywall roll forming machine produce metal profiles?
The production speed of a drywall roll forming machine depends on various factors such as the machine’s design, complexity of the profile being formed, and operator efficiency. Modern machines can typically achieve high production speeds, significantly faster than manual fabrication methods.
Q3: Are drywall roll forming machines difficult to operate?
Drywall roll forming machines are designed to be user-friendly, with intuitive interfaces and controls. Proper training and familiarization with the machine’s operation are important for efficient and safe usage. Manufacturers often provide training and support to ensure operators can operate the machines effectively.
Q4: Can a drywall roll forming machine work with different types of metal materials?
Yes, drywall roll forming machines can work with various metal materials, including galvanized steel, stainless steel, and aluminum. It’s essential to verify the machine’s compatibility with the specific material you intend to use.
Q5: How long does a drywall roll forming machine typically last?
The lifespan of a drywall roll forming machine depends on factors such as machine quality, maintenance practices, and frequency of use. With proper care, regular maintenance, and component replacements as needed, a well-built machine can last for many years, supporting numerous drywall construction projects.