Crash barrier roll forming machines are specialized lines designed to cold-form metal coils into corrugated guardrails and road safety barriers. This automated process efficiently produces finished crash barrier beams.
This comprehensive guide provides everything you need to know about crash barrier roll forming equipment, including:
Introduction to Crash Barrier Roll Forming
Roll forming shapes flat steel coil into corrugated crash barrier beams using a series of progressive bending dies.
Benefits:
- Highly efficient continuous forming
- Consistent and accurate beam dimensions
- Minimal material waste
- Automated mass production
- Flexibility to change beam profiles
Main Components:
- Coil payoff reel
- Feed rollers
- Forming stations
- Flying cutoff
- Control system
Latest crash barrier roll formers deliver high speed production, precision and reliability for road safety applications.
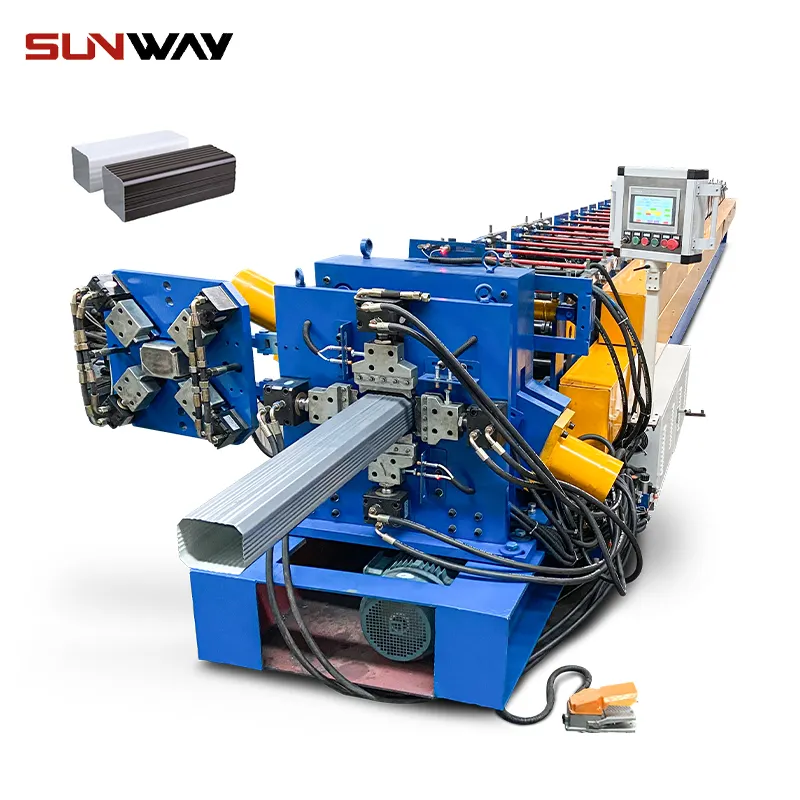
Types of Crash Barrier Roll Forming Machines
Crash barrier roll forming machines come in several configurations:
Types | Descriptions |
---|---|
Mechanical | Basic machines with mechanical drives |
Servo-motor | Advanced programmable servo motor drives |
All-electric | Energy efficient AC motors |
Hydraulic | Powered by hydraulic power packs |
Automatic | Fully automated infeed and cutoff |
Portable | Compact mobile roll formers |
Modern servo-controlled roll formers with automated features provide the best accuracy and productivity.
Crash Barrier Profiles Produced
Common corrugated profiles that can be roll formed include:
- W-beam – Most common symmetrical corrugated shape
- Thrie-beam – Asymmetrical beams with nested joints
- Box-beam – Hollow rectangular beams
- Single slope – Gradual sloped on one side
- Vertical wall – One vertical corrugated side
- Custom – Specialized profiles
With quick die changeover, lines can rapidly switch between different crash barrier profiles.
Crash Barrier Materials Used
Typical materials roll formed into road safety barriers:
- ASTM A36 steel
- Hot-rolled steel
- Galvanized steel
- Corten weathering steel
- Stainless steel
- Aluminum
Steel provides the optimal balance of strength, corrosion resistance, cost and weight for durable crash barriers.
Crash Barrier Roll Forming Process
The production sequence involves:
- Loading a coil of the substrate material into the feed system
- Feeding the strip through progressive roll forming stations
- Gradually cold-forming the corrugated beam profile
- Shearing the beams to specified length with flying cutoff
- Conveying finished crash barrier sections for stacking
Automated servo-motor controls precisely coordinate material movement through the in-feed, forming, cutoff and exit conveyor for high speed production.
Crash Barrier Roll Former Specifications
Typical specifications can be customized:
Parameters | Range |
---|---|
Forming Speed | 10 – 40 m/min |
Strip Width | 200 – 500 mm |
Thickness | 2 – 5 mm |
Beam Height | 150 – 900 mm |
Corrugation Size | 50 – 200 mm |
Sheet Length | 6 – 12 m |
Power | 20 – 75 kW |
Automation | Manual to Fully Automatic |
Choosing appropriate strip parameters, beam dimensions and speed capacity is vital.
Standards for Crash Barriers
Major standards include:
- AASHTO M180 – Corrugated sheet steel beams for highway guardrail
- EN 1317 – Road restraint systems
- NCHRP 350 – US standard for crash testing
- AS/NZS 3845 – Road safety barrier systems
- BS 6779-2 – Vehicle restraint systems on roads
Compliance is critical for performance, quality and safety.
Crash Barrier Roll Former Manufacturers
Leading global manufacturers of crash barrier roll forming lines include:
Company | Location | Description | Pricing |
---|---|---|---|
Metform | USA | Custom high capacity lines | $$ to $$$ |
Behemoth | Canada | Robust heavy duty lines | $$ to $$$ |
Eurobend | UK | Reliable European lines | $$ to $$$ |
Zhongrui | China | Affordable standard lines | $ to $$ |
Fors | Italy | High precision lines | $$$ |
Its | Korea | Value engineered lines | $ to $$ |
Pricing Considerations:
- Production speed and automation
- Line width capacity
- Quick changeover functionality
- Brand, quality and support services
- Customization of specifications
Partner with qualified manufacturers providing properly engineered equipment matched to your production needs.
Buying Considerations for Crash Barrier Lines
Important factors when investing in crash barrier roll forming equipment:
- Required barrier specifications and profile
- Production volume and speed goals
- Width capacity for coil stock
- Level of automation preferred
- Quick changeover ability between profiles
- Precision, accuracy and reliability required
- Available production space and layout
- Power supply needs
- Operator skill level
- Ongoing service and support
Clarifying key requirements will help identify optimal roll former specifications and capabilities.
Installing and Operating Crash Barrier Roll Forming Machines
Proper installation and operation procedures include:
- Stable, level and smooth foundation
- Adequate space around the equipment
- Securing stations and verifying alignments
- Electrical, pneumatic and hydraulic connections
- Integrating safety features and protocols
- Programmed setup and trials for each profile
- Preventive maintenance and lubrication
- Adhering to all safety procedures
Thorough installation, commissioning and maintenance maximizes production uptime and achieves a long service lifetime.
Benefits of Crash Barrier Roll Forming
Key advantages versus other forming methods:
- Continuous high speed production from coil
- Consistent and precision barrier dimensions
- Minimal material waste
- Lower operational costs
- Flexible, quick changeovers between profiles
- Safer enclosed process than open fabrication
- Automated process ideal for large volume production
- Integrates with other highway safety systems
Roll forming provides an efficient and economical barrier fabrication method.
Limitations of Crash Barrier Roll Forming
Some limitations include:
- High initial capital expenditure
- Substantial production volumes required for ROI
- Dedicated tooling for each profile
- Size constraints – width, bend radii etc.
- Material thickness and strength capabilities
- Secondary operations like punching may be needed
Other processes like press braking or stamping may suit lower volume production.
Cost Analysis for Roll Formed Barriers
- Equipment – $100,000 to $750,000
- Tooling per profile – $5,000 to $15,000
- Material coil – Varies based on steel specs
- Operating costs – Labor, maintenance, utilities
- Amortized equipment cost – Based on yearly production rate
- Secondary processing – Punching, coring, etc.
- Logistics – Inbound coils, outbound barrier delivery
High production levels provide lowest cost per linear foot and rapid payback on equipment.
Future Outlook for Crash Barrier Roll Forming
The future outlook for crash barrier roll forming is positive:
- Increasing roadway construction worldwide
- Transition from manual fabrication to automated lines
- Declining equipment costs over time
- Improving line speed, precision, efficiency and flexibility
- Quick-change tooling enabling faster changeovers
- Tighter integration with upstream coil processing
- Overall industry maturation and manufacturing optimization
- New high-strength steels and coatings
With technology improvements, roll formed barriers will continue displacing other approaches.
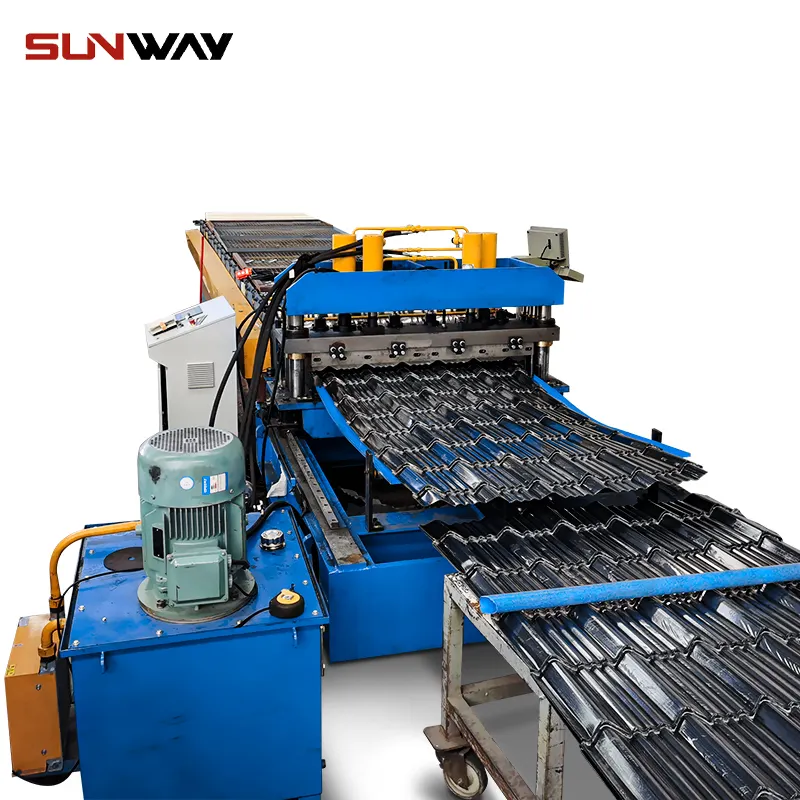
FAQ
Q: What materials can be roll formed into crash barriers?
A: Most commonly ASTM A36, hot-rolled, galvanized and Corten weathering steel. Other metals like aluminum and stainless steel can also be formed.
Q: What thickness coils are typically formed into barriers?
A: Standard thicknesses are 2mm to 5mm. Maximum depends on equipment capacity.
Q: How long does it take to form each barrier section?
A: On high speed lines producing 12m lengths, barriers can be formed in under 1 minute.
Q: How are roll formed barriers cut to length?
A: A flying cutoff shear built into the line cuts barriers at the production speed.
Q: What expertise is required to operate a barrier roll former?
A: Machine operators require training. Skilled technicians needed for programming, maintenance and troubleshooting.
Q: What safety equipment is mandatory?
A: Guards, e-stops, interlocks, automatic shutdowns, and strict operating procedures.
Q: How much does a crash barrier roll forming line cost?
A: Equipment costs range from $100k to $750k+, depending on the production speed, width, automation level, and features.
Q: How much does tooling cost for each barrier profile?
A: Roll forming tooling typically costs $5k to $15k per profile set, based on size and complexity.
Q: How long does it take to changeover between profiles?
A: With quick change tooling, profile changeover takes 15-45 minutes typically.
Q: Can custom barrier profiles be produced?
A: Yes, custom tooling allows production of specialized proprietary barrier designs.